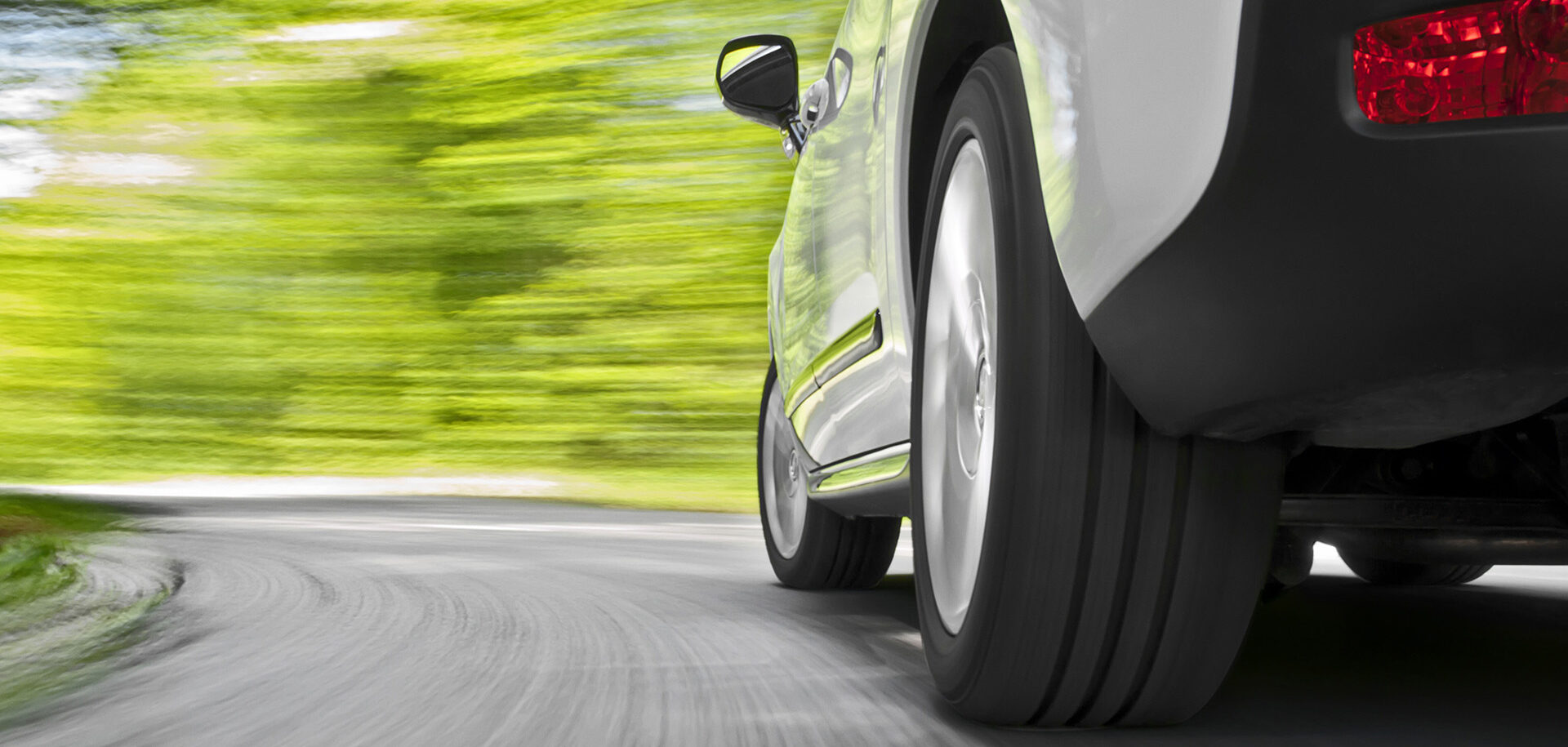
Más sostenibilidad con sellos eficientes
Un reto en el diseño de sellos es lograr la menor fricción posible y mantener, al mismo tiempo, la capacidad de sellado para conservar dentro los lubricantes y la contaminación fuera. Al reducir el par de fricción con la plataforma SKF Virtual Seal, se disminuye el consumo de energía y las emisiones de carbono.
