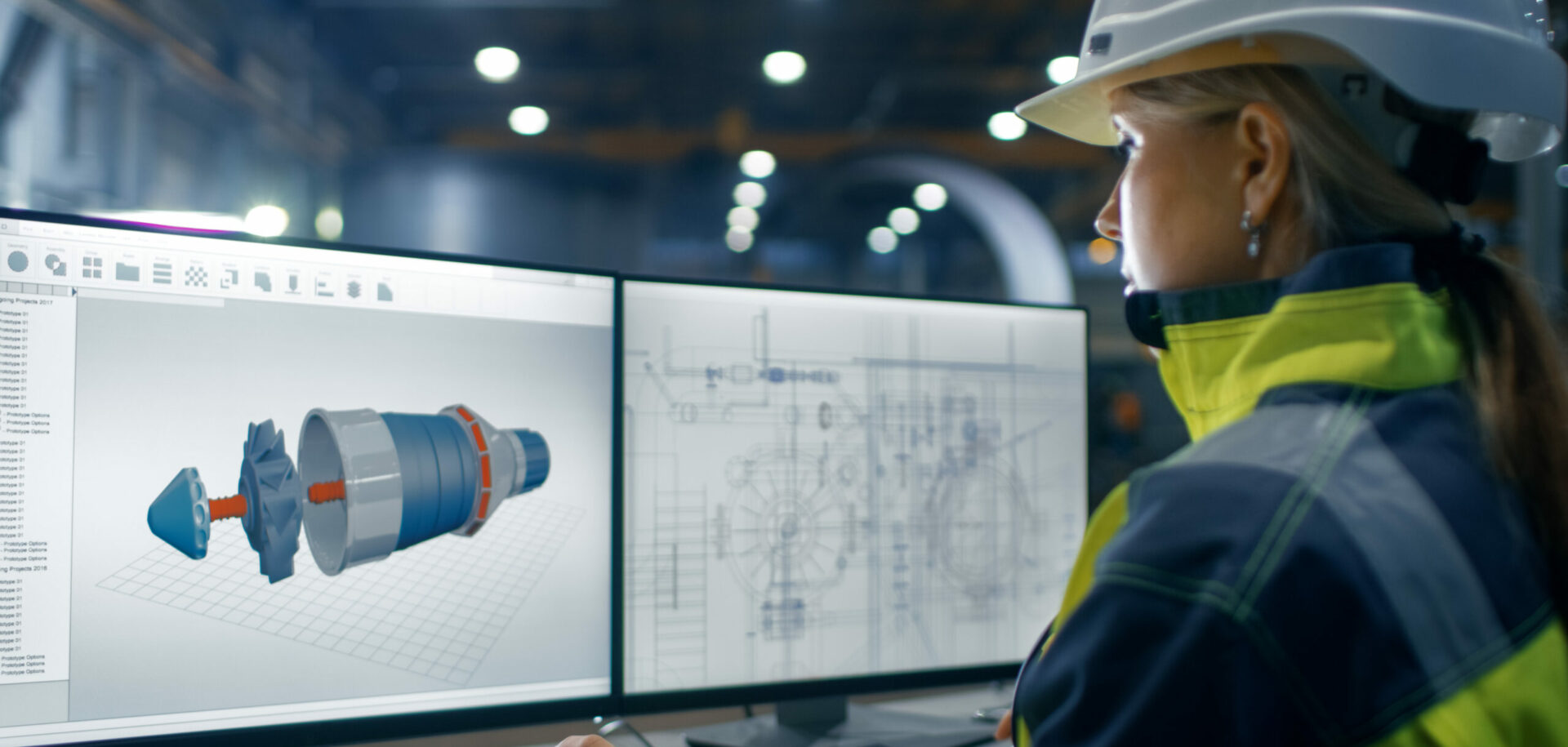
Soluzioni per sistemi di trazione
Nell’industria ferroviaria, i sistemi di trazione, quali i riduttori e i motori di trazione, devono essere potenti, molto affidabili ed economici, avere basse esigenze manutentive e soddisfare le politiche ambientali. I requisiti sono molto più severi di quelli di molte altre industrie, a causa del peso dei veicoli e per la necessità di lunghi intervalli di manutenzione. Così queste applicazioni necessitano di cuscinetti e unità cuscinetto di esecuzione speciale, inserimento di sensori, monitoraggio delle condizioni e speciali servizi di manutenzione.
