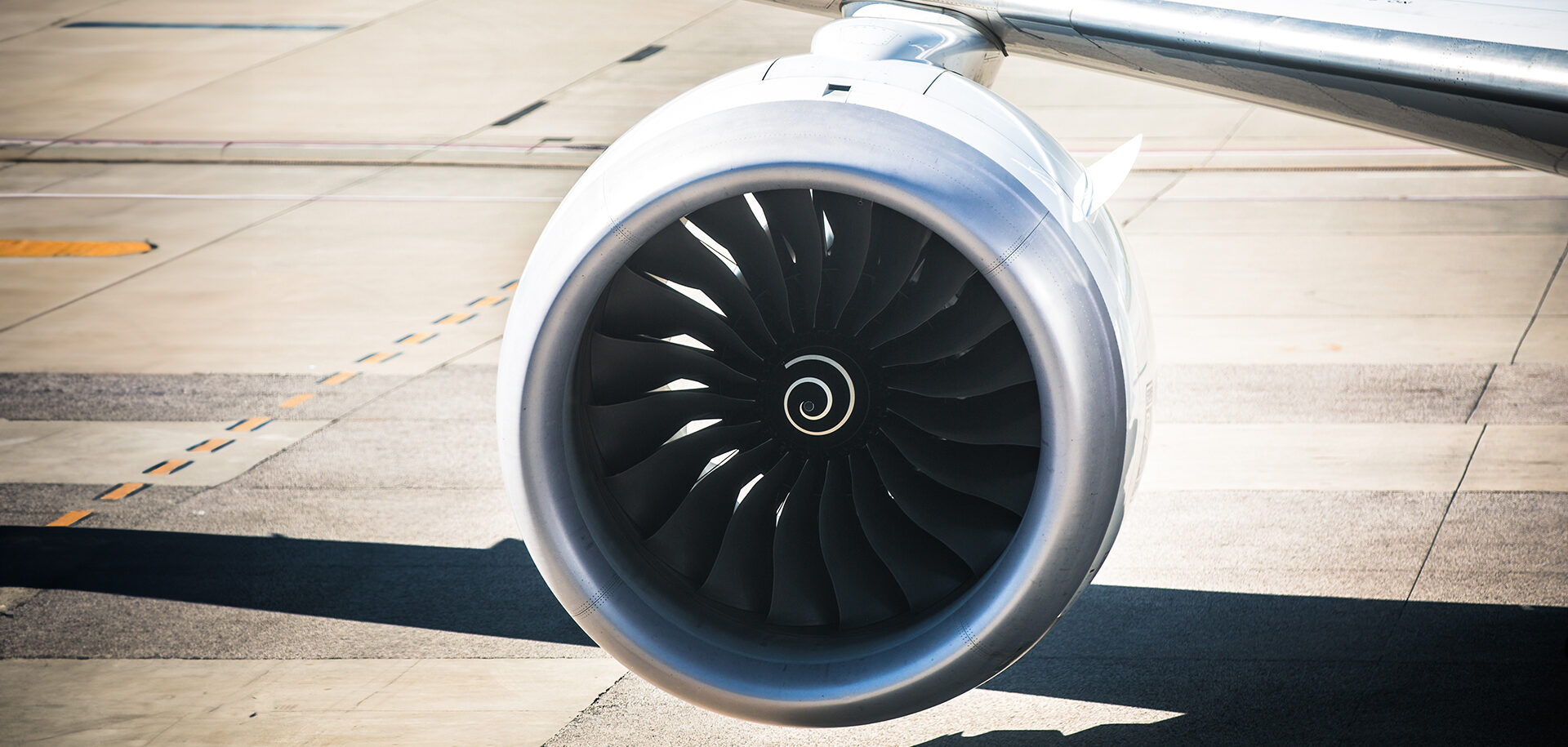
Innovación colaborativa para el futuro de la aviación
El Centro de desarrollo aeroespacial de SKF trabaja codo con codo con sus clientes para desarrollar tecnologías clave para los aviones del futuro.
El sector aeronáutico mundial ha atravesado años turbulentos. Primero, sufrió un colapso de la demanda de pasajeros debido a los confinamientos y las restricciones para viajar derivadas de la pandemia del coronavirus. Después, a medida que el mundo empezaba a volver a la normalidad, experimentó un enorme efecto rebote: solo en 2022, la cantidad de pasajeros de aviones aumentó un 47 %.
