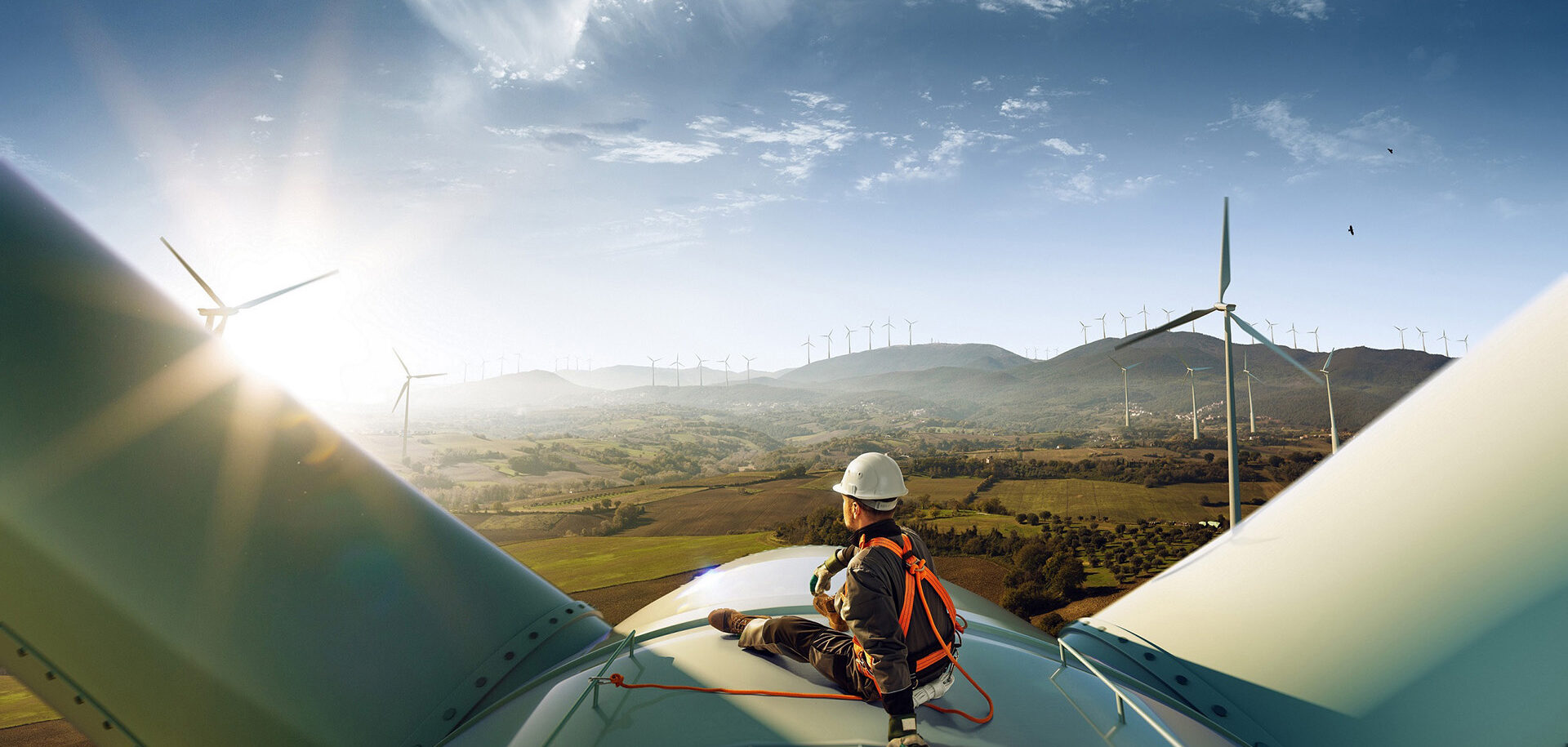
Ridurre il costo livellato dell’energia
I moltiplicatori e i cuscinetti delle turbine eoliche sono componenti critici. Il loro cedimento può causare mancati introiti, costi elevati di riparazione e, in definitiva, un aumento dei costi di produzione dell’energia. SKF e il costruttore di rotismi ZF hanno unito le forze per portare la manutenzione predittiva dei moltiplicatori a un livello superiore, nell’intento di sostenere gli operatori di parchi eolici, ridurre il costo livellato dell’energia (Levelized Cost of Energy, LCoE) e aumentare la redditività del settore.
