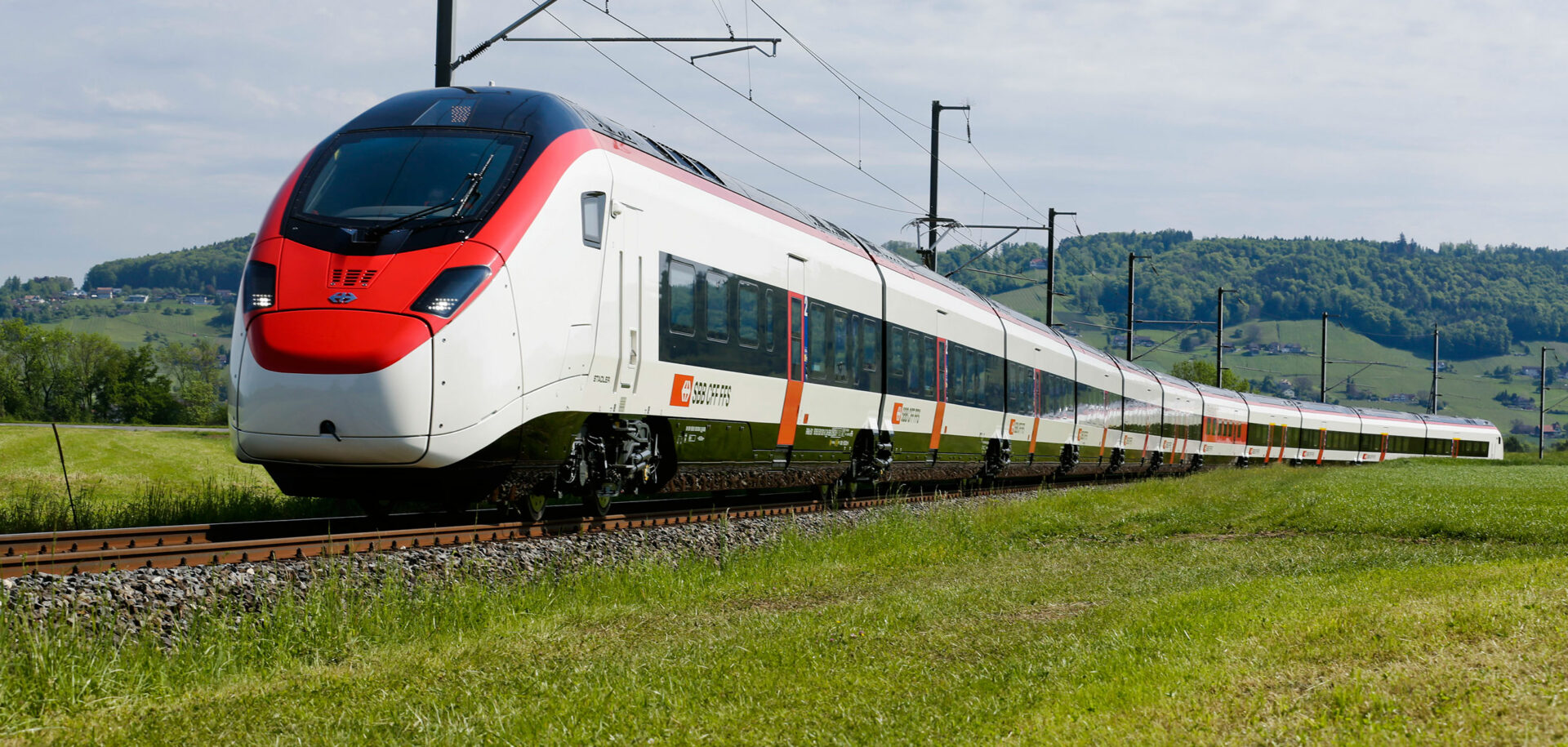
Des essieux faits pour durer
Un nouveau matériau révolutionnaire conçu par GHH-BONATRANS accroît la fiabilité des essieux du matériel roulant et réduit les coûts pendant leur durée de vie.
La prochaine fois que vous prendrez le train et entendrez l’entrechoquement des roues et des rails, prenez quelques minutes pour réfléchir au savoir-faire et à l’expertise déployés par ceux qui les fabriquent.
« Les roues de locomotive sont soumises à des charges considérables », explique Marcel Ujfaluši, responsable du développement commercial et du marketing chez GHH-BONATRANS, l’un des plus grands fabricants mondiaux d’essieux montés pour matériel roulant.
La zone de contact entre roues et rails n’est pas plus grande que la surface d’une pièce d’un euro, poursuit-il. Et cette zone doit supporter le poids et la force de guidage du train et transférer le courant de traction. « Pour que les roues puissent résister à ces contraintes, il faut avoir recours à d’excellents matériaux. »
Ses avantages ne s’arrêtent pas au renforcement de la dureté des roues.