Según la Organización de Aviación Civil Internacional, la demanda de transporte aéreo de pasajeros superará los niveles anteriores a la pandemia en 2023. Los fabricantes de aviones informan que sus líneas de producción trabajan al máximo de su capacidad y las carteras de pedidos están llenas.
Aunque es una gran noticia, al sector de la aviación también le esperan desafíos importantes a más largo plazo, entre ellos los objetivos de sostenibilidad fijados por autoridades de todo el mundo. Sin embargo, a diferencia de muchos sectores, aún no se han identificado las soluciones técnicas necesarias para llegar a las cero emisiones en el transporte aéreo.
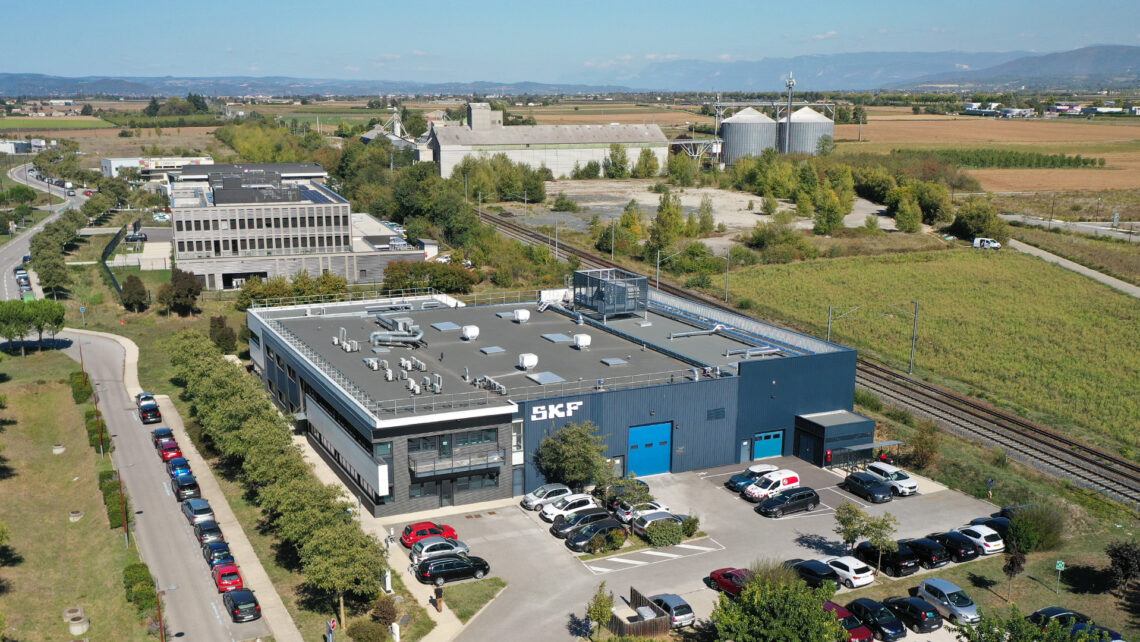
El papel clave de SKF como colaborador
SKF contribuye al desarrollo de la próxima generación de tecnologías aeroespaciales a través de su Centro de desarrollo aeroespacial, un centro de pruebas en Valence, Francia, cuyas instalaciones fueron modernizadas hace poco.
Muchos de los proyectos en los que estamos trabajando hoy probablemente se aplicarán en aviones construidos a partir de la década de 2030
Yves Maheo, director del Centro de desarrollo aeroespacial de SKF
Como afirma Paolo Andolfi, director de ingeniería aeroespacial de SKF: “por primera vez, disponemos de una instalación equipada para probar todos los componentes utilizados en un avión, tanto si se trata de movimientos de rodadura como de deslizamiento, componentes que giran a miles de revoluciones por minuto o que no se mueven en absoluto”.
El desarrollo de productos aeroespaciales es un proceso largo que exige una colaboración intensa. “Desarrollar una tecnología aeroespacial innovadora puede suponer hasta 10 años de trabajo”, explica Yves Maheo, director del Centro de desarrollo aeroespacial. “Muchos de los proyectos en los que estamos trabajando hoy probablemente se aplicarán en aviones construidos a partir de la década de 2030”. Y, a diferencia de otros sectores, los clientes finales participan en los proyectos de innovación desde una fase muy temprana.
