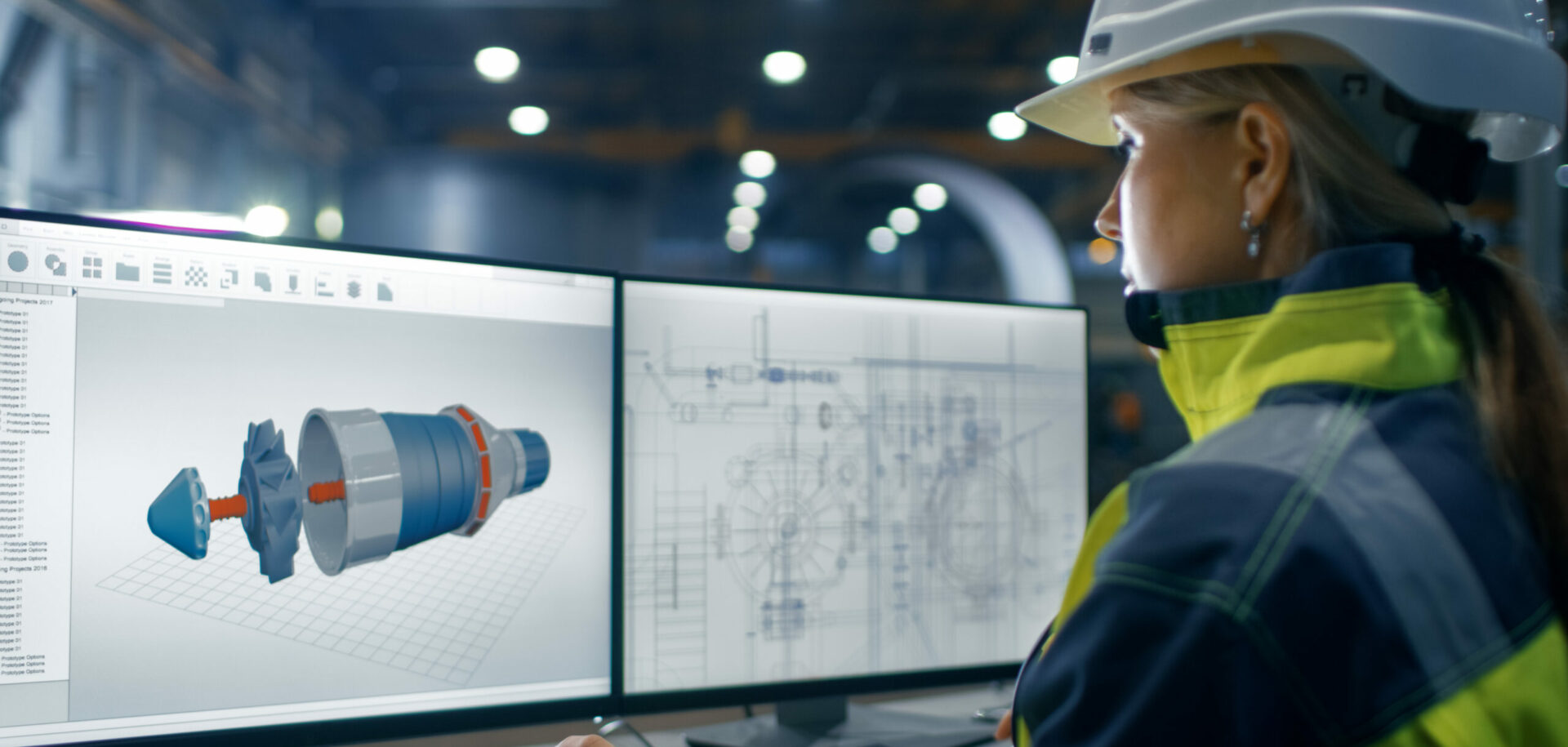
Meccanismi di danneggiamento da impronte sulle piste dei cuscinetti
Le impronte prodotte da particelle contaminanti sulle piste di rotolamento provocano danneggiamenti superficiali nei cuscinetti volventi compromettendone la durata di esercizio. Da molti anni i calcoli SKF della durata ne tengono conto mediante il fattore di contaminazione ηc. Recentemente la stessa SKF ha elaborato modelli avanzati e ha condotto esperimenti per prevedere le interazioni tra i solchi e le impronte lasciate dal passaggio delle particelle e il lubrificante presente sulle piste. L’articolo esplora tali interazioni considerando anche gli effetti degli slittamenti, e spiega in che modo il danneggiamento s’instaura e progredisce.