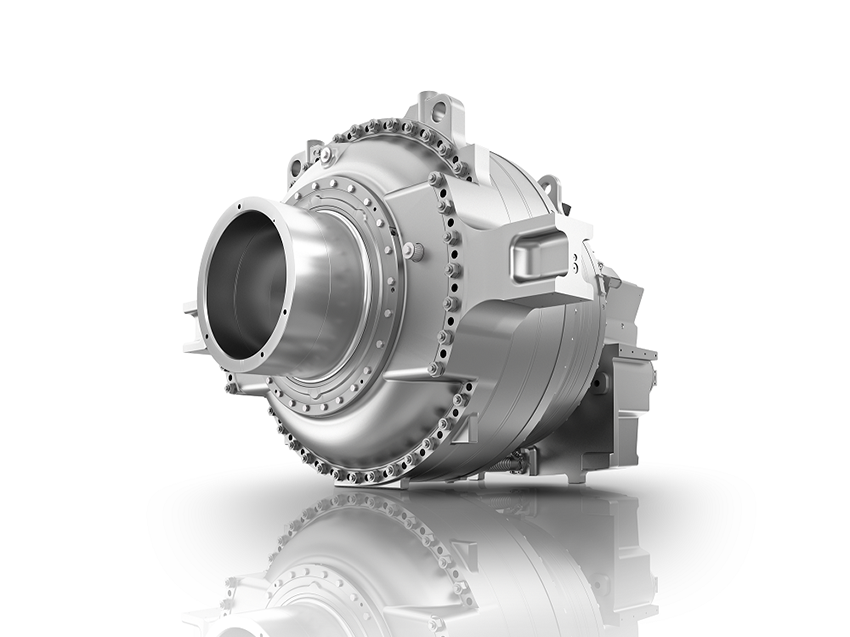
Ma per far sì che l’energia prodotta da eolico sia concorrenziale è necessario che le turbine eoliche garantiscano un funzionamento continuo. Per raggiungere questo obiettivo, bisogna ridurre il costo livellato dell’energia (LCoE) attraverso la manutenzione predittiva. LCoE è la misura del costo di generazione di energia per una turbina nel corso della sua durata in esercizio. Ridurre la manutenzione non programmata aumenta in effetti la redditività del produttore di energia, anche se questo non implica necessariamente un incremento della produzione o una sua maggiore stabilità. Impedire il ricorrere dei cedimenti, tuttavia, riduce il costo delle turbine durante l’intero ciclo di vita e contribuisce ad aumentare la quantità di energia prodotta nel corso della loro vita utile.
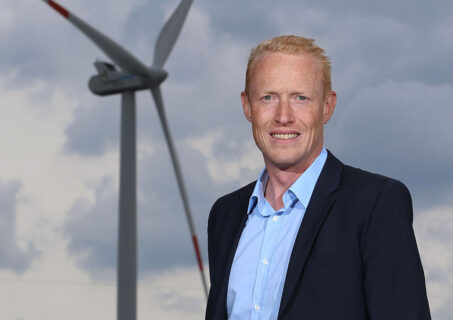
Abbiamo capito l’esigenza specifica e ci siamo resi conto che, insieme, potevamo creare un valore aggiunto per il cliente
Joris Peeters, Head of Digitalisation della Wind Power Technology Business Unit di ZF.
