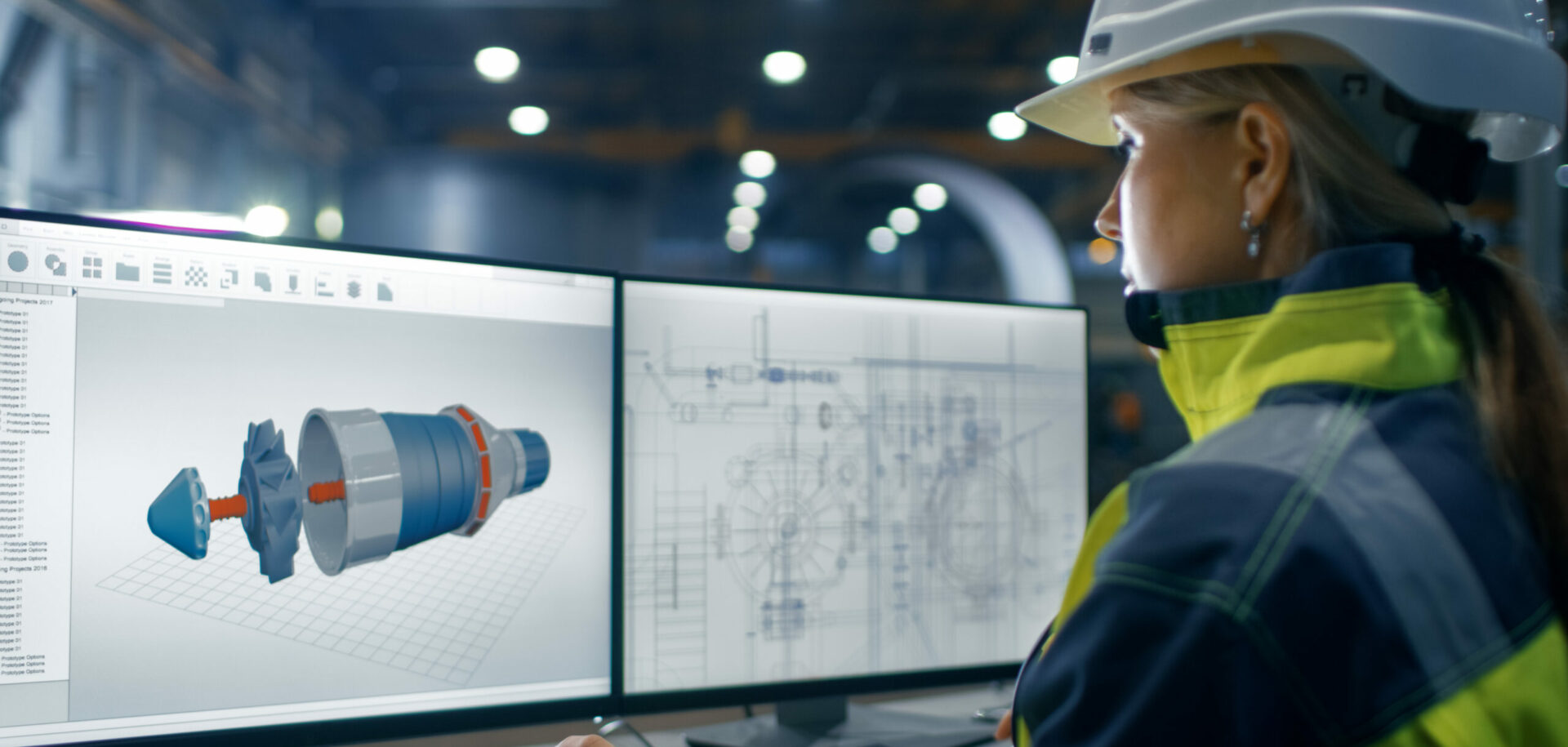
Soluciones para sistemas de tracción
Los sistemas de tracción para aplicaciones ferroviarias, como reductoras y motores de tracción, tienen que ser potentes y cumplir con la normativa medioambiental; también deben ser muy fiables, económicamente rentables y exigir poco mantenimiento. Los requisitos de dichas aplicaciones son mucho más estrictos que en otras industrias debido al gran peso de los vehículos ferroviarios y a la larga duración de los intervalos de servicio. Ello exige rodamientos y unidades de rodamientos específicos, la incorporación de sensores, la monitorización de estado y una serie de servicios.
