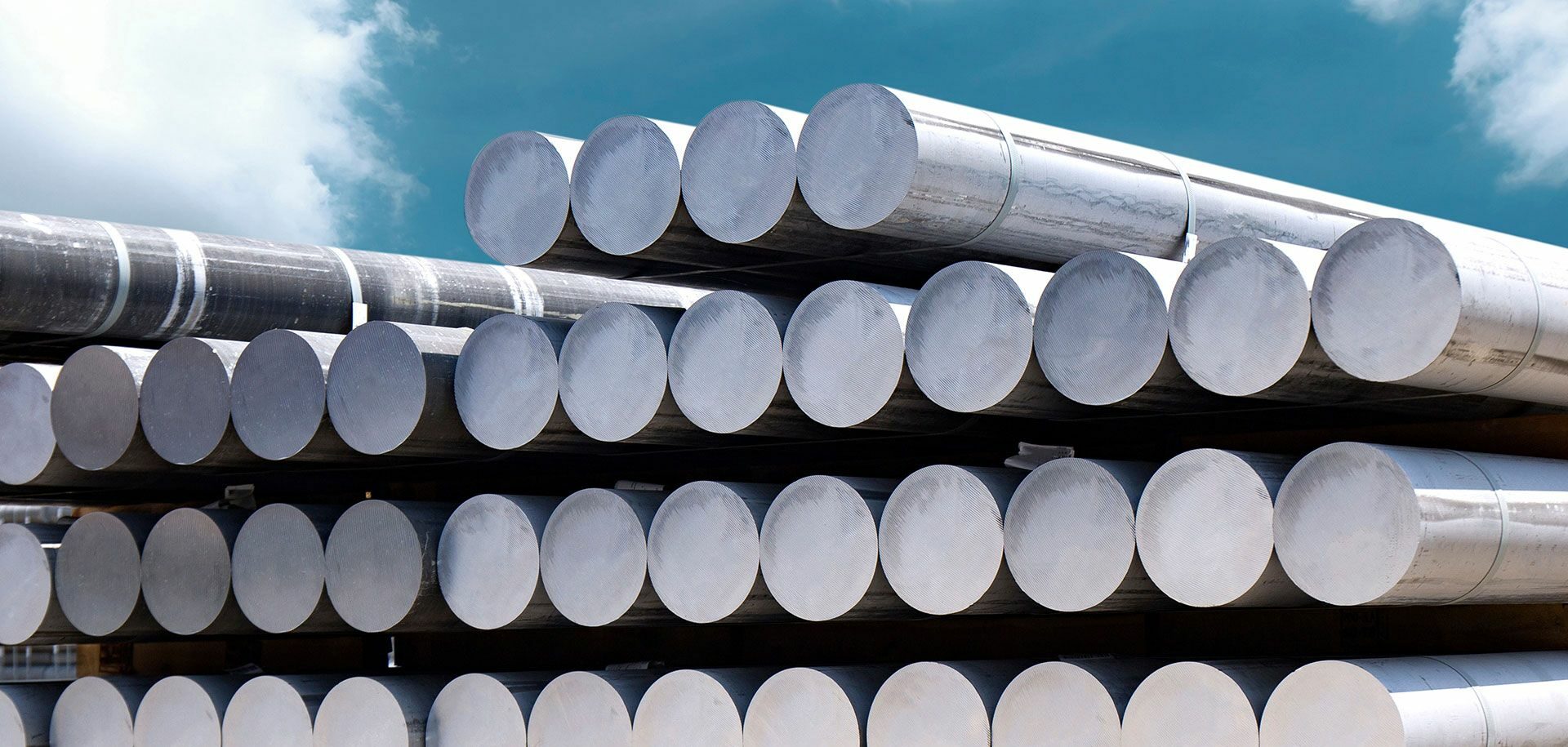
Rapsodia rumana
La filosofía que SKF plantea en ingeniería de la confiabilidad está dando buenos resultados a uno de los productores más importantes de aluminio de Europa.