Sintesi
In ferrovia i sistemi di trazione servono a trasmettere alle ruote la coppia del motore di trazione o di un motore a combustione interna, che normalmente opera a velocità più alta, tramite uno, due o più riduttori. La SKF ha realizzato una gamma di nuove soluzioni atte ad aumentare l’affidabilità, prolungare gli intervalli di manutenzione e razionalizzare i costi. Recentemente la stessa SKF ha pubblicato un manuale tecnico sui sistemi di trazione, che tratta cuscinetti, unità cuscinetto, sensori, monitoraggio delle condizioni e servizi.
Link correlati
SKF Railway Technical Handbook
Contatto vendite
Gottfried Kuře, Gottfried.Kure@skf.com
Nell’industria ferroviaria i sistemi di trazione servono a trasmettere alle ruote la coppia del motore di trazione o del motore a combustione interna (che generalmente operano ad una velocità più alta) tramite uno, due o più riduttori.
La SKF, nella sua qualità di fornitore internazionale dell’industria ferroviaria, offre una grande varietà di soluzioni, che sono il risultato delle vaste e profonde conoscenze acquisite nel corso degli anni in questo settore. Per soddisfare i severi requisiti dei sistemi di trazione la SKF ha realizzato un assortimento unico di prodotti e soluzioni, che comprende cuscinetti, tenute, lubrificanti, sistemi di lubrificazione, meccatronica e servizi.
Applicazioni storiche
Ridotti costi di manutenzione, esigenze di spazio contenuto e maggiore affidabilità sono sempre stati gli elementi chiave per la realizzazione di nuove soluzioni di cuscinetti per i riduttori e i motori di trazione.
I primissimi progetti prevedevano bussole, che richiedevano il controllo quotidiano del livello dell’olio e il suo eventuale ripristino. Nel 1918, la SKF calcolò che i costi di manutenzione dei cuscinetti dei tram potevano essere ridotti del 25-70 % impiegando in luogo delle bussole i cuscinetti orientabili a sfere (fig. 1).
Velocità
Col tempo la velocità dei trasporti merci e passeggeri sono aumentate. La velocità di marcia dei veicoli e il diametro delle ruote determinano la velocità di rotazione dell’albero di uscita del riduttore e dei relativi cuscinetti. La velocità del motore di trazione e quindi quella dell’albero d’ingresso del riduttore è superiore a tale velocità di un valore corrispondente al rapporto di trasmissione degli ingranaggi. Il prodotto di due fattori, la velocità di rotazione del motore (n) e il diametro medio dei cuscinetti (dm) è un parametro importante per la scelta delle dimensioni dei cuscinetti, del loro tipo di gabbia e dei rulli, così come del lubrificante e della sua viscosità.
A parte la velocità di marcia del veicolo, il prodotto n x dm aumenta quando si hanno motori di trazione più veloci a seguito della riduzione delle loro dimensioni d’ingombro. Del resto i motori di trazione più potenti si possono solo realizzare con una velocità più alta. Nello stesso tempo occorre tenere presente un altro fattore, lo scartamento, che limita la lunghezza totale in orizzontale del riduttore e del motore di trazione stesso.
Potenza
Se esaminiamo nel lungo periodo lo sviluppo storico dei motori di trazione notiamo come la potenza sia gradualmente aumentata. Consideriamo ad esempio una tipica locomotiva elettrica tedesca a 4 assi, con quattro motori di trazione: oggi la sua potenza è quasi 10 volte superiore a quella di quando era stata progettata per la prima volta (fig. 2). La potenza dei motori rapportata alla velocità ha un’influenza diretta sul carico applicato sull’albero d’ingresso del riduttore. Nella progettazione dei sistemi di trazione attuali si cerca di ridurre i carichi sui cuscinetti e di impiegare per quanto possibile la lubrificazione ad olio.