Resumen
En ferrocarriles, los sistemas de tracción transmiten el par generado por el motor a las ruedas a través de una o varias reductoras, que normalmente funcionan a grandes velocidades. SKF ha desarrollado nuevas soluciones para incrementar la fiabilidad, prolongar los intervalos de mantenimiento y ofrecer una mayor rentabilidad. Recientemente, SKF ha publicado un manual técnico sobre sistemas de tracción que engloba los rodamientos y las unidades de rodamientos, los sensores, la monitorización de estado y los servicios.
Enlaces relacionados
SKF Railway Technical Handbook
Contacto de venta
Gottfried Kuře, Gottfried.Kure@skf.com
En ferrocarriles, los sistemas de tracción transmiten el par generado por el motor a las ruedas a través de una o varias reductoras, que normalmente funcionan a grandes velocidades.
SKF, proveedor global líder de la industria de ferrocarriles, ofrece una gran variedad de soluciones gracias al amplio y profundo conocimiento sobre aplicaciones ferroviarias adquirido a lo largo de los años. La excepcional gama de productos y soluciones para sistemas de tracción desarrollada por SKF satisface las exigentes demandas de las aplicaciones ferroviarias. Entre los productos pueden citarse rodamientos, obturaciones, lubricantes y sistemas de lubricación, mecatrónica y servicios.
Aplicaciones históricas
Reducir los costes de mantenimiento, ahorrar espacio e incrementar la fiabilidad han sido objetivos clave de SKF a la hora de desarrollar nuevas soluciones de rodamientos para reductoras y motores de tracción.
Los primeros diseños iban provistos de cojinetes lubricados con grasa. Estos exigían que alguien controlase diariamente el nivel del lubricante y lo rellenara si era necesario. En 1918, SKF comprobó que los costes de mantenimiento de los cojinetes de los tranvías podían reducirse entre el 25 y el 70% utilizando rodamientos de bolas a rótula en lugar de cojinetes (fig. 1).
Velocidad
La velocidad de los ferrocarriles de pasajeros y mercancías ha ido aumentando a lo largo de los años. La velocidad del vehículo y un diámetro de rueda dado determinan la velocidad rotativa del eje de salida de la reductora y de sus rodamientos. Un múltiplo de esta velocidad, que viene definido por la desmultiplicación, es la velocidad de entrada a la reductora y la velocidad del motor de tracción. El producto de los dos factores, la velocidad de rotación del motor de tracción (n) y el diámetro medio del rodamiento (dm), es un parámetro importante en la selección del tamaño de rodamiento, del diseño de la jaula y del conjunto de rodillos, además del lubricante y su viscosidad.
Aparte de la velocidad del vehículo, el valor n x dm de los rodamientos del motor de tracción aumenta según la relación de transmisión aplicada. Además, sólo pueden diseñarse motores de tracción de alta potencia aumentando su velocidad. No obstante, un factor de diseño en particular, la distancia entre las dos ruedas –definida por el ancho de la vía férrea– limita las dimensiones de la reductora y motor de tracción.
Potencia
La historia del diseño de los motores de tracción muestra que la potencia de éstos se ha incrementado paso a paso. Como ejemplo, puede considerarse el diseño de una típica locomotora eléctrica alemana de 4 ejes con cuatro motores de tracción. Hoy, la potencia de su motor es casi 10 veces superior en comparación con el primer diseño utilizado (fig. 2). La potencia del motor con respecto a la velocidad ejerce una influencia directa en las cargas que actúan sobre el eje primario, o de entrada, de la reductora. Los diseñadores de sistemas de tracción modernos trabajan para reducir las cargas sobre los rodamientos y para aplicar, en la medida de lo posible, lubricación con aceite.
