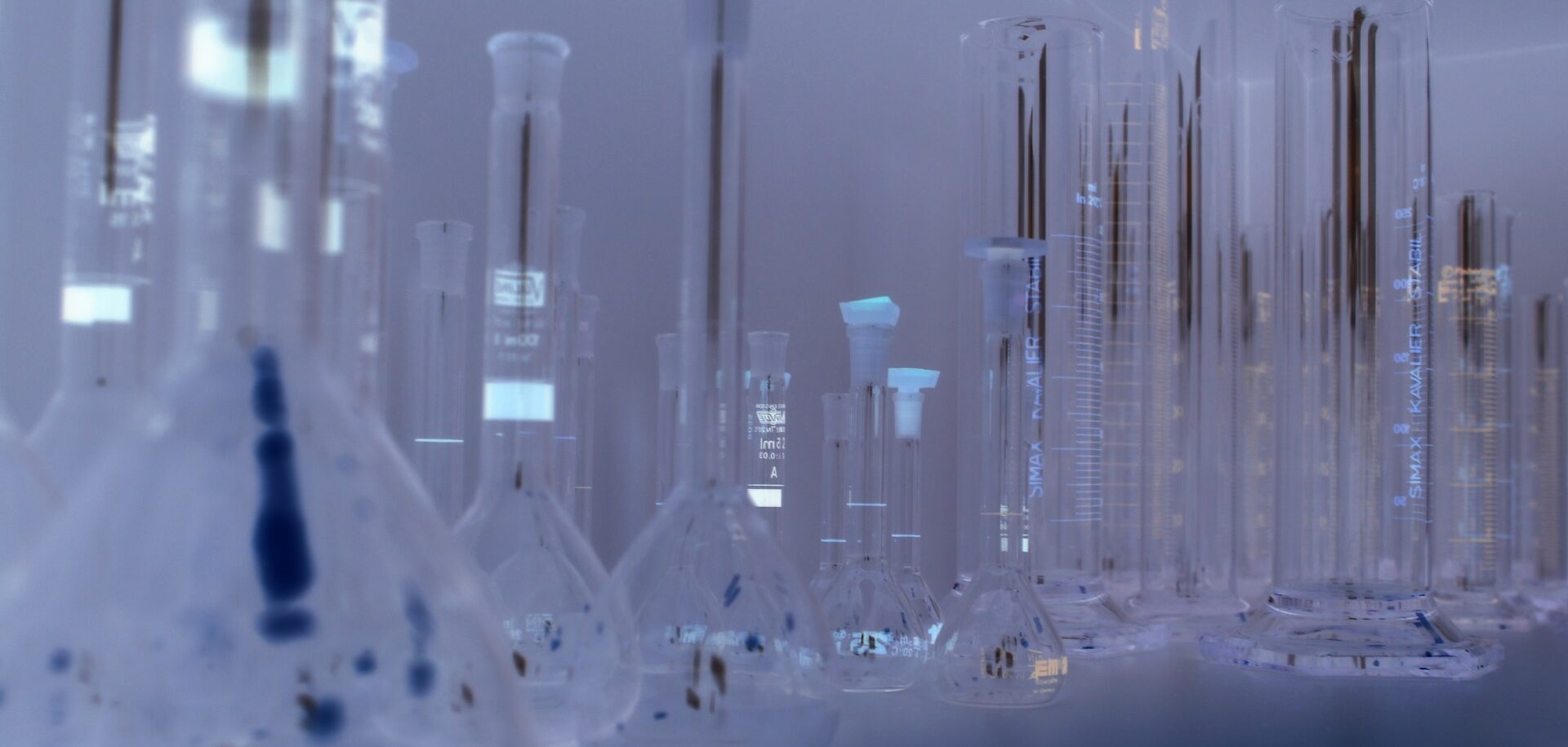
Experimenting with new challenges leading the path to innovation
Universal trends applicable to numerous machines and many industries comprise improved energy efficiency and cost reduction, which, among others, can be achieved by downsizing machines, increasing speeds and loads. As a result, machines are ever more subject to higher stress levels. Bearings are of course no exempt from these trends, highly contributing to the overall equipment performance.
As one of the most widely used machine elements, the impact of bearings on the overall performance of many machines is quite significant. However, accommodating those increasingly higher stresses while ensuring a high level of reliability is a challenging assignment for bearings too. SKF embraces these challenges by performing state-of-the-art research and development activities addressing a large variety of demands in key industries such as railway, electric vehicles, machine tools, metal manufacturing and wind energy.
The new SKF R&D centre
Established in the Netherlands in 1972, the main core of SKF R&D has recently moved from its historical site in Nieuwegein to the unique cycling city of Houten. Here is where the new, sought-after challenging needs for rolling bearings are investigated, tackled and transformed into innovative solutions. Progress in R&D at SKF extensively relies on experiments, and the brand new, cutting-edge laboratories in Houten are an experimental hotbed of innovation.