Intervalli di manutenzione
Una tendenza importante, che continua, è verso un aumento degli intervalli di manutenzione. Un vantaggio nell’impiego dei sistemi di propulsione a corrente alternata (AC) per i veicoli elettrici è la minore necessità di manutenzione, che naturalmente si traduce in maggiori intervalli d’intervento.
Per i cuscinetti dei motori di trazione è pensabile una durata media di 15 anni senza manutenzione. Oggi i cuscinetti lubrificati a grasso per tali motori hanno qualche limitazione nel raggiungere tale durata. Tuttavia alcune nuove esecuzioni, nuovi modelli di calcolo e nuovi test possono essere la base di partenza per raggiungere gradualmente tale obiettivo. Le nuove indicazioni SKF per ottenere una durata ottimale del grasso sono un utile strumento per estendere gli intervalli di manutenzione tradizionali (fig. 3).
Opportunità di riduzione delle dimensioni
Come detto più sopra, per un motore di trazione di una data potenza, l’aumento della velocità consente di avere una minore coppia sia sull’albero del motore stesso sia su quello d’ingresso del riduttore. In tal modo si riducono i carichi sui cuscinetti di quest’ultimo e diventa possibile utilizzare cuscinetti di dimensioni minori; inoltre è anche da sottolineare che i cuscinetti sono già stati nel tempo ridotti di dimensioni grazie all’aumento della capacità di carico (fig. 4). Tutto ciò ha un impatto molto positivo sulla riduzione dell’attrito dei cuscinetti stessi e porta ad un aumento della loro efficienza.
Rodaggio
Un altro esempio di realizzazione è l’evoluzione dei cuscinetti a rulli conici per quanto riguarda la diminuzione della temperatura durante il rodaggio. Durante tale fase un sistema di cuscinetti a rulli conici di tipo tradizionale opera con una significativa quantità di attrito, con conseguente usura, rilevato da picchi di temperatura.
Al contrario, purché sia montato e lubrificato correttamente, un sistema munito degli attuali cuscinetti SKF a rulli conici opera con molto meno attrito, minore sviluppo di calore e usura.
Cuscinetti ibridi e INSOCOAT
Le esigenze dei cuscinetti per i motori di trazione sono aumentate notevolmente a causa dell’introduzione dei motori controllati da convertitore di frequenza. Poiché il passaggio di corrente elettrica attraverso i cuscinetti può in breve tempo arrecare danni (fig. 6), per ridurne in larga misura l’evenienza è opportuno l’impiego dei tipi SKF INSOCOAT e di quelli SKF ibridi.
Nelle applicazioni a corrente continua i cuscinetti SKF INSOCOAT agiscono come normali resistori. Lo strato di ossido di alluminio che riveste la superficie diametrale esterna di uno degli anelli è isolante e la sua resistenza R è un parametro importante. La tensione di rottura dello strato standard è pari a 1.000 V DC, mentre la resistenza è superiore ai 50 MΩ, il che assicura ai cuscinetti un isolamento efficace.
Grazie ai corpi volventi di nitruro di silicio di cui sono dotati, i cuscinetti SKF ibridi offrono un ulteriore miglioramento delle proprietà isolanti, specialmente per le moderne applicazioni che impiegano convertitori ad alta frequenza (fig. 7).
Seguendo le nuove indicazioni circa la durata del grasso è possibile ampliare gli intervalli di manutenzione. Ecco i parametri più importanti di questi cuscinetti:
- progettazione ottimizzata, specialmente per quanto riguarda il numero e le dimensioni dei corpi volventi
- progettazione della gabbia ulteriomente migliorata
- tenute a labirinto per la protezione contro le sostanze contaminanti
- quantità e tipologia specifiche del grasso utilizzato
Unità cuscinetto per i motori di trazione
Le unità cuscinetto SKF TMBU per motori di trazione sono di ingombro ridotto e consentono lunghi intervalli di esercizio senza manutenzione e nello stesso tempo permettono di ridurre la lunghezza totale del motore o in alternativa, a parità di ingombro del motore, di aumentare le dimensioni del rotore e dello statore per ottenere maggiore potenza. Le unità costituiscono un sottosistema comprendente le funzioni di lubrificazione a grasso, tenuta e fissaggio. La presenza della flangia integrata ne facilita il montaggio.