Los sellos son un importante factor para reducir la fricción en los equipos rotativos –en algunas aplicaciones, en hasta el 60 % del par de fricción total. Desde hace varios años, disminuir el consumo de energía en todas las aplicaciones y sectores ha sido una tendencia internacional, y se prevé que se mantendrá durante muchos años más, como puede verse globalmente en el sector. Disminuir el par de fricción de los sellos es, por lo tanto, uno de los principales requisitos de los clientes para mejorar la eficiencia de los sistemas, reducir el consumo de energía y las emisiones globales de dióxido de carbono.
El principal reto para crear el diseño de sello óptimo es obtener la mínima fricción posible y, al mismo tiempo, mantener la capacidad de conservar el lubricante dentro e impedir la penetración de contaminantes en el sistema. Una normativa cada vez más estricta del CO2 se traduce en mayores requisitos de disminuir el nivel de fricción que genera el funcionamiento del sello propuesto.
Este artículo aborda principalmente las pérdidas por fricción del sistema de sello empleado, que repercuten indirectamente en el ámbito de la categoría de emisiones indirectas de alcance 3, según el Protocolo de Gases de Efecto Invernadero y, más exactamente, la subcategoría “Uso de productos vendidos”.
En la mayoría de las aplicaciones de SKF, las pérdidas de potencia por fricción, como parte de la categoría de emisiones indirectas de alcance 3, son el principal factor que contribuye a la liberación total de emisiones de CO2 de nuestros productos de rodamientos, tal como se muestra en este enlace.
Combinación inteligente de herramientas de simulación
Un pronóstico preciso del comportamiento de la fricción y temperatura de un sello exige una combinación de modelos avanzados de material, tribología, lubricación y disipación del calor. El Grupo de investigación e innovación global de SKF Seals ha desarrollado una moderna plataforma de simulación –SKF Virtual Seal (SAMBA)– que conecta el solucionador Abaqus FEA (análisis de elementos finitos) con las ecuaciones del modelo analítico propio de SKF Seals, y permite así predecir la generación de calor por fricción del sello y la evolución térmica del sistema (fig. 1).
SKF ha desarrollado un estimador de emisiones de CO2 que, cuando se conecta con el par de fricción y los resultados de temperatura obtenidos a través de SKF Virtual Seal, muestra cómo pueden obtenerse virtualmente soluciones de sellado más sostenibles con la ayuda de plataformas de simulación avanzadas.
SKF Virtual Seal, un enfoque de multifísica complejo
La evolución transitoria de la temperatura en un sistema de sello se estabiliza cuando hay un equilibrio entre la cantidad de calor generada por el par de fricción del sello y la cantidad de calor disipada a los alrededores del sistema. Por ello, para asegurar un pronóstico realista, es fundamental tener en cuenta conjuntamente el calor por fricción que se genera y la transferencia térmica. Más de cien variables involucradas en el pronóstico de par del sello son interdependientes, lo que incrementa aún más la complejidad de una modelización predictiva. La integración de las ecuaciones de modelización de SKF Virtual Seal en un paquete de análisis de elementos finitos (FEA) permite consolidar todas las variables interdependientes en cada incremento de tiempo en la simulación.
Para implementar los modelos complejos requeridos y sus interacciones con el solucionador FEA, se usan diversos procesos numéricos no estándares, lo que exige contar con aptitudes avanzadas. Hemos desarrollado una interfaz de usuario para facilitar y acelerar la implementación y el uso de la plataforma SKF Virtual Seal, cuyo cometido es hacer que el usuario disponga fácilmente de parámetros de aplicación específicos.
Una vez que se han definido los valores que se van a introducir en la interfaz, un script de Python modifica el modelo FEA estándar y conecta todos los parámetros a un procedimiento precompilado, donde se programan las ecuaciones analíticas. Esto también genera automáticamente, en segundo plano, la conexión bidireccional entre el solucionador FEA y las ecuaciones analíticas de SKF Virtual Seal. El siguiente paso del ingeniero es, entonces, ejecutar una simulación a través del software FEA, tal como se realiza comúnmente, excepto que, durante la simulación, se usa silenciosamente en segundo plano un solucionador semianalítico ahora actualizado.
Validación experimental
Hacia un rendimiento sostenible
El nivel de fricción pronosticado con SKF Virtual Seal puede convertirse en un nivel de emisiones de CO2 a través de la herramienta de sostenibilidad de SKF, el estimador de emisiones de CO2, para permitir un método virtual de selección del sello candidato mejor en su clase en función de un criterio de sostenibilidad tangible. Entonces, las emisiones debidas a pérdidas por fricción se calculan en función de la cantidad regional de emisiones de CO2 por kWh de energía para la ubicación geográfica elegida.