Processi più semplici creano valore aggiunto
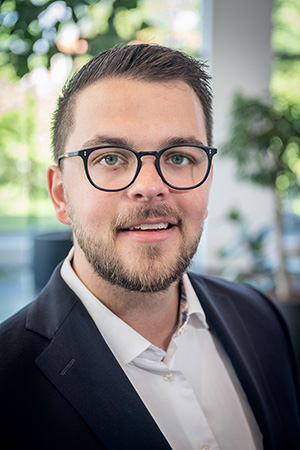
Il condition monitoring remoto è particolarmente utile all’industria eolica, poiché permette agli operatori di esaminare le turbine mentre sono in funzione. SKF e il produttore di rotismi ZF hanno portato la manutenzione predittiva a un nuovo livello. Questo approccio semplifica notevolmente il processo per tutti i soggetti coinvolti e riduce i tempi di riparazione di oltre l’85 percento. Il progetto si basa sulla capacità dei sensori di rilevare anomalie, non solo nei cuscinetti, ma nell’intero ingranaggio.
“La difficoltà è sempre stata che le grandi aziende non condividono i dati”, dichiara Dennis Nordmark, Digitalisation Manager Energy Industries di SKF. “Ma insieme abbiamo 150 anni di conoscenze fondamentali. Integrandole, abbiamo compiuto un vero e proprio balzo in avanti”.
Come dice Joris Peeters, Head of Digitalisation della Wind Power Technology Business Unit di ZF, “SKF e ZF si sono servite di un progetto pilota durato un anno per mostrare ai clienti cosa possono fare insieme. Abbiamo capito l’esigenza specifica e ci siamo resi conto che, insieme, potevamo creare un valore aggiunto per il cliente”.
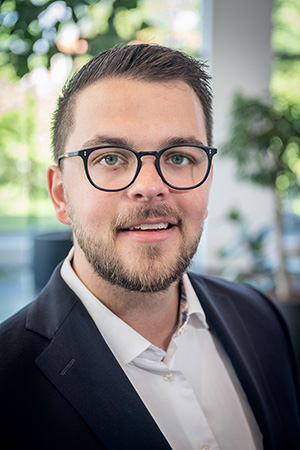
Processi più semplici creano valore aggiunto
Il condition monitoring remoto è particolarmente utile all’industria eolica, poiché permette agli operatori di esaminare le turbine mentre sono in funzione. SKF e il produttore di rotismi ZF hanno portato la manutenzione predittiva a un nuovo livello. Questo approccio semplifica notevolmente il processo per tutti i soggetti coinvolti e riduce i tempi di riparazione di oltre l’85 percento. Il progetto si basa sulla capacità dei sensori di rilevare anomalie, non solo nei cuscinetti, ma nell’intero ingranaggio.
“La difficoltà è sempre stata che le grandi aziende non condividono i dati”, dichiara Dennis Nordmark, Digitalisation Manager Energy Industries di SKF. “Ma insieme abbiamo 150 anni di conoscenze fondamentali. Integrandole, abbiamo compiuto un vero e proprio balzo in avanti”.
Come dice Joris Peeters, Head of Digitalisation della Wind Power Technology Business Unit di ZF, “SKF e ZF si sono servite di un progetto pilota durato un anno per mostrare ai clienti cosa possono fare insieme. Abbiamo capito l’esigenza specifica e ci siamo resi conto che, insieme, potevamo creare un valore aggiunto per il cliente”.
Il principio SEE-THINK-ACT
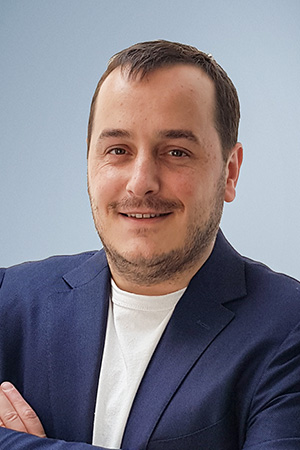
Joris Boeye, Data Analytics Engineer di ZF, racconta che il sistema opera secondo il principio SEE-THINK-ACT: “Il CMS (Condition Monitoring System) rileva un’anomalia, l’analisi di SKF genera un allarme, e noi lo elaboriamo grazie ai dati di produzione e alla conoscenza del sistema di cui disponiamo: questa è la fase SEE”. Poi capiamo qual è il guasto, dov’è collocata la turbina e quanto tempo manca al cedimento: questo è la fase THINK. Infine elaboriamo un adeguato ordine di lavoro, assegniamo i tecnici idonei e scegliamo i ricambi necessari: questa è la fase ACT”.