Sintesi
Sintesi
Se si conoscono i fenomeni che innescano e propagano i vari tipi di danneggiamento sulle superfici dei cuscinetti è possibile individuare metodi che riducano l’incidenza o la gravità dei danneggiamenti stessi. In questo articolo gli ingegneri SKF illustrano il lavoro teorico e sperimentale condotto sull’insorgere e sull’evoluzione delle impronte. Essi hanno creato modelli avanzati della teoria SKF dei cuscinetti che sono in accordo con i dati sperimentali e che spiegano le cause alla base dei danneggiamenti superficiali. Questo lavoro mette anche in evidenza l’importanza della pulizia, di un montaggio appropriato e di una lubrificazione adeguata.
Contatto vendite
Guillermo Morales
Le particelle solide presenti nei contatti lubrificati hertziani provocano dannose impronte superficiali. Il danno può essere influenzato anche dall’entità dei piccoli slittamenti locali dovuti alla cinematica del contatto. L’ammontare dello slittamento differenzia sostanzialmente gli ingranaggi dai cuscinetti volventi. Per conoscere meglio l’evoluzione del processo di danneggiamento è stata condotta un’analisi del comportamento dinamico delle impronte superficiali nei contatti lubrificati hertziani fortemente caricati. In particolare sono stati studiati gli effetti della pressione idrodinamica, delle sollecitazioni nel materiale e dell’affaticamento superficiale attorno alle impronte, mettendo anche a confronto le previsioni teoriche di cedimento con i risultati sperimentali. Quando gli slittamenti nei contatti sono di bassa entità, come è il caso dei cuscinetti volventi, il processo di danneggiamento è dominato dalla riduzione dello spessore del film e dall’affaticamento superficiale attorno ai bordi delle impronte, mentre, con forti slittamenti, come negli ingranaggi, è più probabile che si instauri un processo di affaticamento, dovuto al sovrapporsi di due massimi valori dell’andamento ondulatorio della dinamica delle pressioni.
Nei contatti lubrificati hertziani fortemente caricati, la presenza di solchi e impronte superficiali dà origine a danneggiamenti. Questi tipi di contatti sono presenti in molti organi meccanici e generalmente operano in presenza di una lubrificazione elastoidrodinamica (EHL) e talvolta di una lubrificazione mista. Le anomalie superficiali possono creare localmente variazioni nello spessore del film e fluttuazioni di pressione, che, a loro volta, causano concentrazioni delle sollecitazioni. Nel passato molti ricercatori hanno studiato le sollecitazioni indotte dalle anomalie geometriche superficiali in contatti di tipo hertziano (EHL) utilizzando metodi numerici, sperimentali e semi-analitici. La tendenza attuale verso la riduzione delle dimensioni delle macchine e un aumento dell’efficienza e delle temperature di esercizio conduce a un aumento delle sollecitazioni superficiali nei cuscinetti volventi, nei quali spesso si riscontrano un minore spessore del film lubrificante, velocità più alte (o anche molto basse) e fenomeni dinamici più marcati. È molto probabile che tutti questi fattori aumentino il rischio di guasti a seguito della presenza di irregolarità delle piste, ad es. impronte. Ai fini di una durata ottimale dei cuscinetti, la pulizia dell’olio è molto importante e, per tale motivo, sia il modello SKF della durata [1] sia la norma ISO 281 [2] prevedono, come parametro di input, appunto le caratteristiche di pulizia del lubrificante. In un precedente articolo [3] erano stati discussi gli effetti della pulizia del lubrificante e il suo impatto sulla durata, mentre qui diamo una descrizione più dettagliata del comportamento delle impronte relativo alle condizioni di lubrificazione del contatto.