El beneficio de esta herramienta es que proporciona estimaciones y constituye un paso más en el incremento de la concientización partiendo de un método de medición concreto del impacto de nuestros productos.
De la teoría a la aplicación en el mundo real
Para destacar el potencial del pronóstico virtual de las emisiones de carbono en las fases iniciales de un proyecto, véanse los dos ejemplos concretos que siguen en los sectores automotriz y de ferrocarriles.
Caso de extremo de rueda automotriz
En este primer ejemplo, un fabricante del sector automotriz solicita un nuevo diseño de conjunto sellador de baja fricción para unidades de rodamientos para cubos de rueda (HBU). El requisito final es disminuir el 20 % en la fricción respecto de la generación anterior de conjuntos selladores para HBU.
En función de los resultados de simulación de SKF Virtual Seal, la optimización de la grasa para sellado pronostica una reducción de la fricción del 28 %:
- 0,33 Nm para la solución que utiliza la grasa original (grasa A)
- 0,24 Nm para la solución que utiliza la nueva grasa de baja fricción (grasa B).
Esta solución supera el objetivo de reducción de fricción del cliente. Además, resultados experimentales de pruebas de validación de productos confirman los pronósticos de SKF Virtual Seal, tal como se muestra en la fig. 3.
De par a emisiones de CO2
Introduciendo los resultados del par en el estimador de emisiones de CO2 de SKF, se puede obtener un valor aproximado de las mejoras de rendimiento de nuestra nueva solución de sellos para HBU en las emisiones de producto indirectas de alcance 3. Nuestra herramienta de sostenibilidad traduce las pérdidas de potencia por fricción en las emisiones esperadas de CO2. La comparación resultante entre la solución con los nuevos conjuntos selladores para HBU con una grasa optimizada y la solución existente para aplicaciones de extremos de rueda automotrices se muestra en la fig. 4.
Caso de aplicación de rodamientos de ferrocarriles
Este segundo ejemplo del mundo real procede de un nuevo programa de colaboración establecido entre un fabricante de equipo de ferrocarriles y SKF, con objeto de desarrollar un sistema de rodamientos completamente nuevo para la nueva generación de trenes regionales de una importante ciudad europea. El objetivo de la nueva unidad de rodamientos para trenes (TBU) es reducir la fricción en un 30 % en comparación con la generación anterior.
En el caso del sector automotriz antes mencionado, el nuevo diseño de sellos para TBU se ha mejorado con el soporte de la plataforma SKF Virtual Seal, con un pronóstico de reducción del nivel de fricción de un 44 %:
- 0,77 Nm en la solución original
- 0,43 Nm en la solución mejorada.
Tal como se muestra en la fig. 5, los resultados experimentales procedentes de las pruebas de validación del producto coinciden, una vez más, con los resultados predictivos de la modelización de SKF Virtual Seal.
De par a emisiones de CO2
De modo similar, nuestra herramienta de sostenibilidad convierte las pérdidas de potencia por fricción del sello para TBU en un pronóstico de emisiones de CO2. La comparación resultante entre la nueva solución de sellado para TBU y la solución original se muestra en la fig. 6.
Conclusión
La innegable urgencia de actuar ante el cambio climático desplaza cada vez más el centro de interés hacia la sostenibilidad. Por lo tanto, es de suma importancia debatir y aumentar la concientización de las partes involucradas en toda la cadena de valor, como proveedores, fabricantes y clientes, sobre el impacto ambiental de nuestros productos.
La sostenibilidad ambiental tiene una definición muy amplia, como se ha señalado en el alcance 3 del Protocolo de Gases de Efecto Invernadero. Los ejemplos en este artículo muestran una de las muchas medidas necesarias que ha adoptado SKF para reducir el impacto sobre el planeta mediante productos con menores emisiones de CO2, pero conservando la competitividad.
Parte de esta labor implica la creación de herramientas de cálculo basadas en la web, como la herramienta de sostenibilidad de SKF – estimador de CO2, y plataformas de modelización avanzadas, como SKF Virtual Seal, para calcular el impacto ambiental desde el diseño inicial hasta las fases de selección del producto y posteriores, preparando así el camino hacia métodos más ecológicos.