Ma, come dice Nordmark, “La sfida è stata unire le nostre conoscenze sulle vibrazioni dei cuscinetti con le conoscenze dei data scientist di ZF, i quali avevano bisogno di contestualizzare i dati per trasformarli in informazioni”.
L’analisi degli scostamenti fa parte delle conoscenze fondamentali di SKF e ZF nei loro rispettivi campi, continua. “Analogamente a quando si passa con l’auto su un’irregolarità dell’asfalto, i sensori del CMS rilevano una specie di ‘asperità’ quando riscontrano un problema in un punto del moltiplicatore. Naturalmente rilevare una minima differenza nelle vibrazioni dei cuscinetti è molto più difficile, ma il principio è simile. Così come attraverso le ruote e le sospensioni dell’auto rileviamo l’irregolarità della superficie stradale e grazie alla nostra esperienza di guida possiamo attribuirne la causa a una deformazione del manto stradale. In modo simile, il comportamento vibrazionale dei cuscinetti cambia quando c’è, per esempio, un disallineamento dell’albero. Grazie alle conoscenze specialistiche combinate, gli analisti di SKF e ZF riescono a capire i cambiamenti vibrazionali, i componenti che li causano, gli interventi di riparazione e i tempi necessari.
“L’obiettivo è individuare i danneggiamenti incipienti prima che si verifichi un fermo imprevisto. E ogni ora conta. Considerando come base un prezzo dell’elettricità di 60 euro per Megawattora, la perdita giornaliera per una turbina da 3,5 Megawatt può ammontare a 1.800 euro. Un fermo non programmato di quattro settimane può corrispondere a 55.000 euro di mancati introiti”.
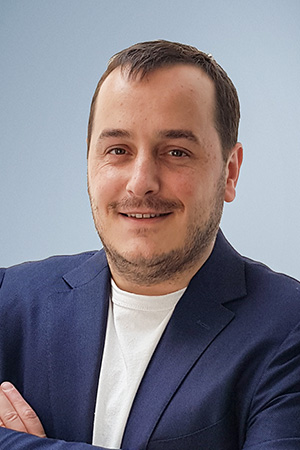
Il principio SEE-THINK-ACT
Joris Boeye, Data Analytics Engineer di ZF, racconta che il sistema opera secondo il principio SEE-THINK-ACT: “Il CMS (Condition Monitoring System) rileva un’anomalia, l’analisi di SKF genera un allarme, e noi lo elaboriamo grazie ai dati di produzione e alla conoscenza del sistema di cui disponiamo: questa è la fase SEE”. Poi capiamo qual è il guasto, dov’è collocata la turbina e quanto tempo manca al cedimento: questo è la fase THINK. Infine elaboriamo un adeguato ordine di lavoro, assegniamo i tecnici idonei e scegliamo i ricambi necessari: questa è la fase ACT”.
Ma, come dice Nordmark, “La sfida è stata unire le nostre conoscenze sulle vibrazioni dei cuscinetti con le conoscenze dei data scientist di ZF, i quali avevano bisogno di contestualizzare i dati per trasformarli in informazioni”.
L’analisi degli scostamenti fa parte delle conoscenze fondamentali di SKF e ZF nei loro rispettivi campi, continua. “Analogamente a quando si passa con l’auto su un’irregolarità dell’asfalto, i sensori del CMS rilevano una specie di ‘asperità’ quando riscontrano un problema in un punto del moltiplicatore. Naturalmente rilevare una minima differenza nelle vibrazioni dei cuscinetti è molto più difficile, ma il principio è simile. Così come attraverso le ruote e le sospensioni dell’auto rileviamo l’irregolarità della superficie stradale e grazie alla nostra esperienza di guida possiamo attribuirne la causa a una deformazione del manto stradale. In modo simile, il comportamento vibrazionale dei cuscinetti cambia quando c’è, per esempio, un disallineamento dell’albero. Grazie alle conoscenze specialistiche combinate, gli analisti di SKF e ZF riescono a capire i cambiamenti vibrazionali, i componenti che li causano, gli interventi di riparazione e i tempi necessari.
