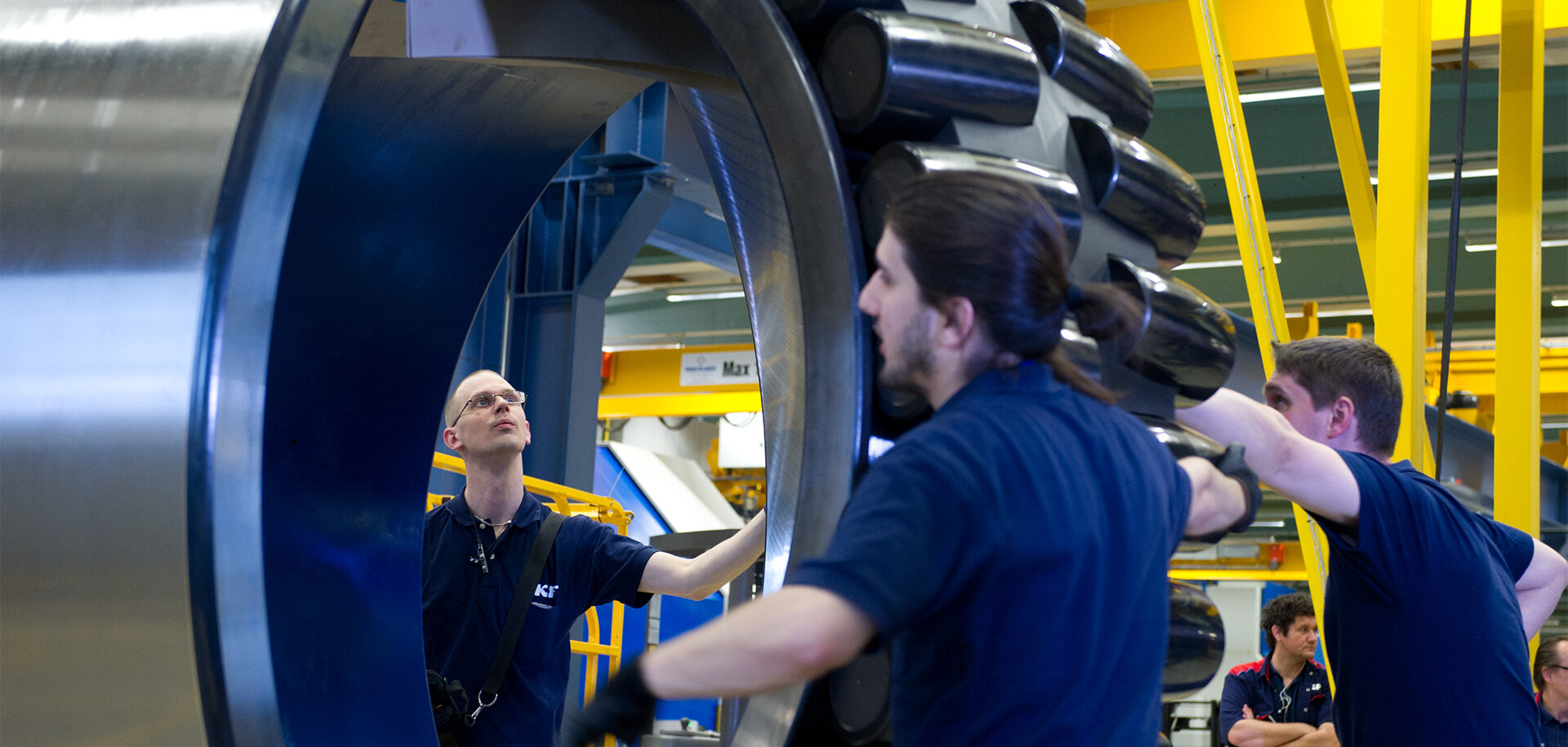
Mejor rendimiento con rodamientos revestidos
Los revestimientos incrementan al máximo la vida útil y el rendimiento de los rodamientos y rótulas, y pueden satisfacer condiciones operativas y requisitos de rendimiento de la aplicación muy diversos. Actualmente SKF ofrece más de 35 revestimientos especiales diferentes.