Molti autori hanno studiato l’argomento prendendo in considerazione contatti sia lubrificati sia senza lubrificazione, includendo sia alti che bassi valori di slittamento, tuttavia senza dare un quadro complessivo sufficientemente chiaro dei meccanismi di cedimento. Cheng et al. [4] hanno indagato sullo sviluppo delle cricche a fatica in contatti hertziani volventi su una superficie in cui erano state prodotte artificialmente impronte e solchi. I contatti erano in condizioni di lubrificazione EHL, con un fattore di slittamento S = ±0,24, ossia, con i simboli di fig. 2, S = 2 (u2-u1)/(u2+u1). Utilizzando un fluido non-newtoniano, l’analisi era stata integrata da alcune simulazioni numeriche, le quali indicavano come la presenza di slittamenti modifichi la posizione e la grandezza delle fluttuazioni di pressione che si sviluppano attorno alle impronte. Questo fenomeno è più marcato sul bordo anteriore dell’impronta (leading edge) quando la superficie incisa viaggia più lentamente di quella liscia e viceversa (fig.1). Nélias e Ville [5], Ville e Nélias [6] hanno eseguito numerose osservazioni e simulazioni numeriche di impronte sottoposte a un contatto EHL in condizioni di puro rotolamento e di rotolamento con slittamento. Le simulazioni numeriche di Nélias e Ville [5] con semplici fluidi newtoniani avevano dimostrato come un aumento dello slittamento aumenti la sollecitazione massima di taglio al di sotto del contatto (per es. un maggiore attrito con l’aumentare dello slittamento, come risulta da un semplice fluido newtoniano). Quindi veniva osservato che quanto maggiore è lo slittamento imposto sul contatto EHL tanto più elevata è la sollecitazione massima di taglio sotto la superficie e tanto più breve è la durata a fatica attorno all’impronta. Ville e Nélias [6] hanno condotto anche esperimenti e alcune simulazioni per S = ±0,015. Gli esperimenti hanno confermato le prime conclusioni, secondo le quali il punto preferito d’inizio del danno a fatica dipende dalla direzione dell’attrito. Un’impronta sulla superficie più lenta tende a sviluppare un cedimento a fatica sul bordo anteriore dell’impronta stessa, mentre una superficie più veloce tende a sviluppare il cedimento su quello posteriore. In caso di puro rotolamento, si pensa che le fratture da fatica possano apparire da entrambi i lati. In esperimenti con contatti non lubrificati (Xu et al. [7]) si è potuto notare come la cricca iniziale compaia nel bordo posteriore dell’impronta sulla superficie conduttrice; Xu et al. hanno così concluso che è la forza d’attrito sulla superficie di contatto che rappresenta il principale meccanismo che favorisce la frattura delle superfici con impronte.
Tipi di impronte
In fig. 2 è rappresentata la geometria idealizzata di un’impronta. Supponendo che la particella venga intrappolata nel contatto (le particelle molto grandi non vengono intrappolate, mentre quelle molto piccole attraversano il film lubrificante senza provocare impronte), si producono così impronte di forma diversa a seconda della durezza e della geometria della particella e della durezza del materiale che subisce l’impronta stessa. Le impronte di grande diametro (ø), molto profonde (hp) e con bordi a forte rilievo (sp) sono le più pericolose. La fig. 3 mostra le caratteristiche di particelle di tipo diverso, associate al corrispondente tipo d’impronta. Le particelle di bassa durezza malleabili o duttili (di fibra o di metallo) producono impronte poco profonde dotate di bordi a rilievo. Le particelle fragili e dure si frammentano in numerose particelle molto piccole producendo agglomerati di piccole impronte. Le particelle friabili, tenaci e dure, producono agglomerati più grandi di materiale frammentato, che incidono l’acciaio, dando luogo a impronte con spigoli vivi.
