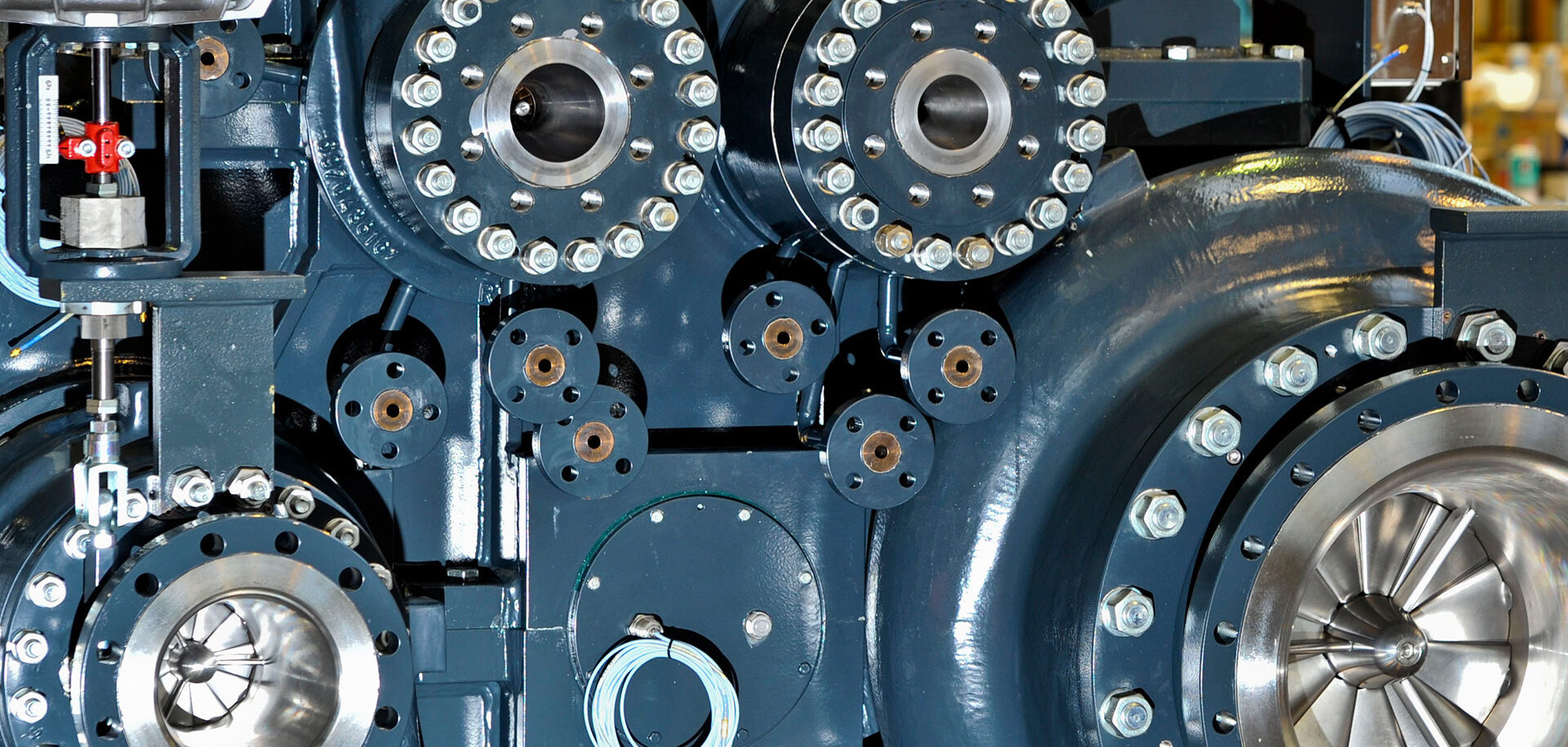
La transición de rótulas hidrodinámicas a rodamientos genera beneficios
Las soluciones de ingeniería que ofrece SKF permiten pasar de rodamientos con película de fluido a sistemas más eficientes con rodamientos.
La importancia de la eficiencia energética y de los recursos, especialmente en la producción industrial y el suministro de energía, es una cuestión que hoy está más que nunca en el orden del día. A pesar de los avances tecnológicos, se sigue derrochando mucha energía por todo el mundo a causa de las pérdidas por fricción mecánica y dinámica de los fluidos en la maquinaria rotativa, como compresores, turbinas, sopladores y bombas. Aquí presentamos descripciones y ejemplos de la vida real donde podrían obtenerse considerables ahorros en energía y costos sustituyendo los rodamientos hidrodinámicos con película de fluido por rodamientos modernos con elementos rodantes.
