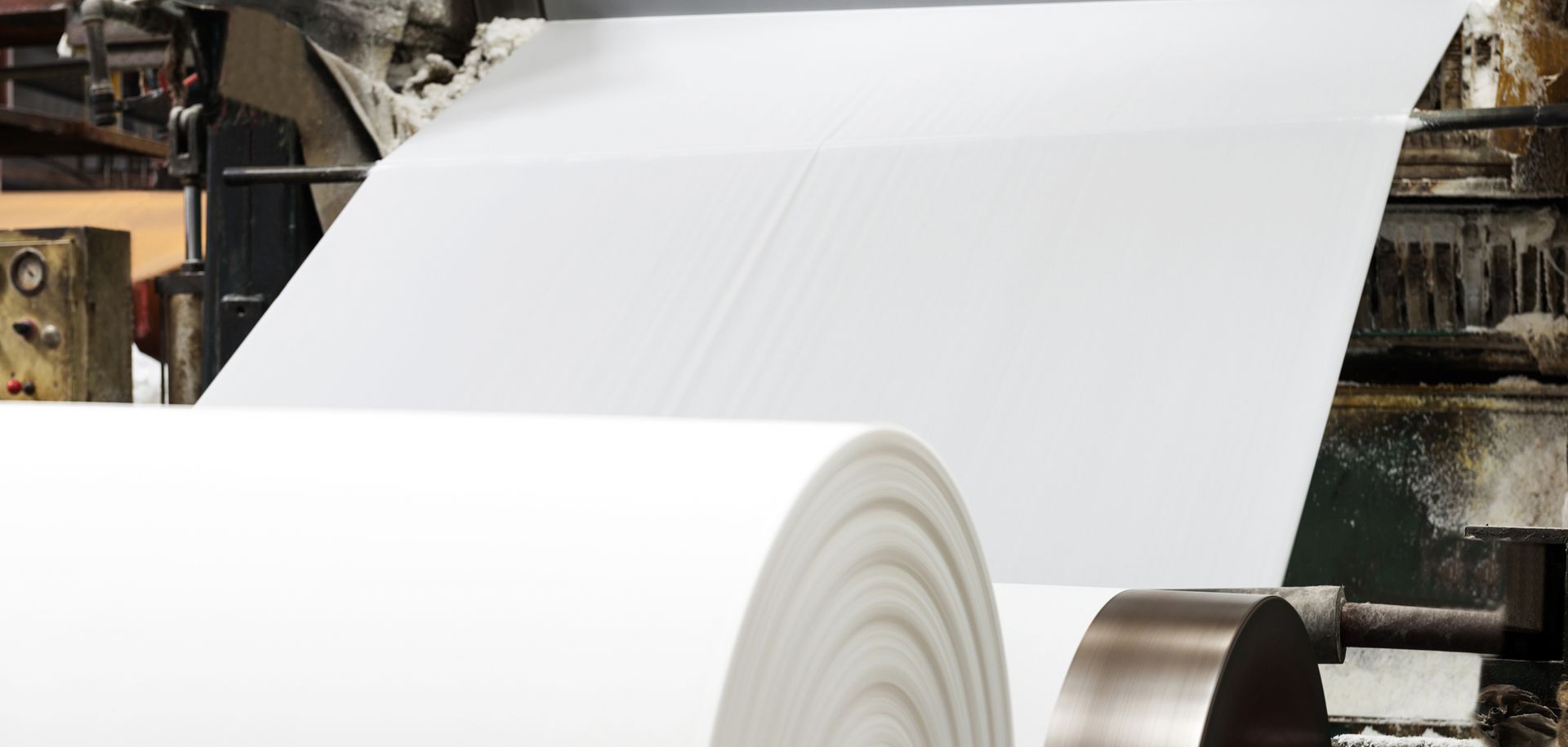
Une solution innovante pour l’industrie papetière
Le fabricant allemand de machines à papier, Voith, a fait appel aux équipes de l’usine DGBB de SKF située à Saint-Cyr-sur-Loire (Indre-et-Loire) pour développer de nouveaux roulements spécifiques. Ceux-ci ont permis d’augmenter de près de 50 % le temps moyen entre deux pannes mais aussi pour Voith d’intervenir beaucoup plus rapidement sur les machines de ses clients ; à ces résultats s’ajoute un système très innovant d’étanchéité facilitant considérablement le montage des roulements.
Voith
Ce groupe familial allemand, qui emploie environ 20 000 personnes dans le monde, est spécialisé dans la fabrication de machines à papier.