Interazioni
Per meglio comprendere le interazioni tra le impronte e il prospiciente lubrificante rinchiuso in un contatto hertziano, la SKF ha elaborato appositi modelli ed esperimenti [8, 9], volti a studiare i fenomeni associati. Qui di seguito viene descritto in primo luogo il comportamento delle impronte o di altri disturbi
geometrici delle superfici, che entrano nella zona di contatto.
Disturbo geometrico della superficie in un contatto lubrificato fortemente caricato
Quando un disturbo della superficie penetra in un contatto EHL, genera due tipi di onde di pressione e di spessore del film lubrificante. La prima è l’onda di pressione prodotta dalla deformazione elastica stazionaria del disturbo. Essa si accompagna ad un’onda opposta nello spessore del film che viaggia all’interno del contatto con la stessa velocità della superficie che la produce (u2); questa è denominata “integrale particolare”. La seconda onda è prodotta dal disturbo all’ingresso del contatto, dato che ogni anomalia geometrica su una delle superfici agisce come una valvola che condiziona il flusso del lubrificante che penetra nel contatto. Quest’onda possiede componenti in forma sinusoidale dello spessore del film e della pressione che si propagano all’interno del contatto con la velocità media del lubrificante ( ū = (u2+ u1)/2). Questa è denominata “funzione complementare”; le ondulazioni finali della pressione e dello spessore del film sono la combinazione di dette componenti (fig. 4).
Disturbo geometrico della superficie nei contatti di rotolamento-slittamento con condizioni di basso slittamento (cuscinetti)
Le condizioni di basso slittamento si verificano normalmente al centro dei contatti sulle piste dei cuscinetti volventi (S < 0,05). Mediante il modello numerico SKF, è possibile simulare il passaggio di un’impronta attraverso un contatto lubrificato fortemente caricato e calcolare sia la geometria deformata che viene generata all’interno del contatto sia le ondulazioni di pressione che si sviluppano. La fig. 5 mostra l’impronta “modello” iniziale imposta sulla superficie superiore del contatto e il profilo lungo l’asse dell’impronta deformata isolata e l’ondulazione di pressione generata al centro del contatto, calcolata in condizioni di puro rotolamento. Se si aumenta leggermente lo slittamento in entrambi i sensi (–0,05 < S < 0,05) si alterano considerevolmente i risultati. La stessa fig. 5 mostra come lo spessore deformato del film si presenti collassato nella parte anteriore dell’impronta (nel leading edge). Nello stesso tempo si notano pressioni leggermente maggiori nel bordo posteriore (nel trailing edge). Tutto ciò fa pensare che quando esiste un buon film lubrificante, è probabile che le impronte cedano prima sul bordo posteriore, per il fatto che le pressioni sono maggiori, anziché sul bordo anteriore dell’impronta per contatto metallo su metallo. Tuttavia, se la lubrificazione è scarsa, è prevedibile che si manifesti usura e magari affaticamento superficiale sul bordo anteriore. Tutto ciò è in pieno accordo con i risultati degli esperimenti (fig. 6) condotti dall’SKF ERC, presso il quale si sono impiegati normali cuscinetti a sfere in cui si erano praticate artificialmente delle impronte sulle piste. In questi esperimenti è stata osservata una zona di affaticamento superficiale sul bordo posteriore dell’impronta (micro-scagliature), mentre sul bordo anteriore si era manifestata una notevole usura, probabilmente causata dal film lubrificante localmente collassato.
Disturbo geometrico della superficie nei contatti di rotolamento-slittamento con condizioni di slittamento moderato (ingranaggi)
Negli ingranaggi possono essere presenti condizioni di slittamento moderato (S ~ 0,1). Utilizzando il modello numerico SKF con comportamento non-newtoniano del fluido (quindi più realisticamente aumentando lo slittamento non aumenta l’attrito), è possibile simulare il passaggio di un’impronta attraverso il contatto lubrificato con le dovute condizioni di slittamento.