“L’obiettivo è individuare i danneggiamenti incipienti prima che si verifichi un fermo imprevisto. E ogni ora conta. Considerando come base un prezzo dell’elettricità di 60 euro per Megawattora, la perdita giornaliera per una turbina da 3,5 Megawatt può ammontare a 1.800 euro. Un fermo non programmato di quattro settimane può corrispondere a 55.000 euro di mancati introiti”.
Miglioramento del costo livellato dell’energia
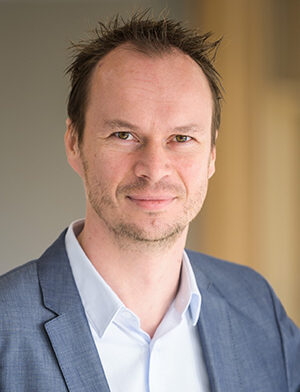
Il progetto pilota condotto in un parco eolico formato da un centinaio di turbine ha dimostrato che è possibile. In cifre? Ispezioni sul campo non programmate ridotte del 60 percento, tempi di riparazione ridotti dell’85 percento e produzione annuale di energia aumentata dello 0,4 percento. La fase di avviamento commerciale del programma è prevista nel corso del 2021.
Raf Kerkhofs, Business Development Manager Wind Operation and Maintenance di SKF, sostiene che il potenziale è enorme. “SKF e ZF ottengono entrambe una prospettiva più approfondita sul funzionamento dei loro prodotti e possono aiutare i clienti a pensare in modo proattivo a soluzioni e miglioramenti”, afferma.
E Peeters di ZF commenta: “Ora stiamo applicando la nuova soluzione ai CMS esistenti. In seguito potremo adottarla per le nuove installazioni. Possiamo migliorare le impostazioni di allarme, e alla fine arriveremo anche ad avere powertrain autonomi, che usciti dalla fabbrica saranno in grado di attivare le proprie riparazioni”.
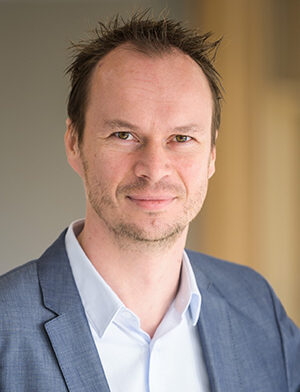
Miglioramento del costo livellato dell’energia
Il progetto pilota condotto in un parco eolico formato da un centinaio di turbine ha dimostrato che è possibile. In cifre? Ispezioni sul campo non programmate ridotte del 60 percento, tempi di riparazione ridotti dell’85 percento e produzione annuale di energia aumentata dello 0,4 percento. La fase di avviamento commerciale del programma è prevista nel corso del 2021.
Raf Kerkhofs, Business Development Manager Wind Operation and Maintenance di SKF, sostiene che il potenziale è enorme. “SKF e ZF ottengono entrambe una prospettiva più approfondita sul funzionamento dei loro prodotti e possono aiutare i clienti a pensare in modo proattivo a soluzioni e miglioramenti”, afferma.
E Peeters di ZF commenta: “Ora stiamo applicando la nuova soluzione ai CMS esistenti. In seguito potremo adottarla per le nuove installazioni. Possiamo migliorare le impostazioni di allarme, e alla fine arriveremo anche ad avere powertrain autonomi, che usciti dalla fabbrica saranno in grado di attivare le proprie riparazioni”.
Sistema SKF IMx per il condition monitoring
SKF IMx è una soluzione di nuova generazione potente ed efficace in termini di costo, dedicata al condition monitoring delle turbine eoliche. È una centralina di misura robusta, progettata per essere installata nei parchi eolici su terra ferma e in mare aperto.
Gli input di segnale dinamico del sistema sono configurabili per una varietà di sensori. Insieme al software SKF @ptitude Observer, SKF IMx fornisce un sistema completo per la rilevazione precoce e la prevenzione dei guasti, consigli automatici per la correzione delle condizioni esistenti o incipienti e la manutenzione avanzata basata sulle condizioni per migliorare l’affidabilità, la disponibilità e le prestazioni.