“Colaboramos con nuestros clientes en todos los niveles”, continúa Maheo. “Nuestros clientes comparten con nosotros sus hojas de ruta tecnológicas, y nosotros compartimos las nuestras con ellos. Envían sus ingenieros aquí, a Valence, para trabajar con nuestros equipos en pruebas y proyectos de desarrollo”.
Esa relación de trabajo estrecha ayuda a SKF a garantizarse en cada proyecto una profunda comprensión de las necesidades de sus clientes. “Ejemplo de ello es Textilub, un nuevo compuesto textil autolubricante que se utiliza en los actuadores aeroespaciales”, explica Maheo. “Los aviones tienen una larga vida útil; inevitablemente, habrá piezas que se gasten y que habrá que sustituir. Gran parte de nuestro trabajo se ha centrado tradicionalmente en mejorar la durabilidad de esos componentes. Sin embargo, cuando hablamos con nuestros clientes, nos dicen que, aunque está bien alargar la vida útil de los componentes, lo que realmente les interesa son piezas que se desgasten de forma regular y predecible. De este modo, les resulta más fácil programar las revisiones y las sustituciones. Esta perspectiva la tendremos en cuenta en el desarrollo de materiales nuevos”.
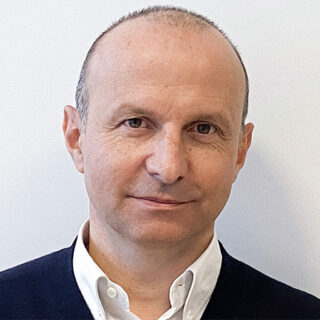
director de ingeniería aeroespacial de SKF
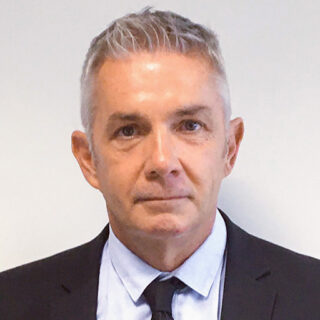
director del Centro de desarrollo aeroespacial de SKF
Híbridos avanzados
Otro foco actual de intensa investigación es el desarrollo de rodamientos para generaciones futuras de motores a reacción. Estos componentes forman parte del corazón de un avión moderno, ya que soportan el eje principal –que gira a gran velocidad– de los grandes motores turbofán.
Los motores modernos cuentan con más de 10 rodamientos a lo largo de su eje principal. La aparición de diseños de motores que incorporan una caja de engranajes entre el ventilador situado en la parte delantera del motor y los componentes del compresor situados detrás ha obligado a instalar rodamientos adicionales para soportar las grandes cargas.
Las capacidades de los rodamientos utilizados en un motor condicionan significativamente su rendimiento. Deben soportar cargas elevadas y velocidades de rotación altas, y funcionar de forma confiable durante mucho tiempo en un entorno hostil caracterizado por temperaturas elevadas. Además, los ingenieros, cuando definen la arquitectura de un nuevo diseño de motor, deben prever el espacio que ocuparán los rodamientos.
Por otra parte, cada diseño nuevo somete los rodamientos a cargas cada vez mayores en un intento de maximizar la eficiencia energética del espacio disponible. Esa evolución está llevando los diseños y materiales de los rodamientos existentes al límite de sus posibilidades físicas.
Un proyecto recién concluido en el que han participado expertos de todos los ámbitos de SKF ha permitido desarrollar un nuevo material que podría suponer un avance significativo en el rendimiento de los rodamientos futuros para motores. El proyecto ARCTIC (Tecnologías avanzadas de rodamientos para potenciar capacidades) fue financiado por la empresa común Clean Sky 2, en el marco del programa de investigación e innovación Horizon 2020 de la Unión Europea, con Rolls-Royce como principal patrocinador del proyecto.
“Hoy, los rodamientos que ofrecen el máximo rendimiento para los motores de aviación utilizan un diseño híbrido compuesto por elementos rodantes de cerámica y aros de acero”, afirma Alexandre Mondelin, ingeniero de desarrollo de productos de SKF. En estos diseños, explica, el límite del rendimiento del rodamiento viene determinado por la capacidad del aro de acero para soportar las elevadas tensiones de contacto generadas por las bolas cerámicas, que son más rígidas.