ALRO –la sigla de Aluminium Romania– es uno de los más grandes productores de aluminio de Europa y una de las empresas industriales más importantes de Rumania. Da empleo a más de 3 400 personas que trabajan en tres centros de producción repartidos por el país. Los dos centros que se encuentran en Slatina incluyen una fundición, un centro de I+D e instalaciones de procesamiento (rectificadores, una planta de ánodos, una nave de colada, trenes de laminación en frío y caliente, y un taller de extrusión). La refinería de alúmina, integrada en el Grupo ALRO, está situada en Tulcea, Rumania, cerca del Delta del Danubio y del Mar Negro.
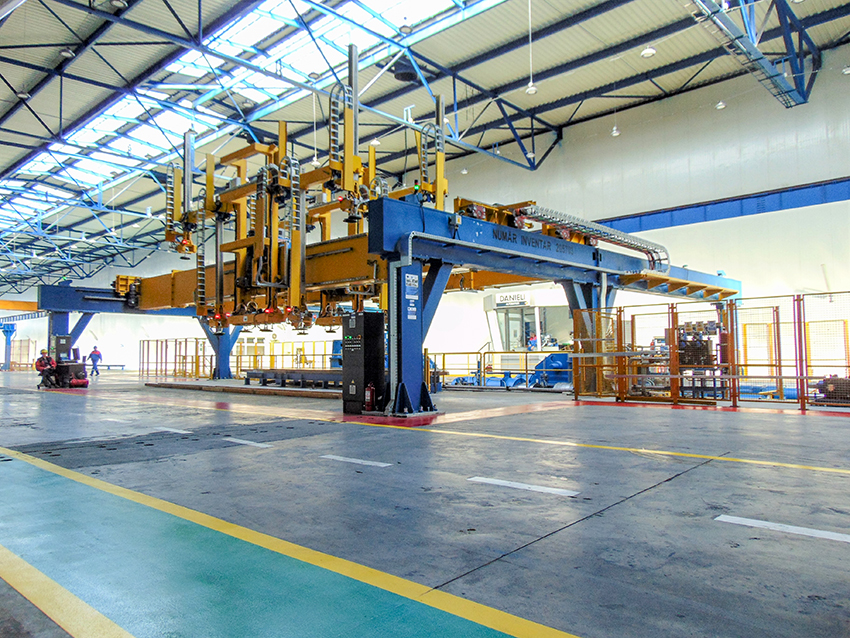
La planta ocupa un área importante de Slatina y consume el 5% de la producción total de electricidad de Rumania. Fabrica productos primarios de aluminio como alambrón, tochos y planchas, y productos semifabricados como placas, láminas, bobinas, flejes y perfiles. A través de distintas innovaciones y desarrollos, ALRO ha creado una cartera de productos que cubre las necesidades de más de 300 clientes en todo el mundo, en los sectores de cables y conductores, construcción, automoción, aeronáutica e ingeniería.
SKF ha transformado nuestro enfoque del mantenimiento.
Gheorghe Dobra, director ejecutivo de ALRO
“Gracias a nuestros logros recientes en el control de costos para potenciar la eficiencia operativa y a la implementación de programas ambiciosos para aumentar la capacidad de producción, las cifras de producción correspondientes a 2018 sumaron 210 000 toneladas de aluminio primario, 283 000 toneladas de aluminio fundido, 31 000 toneladas de aluminio reciclado y 105 000 toneladas de productos de aluminio procesado (incluidos los perfiles extruidos), todos ellos productos de alto valor agregado. Esperamos alcanzar las 120 000 toneladas de aluminio procesado en 2021”, afirma Dobra.
El aluminio es el elemento número 13 de la tabla periódica y constituye más del 8% de la masa de la corteza terrestre. Sin embargo, el aluminio puro no existe como tal en la naturaleza. Fue aislado por primera vez por el físico danés Christian Oersted en el siglo XIX, cuando aplicó la reducción electrolítica a diversos minerales ricos en aluminio. Hoy en día, el aluminio se produce principalmente a partir de la alúmina, que a su vez se obtiene de la bauxita, un mineral arcilloso que se encuentra principalmente en regiones trópicas. Para producir una tonelada de aluminio, se necesitan entre cuatro y cinco toneladas de bauxita.