Hoy en día se espera que un rodamiento pueda utilizarse y girar casi indefinidamente si se cumplen tres condiciones operativas: 1) las tensiones aplicadas se mantienen por debajo de un cierto valor; 2) lubricación adecuada; y 3) ninguna contaminación. Naturalmente, en algunos casos, una aplicación puede distar mucho de ser ideal, y surgir problemas inesperados que incrementen los costos operativos y de mantenimiento.
Para mejorar la vida útil y el rendimiento de un rodamiento, se han desarrollado diferentes estrategias cuando las condiciones existentes no son las ideales. Una de ellas es el uso de revestimientos, que pueden proporcionar una amplia gama de características, entre ellas:
- resistencia al desgaste
- incremento o reducción de la fricción
- resistencia a la corrosión
- propiedades de deslizamiento y rodadura de emergencia
- lubricación mejorada o menor necesidad de lubricación durante períodos de funcionamiento
- propiedades humectantes mejoradas del lubricante
- aislamiento eléctrico
- barrera de hidrógeno
- prevención de la corrosión por contacto
- mejora del aspecto estético
El revestimiento de un substrato de acero para rodamientos estándar con materiales que desempeñen las funciones deseadas puede mejorar significativamente el rendimiento de todo el rodamiento. Los rodamientos revestidos también pueden utilizarse para compensar la diferencia entre el acero para rodamientos estándar y los rodamientos híbridos de cerámica. En algunas aplicaciones, los elementos rodantes de cerámica son una buena solución, aunque costosa y, en ciertos casos, no disponible comercialmente. Entonces el funcionamiento de los rodamientos estándares puede alcanzar el nivel adecuado aplicando revestimientos.
Algunos revestimientos se depositan en capas muy delgadas, lo que proporciona una importante ventaja. Un espesor de solo unas pocas micras permite utilizar rodamientos estándares del canal de producción, sin el gasto de modificar los parámetros de producción de mecanizado.
Resumen de tecnologías de revestimiento
SKF utiliza diferentes tecnologías de revestimiento, tal como puede verse en la fig. 1. Pueden dividirse en tres categorías principales:
- Procesos en estado gaseoso, donde el material de revestimiento se somete a una fase gaseosa o de vaporización antes de depositarse en la superficie. Pueden constar de procesos de deposición por vacío, como deposición de vapor físico (physical vapour deposition, PVD), y deposición química de vapor asistida por plasma (plasma-assisted chemical vapour deposition, PACVD).
- Procesos en estado de disolución, en los que el material de revestimiento está presente en una fase líquida antes de ser depositado como sólido en la superficie. Los métodos pueden dividirse en las categorías de deposición química (por ejemplo, deposición no electrolítica, conversión química, reacciones químicas homogéneas e inmersión y rociado líquido), deposiciones electroquímicas, como la deposición galvánica de un revestimiento metálico en un electrodo mediante un proceso electrolítico.
- Procesos en estado de fusión, donde el material de revestimiento está fundido o semifundido (reblandecido) antes de ser depositado como sólido sobre la superficie mediante el uso de una fuente de alta energía. Los métodos se dividen en deposición por rociado (que abarca una amplia gama de técnicas en las que la temperatura del material se eleva rápidamente en un medio gaseoso caliente y se proyecta simultáneamente a alta velocidad sobre una superficie para obtener un revestimiento), y recubrimiento mediante tecnología de láser.