Despite the complex and eclectic nature of the large number of projects being run in the R&D laboratories, the final aim of this unceasing research can be thought of as common to all industries that SKF serves: to ensure reliable equipment performance. To reach this ultimate goal, the R&D centre is provided with a comprehensive selection of rigs and tools enabling research in the areas of lubricants, bearing steels, ceramics, coatings, polymers, seals and sensors. In parallel, the expertise covered by the researchers working here range from engineering to material science, from chemistry to physics. Each single feature of a bearing, i.e. its material, design, surface properties and lubricant, is analysed into its tiny details and tested under the relevant application conditions.
All this makes the R&D centre in Houten a melting pot of science where, working in synergy and at a fast pace, SKF researchers jointly concentrate their efforts into fighting friction and wear, leading customer-driven projects that result into the development of new products and/or improved knowledge of the increasingly demanding applications and related issues.
Steel
As most bearing rings and rolling elements are made of steel, extensive laboratory work is carried out to screen different steel grades with a variety of heat treatments including through hardening, carbonitriding, case carburising and induction hardening, so that the right steel variant is chosen for the target application.
Dilatometry is used to quantify the material response to heat treatments, by measuring the dimensional changes of steel as a function of temperature. A combination of visual inspection techniques including optical microscopy, interferometry and scanning electron microscopy (SEM), is used to investigate the surface conditions of bearings collected from the field, as well as to characterise the microstructure of the steel under study. X-Ray diffraction, to assess residual stresses and phase composition, can be employed in conjunction with hardness measurements to look for a detailed correlation between steel microstructure and its performance, and reliably select the right steel and heat treatment for the required customer application.
The scope of these activities can be broad and generally aimed at improving the resistance of steel to a variety of potential damage mechanisms typically found in rolling bearings. In particular, the relevant phases of damage initiation and propagation, and their relative effect on the overall lifetime of rolling bearings, are among the main fields of interest. However, each activity is tailored for the specific application under study, which can range from extending the maintenance interval of bearings used in railway, to developing reliable solutions for more powerful wind turbines.
Coatings
In certain demanding applications the bearing’s bare steel surface properties, however optimised in terms of hardness and texture, cannot meet the needed requirements. A solution capable to provide value and benefits to bearings’ performance is coatings, which equip SKF bearings with specific, application-targeted surface properties that would be otherwise impossible to achieve with just steel.
An anti-corrosion coating could help greatly extend the bearing life in bearings subjected to water contamination, which is likely to happen in an industrial environment such as a steel mill. The employment of an antiwear coating offers huge potential in applications where it is desired to keep the optimal surface fatigue and wear resistance properties while extending the lifetime and improving reliability, such as in a gearbox of a wind turbine.
Experimental work carried out at the R&D centre in Houten focusses on optimising the coatings materials and their deposition techniques, as well as testing coating solutions to assess their suitability for a target application. Detailed characterisation of coatings and their thin layers relies on the use of the advanced X-ray Photoelectron Spectroscopy (XPS) to evaluate their composition, coupled with SEM microscopy to study their thickness, and classical scratch and reciprocating sliding testing to assess their adhesion and wear properties.
Hybrid bearings
Even though most of the currently operating bearings are made uniquely of steel, hybrid bearings outperform them in a vast range of applications. The material choice for hybrid bearings, with rings made of steel but rolling elements made of ceramic silicon nitride, carries many advantages.
Their light weight certainly leads to clear benefits in applications where performance rhymes with speed, such as in motorsport. With their greater durability in conditions of poor lubrication, they are compliant with the strict safety demands present in aerospace. Thanks to their much higher stiffness, they are particularly suitable for high-speed applications where precision is a must, as in machine tool spindles. Furthermore, by being electrically insulated, they are immune to the phenomena of electrical erosion, commonly found in electric vehicles and in the generator of wind turbines. The advantages of hybrid bearings are clearly endless.
An area of opportunity for hybrid bearings, and the focus of many of the experimental activities performed at the SKF R&D laboratories, is to increase their tolerance to defects in the ceramic material, as well as to improve their performance predictions by taking the same defects into account. Hence, much effort is spent working on examining the quality of ceramic rolling elements. The detection of fine imperfections, which would be invisible under the standard white light of an optical microscope, is performed by using fluorescence penetrant inspection in a dark room. The microstructure of the ceramic material is of course equally important as surface quality, hence this is thoroughly examined microscopically. Its effect on the mechanical properties of the ceramic rolling elements is then assessed by performing hardness and strength testing, including a Notched Ball Test which was specifically developed to test ceramic balls.
Big emphasis is also put into new methods, including artificial intelligence, aiming at generating knowledge of existing products, as well as developing new materials that are customised for the specific applications.
The cage
An often overlooked component of a bearing, but actually one with a very tough job, is the cage. Its primary function is to guide the rotation of the rolling elements while keeping a defined distance between them and preventing their direct contact.
The new requirements for higher loads and speeds in many applications is often the reason behind the choice of a cage made of polymer, which under these conditions often provides lower friction and better guidance than steel and other metals. However, current demanding needs to withstand the severe loads encountered in more powerful, bigger wind turbines, as well as the combined extreme temperatures and speeds found in the latest electric vehicles, pose extraordinary challenges also for polymer cages. It is therefore essential to perform the intensive and extensive characterisation and testing of polymer materials carried out in the SKF R&D laboratories.