Voith a fait appel à l’usine autrichienne SKF (à Steyr, centre de développement des roulements spécifiques pour les applications industrielles) dans le but d’améliorer les roulements montés sur les rouleaux de ses machines. Il en est sorti une solution clé en main conjointement réalisée à Steyr et par le centre de développement de Saint-Cyr-sur-Loire (DGBB), l’usine de référence pour les roulements à section mince qui a permis la définition et la production dudit roulement.
Le produit est ensuite revenu en Autriche pour les tests de validation (graisse, vitesse étanchéité…) sur les bancs d’essais de Steyr. Une situation « 100 % européenne », en somme et dont la collaboration a donné naissance à une vraie solution innovante et sur mesure.
« Voith, fabricant d’énormes machines qui transforment la pulpe en bande de papier, était à la recherche d’une solution capable à la fois d’accroître la fiabilité et la performance de ses machines tout en facilitant leur maintenance grâce à un système de roulement facilement remplaçable lorsque nécessaire et, in fine, lui permettant d’intervenir rapidement et de façon optimale », résume Dominique Hibert, directeur de l’usine SKF chargée de produire les roulements rigides à billes – autrement appelés DGBB.
La particularité de ces machines réside d’une part dans leur complexité (pas moins de 1 500 roulements équipent les plus grandes d’entre elles, et de nature variée : roulements sphériques, coniques ou rigides à billes), d’autre part dans leur vitesse – pas moins de 1 500 mètres/minute – et leurs sollicitations élevées ; « n ‘oublions pas que la hantise des papetiers, c ‘est l’arrêt de production et le temps de remise en route après l’intervention, lequel atteint parfois plusieurs jours ».
Ce système permet de réduire les coûts de maintenance et de remplacement, mais également des délais d'intervention.
Fin 2014, partant d’un cahier des charges clairement défini autour d’exigences finalement très proches d’une entreprise « classique » (réduction des pannes, production horaire et fiabilité en hausse), les équipes de SKF se mettent au travail pour finalement proposer au client allemand un roulement à section mince. « Au regard des spécificités de Voith, nous avons proposé un roulement doté d’une bille sur deux, c ‘est-à-dire un emplacement vide sur deux dans la cage, révèle Dominique Hilbert. A ces billes en acier nous en avons ajouté une en céramique servant à nettoyer et à refaire la piste de roulement, réduisant ainsi considérablement les risques d’usure et assurant au roulement une surface lisse en permanence ».
Outre la partie billes, SKF est intervenu sur les cages permettant de séparer les billes entre elles. « Nous avons proposé un nouveau type de cages acceptant des vitesses de défilement encore plus élevées – jusqu’à 2 500 mètres par minute », poursuit Dominique Hilbert.
Une autre évolution majeure concerne cette fois l’étanchéité du roulement. Si l’environnement de ces roulements est propre (ceux-ci sont enfermés dans un rouleau), il n’en reste pas moins que la solution joue un rôle majeur d’étanchéité afin de conserver la graisse (celle-ci est centrifugée sur la bague extérieure à cause des fortes vitesses de rotation et de la bague extérieure tournante) à l’intérieur du roulement sans frottement (le rouleau est autoentraîné par la bande de papier). Concrètement, la solution consiste en un capot métallique avec un espace entre le capot et la bague intérieure (pas de frottement), et un joint torique entre le capot et la bague extérieure pour éviter que la graisse fuie sous l’effet de la centrifugation.
SKF France à Saint-Cyr-sur-Loire
Réparti sur 30 hectares, ce site est le plus grand de France avec près de 1 300 collaborateurs. Il produit 60 millions de roulements par an et compte la plus large gamme de produits et de solutions en France, appliqués aux secteurs de l’industrie, de l’automobile et du ferroviaire. Le site SKF de Saint-Cyr-sur-Loire comprend également des services logistiques, un laboratoire, un centre d’essai, ainsi que des activités de recherche et de développement.
Jusqu’à présent, les roulements étaient ouverts puis graissés par les utilisateurs. Désormais, celui-ci est directement graissé et fermé au moment du montage sur la machine. Concrètement, la solution consiste à clipser sur le joint torique un capot métallique. Ce système permet ainsi une durée de vie nettement plus importante, réduisant par là même les coûts de maintenance et de remplacement, mais également des délais d’intervention et de temps de maintenance ; « il suffit désormais de démonter et de remplacer le roulement, précise Dominique Hilbert. Le fait d’être prêt à l’emploi, le roulement est directement remplacé sans opération supplémentaire (graissage et jointage) ».