Peter JanoŠ, responsable CCV de GHH-BONATRANS
Ce cadre sait de quoi il parle. Installée à Bohumín, à la frontière orientale de la République tchèque, GHH-BONATRANS fournit des essieux montés aux plus grands fabricants de matériel roulant et compagnies ferroviaires du monde entier.
Grand concepteur d’essieux
Le BONASTAR®4BD est principalement destiné aux ensembles roues et essieu, mais GHH-BONATRANS a mis au point ce matériau pour tous les types d’essieux montés pour trains de passagers ou de marchandises : trains à grande vitesse et express régionaux, trains de banlieue, tramways, métros, etc..
Éminent concepteur et fabricant européen d’essieux, l’entreprise fournit une gamme complète de produits et solutions, notamment des essieux montés pour trains et locomotives à grande vitesse, des solutions pour tramways à plancher surbaissé (roues haute résistance et systèmes d’isolation phonique).
Défi relevé
La durée de vie de la graisse est un point crucial pour porter à 1,7 million de km les intervalles entre les révisions. Celle des roulements dépend de plusieurs facteurs : température de fonctionnement, vitesse de rotation, dimensions des roulements et propreté. « Le plus difficile a été de trouver un moyen de réduire les frottements pour obtenir moins d’échauffement – et éviter l’usure – sans compromettre la solidité du matériau ou la durée de vie des roulements », explique Jan Babka, technico-commercial industrie ferroviaire chez SKF.
Les améliorations continues apportées en matière de conception et de fabrication ont permis de réduire le moment de frottement dans les roulements. Une solution d’étanchéité optimisée évite la pénétration des contaminants.
Afin de réduire l’usure au minimum, SKF applique sa technologie brevetée, le traitement thermique Xbite, aux bagues des roulements. Avec Xbite, on obtient la même dureté que par trempe martensitique, mais avec d’autres avantages : ténacité de plus haut niveau et plus grande résistance à la fatigue.
Dès sa création il y a deux siècles, sa réputation d’excellence est allée de pair avec l’attention qu’elle accorde à la sécurité et à la fiabilité. Mais elle a dû se battre pour défendre cette réputation. Des générations successives d’ingénieurs ont bataillé pour réduire les coûts de cycle de vie (CCV) des essieux sans altérer leurs performances.
Les ingénieurs de la recherche d’aujourd’hui sont convaincus que leur dernière invention est une avancée majeure pour le secteur. Il s’agit du BONASTAR®4BD, un matériau révolutionnaire pour roues dont la durée de vie exprimée en kilomètres est 30 % supérieure à celle des roues en qualité d’acier standard.
Ce matériau offre une plus grande résistance à la fatigue en sous-couche (l’endommagement provoqué par le contact roulant-glissant) et, par conséquent, au développement de déformations à la surface de roulement des roues. Tout ceci renforce la fiabilité et réduit les CCV.
Le responsable CCV de GHH-BONATRANS, Petr Janoš, ne dévoile pas les détails de cette technologie récemment brevetée, mais en décrit volontiers les avantages. « Nous avons étudié plusieurs compositions chimiques et testé différentes variétés de traitement thermique – chauffage ou refroidissement à des températures extrêmes – pour obtenir un durcissement accru. Mais ses avantages ne s’arrêtent pas au renforcement de la dureté des roues. »
Effectivement. Les relations de longue date entretenues par GHH-BONATRANS et SKF, qui lui fournit des roulements cartouches à rouleaux coniques (TBU), ont débouché sur une union technologique des cerveaux qui promet de réduire encore les CCV en diminuant la périodicité des opérations de maintenance.
« Pour faire baisser les CCV, il est indispensable de diminuer le nombre de révisions des bogies pendant la durée de vie du matériel roulant », estime Jan Babka, technico-commercial industrie ferroviaire chez SKF.
Les TBU SKF peuvent fonctionner jusqu’à 1,7 million de kilomètres entre chaque révision. Ceci permet de faire coïncider celle-ci avec celle des roues en BONASTAR®4BD.
Le développement continu des TBU a permis à SKF de réduire de 30 % le moment de frottement dans le roulement. La baisse des températures de fonctionnement prolonge la durée de vie de la graisse et rallonge donc considérablement les intervalles entre les interventions de maintenance des essieux montés.
D’après Jan Babka, ceci va permettre à l’utilisateur final de faire de très substantielles économies. L’association des TBU SKF et du BONASTAR®4BD permet aux opérateurs ferroviaires d’espacer davantage les opérations de maintenance et d’économiser jusqu’à 3 000 euros par bogie et par an, affirme-t-il.