To better understand the degree of crystallinity of polymers, Differential Scanning Calorimetry (DSC) is performed. Tensile tests, conducted in a climate chamber enabling test temperature ranging from -70 to 300 ˚C, allow to then find the link between the polymer microstructure and its strength. This knowledge is used to generate input for simulation tools used to predict the cage performance in the target applications. For example, by performing Dynamic Mechanical Thermal Analysis (DMTA) measurements, the application of the time–temperature superposition principle makes it possible to predict how stable the polymer material will be in a specific application, and therefore how the cage will respond under certain conditions of bearing speed, temperature and load.
Grease
The lubricant is, in all aspects, an integral component of the bearing which largely affects its performance, particularly its torque and lifetime. The main purpose of the lubricant is to form a thin lubricating layer that prevents the surfaces of the rolling elements and the raceways from coming into direct contact, thus lowering friction while preventing damage.
Due to its capacity to stay in place without leaking, as well as its sealing abilities, in many applications grease is the lubricant of choice for rolling bearings; indeed, more than 80 % of rolling bearings are grease-lubricated. However, choosing the right grease for the specific application is an intricate task. Partly due to the wide selection of formulations available, the extensive number of parameters which can be used to define the properties of grease is indicative of its great complexity.
The specific types of ingredients contained in a grease, their content, as well as the way in which the grease is manufactured, determine its consistency, oil bleeding, mechanical stability, dropping point, as well as a large number of rheological properties which affect the way in which grease flows. These properties are thoroughly investigated by using both standard and customised tests, with the aim of identifying the key factors which regulate the overall grease performance in specific applications. Eventually, the objective of these activities translates into specific questions: “What makes grease a high-speed grease? Or a high-temperature grease? Or a heavy-duty grease? Or a combination of these requirements”? The right answer to these questions will, for example, support on extending the maintenance interval in high-speed railway applications, improving the reliability of wind turbines, ensuring a long bearing life in electric vehicles, or reducing energy consumption in the automotive industry.
Seals
Apart from standalone shaft seals, bearings are also equipped with dedicated seals used to close the gap between the outer and the inner ring in order to retain the grease inside the bearing and protect against external contamination. Because they often need to be adaptive to the static and dynamic misalignments in application, most seals are made of a flexible rubber elastomer. The design of seals can vary greatly according to the application. Tight seals are required in slow-rotating bearings in highly contaminated environments, such as in mining, while non-contacting seals might be the right solution in very high-speed applications, such as electrical vehicles gearboxes and machine tool spindles.
With regards to the specific material of the seal, this is wisely chosen according to the range of operating temperatures and speeds over which the required elasticity, wear resistance and ageing can vary considerably. Advanced dynamic simulation methods are used to respond to the customer needs for a great variety of application conditions. Simultaneously, SKF researchers have developed testing capabilities and methods to validate these models and efficiently test new sealing concepts. The sealing performance, in terms of lubricant retention or contaminant exclusion, combined with the frictional response of seals during rotation, can be tested with the introduction of transverse movements, misalignments and across a wide range of speeds, temperatures and loads. Given the very application-driven nature of these activities, the testing rigs are often customised to answer and meet specific demands.
The bearing as a whole
Evidently, the individual features of a bearing need to work well together. Possibly in the first place, the materials need to be chemically compatible, such as the cage and seal materials with the lubricating grease.
Tribology, the study of surfaces in relative motion, is a main field of interest in the SKF R&D laboratories, as it encompasses all the relevant mechanical and chemical aspects involved during the operation of a bearing. The interaction between steel, coatings, ceramics with lubricants is evaluated by using rigs that simulate the conditions of the lubricated contacts between the rolling elements and the raceways. These are ball-on-disc, pin-on-disc, ring-on-flat, rings-on-roller machines that are employed to investigate friction, lubricant film thickness, as well as a number of surface and subsurface damage mechanisms comprehending wear (in all its possible manifestations), surface distress, pitting and smearing.
Using those simple rigs in place of full bearings enables to partly decouple some of the many phenomena occurring simultaneously in a bearing, so that the relevant knowledge can be developed to understand the most complex issues in depth, and reach the new challenges in full. This generated knowledge is eventually evaluated at a universal level by assessing the overall performance of the bearing where they belong.
The R&D facilities are equipped with full bearing testing rigs, designed in a versatile way to study the most diverse subjects: bearing torque, bearing and grease life, grease flow in large size bearings. Here the effects of the material, surface features and design of raceways, rolling elements, cage, seals, grease type and its filling are studied concurrently. If a weak link is identified in the bearing, this is approached and investigated in detail at a more fundamental level, in the attempt to optimise solutions in an iterative way.
When it comes to bearings, the devil is in the details. These can be as small as a micron for coatings, or of nanometres size for surface roughness and lubricant film thickness, but can have a huge impact on the bearing performance. As a complex machine element, the right bearing for the specific application is the culmination of the efforts of many different competences. At the SKF R&D facilities in Houten, all these come together to assure a reliable equipment performance.