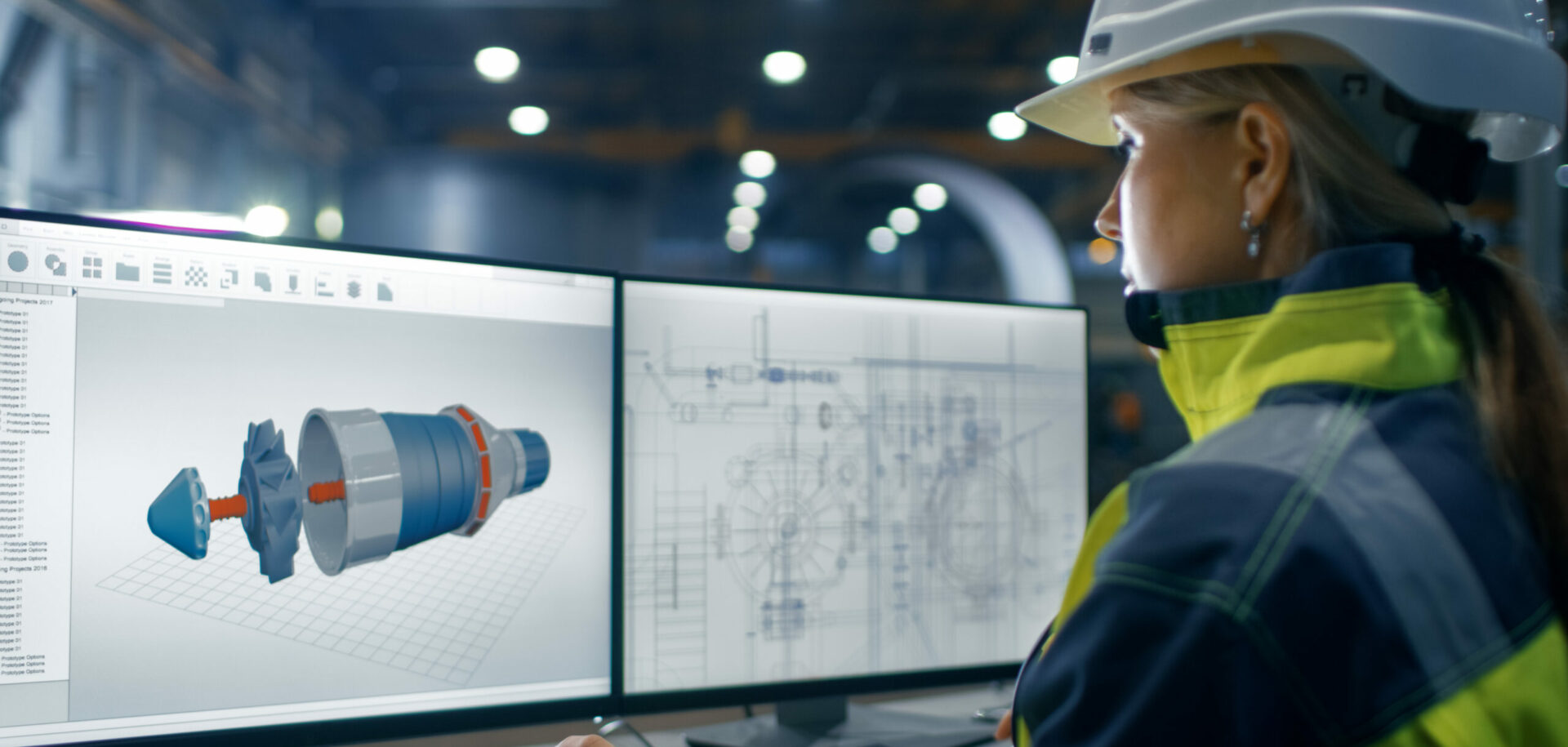
Modellazione e simulazioni decisive per la costruzione della più grande ruota panoramica del mondo
Per costruire la più grande ruota panoramica del mondo, come la High Roller di Las Vegas, si sono utilizzati componenti e processi di lavorazione tecnicamente avanzati. Nella sua collaborazione con la Arup, progettista della ruota, e l’American Bridge, la ditta appaltatrice, la SKF ha utilizzato gli strumenti di analisi e progetto più recenti e idonei ad assicurare continuità di funzionamento al gruppo costituito dal mozzo e dall’albero principale.