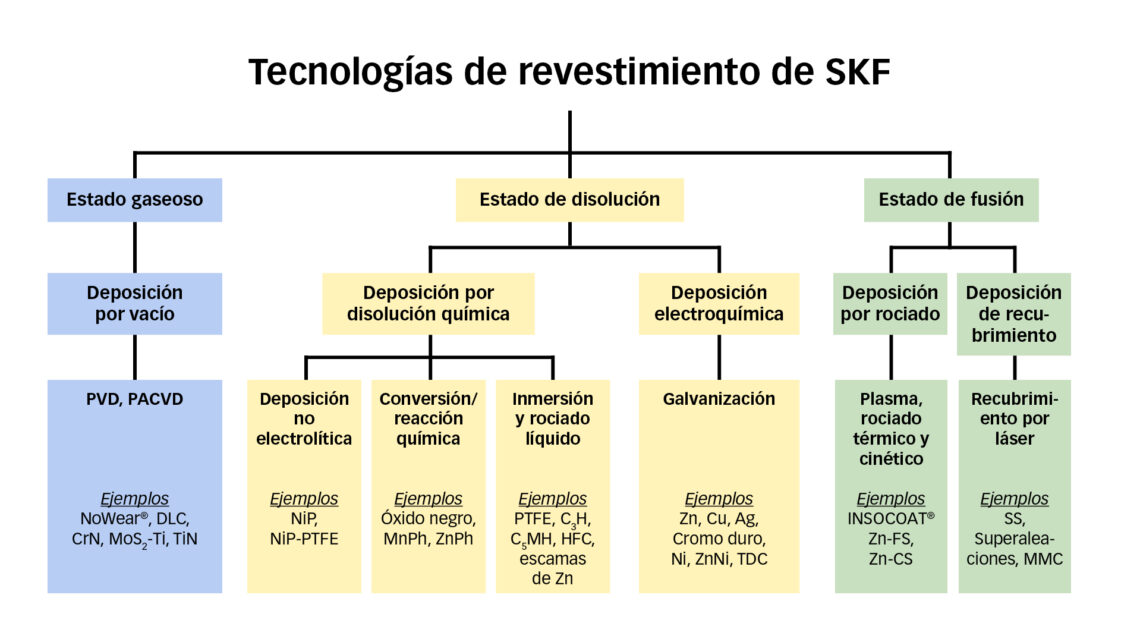
El mundo de revestimientos de SKF
SKF tiene una cartera de más de 35 modernos revestimientos que pueden usarse en un gran número de aplicaciones o diferentes piezas de sus rodamientos. Todos los revestimientos se han optimizado para las demandas concretas de los rodamientos y se basan en especificaciones exactas y un estricto control de la calidad. Se fabrican en instalaciones del más alto nivel, que frecuentemente superan los estándares habituales de equipo y revestimiento, y proporcionan lo máximo en calidad, confiabilidad y repetibilidad.
Algunos revestimientos se depositan en capas muy delgadas, lo que proporciona una importante ventaja
En este artículo, presentaremos algunos de los revestimientos de SKF más frecuentemente usados. La lista completa de revestimientos de SKF, junto con sus propiedades físicas y tribológicas y todas las aplicaciones, se ha publicado recientemente en el catálogo en línea de revestimientos, SKF Coatings.
Rodamientos
En los rodamientos, la fig. 2 muestra los 12 principales revestimientos que proporcionan cinco funciones importantes en aplicaciones de los elementos rodantes, que incluyen antidesgaste por deslizamiento en jaulas, aislamiento eléctrico, anticorrosión por contacto, anticorrosión y antidesgaste en caminos de rodadura.
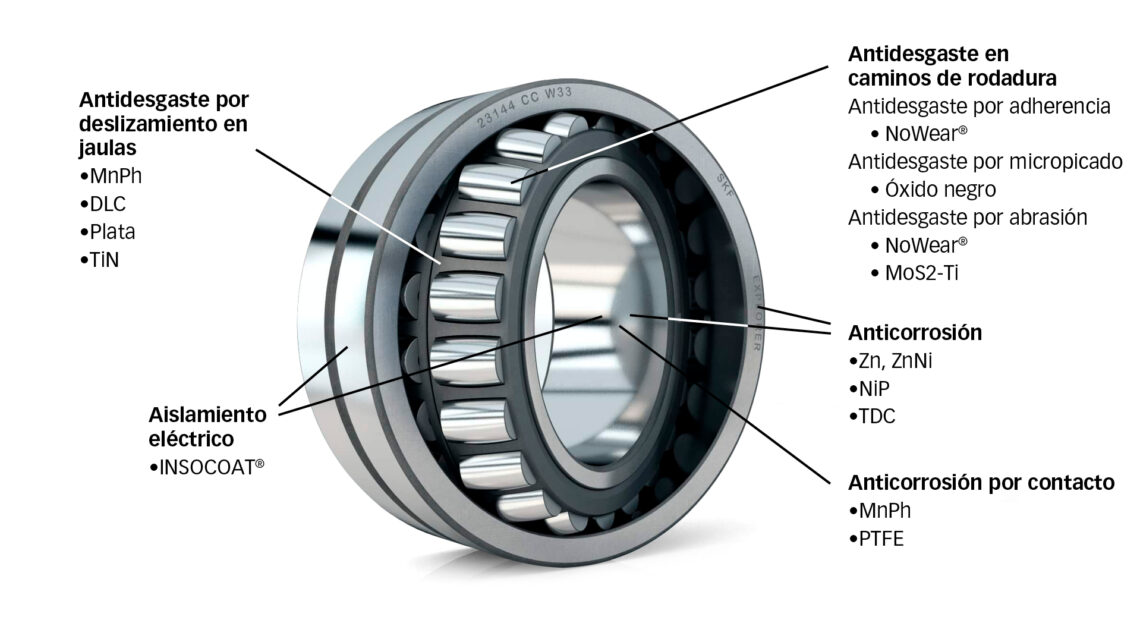
a. Antidesgaste en caminos de rodadura
Óxido negro: Es un tratamiento superficial en el que tiene lugar una reacción química en la superficie del acero para rodamientos. Todos los componentes de la superficie del rodamiento están revestidos. Las piezas se sumergen en diferentes soluciones acuosas alcalinas de sal a temperaturas del intervalo 140–150 °C. La reacción entre el hierro de la aleación de acero y los reactivos produce una capa negra de un espesor de aproximadamente 1 μm compuesta de una mezcla bien definida de FeO, Fe2O3 and Fe3O4. Ofrece muchas ventajas, como la reducción al mínimo del desgaste adhesivo y por deslizamiento. También mejora el rodaje al promover una superficie muy lisa, por lo que proporciona una fricción final de régimen estable inferior a la de los rodamientos sin revestir. Otra ventaja es el incremento de la adhesión del aceite a la superficie, lo que da como resultado una ligera protección contra la corrosión. El óxido negro también es una barrera contra el hidrógeno, que protege el acero subyacente. Además, la capa incrementa la resistencia contra micropicado, adherencia, desconchado, corrosión por contacto y la formación de grietas en la superficie y fatiga prematura. Finalmente, la capa protege la superficie contra aditivos para presiones extremas (extreme pressure, EP) que son nocivos y que frecuentemente se usan en lubricantes para cajas de engranajes de turbinas eólicas.