Le unità TMBU sono prelubrificate e dotate di schermi di protezione del tipo a labirinto quindi senza contatto né usura; la flangia consente di montarle facilmente al corpo del motore (fig. 8). La lubrificazione è assicurata da un grasso speciale, di lunga durata anche a temperature di esercizio elevate. Possono essere fornite nell’esecuzione ibrida con corpi volventi in ceramica per la protezione dai passaggi di corrente e con sensori per il monitoraggio delle condizioni di lavoro. Funzioni opzionali sono l’isolamento elettrico e il monitoraggio di temperatura, velocità e posizionamento assoluto per il dispositivo di controllo del sistema di propulsione.
Sensori
Le unità TMBU sensorizzate (fig. 9) offrono varie opportunità di monitoraggio e misurazione: rilevamento della posizione assoluta per i dispositivi di controllo dei motori di trazione; rilevamento del senso di rotazione; misurazione della velocità per i sistemi frenanti; misurazione della temperatura per monitorare le condizioni di lavoro.
In molti casi questi sensori sono integrati nelle tenute dell’anello esterno del cuscinetto, consentendo di risparmiare spazio e ridurre il numero di componenti.
Monitoraggio delle condizioni
Il monitoraggio delle condizioni è una tecnologia matura, in grado di aumentare la sicurezza e l’affidabilità degli impianti e prolungare gli intervalli di manutenzione. Utilizzando sistemi di rilevamento (fig. 10) e applicando sofisticati algoritmi per l’elaborazione dei dati, è possibile rilevare gli eventuali danneggiamenti incipienti sufficientemente in tempo per prepararsi alle riparazioni prima che si verifichino guasti meccanici più gravi.
Ricondizionamento
Rispetto alla produzione di esemplari nuovi il ricondizionamento dei cuscinetti1) può ridurre considerevolmente le emissioni di CO2, in quanto richiede fino al 97 % di energia in meno. Prolungando la durata di esercizio di un cuscinetto (fig. 11), si evita di produrre scarti e di sfruttare inutilmente risorse naturali. Il compito di giudicare se un cuscinetto può essere ricondizionato oppure no può essere affidato agli specialisti SKF.
Il ricondizionamento dei cuscinetti dà un grande contributo nell’ottimizzare i costi di esercizio, offrendo:
- una significativa riduzione dei costi rispetto all’acquisto di cuscinetti nuovi
- una più lunga durata di esercizio
- una migliore disponibilità, abbinata alla riduzione degli stock
- la possibilità di analizzare le cause di un danneggiamento al fine di prevedere azioni correttive
- migliori prestazioni grazie alla possibilità di aggiornamento delle caratteristiche dei cuscinetti durante la ricostruzione
- un feedback applicativo utilizzabile dai clienti per migliorare il funzionamento e la manutenzione dei suoi sistemi
- la riduzione dell’impatto sull’ambiente grazie alla diminuzione degli scarti, dell’impiego di materie prime e del consumo di energia.
Pubblicazioni
Recentemente, la SKF ha pubblicato un manuale tecnico dedicato ai sistemi di trazione delle applicazioni ferroviarie, in particolare ai cuscinetti dei motori di trazione e dei riduttori, ai sensori, al monitoraggio delle condizioni e ai servizi di manutenzione. Il manuale fornisce anche suggerimenti su come ottimizzare la durata di esercizio dei cuscinetti, eseguendo in modo appropriato il montaggio, la manutenzione e il monitoraggio delle condizioni.
1) In ferrovia, per differenziare specifiche esigenze, oltre al termine generico di “ricondizionamento” alcuni costruttori utilizzano “ricostruzione” o “ripristino”. Per le operazioni di rettifica e lucidatura di solito si usa Il termine “rilavorazione”. A quanto pare non c’è un accordo generale sulle definizioni, che possono sovrapporsi e generare confusione.
INSOCOAT e SKF Explorer sono marchi registrati del Gruppo SKF.