Los equipos industriales, como bombas, compresores y sopladores, pueden funcionar de 4000 a 8000 horas al año, lo que implica que la energía eléctrica para accionarlos generalmente sea, por mucho, el mayor costo de su ciclo de vida (LCC) y emisiones. En muchos casos, un poderoso medio para mejorar su eficiencia energética es el uso de equipos de velocidad variable (VSDs) de transmisión directa, y la selección de un diseño cuidadoso de impulsor, rodamientos y sistemas de sellado.
Durante miles de años, la humanidad ha utilizado elementos rodantes (barras, rodillos, bolas) para reducir la fricción y las pérdidas de calor en la maquinaria de transporte y rotativa, y para obtener una colocación confiable y precisa de los ejes rotativos. Es por ello que los rodamientos, a veces, también se denominan rodamientos antifricción o de precisión. Sin embargo, por diferentes razones técnicas e históricas, en el mundo se siguen usando muchos “rodamientos de fricción”, también denominados rótulas, rodamientos deslizantes, lisos, de película de fluido o con segmentos basculantes, o más específicamente, rodamientos hidrodinámicos o hidrostáticos.
Rodamientos hidrodinámicos frente a rodamientos con elementos rodantes
Los rodamientos hidrodinámicos dependen de la película de fluido (aceite) que separa la superficie de acero del eje rotativo del soporte fijo, utilizando los principios largamente conocidos de la lubricación hidrodinámica. Un rodamiento hidrodinámico bien lubricado no muestra prácticamente signos de fatiga ni desgaste mecánico, y proporciona más amortiguación de película de fluido que los rodamientos de bolas o rodillos. Gracias a la película de aceite, que es relativamente espesa, la suciedad y otras partículas tienen un menor impacto en su rendimiento debido a que las partículas duras quedan parcialmente integradas en el material más blando del manguito o amortiguador, y por ello, no pueden dañar las contracaras.
No obstante, en los rodamientos hidrodinámicos, la holgura es mayor, y los arranques y paradas frecuentes o el funcionamiento a muy baja velocidad les ocasionan desgaste y rayas, como puede suceder en aplicaciones de accionamiento con sistemas de frecuencia variable. Cuando el aceite lubricante es de baja viscosidad o queda muy diluido por el líquido procesado, puede suceder que la película lubricante formada ya no sea suficiente para un buen rendimiento de los rodamientos hidrodinámicos, especialmente en los de empuje con segmentos basculantes. A este respecto, los rodamientos con elementos rodantes constituyen una buena alternativa debido a que pueden funcionar con lubricantes de menor viscosidad y más diluidos, en especial cuando se utilizan elementos rodantes de cerámica.
También suelen preferirse los rodamientos con elementos rodantes en casos de funcionamiento intermitente y en entornos fríos gracias a su baja fricción de arranque, en especial al usar rodamientos híbridos con elementos rodantes de cerámica. Sin embargo, lo que es más importante para la eficiencia energética es que la fricción de rodaje suele ser muy inferior en los rodamientos con elementos rodantes, al menos a media y baja velocidad. Para funcionar, según se afirma en J/E Bearing & Machine Ltd [1], toda la película de fluido en las rótulas hidrodinámicas exige hasta tres veces más energía, incluso si se excluyen las pérdidas en el arranque. La figura esquemática de abajo ilustra un resultado típico al comparar las pérdidas por fricción (potencia) en rodamientos lisos en comparación con rodamientos de bolas o rodillos.
En el lado ganador: rodamientos en turbocompresores y cigüeñales
Como saben muy bien los ingenieros y entusiastas de automóviles de altas prestaciones, los turbocompresores con rodamientos de bolas han dominado el panorama del deporte de motor desde que los primeros rodamientos de bolas sustituyeron a los rodamientos lisos en los turbocompresores usados en las competiciones de las 24 horas de Le Mans durante la década del noventa. Hubo dos razones principales para el cambio. Primero, los sistemas con rodamientos de bolas mostraron una menor fricción de rodaje. Y en segundo lugar, evitaban la necesidad de bombas de aceite de alta presión, que ocasionaban pérdidas de potencia en los sistemas de rodamientos lisos, donde debe bombearse una gran cantidad de aceite a través de delgados agujeros en los manguitos de los rodamientos lisos. Los diseños recientes usan unidades de cartucho con rodamientos de bolas de cerámica híbridos, que ahorran espacio, lo que lleva el rendimiento a niveles aún más altos.