NoWear®: SKF fue la primera empresa del mundo en utilizar revestimientos a base de carbono en los rodamientos. Pueden revestirse todos los componentes de la superficie de los rodamientos, pero los mejores resultados se obtienen revistiendo solamente los rodillos. Las piezas se introducen en una cámara de vacío donde se usa un método de PACVD, con reacciones químicas y físicas en presencia de plasma que produce una mezcla de vapor de carbono+metal que se condensa en la pieza de trabajo a temperaturas inferiores a 180 °C. El revestimiento gris oscuro amorfo resultante, que tiene un espesor de unos 3 μm, una dureza moderada y fricción muy baja incluso en estado seco, se optimiza para utilizarse en caminos de rodadura de rodamientos sometidos a presiones de contacto elevadas. NoWear®, patentado en 1999, reduce la adhesión, la adherencia, la fatiga de la superficie y el micropicado, y asegura un desgaste muy bajo en situaciones de lubricación deficiente. Además, el avanzado revestimiento multicapa contiene una subcapa especial para incrementar la adhesión y una capa superior grafítica para mejorar el rodaje.
MoS2+Ti: Es una capa amorfa de bisulfuro de molibdeno (MoS2) dopada con titanio (Ti) de un espesor de 1–3 μm, y una dureza similar a NoWear®, pero diseñada especialmente para que su fricción sea muy baja y tenga alta resistencia al desgaste en entornos secos, de vacío y recintos limpios. Las piezas se introducen en una cámara de vacío donde se utiliza un método de PVD, con reacciones físicas en presencia de un plasma que produce un vapor que se condensa en la pieza de trabajo a temperaturas inferiores a 180 °C.
b. Anticorrosión
Zn y ZnNi: El zinc y la aleación de zinc-níquel son capas del orden de 1–15 μm de espesor, depositadas con métodos electrolíticos, y pasivadas posteriormente para incrementar la protección. En general, se usan en aplicaciones sin camino de rodadura. Aun cuando el zinc ha sido el enfoque tradicional, la aleación con níquel, con fines anticorrosivos, ha superado algunos de los inconvenientes de los revestimientos de zinc puro, como su baja dureza. Además de sus propiedades anticorrosivas, el zinc proporciona una alta fricción que puede usarse con efectos antideslizamiento o anticorrosión por contacto en superficies externas, para diámetros externos o internos, o para los agujeros de los soportes de rodamientos.