Intervalos de mantenimiento
Una tendencia importante, y que según las previsiones persistirá, es la prolongación de los intervalos de mantenimiento. La tecnología de propulsión con corriente alterna (CA) en vehículos de tracción eléctrica requiere un mantenimiento menor, lo cual lógicamente conduce a una prolongación de los intervalos de mantenimiento.
En los rodamientos de los motores de tracción, se prevé una vida útil media de 15 años sin mantenimiento. Hoy, los rodamientos de los motores de tracción lubricados con grasa tienen algunas limitaciones para poder alcanzar esta cota. Sin embargo, algunos nuevos diseños, modelos de cálculo y resultados de ensayos podrían servir de base para alcanzar este objetivo paso a paso. Las nuevas directrices de SKF para optimizar la vida útil de la grasa pueden resultar una herramienta eficaz a la hora de prolongar los intervalos de mantenimiento convencionales (fig. 3).
Oportunidades de reducción de tamaño
Tal como ya se ha mencionado antes, para una determinada potencia nominal de motor, un incremento en la velocidad del motor permite un menor par en su eje y en el eje primario de la reductora. Esto reduce las cargas sobre los rodamientos y posibilita la incorporación de diseños de rodamiento pequeños; asimismo, durante el transcurso de los años, se ha reducido el tamaño de los rodamientos debido al aumento de la capacidad para soportar cargas de los mismos. Esto ha tenido un impacto muy positivo en la reducción de la fricción en el rodamiento, y conduce a un incremento en su eficiencia operativa.
Rodaje
Otro ejemplo de desarrollo es la evolución de los diseños de los rodamientos de rodillos cónicos, que ha permitido conseguir temperaturas de funcionamiento más bajas durante el rodaje. Durante este periodo, una disposición que incorpore rodamientos de rodillos cónicos de diseño convencional funciona con una cantidad significativa de fricción, ocasionando desgaste, que puede observarse como un valor pico en la temperatura.
Un montaje que utilice el actual diseño de rodamiento de rodillos cónicos de SKF funciona con una fricción y un calor y desgaste por fricción significativamente inferiores, siempre que los rodamientos estén correctamente montados y lubricados.
Rodamientos INSOCOAT y rodamientos híbridos
Las exigencias para los rodamientos de los motores de tracción se han acentuado significativamente debido a la introducción de motores de tracción controlados por convertidores de frecuencia, ocasionando un paso de la corriente eléctrica por los rodamientos que puede causar daños en un corto período de tiempo (fig. 6). El revestimiento INSOCOAT y los rodamientos híbridos reducen considerablemente este riesgo.
En aplicaciones de corriente continua (CC), un rodamiento INSOCOAT actúa como una resistencia normal (puramente óhmica). La capa de óxido de aluminio actúa como aislante; dicha resistencia (R) es el parámetro importante, soportando tensiones de hasta 1.000 V CC, con una resistencia superior a 50 MΩ, lo cual proporciona un aislamiento suficiente al rodamiento.
Los rodamientos híbridos mejoran aún más las propiedades de aislamiento eléctrico, especialmente en aplicaciones de sistemas de convertidores de alta frecuencia modernos, debido a que están equipadas con elementos rodantes fabricados con nitruro de silicio, apto para rodamientos. Estos rodamientos poseen unas propiedades de aislamiento eléctrico superiores, incluso con frecuencias muy altas.
La prolongación de los intervalos de mantenimiento puede basarse en la aplicación de las nuevas directrices sobre la vida útil de la grasa. Los parámetros clave son:
- Diseño de rodamiento optimizado, en especial en cuanto al número y tamaño de los elementos rodantes.
- Perfeccionamiento del diseño de la jaula.
- Obturaciones de laberinto, para proteger a la disposición de rodamientos contra la entrada contaminantes.
- Tipo y cantidad específicos de grasa aplicada.