Sintesi
Nelle operazioni di costruzione e installazione del sistema di cuscinetti di dimensioni mai viste per la più grande ruota panoramica del mondo, la SKF ha profuso tutta la sua esperienza nella progettazione e nelle analisi per fare in modo che la durata dei cuscinetti stessi soddisfi i requisiti operativi estremamente rigorosi. L’attenta analisi eseguita utilizzando, per ogni esigenza tecnica, strumenti sofisticati di modellazione e simulazione, ha consentito di identificare il sistema più idoneo.
Link correlati
Contatto vendite
Randy A. Greaser, Randy.A.Greaser@skf.com
Con i suoi 168 metri di altezza, la High Roller di Las Vegas è la più grande ruota panoramica del mondo. Ognuna delle sue 28 gondole con aria condizionata porta 40 passeggeri in un viaggio che dura circa mezzora. Fa parte di The Linq, un’area all’aria aperta da 550 milioni di dollari, attrezzata per shopping, ristorazione e divertimento, e ha trasformato il panorama della città, dando ai visitatori una nuova vista sulla Strip. Iniziata nel 2011, l’High Roller è stata inaugurata a marzo del 2014.
Dietro allo sfarzo e al glamour che questa nuova attrazione conferisce allo skyline di Las Vegas c’è stata l’ambizione di costruire una struttura gigantesca, ma capace di soddisfare rigorose esigenze di sicurezza e reggere condizioni di lavoro gravose. Alla SKF venne chiesto di studiare, fornire e assemblare il sistema dei cuscinetti dell’albero principale da parte del maggiore appaltatore, l’American Bridge, il quale ne ha curato l’installazione, lavorando insieme ai progettisti delle strutture della Arup Engineers, responsabile delle specifiche. L’Arup aveva già lavorato a quella che era in precedenza la ruota panoramica più grande, la Singapore Flyer.
La ruota dell’High Roller gira su un paio di cuscinetti orientabili a rulli speciali, che pesano ciascuno circa 8,8 tonnellate e hanno un diametro esterno di 2,3 metri, un foro di 1,6 metri e una larghezza di 0,63 metri; i rulli sono 30 per corona. I cuscinetti sono i più grandi finora costruiti presso lo stabilimento SKF di Göteborg. Per determinarne il gioco interno radiale ottimale sono state utilizzate tecniche di simulazione. Tra le caratteristiche speciali citiamo i fori di lubrificazione sull’anello interno (esec. W26), il rivestimento SKF NoWear dei rulli e quello in PTFE del foro. Sono inoltre stati previsti una lubrificazione automatica di tipo avanzato e particolari sistemi di tenuta.
L’High Roller è una ruota tensionata di 143 metri di diametro. Oltre ai due cuscinetti SKF, è dotata di 4 piloni di supporto in acciaio, un grosso braccio di controventatura, un albero principale fisso, un mozzo rotante, un “cerchione” tubolare con una sezione di 2 metri di diametro e 112 cavi radiali d’acciaio. Le cabine sono montate all’esterno del cerchione e vengono fatte ruotare da motori elettrici per mantenerne il pavimento in posizione costantemente orizzontale.