La fig. 7 mostra le ondulazioni isolate di pressione, lo spessore del film e le sollecitazioni sotto-superficiali normalizzate di von Mises calcolate per un contatto fortemente caricato, in due diverse condizioni di moderato slittamento (S=0,1 – superficie inferiore liscia più veloce di quella superiore incisa e S=–0,1 – superficie inferiore liscia più lenta di quella superiore incisa). Per queste condizioni moderate di slittamento si può vedere come, invertendo il segno dello slittamento si inverta la posizione della massima ondulazione di pressione, quindi la posizione del primo possibile cedimento. Ciò forse spiega alcuni risultati apparentemente contradditori negli esperimenti citati nella letteratura.
Disturbo geometrico della superficie nei contatti di rotolamento-slittamento con condizioni di slittamento elevato (ingranaggi)
Elevati slittamenti (S > 0,1) non si manifestano nella parte centrale delle piste dei cuscinetti, mentre possono essere presenti nei contatti di ingranaggi. Con il modello numerico SKF che adotta un realistico comportamento non-newtoniano del fluido lubrificante, (cioè un aumento dello slittamento non comporta un aumento dell’attrito) è possibile simulare il passaggio di un’impronta attraverso il contatto lubrificato con le dovute condizioni di slittamento. La fig. 8 mostra le ondulazioni isolate della pressione e dello spessore del film in funzione del tempo per una condizione di forte slittamento (S= –0,5 – la superficie liscia inferiore è più veloce di quella superiore incisa).
Nella fig. 8 si può vedere come la posizione originaria dell’impronta segua il valore minimo dell’ondulazione di pressione (Δp); tuttavia, dato che lo slittamento è elevato, le due componenti d’onda hanno abbastanza tempo per separarsi progressivamente una dall’altra; questo avviene per le ondulazioni sia della pressione sia dello spessore del film. Nell’ultimo intervallo di tempo (Δt), l’ondulazione dello spessore del film (Δh) generata all’ingresso del contatto ha già abbandonato il contatto, mentre quella della pressione è ancora all’interno del contatto stesso. In questo caso, il cedimento del contatto dipenderà da come le onde di pressione si sovrappongono e si combinano durante i numerosi cicli di affaticamento. Il cedimento, in questo caso, può comparire anche in un punto molto lontano dell’impronta.
Affaticamento della superficie attorno alle impronte nei cuscinetti volventi
Come indicato in fig. 6, nei cuscinetti si osserva spesso un affaticamento della superficie (micro-scagliature) attorno alle impronte nell’area vicino ai bordi. In generale tale fenomeno compare prima sul bordo dove l’ondulazione di pressione è maggiore. Se lo spessore del film è elevato, l’affaticamento attorno all’impronta impiega molto tempo prima di progredire o può non progredire affatto; se però la lubrificazione non è buona, l’evoluzione del danno è facilitata. Il modello di affaticamento superficiale elaborato dalla SKF [9], può essere applicato anche allo studio dell’affaticamento delle impronte superficiali. Questo modello utilizza lo stesso calcolo della pressione idrodinamica come sopra descritto, ma modificato per tenere conto di una lubrificazione parziale (quindi con alcune zone a contatto metallo su metallo). In questa sezione le simulazioni tendono a dimostrare che l’affaticamento superficiale che si sviluppa attorno alle impronte ha lo stesso fondamento fisico del normale affaticamento superficiale delle piste in caso di scarsa lubrificazione. I risultati sperimentali e delle simulazioni numeriche sono indicati nelle figg. 6 e 9. I risultati sperimentali riportati nella fig. 9a sono dopo 2.250 milioni di cicli di carico. La fig. 9b mostra il profilo della pressione di contatto e una mappa delle sollecitazioni sotto-superficiali al centro del contatto lungo l’asse X. La fig. 9d riporta il progresso dell’affaticamento superficiale attorno all’impronta secondo quanto previsto dal modello numerico per questo caso di 2.250 milioni di cicli di carico; si nota come i risultati di figg, 9a e 9d siano infatti molto simili. La fig. 9c riporta la simulazione numerica del progredire dell’affaticamento superficiale dopo 750 milioni di cicli di carico. Questo risultato si può confrontare con quello di fig. 6; si nota come anche in questo caso i due risultati siano simili.