NiP: La aleación plateada de níquel-fósforo con espesores del orden de 10–50 μm se deposita con un método autocalítico no electrolítico. Hay tres versiones con diferentes concentraciones de fósforo, entre el 6 % y el 14 %. Un incremento de fósforo mejora las propiedades anticorrosivas pero es perjudicial para la dureza y resistencia al desgaste. Generalmente, se usa en aplicaciones sin caminos de rodadura, donde se precisa una combinación de propiedades anticorrosivas y antidesgaste. También puede utilizarse en caminos de rodadura con espesores inferiores a 3 μm.
TDC (cromo denso delgado): Es una capa de cromo policristalino plateada de un espesor de 2-5 μm. El revestimiento se aplica mediante electrolisis, con un electrolito ácido de cromo. El proceso se cataliza posteriormente, por ejemplo, con dicromato de potasio, para formar una capa delgada de cromo de estructura nodular. Las capas de TDC pueden aplicarse en caminos de rodadura y superficies externas de los rodamientos. Además de buena resistencia a la corrosión, el revestimiento tiene una alta dureza, baja fricción y elevada resistencia al desgaste.
c. Anticorrosión por contacto
PTFE: Es un revestimiento polimérico de 10–20 μm de espesor. Se aplica politetrafluoroetileno (PTFE) en polvo por la superficie mediante atomizador de aire o rociado electrostático, y la capa se forma mediante un proceso de sinterización térmica. Tiene unas propiedades de deslizamiento excelentes, fricción muy baja y propiedades anticabeceo. Proporciona rodamientos con poderosas características anticorrosión por contacto permanentes en diámetros interiores o exteriores de aros de rodamiento.
d. Aislamiento eléctrico
INSOCOAT®: Es una capa de óxido de aluminio aislante de la electricidad de unos 100–300 μm de espesor aplicada en un proceso atmosférico de rociado con plasma. Partículas fundidas de Al2O3 se rocían sobre el substrato de acero, y posteriormente se sella la estructura porosa. Un paso adicional de rectificado de acabado contribuye a dar las dimensiones correctas al rodamiento. El revestimiento se aplica sobre las superficies externas del aro exterior del rodamiento o la superficie interna del agujero del aro interior. Las principales ventajas de INSOCOAT® tienen que ver con el aislamiento eléctrico que evita el paso de la electricidad por el rodamiento, que causa erosión en las superficies de rodadura.
e. Antidesgaste por deslizamiento en jaulas
Ag: Se depositan capas de plata (Ag) de espesores del orden de 2-4 μm mediante métodos galvánicos, normalmente con una subcapa de cobre para incrementar la adhesión. Es una capa de metal blando con propiedades de lubricación en seco usada a altas temperaturas y en entornos en vacío. Posee una conductividad eléctrica excelente y una buena protección contra la corrosión de productos químicos (moderadamente alcalinos y ácidos). Se usa principalmente para platear jaulas de acero y, en casos poco frecuentes, aros y rodillos en ciertas aplicaciones exigentes, como lubricación en seco en aplicaciones en vacío, de alimentos y aeroespaciales.
TiN: Los revestimientos de nitruro de titanio (TiN) son capas de color dorado con espesores del orden de 1–5 μm. Las piezas se introducen en una cámara de vacío donde se utiliza un método de PVD, con reacciones físicas en presencia de un plasma de nitrógeno que produce un vapor, que se pulveriza desde un objetivo de titanio y se condensa en la pieza de trabajo a temperaturas inferiores a 180 °C. Se usan como revestimientos resistentes al desgaste en jaulas, en presencia de lubricantes y manguitos revestidos para la industria de los alimentos.
Rótulas
En el caso de las rótulas, en la fig. 3 se enumeran los principales ocho revestimientos que proporcionan tres importantes funciones en aplicaciones con estas rótulas: revestimientos anticorrosivos y antidesgaste en rodamientos con o sin lubricación con grasa.