Criteri di progetto
Per quanto riguarda il sistema dei cuscinetti dell’albero principale (fig. 1), si sono dovute affrontare diverse sfide, non ultima quella di realizzare una soluzione sicura e affidabile. Nel caso dell’albero e dei cuscinetti vanno tenuti in conto i carichi elevati e le grosse deformazioni degli alloggiamenti, unitamente alla variabilità di allineamento dell’albero stesso. Secondo le specifiche il carico è pari a 1.350 tonnellate su ciascun appoggio. Per ciascuno dei 56 cavi radiali inferiori, la tensione è di 132 tonnellate, mentre per quelli superiori è di 47 tonnellate, con una tensione totale radiale dei cavi di 4.600 tonnellate.
Nel progetto si è assunta una velocità di rotazione attorno all’asse Z pari a 0,033 giri/min. Nel modello si è ipotizzato un carico costante su ciascun cuscinetto dovuto al vento e applicato sull’anello esterno nella direzione dell’asse Z. Nelle simulazioni si sono ipotizzati vari carichi dovuti al vento in diverse condizioni di esercizio. Il disallineamento calcolato dei cuscinetti ha previsto carichi costanti dovuti al vento nelle varie condizioni; nelle simulazioni non è stato previsto l’effetto di venti variabili.
È anche stato considerato il carico sui cuscinetti durante l’installazione. La rottura di un cuscinetto è estremamente costosa e quindi la SKF ha deciso di applicare il metodo Six Sigma alla progettazione, alla fabbricazione e all’assemblaggio. In questa prestigiosa applicazione, l’albero e i cuscinetti devono soddisfare rigorosi criteri in termini di prestazioni; in particolare ai cuscinetti è stata data la massima attenzione per assicurarne la lunga durata di esercizio. A tale scopo la SKF ha utilizzato su larga scala strumenti sofisticati di analisi, basati sui più moderni principi dell’ingegneria.
Approccio al progetto
Disegno e analisi del progetto sono stati suddivisi in quattro fasi utilizzando su larga scala programmi di modellazione e analisi, per ottenere un risultato finale coerente con le effettive condizioni operative. L’obiettivo era di valutare le complesse interazioni tra tutti i componenti del sistema e di identificare i key performance indicator. Essenzialmente si trattava di studiare gli effetti delle deformazioni degli alloggiamenti, la distribuzione dei carichi e le pressioni nei contatti sulle piste dei cuscinetti. Una particolare attenzione è stata dedicata alla valutazione degli effetti di carichi e deformazioni sulle prestazioni dei cuscinetti in termini di sforzi e movimenti.
La SKF dispone di strumenti avanzati di simulazione, sviluppati appositamente per lo studio dei sistemi di cuscinetti e per valutare i diversi fattori che ne influenzano il comportamento, quali il gioco interno, i disallineamenti, la flessibilità della struttura di supporto e le diverse condizioni al contorno.
Le fasi del progetto hanno avuto il seguente sviluppo:
Fase 1 – Definizione progetto con Design for Six Sigma (DfSS)
- Definizione progetto
- Documenti base DfSS
- Acquisizione dati per il progetto
Fase 2 – Simulazioni per le analisi
- Modello di cuscinetto rigido con carichi su punti
- Inflessioni e deformazioni come input
- Modello flessibile comprendente il mozzo e i componenti dell’albero
- Carichi dovuti alla tensione dei cavi (4 simulazioni)
Fase 3 – Analisi sensibilità cuscinetti
- Effetti delle variazioni delle condizioni al contorno
- Riesame del disegno interno dei cuscinetti
- Studio parametrico della geometria interna dei cuscinetti
- Analisi FE della gabbia
Fase 4 – Analisi FE degli sforzi trasmessi dalla bussola all’installazione
- Creazione del modello FE
- Analisi FE delle forze di avanzamento senza il carico dei cavi
- Analisi FE delle forze di avanzamento con il carico dei cavi
Nella fase 1 si è definito in modo chiaro il progetto e si sono identificati tutte le informazioni e documenti necessari per seguire il metodo Design for Six Sigma (DfSS). Parte della metodologia DfSS è l’impiego dell’FMEA (Failure Mode and Effect Analysis) per dare un indirizzo allo sviluppo delle attività di ingegneria e delle soluzioni. L’FMEA è stata adottata per identificare le possibili cause di guasto basandosi su precedenti esperienze ed è servita come riferimento nella scelta delle caratteristiche del disegno, delle attività di simulazione e delle conseguenti raccomandazioni. L’FMEA è stata elaborata da un team costituito da Arup, American Bridge e SKF.