Ahorros enormes en la producción de electricidad ecológica
Una central geotérmica de 250 MW recientemente construida en Asia utiliza la tecnología del ciclo Rankine orgánico (OCR) para producir energía eléctrica ecológica mediante calor geotérmico. Para el accionamiento de los generadores de electricidad, se usan casi 200 equipos denominados expansores de tornillo, que se basan en el mismo principio mecánico que los compresores de dos tornillos, pero funcionan en sentido inverso, para producir energía mediante la expansión del vapor, similarmente a una turbina de vapor. Un reto concreto era alcanzar los objetivos de eficiencia establecidos por el propietario de la central. Los primeros ensayos mostraron que no podían alcanzarse usando rodamientos hidrodinámicos. Hay que observar que, en cada expansor de gran tamaño, se usan cinco o seis rodamientos hidrodinámicos.
Ahorrar 18 kW de pérdidas de potencia puede significar un aumento de más de 100 000 kWh en la producción de energía eléctrica, por equipo y año. Multiplicado por el gran número de expansores de tornillo usados en la planta, esto se traduce en unos beneficios anuales de más de un millón de dólares.
Enfriadores industriales y bombas de calor
En general, los grandes enfriadores comerciales o industriales o las bombas de calor están acopladas a compresores centrífugos o alternativos, que comprimen un gas refrigerante para permitir la transferencia de calor de una fuente de temperatura más baja a un recipiente de temperatura más elevada. Tradicionalmente, muchos compresores de refrigeración son o siguen siendo de diseño accionado por engranajes, con rodamientos hidrodinámicos lubricados por una mezcla de aceite y refrigerante.
Frecuentemente no se obtiene el efecto deseado con la introducción de nuevos refrigerantes ecológicos (p. ej., hidrofluoroolefinas [HFO] con un bajo potencial de calentamiento global y de agotamiento de la capa de ozono) y los niveles de temperatura mucho más altos necesarios en las bombas de calor o enfriadores de los centros de datos: el ritmo de dilución del aceite por los refrigerantes aumenta, a veces a rangos de dilución del 50 % o más. En ciertos casos, la viscosidad del aceite se convierte en demasiado baja para los rodamientos hidrodinámicos, y las disposiciones de rodamientos de los compresores tienen que cambiarse por rodamientos, lo que también supone una ventaja adicional de menos pérdidas por fricción y mayor exactitud en la colocación del impulsor.
Los datos muestran que los rodamientos crean menores pérdidas por fricción y también conducen a menos pérdidas volumétricas por holgura de sellado gracias a su mayor precisión de rodaje. Un efecto positivo en la eficiencia también se atribuye al hecho de que, para la lubricación, los rodamientos con elementos rodantes necesitan mucho menos aceite (generalmente, menos del 10 %) que los rodamientos hidrodinámicos, y menos aceite se mezcla con el refrigerante, lo que genera menos contaminación del aceite en los intercambiadores de calor. Por lo tanto, pueden conseguirse mejoras del 3 al 4 % en la eficiencia de los enfriadores usando rodamientos con elementos rodantes lubricados con aceite en lugar de rodamientos hidrodinámicos. Otro importante paso para mejorar la eficiencia puede conseguirse diseñando enfriadores exentos de aceite, basados en rodamientos magnéticos de SKF, o la solución de rodamientos de Lubricación por refrigerante puro (PRL) de SKF, tal como se describe en el folleto Evolving Chiller Performance de SKF y en el artículo de la revista Evolution.
Compresores de tornillo grandes para amoníaco
Recientemente, SKF ha estado fuertemente implicado en el diseño de una nueva generación de compresores de tornillo grandes para amoníaco y aplicaciones de refrigeración. El cliente, una empresa líder del sector, usaba generalmente rodamientos lisos hidrodinámicos con holguras relativamente grandes para soportar las cargas radiales, y rodamientos de bolas de contacto angular para las cargas de empuje. Normalmente se ensayan rodamientos de rodillos cilíndricos con tolerancias de holgura radial ajustadas como alternativa a los rodamientos hidrodinámicos. Esto mejora la eficiencia volumétrica del compresor y también puede reducirse el consumo de aceite del sistema.