El proyecto ARCTIC tenía como objetivo crear una nueva aleación de acero combinada con elementos rodantes de cerámica capaces de soportar un incremento del 15 % en la tensión de contacto y del 25 % en la velocidad de rotación comparado con los aceros convencionales para rodamientos aeroespaciales. Desarrollar un material con estas características partiendo de cero supuso un desafío enorme. Los aceros utilizados en los rodamientos para motores actuales fueron desarrollados en la segunda mitad del siglo XX. “Tampoco es habitual desarrollar un acero nuevo pensado para una sola aplicación”, precisa Jean-Baptiste Coudert, ingeniero de desarrollo tecnológico de SKF.
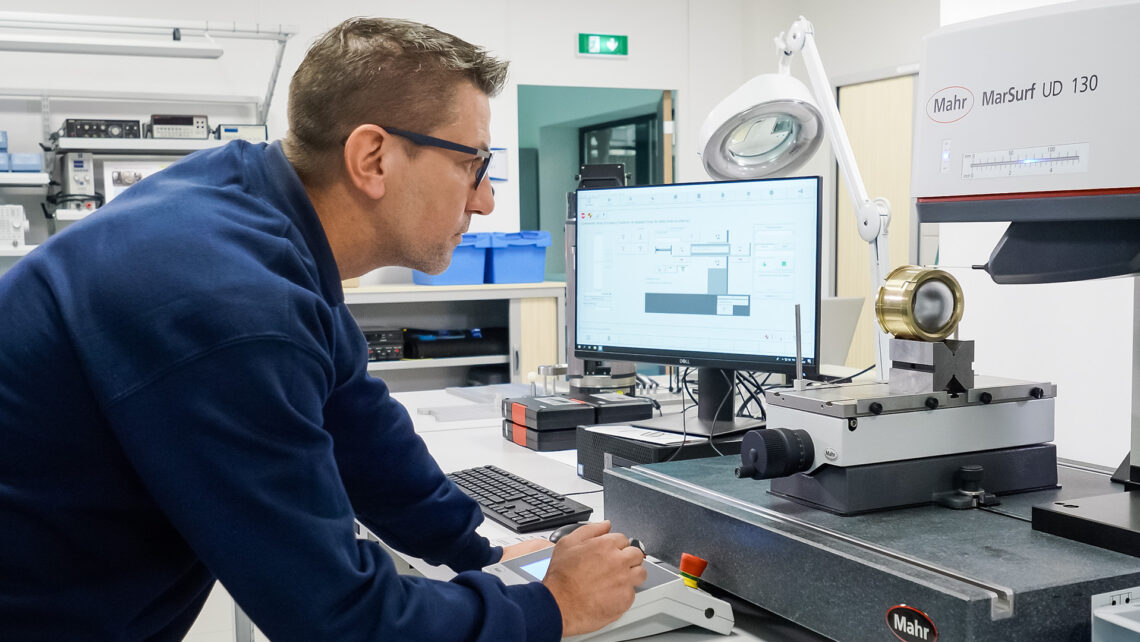
Una aleación innovadora
Para desarrollar el acero nuevo, un equipo del Centro de investigación y desarrollo tecnológico de SKF en los Países Bajos aportó décadas de experiencia en ciencia de materiales y, utilizando el software propio de simulación de materiales Thermo-Calc, probó docenas de formulaciones prototipo. También tuvo que idear un nuevo ciclo de tratamiento térmico y garantizar la viabilidad económica a escala industrial tanto del proceso de fabricación del material como del tratamiento térmico. A continuación, Yves Maheo y su equipo en Valence tuvieron que diseñar y construir un banco de pruebas nuevo capaz de funcionar a velocidades y potencias altas para probar a escala real los rodamientos del eje principal fabricados con el acero nuevo.
La aleación definitiva, patentada y denominada ARCTIC15, cumplió todos los objetivos del proyecto. Un aumento del 15 % en la capacidad de carga puede parecer modesto, pero se traduce en un aumento significativo del rendimiento del motor. Los rodamientos híbridos fabricados con el acero nuevo pueden soportar un 50 % más de carga que los diseños convencionales, lo que permite reducir el diámetro tanto de los rodamientos como del eje principal.