Discussione e conclusioni
Nei contatti lubrificati di rotolamento-slittamento fortemente caricati le impronte costituiscono un notevole rischio per la durata di esercizio degli organi di macchine. Nel presente studio sono stati applicati i modelli avanzati SKF di simulazione all’analisi degli esperimenti eseguiti su cuscinetti radiali presso l’SKF ERC nell’intento di conoscere meglio gli effetti delle variazioni di pressione idrodinamica che sono causate dal passaggio delle impronte attraverso i contatti di rotolamento-slittamento. Le simulazioni spiegano la presenza di una zona opaca che si forma sul bordo anteriore del contatto (vedere i risultati della fig. 6 confrontandoli con la fig. 5, che mostra la previsione di collasso del film lubrificante sul bordo anteriore del contatto). Il forte affaticamento superficiale del bordo posteriore dell’impronta è anche in linea con la previsione di fig. 5 (con S = 0). In verità, in tutti i casi calcolati, il bordo posteriore dell’impronta è sempre quello soggetto al più alto valore della pressione. Per uno slittamento virtualmente nullo è assente l’area opaca del bordo anteriore dell’impronta (vedere la fig. 6 di [8]), mentre si genera una leggera micro-scagliatura. Ciò si spiega con la presenza di un micro-slittamento dovuto a una deformazione microscopica dei corpi in contatto, che in pratica non si può evitare, anche nel caso di contatti hertziani in presenza di slittamento nominale di valore zero. Con una lubrificazione elastoidrodinamica o parzialmente tale, a causa delle proprietà piezo-viscose del lubrificante e dell’attrito limite, questa microscopica quantità di slittamento è sufficiente affinché si generi la trazione superficiale necessaria per la formazione dell’affaticamento superficiale (tuttavia è insufficiente per un’azione di lucidatura). In fig. 9 è riportato il calcolo del progresso dell’affaticamento superficiale in funzione della quantità di cicli di carico per il caso dei cuscinetti volventi. Si può notare come in questo caso il modello di calcolo di previsione della fatica si accordi bene con le osservazioni sperimentali. Nell’articolo sono riportate alcune microfotografie delle impronte, come esempi di una quantità di altri test, i cui risultati sono tutti in linea con i campioni sperimentali qui descritti. Pertanto il buon accordo tra il modello di previsione e i risultati dei test consente una conclusione positiva per quanto riguarda la validità sperimentale del lavoro.
Da quanto sopra si possono trarre le seguenti conclusioni:
- La modellazione della durata a fatica di tipici difetti superficiali e dei valori estremi di rugosità come solchi, impronte e incisioni di varia origine, richiede una valutazione delle variazioni di pressione e del relativo spessore locale del film quando l’impronta attraversa il contatto hertziano. Il presente modello numerico non-newtoniano è uno strumento efficace per migliorare la conoscenza del fenomeno.
- Con i bassi slittamenti (S << |0.1|) presenti nei contatti hertziani dei cuscinetti a sfere e a rulli la massima pressione di rotolamento è sempre nella zona posteriore dell’impronta, mentre nella zona anteriore domina l’usura. Entro questo campo di slittamento, la pressione di rotolamento sull’impronta non aumenta in modo significativo con l’aumentare dello slittamento stesso [8]. Il rischio di affaticamento superficiale dovuto all’impronta dipende quindi principalmente dal numero di cicli di passaggio.