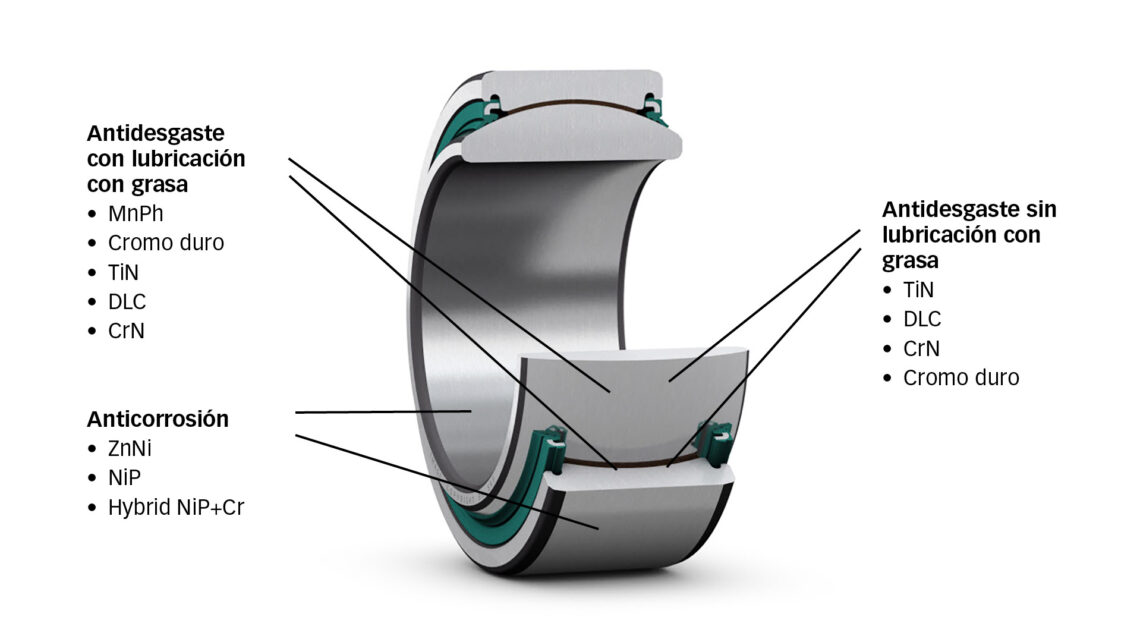
a. Antidesgaste sin lubricación con grasa
Cromo duro: Es una capa de cromo (Cr) duro plateada de un espesor del orden de 3–15 μm depositada mediante un proceso de electrodeposición con electrolito ácido de cromo. El proceso finaliza con limpieza, eliminación de cromo hexavalente [Cr(VI)] y preservación de aceite. El revestimiento proporciona un buen contacto deslizante entre componentes de rótulas, con alta dureza y elevada resistencia al desgaste. La capa de cromo resultante tiene microgrietas, lo que significa que, en pequeños espesores, tiene unas propiedades anticorrosivas limitadas.
CrN: El nitruro de cromo (CrN) es una capa de color gris plateado depositada mediante PVD en espesores del orden de 1–6 μm. Las piezas se colocan en una cámara de vacío, en donde objetivos sólidos de cromo puro se bombardean con plasma de iones de Ar+N que vaporizan el material de Cr (proceso de “pulverización”). Los átomos de Cr se combinan con el N y se condensan sobre las piezas de trabajo mantenidas a menos de 180 °C. El resultado es un revestimiento duro que funciona bien en aplicaciones antidesgaste por deslizamiento y también en algunos entornos corrosivos. Puede usarse asimismo en aplicaciones de rodamientos que combinan aros revestidos de CrN y rodillos revestidos de NoWear®. También puede emplearse como subcapa de otros revestimientos para incrementar el soporte a la presión de contacto.
