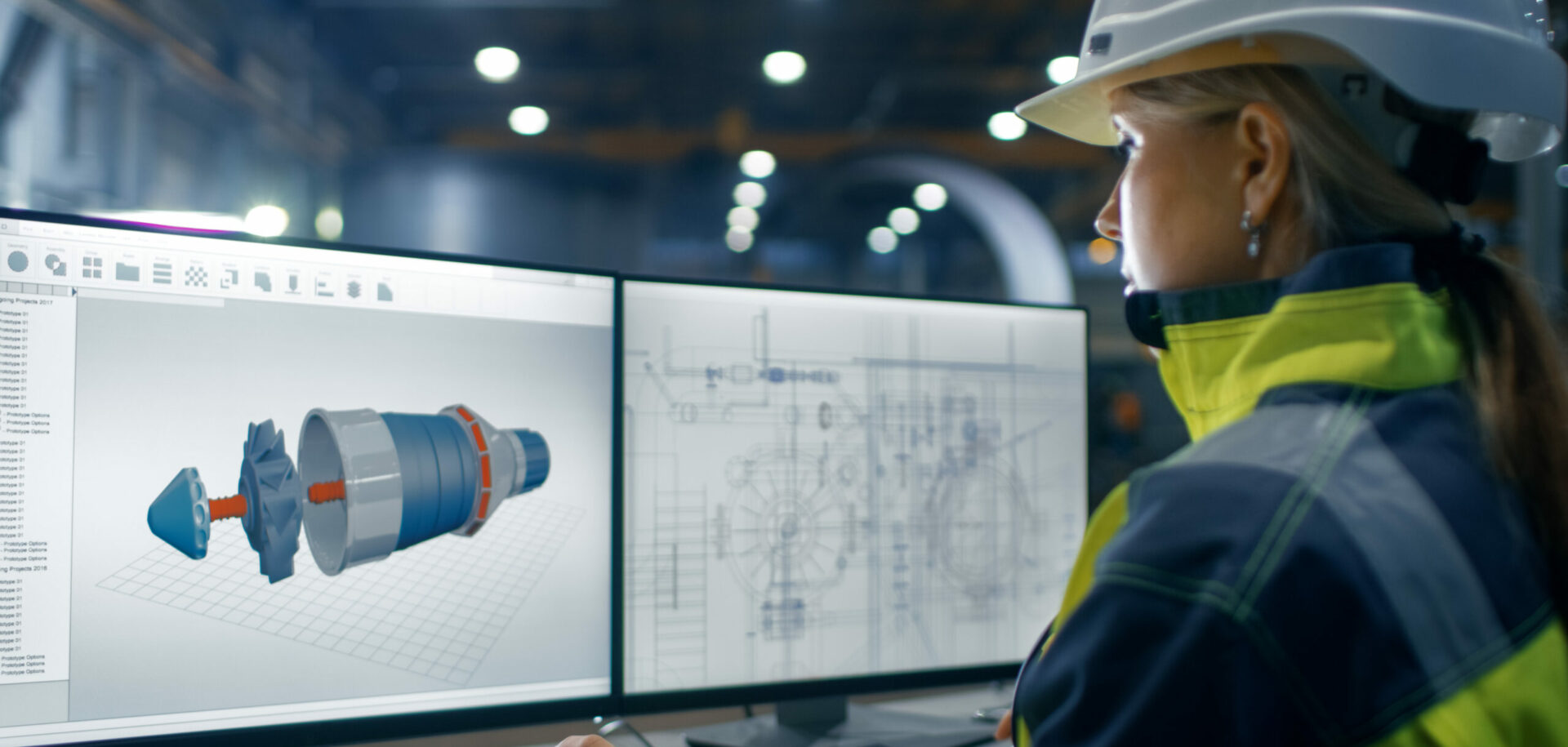
Wheel of fortune
To take a spin on the world’s tallest observation wheel, you have to visit the fabled Las Vegas Strip in the US and climb aboard the High Roller. It rotates on a pair of custom-designed SKF spherical roller bearings the largest ones ever built in SKF’s factory in Gothenburg, Sweden.
If you’re afraid of heights, don’t go up in the Las Vegas High Roller. At 168 metres, it is the world’s tallest observation wheel – three metres higher than the Singapore Flyer, the previous record holder, and 33 metres taller than the London Eye.
On the other hand, if you want to get a bird’s-eye view of the glitzy Las Vegas Strip and across the desert to the mountains on the far horizon, the High Roller is the way to go. The towering device, commonly known as a Ferris wheel, is the centrepiece of The Linq, Caesars Entertainment Corporation’s shopping, dining and entertainment district, developed at a cost of 550 million US dollars. The wheel stands just across the street from the Caesars Palace hotel-casino.
In casino parlance, a high roller is someone who wagers large amounts of money, so the name is doubly fitting for a Las Vegas attraction. The Las Vegas High Roller, looking like a gigantic bicycle wheel, has transformed the city’s skyline since it opened in March 2014. Its 28 spherical cabins are each able to accommodate 40 visitors, so fully loaded it can carry 1,120 people around.
The wheel rotates on two custom-designed SKF spherical roller bearings, each weighing about 8.8 tonnes, the biggest ever manufactured by SKF at its factory in Gothenburg, Sweden. (For a technical article on the wheel’s bearing assembly, see Evolution #1-2015.)
Jason Krolicki of Arup Engineering was the project manager for the design and engineering of the High Roller. “We specified SKF as one of the preferred suppliers from the beginning,” he says. “We had performance specification requirements that included a 50-year design life.”
During that half-century, the wheel will rotate an estimated 650,000 times, so the bearings have to be dependable and designed to resist fatigue. The engineering studies took into account such factors as wind loads, moisture levels and seismic events. The result is a wheel that should be turning not only until 2064, but continuously for some years to come.
The general contractor for the construction of the High Roller was the civil engineering firm American Bridge. Dan Schwarz, the project manager for the High Roller at American Bridge, says SKF faced some unusual challenges involved with installing an intricate mechanism in the Nevada desert.
“Concerns about lubrication and dust infiltration required a special sealing system that SKF was able to provide,” Schwarz says. “You can’t have contaminants such as sand getting inside the bearings, or they won’t last for the 50 years they want them to.”
The automatic lubrication system injects a total of about one kilogram of grease into each bearing every day, says Randy Greaser, the SKF account manager for the project. The grease lubricates the sealing system, which was also designed and supplied by SKF.
“What was challenging about this project is that you’re doing something one time,” Greaser says. It’s not like designing, say, a hub system for a car, when you have multiple opportunities to test the system and revise it. Numerous questions have to be answered in advance: How are you going to ship the bearings? How to lift them into place? How to install them on the spindle? How to mount them in the housing?
“You’ve got one shot to do it, and you’ve got to get it right,” he says. “It’s something that’s never been done before; we’re only going to do it once, so we have to do everything right the first time. It was the most interesting project I’ve ever worked on at SKF.”
Jason Krolicki of Arup Engineering says SKF was an important partner in the High Roller project. “The people at SKF were professionals through and through,” he says. “It was critically fundamental to have a design partner like SKF engaged in the project because we knew the bearing issue was so important to its success. Their professionalism came through from the beginning.”