- Quando lo slittamento aumenta a valori di S > |0.1| oppure con ridotti spessori del film, con uno slittamento negativo si può verificare uno spostamento verso la zona anteriore del contatto della posizione in cui la pressione ha il valore massimo, il che spiega i risultati ottenuti dagli altri ricercatori, che hanno osservato cedimenti nella parte anteriore dell’impronta.
- Con un ulteriore aumento dello slittamento a valori S ≈ 0.3 − 0.5, come negli ingranaggi, il processo di affaticamento sulle impronte è più complesso, in quanto le onde della pressione e dello spessore del film sono separate. La posizione della massima pressione diventa dipendente dalla progressione del tempo, dalla dimensione del contatto hertziano e dalle condizioni di lavoro.
- Le condizioni di lavoro e le risultanti pressioni idrodinamiche hanno un effetto prevalente nel controllo delle pressioni massime generate durante il ciclo di carico del passaggio dell’impronta. Nelle piste dei cuscinetti, il rischio di affaticamento superficiale dell’impronta è correlato prevalentemente a queste pressioni più che al valore del rapporto slittamento-rotolamento o alla direzionalità dell’attrito associato. Tuttavia la direzionalità della sollecitazione da attrito può avere un suo ruolo durante la fase di propagazione delle cricche che si sviluppano attorno alle impronte e questo può spiegare alcune conclusioni riportate in lavori precedenti. Si è anche dimostrato che il fenomeno dell’affaticamento superficiale che si manifesta attorno alle impronte può essere descritto con lo stesso modello fisico dell’affaticamento superficiale delle piste dei cuscinetti [9].
Come ridurre i rischi delle impronte
Per ridurre il rischio di impronte si può agire in tre modi:
- il lubrificante va mantenuto il più pulito possibile, ossia bisogna filtrare bene l’olio, usare grasso pulito e conservare integre le tenute
- si devono seguire i suggerimenti di montaggio della SKF, in quanto con un montaggio non corretto si possono provocare impronte sulle piste
- occorre mantenere sempre un buon film lubrificante nei cuscinetti scegliendo, un lubrificante avente una viscosità idonea. Un film correttamente formato può ridurre al minimo l’affaticamento superficiale attorno alle impronte e può estendere la durata delle superfici.
Bibliografia
[1] Catalogo Generale SKF – 6000/I IT, Giugno 2008.
[2] Norma Internazionale: Cuscinetti volventi – Coefficiente di carico dinamico e durata di base, ISO 281
[3] Gabelli, A., Morales-Espejel, G.E., Ioannides, E., “Lubrificazione e Contaminazione – Effetti sulla durata dei cuscinetti, parte 2” – SKF Evolution #3 2010.
[4] Cheng, W., Cheng, H.S., and Keer, L.M. (1994), “Experimental Investigation on Rolling/Sliding Contact Fatigue Crack Initiation with Artificial Defects,” Tribology Transactions, 37, pp 1–12.
[5] Nélias, D. and Ville, F. (2000), “Detrimental Effects of Debris Dents on Rolling Contact Fatigue,” Journal of Tribology, 122, pp 55–64.
[6] Ville, F. and Nélias, D. (1999), “Early Fatigue Failures in EHL Contacts Due to Dents in EHL Contacts,” Tribology Transactions, 42, pp 795–800.
[7] Xu, G., Sadeghi, F., and Hoeprich, M. R. (1998), “Dent Initiated Spall Formation in EHL Rolling/Sliding Contact,” Journal of Tribology, 120, pp 453–462.
[8] Morales-Espejel, G.E., Gabelli, A. (2011), “The Behaviour of Indentation Marks in Rolling-Sliding Elastohydrodynamically Lubricated Contacts,” Tribol. Trans., vol. 54, pp 589–606.
[9] Morales-Espejel, G.E., Brizmer, V. (2011), “Micropitting Modelling in Rolling-Sliding Contacts: Application to Rolling Bearings,” Tribol. Trans., vol. 54, pp 625–643.