DLC (carbono tipo diamante): Es el nombre genérico de un grupo de revestimientos a base de carbono con composiciones que contienen una mezcla de microestructuras de grafito y diamante. Pueden incluir o no hidrógeno, y su espesor es normalmente de entre 2 y 4 μm. Las piezas por revestir se colocan en una cámara de vacío, donde se aplican varias capas sobre las superficies del componente de rodamiento mediante procesos de PVD o PACVD, según la aplicación. Su composición influye en las propiedades de los revestimientos. Los de DLC se han creado para situaciones de gran desgaste y lubricación deficiente. Poseen una gran resistencia al desgaste por deslizamiento y desgaste adhesivo, capacidad de soportar cargas elevadas, excelente protección contra la abrasión, y protegen la superficie en condiciones de lubricación deficiente. Los revestimientos de DLC son ideales para rótulas, mecanismos de accionamiento lineal de rodamientos, ejes de rodamientos, casquillos, pasadores de rodillos de leva con eje y piezas deslizantes en rodamientos (como jaulas y sellos). El avanzado revestimiento NoWear® de carbono-metal también pertenece a esa familia de revestimientos a base de carbono; sin embargo, existen ciertas diferencias. Los valores de dureza de los revestimientos de DLC para aplicaciones deslizantes son del orden de 18–30 GPa (1800–3000 HV), mientras que los valores de los revestimientos NoWear® (usados en aplicaciones rodantes) son de unos 12 GPa (~ 1200 HV).
b. Antidesgaste con lubricación con grasa
MnPh: El fosfato de manganeso (MnPh) es una capa entre gris y negra de un espesor del orden de 2–15 μm. El revestimiento se efectúa mediante una reacción química, y normalmente se revisten todas las superficies de las piezas de trabajo. Las piezas se sumergen en un fluido fosfatado de manganeso, y el hierro de la pieza de trabajo reacciona con los cationes de manganeso y aniones de fosfato en el fluido. El revestimiento posee propiedades antidesgaste y anticorrosión por contacto, lo que mejora significativamente la resistencia a la adherencia y el micropicado. También protege en condiciones de valores kappa bajos y lubricación deficiente, y proporciona una mejor adhesión del aceite. Además, el MnPh ofrece una buena protección contra la corrosión (en estado aceitado) y posee buenas propiedades de aislamiento eléctrico.
c. Anticorrosión
Hybrid NiP+Cr: Se trata de una bicapa dura de color plateado de revestimientos de níquel-fósforo y cromo, de un espesor del orden de 10–30 μm. Todo el proceso de revestimiento consiste en dos partes separadas. Primero se recubre la superficie mediante niquelado por vía química para mejorar la protección contra la corrosión y conferir resistencia química, y luego con una capa de cromo duro mediante deposición electrolítica que añade resistencia mecánica.
Los revestimientos son el camino hacia la sostenibilidad
En el sector de los rodamientos, la sostenibilidad abarca aspectos como la conservación de la energía y los recursos, la reducción al mínimo de los desechos, la mejora de la eficiencia de los procesos, y el uso de materiales renovables. Como líder tecnológico global, SKF considera la transformación técnica actual como una responsabilidad y una gran oportunidad. La reutilización de los materiales y componentes industriales, como el aceite y los rodamientos, es un buen comienzo. La oferta –desde sellos y rodamientos hasta componentes y sistemas industriales de importancia clave– puede contribuir, por ejemplo, a desarrollar soluciones livianas y de baja fricción para el sector automotriz que pueden reducir las emisiones de CO2. Otro enfoque sostenible es aprovechar las tecnologías de revestimiento, que en algunas aplicaciones reducen la fricción (y, por tanto, el consumo de energía) y prolongar la vida útil de los rodamientos, lo que disminuye el consumo de nuevas materias primas.
Observaciones finales
El interés por el uso de revestimientos en aplicaciones de rodamientos aumenta. Al seleccionar materiales y arquitecturas de revestimiento, es posible personalizar propiedades físicas, mecánicas y tribológicas únicas para atender las crecientes demandas tecnológicas. Particularmente, los revestimientos de SKF se han analizado cuidadosamente para que proporcionen propiedades óptimas, y, en algunos casos, los procesos se han ajustado más allá de las normas DIN e ISO, según las diferentes aplicaciones.
Este artículo se ha concentrado en exponer brevemente algunos de los diferentes tipos de revestimientos de SKF, para aclarar algunas cuestiones sobre la terminología, los aspectos técnicos y el diseño de los revestimientos. Puede obtenerse más información en nuestro catálogo de revestimientos, SKF Coatings.