Aplicando esta tecnología al diseño actual, se consiguió reducir las pérdidas de potencia en hasta un 25 %, con el consiguiente ahorro de peso al poder reducir las dimensiones de los sistemas de lubricación y refrigeración. Las posteriores optimizaciones del diseño podrán aumentar la densidad de potencia y allanar el camino para mejorar la eficiencia de consumo de combustible y reducir las emisiones de dióxido de carbono y óxidos de nitrógeno entre un 25 y un 30 % (objetivos del cliente).
En las pruebas, ARCTIC15 demostró una serie de beneficios adicionales. Dura más que los aceros convencionales, especialmente en condiciones de lubricación deficiente o sin aceite. Además, los rodamientos cerámicos híbridos ARCTIC15 generan menos vibraciones que los rodamientos tradicionales, y esto se traducirá, a su vez, en mejoras del rendimiento y la confiabilidad globales del motor.
Actualmente, SKF está trabajando con Rolls-Royce para industrializar la solución, al que seguirán pruebas de los rodamientos híbridos ARCTIC15 en los prototipos de Rolls-Royce de su motor turbofán con engranajes de próxima generación para la aviación civil, el UltraFan® H2.
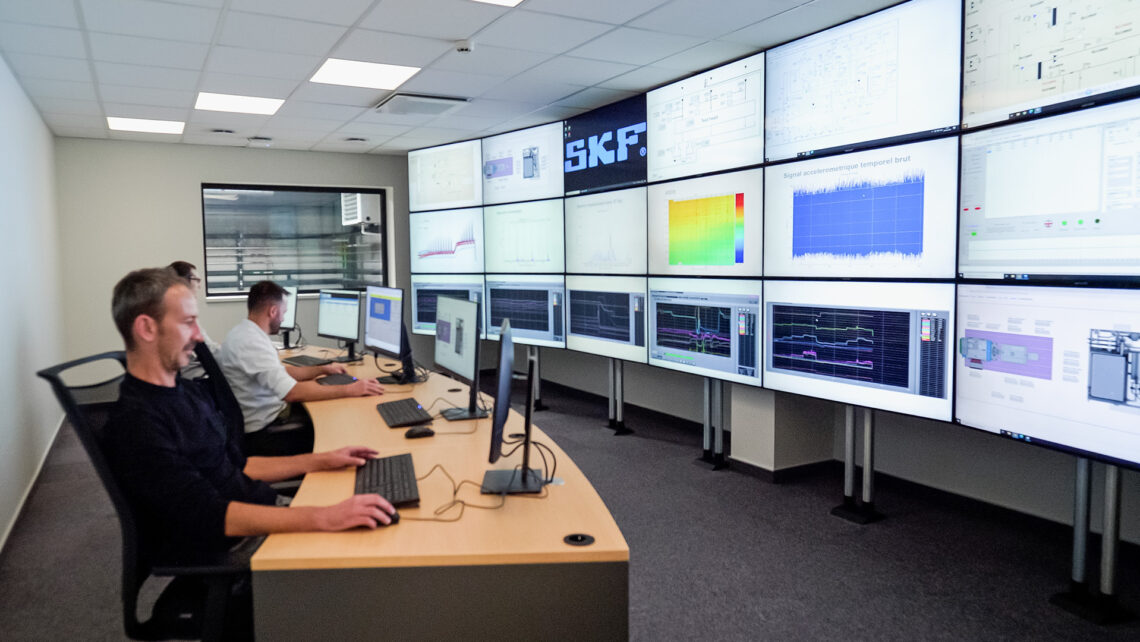
Crece el volumen de pasajeros
El sector aéreo fue uno de los más perjudicados por la pandemia del coronavirus, ya que las restricciones para viajar impuestas en todo el mundo provocaron un colapso de la demanda de vuelos. Ahora, tres años después de los primeros confinamientos, la mayoría de los países han levantado las últimas restricciones que quedaban sobre el movimiento de personas. Incluso China, que impuso algunas de las normas más estrictas, anunció en marzo de 2023 que volvería a las normas anteriores a la pandemia en materia de visados para turistas extranjeros y viajeros de negocios.
El resultado ha sido una explosión de la demanda de vuelos. En 2022, la cantidad de pasajeros de aviones aumentó un 47 % respecto del año anterior, y el total de pasajeros-kilómetro creció un 70 % al popularizarse nuevamente los vuelos de larga distancia.