Il punto di partenza per la creazione dei documenti base del DfSS è stata l’identificazione dei parametri che influenzano la durata a fatica di cuscinetti (fig. 2), nell’intento di produrre un diagramma a blocchi che definisca le interazioni del sistema di cuscinetti con le parti circostanti e comprenda gli input e gli output desiderati. Per identificare tutti i parametri che sovrintendono alle prestazioni, o quelli che su queste hanno influenze negative, come la rumorosità, si è utilizzato un diagramma parametrico.
La SKF è poi passata alla fase 2 concettuale e di scelta. Al fine di configurare i cuscinetti, è stata eseguita un’analisi delle loro prestazioni utilizzando i modelli di simulazione creati in precedenza. Ciò ha comportato l’applicazione del pacchetto di software SKF Simulator (Orpheus), che è stato studiato per le indagini sulle applicazioni di cuscinetti volventi come sistemi integrati. Orpheus è in grado di analizzare il comportamento statico e modale delle applicazioni. In primo luogo si costruisce un modello collegando tutti i tipi di componenti della macchina, quali cuscinetti, alberi, ingranaggi e sopporti. Per definire i carichi sui componenti si può usare una combinazione di forze, spostamenti e velocità di rotazione. Gli stessi componenti possono essere sia elementi speciali (non-lineari), definiti nell’ambito dell’SKF Simulator (cioè i cuscinetti volventi), sia elementi arbitrari come gli alberi e gli alloggiamenti. Questi ultimi devono avere un comportamento lineare e la loro rigidezza e le loro proprietà di smorzamento si ricavano con il metodo degli elementi finiti. Speciali metodi di riduzione vengono applicati sui modelli ad elementi finiti originali per ridurre il numero dei gradi di libertà e quindi diminuire il tempo di calcolo. Per le analisi in questo progetto sono state scelte quattro condizioni di carico.
Per le simulazioni del modello rigido (statico), il cuscinetto è stato modellato come singolo cuscinetto orientabile a rulli con quattro gruppi diversi di carico radio-assiale applicati sull’anello esterno. L’anello interno è stato bloccato in tutti i gradi di libertà, mentre l’anello esterno è stato considerato libero di muoversi in tutti i gradi di libertà. Come disallineamento relativo tra l’anello interno e quello esterno nei sensi positivo e negativo è stato definito un dato angolo (fig. 3).
Dopo questa analisi, la modellazione si è dedicata agli effetti della flessibilità strutturale sulle prestazioni dei cuscinetti, cosa che ha comportato l’inclusione del mozzo e dell’albero come componenti totalmente flessibili, prima di eseguire ulteriori simulazioni basate sulle quattro opzioni di carico.
Uno degli aspetti importanti del progetto è la necessità di assicurarsi che il gruppo dei cuscinetti sia in grado di reggere alle condizioni effettive di lavoro. Nella fase 3 è stata analizzata la sensibilità dei cuscinetti alle variazioni delle condizioni al contorno e della geometria interna. Le analisi sono servite per valutare il disegno dei cuscinetti in funzione delle condizioni di lavoro dell’applicazione. Inoltre è stata eseguita un’analisi FE della gabbia. L’analisi della geometria interna ha portato ad una revisione del profilo dei rulli inizialmente previsto.
Le fasi di ottimizzazione iniziali hanno identificato la possibilità di migliorare la durata variando oltre al profilo dei rulli, la rigidezza del gruppo albero-mozzo. Si è quindi scelto il disegno ottimale valutando successivamente con le simulazioni le varie condizioni di carico.