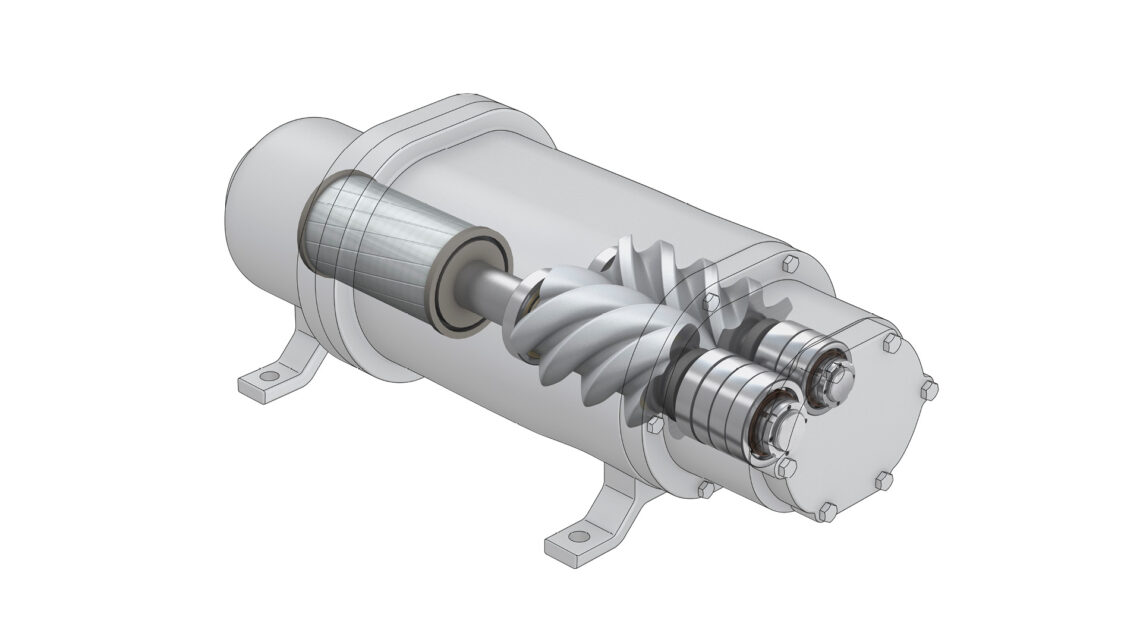
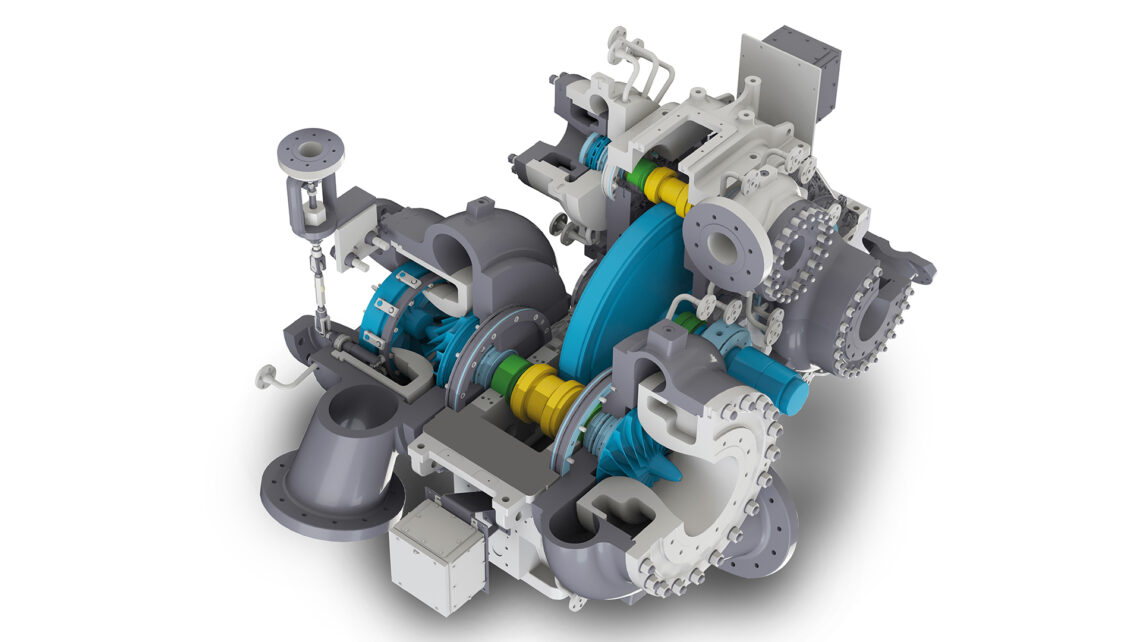
Esta imagen y la imagen principal, por cortesía de Atlas Copco Gas and Process.