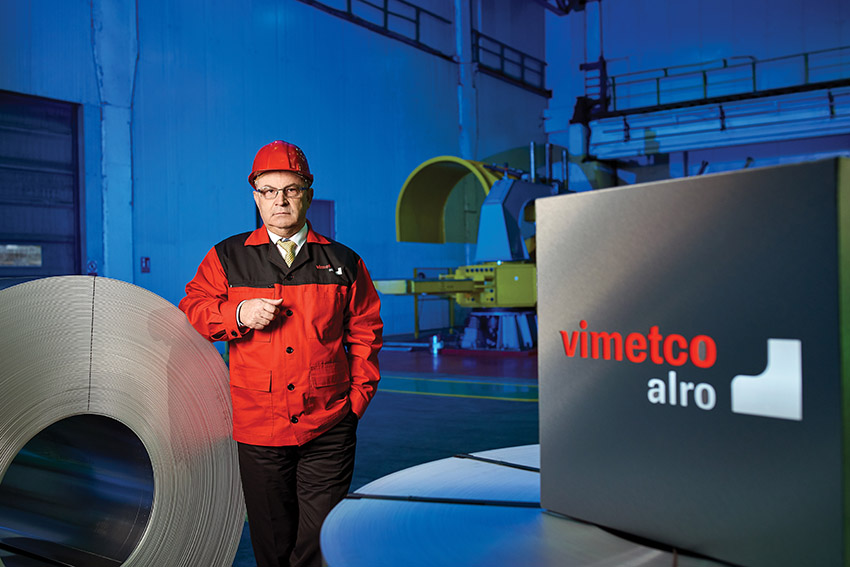
Cada una de estas categorías de productos es una materia prima clave que se utiliza para fabricar automóviles, trenes, aviones, teléfonos, cables, intercambiadores de calor, computadoras y un sinfín de productos especializados y domésticos.
Como productor de aluminio de primera clase, el Grupo ALRO está presente en toda la cadena de valor, desde la extracción de bauxita hasta la fabricación de productos automotrices y aeroespaciales (incluidas una planta de ánodos e instalaciones de reciclaje de aluminio). En el lenguaje empresarial, es lo que se conoce como integración vertical, ya que la empresa controla todos los eslabones del proceso de producción, desde una mina de bauxita en Sierra Leona (el mineral tarda dos semanas en llegar en barco al puerto de Tulcea, en el Danubio rumano) hasta las plantas de producción de aluminio primario y procesado en Slatina.
Dobra prevé un futuro sostenible para su empresa. “ALRO seguirá siendo un productor de aluminio competitivo durante mucho tiempo”, declara.
El éxito continuado de ALRO como productor de aluminio de propiedad privada en Rumania se debe en gran medida a las inversiones constantes en tecnologías y procesos nuevos para aumentar su eficiencia global. Por ejemplo, solo en 2018 se invirtieron 54,8 millones de euros.
Una parte de este esfuerzo ha recaído en SKF Rumania, que se encarga de implementar la gestión del ciclo de vida en ALRO. Esto ha ayudado a la empresa a determinar cómo utilizar mejor los rodamientos y los equipos de monitoreo de condición de SKF en cientos de canales de medición, como hornos, trenes de laminación en frío y en caliente, máquinas cepilladoras y maquinaria relacionada. Se trata de inculcar una cultura de “ingeniería de la confiabilidad” en la que los activos de ALRO se gestionan de acuerdo con las mejores prácticas para todo el ciclo de vida.
“Iniciamos nuestra colaboración con SKF en 2009. En nuestra opinión, son los mejores de su sector”, dice Dobra. “SKF ha transformado nuestro enfoque del mantenimiento; nuestros costos han bajado un 15%. El primer paso fue implementar la tecnología SKF Machine Health para evitar un 100% de paradas no programadas, y casi hemos alcanzado esta meta. Hemos invertido en esta tecnología, en los cambios de cultura y de procesos, y ahora avanzaremos hacia otras metas, como la digitalización de datos dentro del mantenimiento y el control de procesos. Nuestra colaboración con SKF es una parte muy importante de nuestros planes de negocio actuales y futuros”.