Analisi della durata dei cuscinetti
Come già detto, i cuscinetti della High Roller devono essere affidabili e di lunga durata. Pertanto la SKF ha utilizzato due importanti metodi di calcolo della durata, il DIN ISO 281 e il metodo SKF Advanced Fatigue Calculation (AFC).
I valori di riferimento sono quelli della durata a fatica L2.53 e L10. La durata L10 si definisce come quella del 90 % dei cuscinetti che superano il valore calcolato con una probabilità di cedimento del 10 %. Una durata a fatica con una probabilità minore di cedimento può essere calcolata mediante una distribuzione di Weibull con un fattore di forma pari a 1,5. L2.53 è stata scelta per aumentare l’affidabilità del sistema.
Tutti i calcoli di durata sono stati eseguiti utilizzando il programma avanzato SKF di simulazione, SKF Simulator. Nel caso dei moderni cuscinetti di alta qualità la durata di base può differenziarsi notevolmente da quella effettiva. In una data applicazione la durata di esercizio dipende da molti fattori: lubrificazione, grado di contaminazione, disallineamento, installazione appropriata, condizioni dell’ambiente, movimenti strutturali, vibrazioni a cuscinetto fermo e scariche elettriche.
Il metodo della durata SKF AFC prende in considerazione l’interazione delle sollecitazioni di contatto sui corpi volventi lungo tutta la loro lunghezza e valuta il numero totale di cicli di sollecitazione compiuto fino a che la durata nell’intero volume sotto carico non si esurisce. SKF AFC tiene conto anche delle condizioni del lubrificante, in particolare lo spessore del film in esercizio e la contaminazione per ogni singolo contatto.
La SKF ha ottenuto significativi aumenti di L2.53 grazie al procedimento DfSS e ai risultati delle analisi delle simulazioni. Con la modifica del profilo standard dei rulli, l’aumento della rigidezza del mozzo, il rivestimento a basso attrito anti-usura SKF NoWear e l’imposizione di un sistema automatico di lubrificazione, la durata calcolata è aumentata più del 10%. Diversamente dalla maggioranza dei cuscinetti, che vengono progettati genericamente per tutta una varietà di applicazioni, quelli della ruota in questione sono stati progettati appositamente. La SKF ne ha modificato il profilo dei rulli per tener conto del fatto che le velocità sono basse e i carichi elevati.
Le varie simulazioni hanno fornito alla SKF i dati per impostare il giusto grado di rigidezza dell’albero e del mozzo, combinando considerazioni di carattere tecnico ed economico. Le pressioni di contatto dei corpi volventi sono in relazione diretta con tale rigidezza e il costo per migliorarla è stato correlato al prevedibile aumento della durata L2.53. Sulla base di questi studi, si è deciso di aumentarla. In tutte le condizioni di lavoro i requisiti di durata sono stati più che soddisfatti.
Infine, i risultati delle simulazioni sono stati utilizzati per determinare le procedure d’installazione e i relativi equipaggiamenti. Le procedure effettive sono state pressoché identiche a quelle previste nelle simulazioni. Appunto come previsto, l’installazione ha richiesto l’impiego dell’iniezione idraulica per facilitare un corretto montaggio dei cuscinetti. L’incuneamento assiale richiesto per ottenere il gioco interno finale voluto si è situato entro il 2 % del valore calcolato. Questo ha fatto molta impressione vista la complessità della conformazione del mozzo.
In conclusione
Il metodo Six Sigma, unitamente ai programmi di simulazione, ha fornito alla SKF gli elementi per progettare un mozzo coerente con i requisiti imposti in termini di fabbricazione, trasporto, montaggio e costi. La soluzione per gruppo mozzo albero è stata fornita dalla SKF nei tempi e nei limiti di budget.
NoWear è un marchio registrato del Gruppo SKF