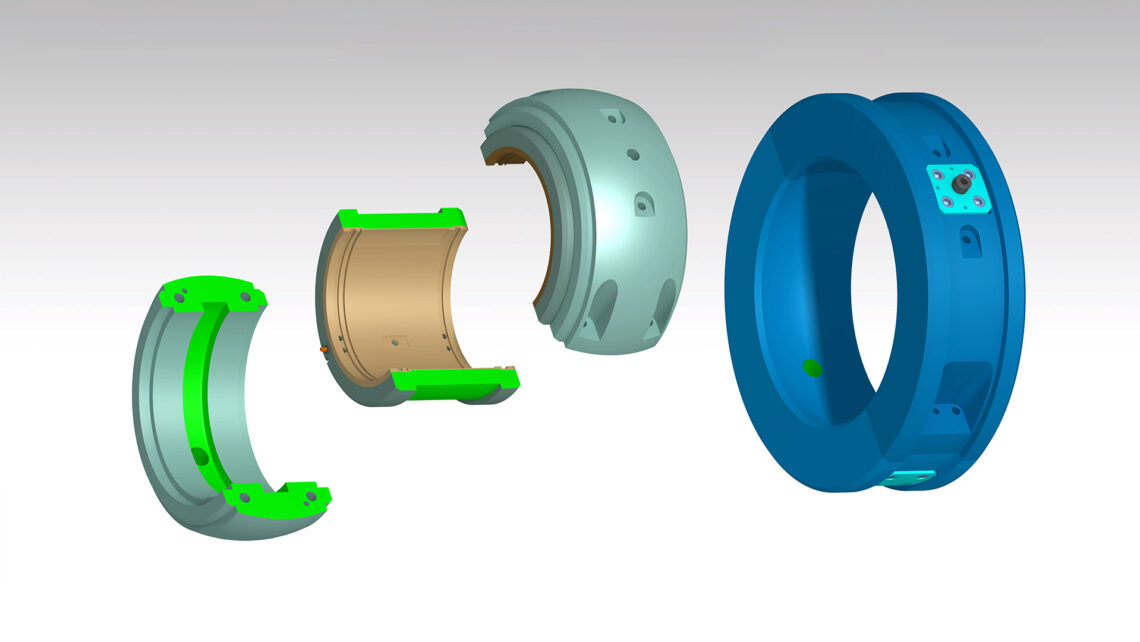
Beneficios de los rodamientos con elementos rodantes frente a las rótulas hidrodinámicas
- Su gran precisión de colocación permite valores de holgura bajos en los sellos e impulsores, lo que reduce las pérdidas de flujo (pérdidas volumétricas)
- Menor fricción de rodaje en los rodamientos
- Más apropiados para funcionamiento con arranques/paradas frecuentes o velocidades muy bajas (p. ej., sistemas de accionamiento de velocidad variable)
- Pueden afrontar viscosidades bajas y una alta dilución del aceite
- En general, se necesitan unos volúmenes de aceite lubricante un 90 % más bajos, y menos mantenimiento del sistema de aceite
- Reducción en la complejidad y el costo de todo el sistema
- Disposiciones de rodamientos más simples para cargas de empuje y cargas combinadas o grandes desalineaciones.
[1] J/E Bearing & Machine Ltd., “Plain or Rolling Bearings – Which is Best?”
[2] Vanhaelst R, Kheir A, Czajka J, “A Systematic Analysis of the Friction Losses on Bearings of Modern Turbocharger”, Combustion Engines 1/2016 (164), páginas 22 a 31.
[3] Morales G E, Hauleitner R, Wallin H H, “Tecnología de relubricación por refrigerante puro en compresores centrífugos sin aceite”, Evolution, 2 de marzo de 2017.
[4] “SKF GBLM – A New Rating Life Model Applied to Hybrid Bearings”, Evolution, 4 de febrero de 2021.