Unidad de rodamiento para motores de tracción
La unidad de rodamiento para motores de tracción (TMBU) se basa en un diseño compacto que ahorra espacio y, puesto que se trata de una solución libre de mantenimiento, permite prolongar los intervalos de mantenimiento. La longitud total del motor puede reducirse, o puede incrementarse la longitud del devanado en el estator y rotor en un motor de dimensiones dadas para obtener mayor potencia. Este principio de diseño de subsistemas incorpora varias características en una sola unidad, como grasa, obturaciones y funciones de fijación. El diseño de brida integrada facilita su montaje.
La TMBU es una unidad de rodamiento protegida y prelubricada, diseñada para el montaje ensamblado en el soporte del motor (fig. 8). Se selecciona una grasa especial para conseguir una vida prolongada, incluso a temperaturas de funcionamiento elevadas. La unidad está provista de obturaciones de laberinto no rozantes, que no ocasionan desgaste. Dicha unidad puede suministrarse con diseño híbrido provisto de elementos rodantes de cerámica para evitar daños por el paso de la electricidad, y sensores que permiten detectar las condiciones operativas. Otras características opcionales son el aislamiento eléctrico y la monitorización de datos de funcionamiento como la temperatura, la velocidad y el posicionamiento absoluto para el sistema de control de la propulsión.
Sensores
El concepto de TMBU sensorizada (fig. 9) ofrece varias posibilidades de detección y medición: la detección de la posición absoluta para los dispositivos de control del motor de tracción y la detección del sentido de rotación, la medición de la velocidad para los sistemas de control de los frenos y la medición de la temperatura para monitorizar las condiciones operativas.
En la mayoría de los casos, los sensores están integrados en el sistema de obturación del aro exterior de la unidad de rodamiento. Este diseño permite ahorrar espacio y reducir el número de piezas.
Monitorización de estado
La monitorización de estado consiste en una tecnología avanzada, con capacidad de incrementar la seguridad y fiabilidad, así como de prolongar los intervalos de mantenimiento. Utilizando sistemas de detección del estado (fig. 10), y aplicando sofisticados algoritmos para el procesamiento de datos, se pueden detectar daños incipientes, lo que permite anticipar las reparaciones oportunas antes de que se produzcan daños mecánicos o averías.
Reacondicionamiento de rodamientos
En comparación con la fabricación de un rodamiento nuevo, el reacondicionamiento de rodamientos1 conlleva una reducción significativa de las emisiones de CO2, y consume hasta un 97% menos de energía. Prolongando la vida útil de los rodamientos (fig. 11), evitamos desechar componentes y hacer un uso innecesario de los recursos naturales. Los especialistas de SKF pueden evaluar si un rodamiento puede reacondicionarse o no.
El reacondicionamiento de los rodamientos ayuda mucho a optimizar los costes durante el ciclo de vida, ofreciendo:
- una significativa reducción de los costes en comparación con los rodamientos nuevos,
- una vida útil prolongada,
- mayor disponibilidad, lo cual contribuye a una reducción de las existencias,
- un análisis de la causa raíz de las averías y estudio de acciones correctivas,
- un aumento en su rendimiento gracias a la mejora que conlleva el reacondicionamiento,
- “feedback” sobre las aplicaciones para mejorar la tecnología operativa y de mantenimiento del cliente,
- reducción del impacto medioambiental gracias a una reducción de residuos, del uso de materias primas y del consumo energético.
Publicaciones
Recientemente, SKF ha publicado un manual técnico sobre sistemas de tracción para aplicaciones ferroviarias. Su contenido se centra en los rodamientos de los motores de tracción y reductoras, en los sensores, la monitorización de estado y servicios. También ofrece recomendaciones para incrementar al máximo la vida útil de los rodamientos, describiendo un montaje, mantenimiento y monitorización de estado apropiados.
1) Además del término “reacondicionamiento” aquí usado, algunas empresas y fabricantes de ferrocarriles también utilizan otros términos como “recuperación” y “reparación” para diferenciar demandas específicas. El término “remecanizado” normalmente engloba las operaciones de rectificado y pulido. No obstante, no parece que exista una definición global para estos términos y su coincidencia parcial puede resultar contradictoria.
INSOCOAT y SKF Explorer son marcas registradas del Grupo SKF.