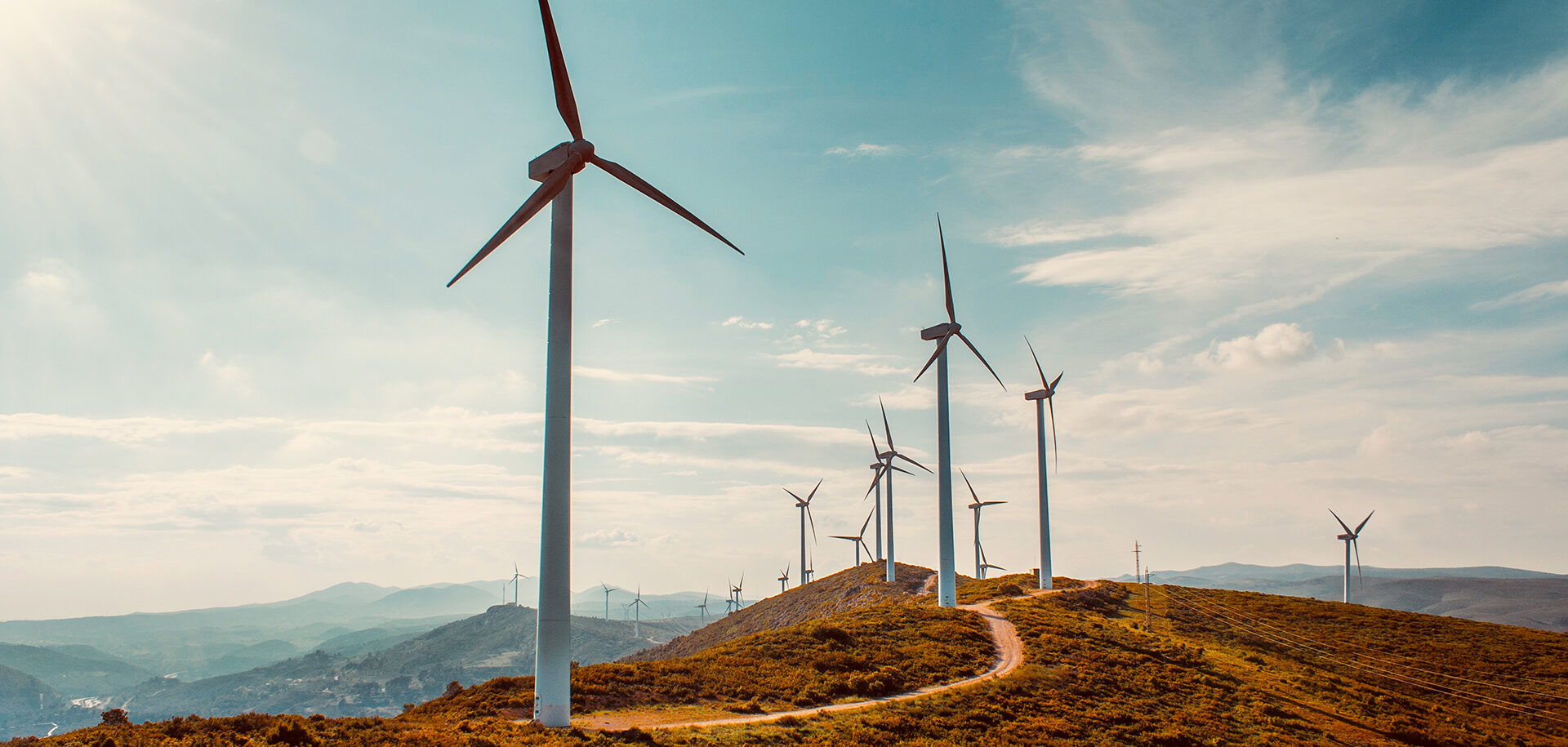
Miglioramento dell’accuratezza del monitoraggio delle turbine eoliche
Monitorare le condizioni di lavoro delle turbine eoliche è estremamente impegnativo. Ogni turbina è soggetta a costanti cambiamenti dovuti all’instabilità climatica, di conseguenza, una condizione che potrebbe causare forti sollecitazioni su alcuni componenti potrebbe essere erroneamente identificata come un difetto. Grazie allo sviluppo di un nuovo strumento diagnostico, SKF ha compiuto un importante passo avanti nel ridurre la possibilità che si verifichino falsi allarmi quando si monitorano i sistemi di trasmissione delle turbine eoliche.
Protean, un nuovo strumento diagnostico, è stato sviluppato proprio per ridurre l’incidenza dei falsi allarmi distinguendo le sollecitazioni temporanee dai danneggiamenti. La sua funzione diagnostica è progettata per funzionare con il software per il condition monitoring SKF @ptitude Observer, ampiamente diffuso nel settore eolico per monitorare i sistemi di trasmissione delle turbine eoliche, e consente ai responsabili della gestione e della manutenzione (O&M, Operation and Maintenance) e ai tecnici dei sistemi di condition monitoring di concentrarsi su potenziali problemi di prestazioni effettive, mitigando il rischio di falsi allarmi. Per i clienti che lo hanno installato, questo può rappresentare un notevole risparmio di tempo e rendere il condition monitoring più efficiente ed efficace.
Come funziona Protean
Essenzialmente Protean riconosce le condizioni di lavoro della macchina e “apprende” il comportamento normale rispetto a diversi indicatori di condizione. Dopo un periodo di addestramento di circa una settimana, Protean imposta automaticamente i livelli di soglia per i vari indicatori di condizione definiti dall’operatore. Gli indicatori di condizione sono progettati per rilevare diverse tipologie di difetti, ad esempio difetti dei cuscinetti e degli ingranaggi, squilibrio, ecc. Questi indicatori di condizione vengono poi configurati per ogni componente della macchina; ciò significa che viene utilizzato almeno un indicatore di condizione per ogni cuscinetto installato. Se si verifica un allarme, Protean ricalcola il livello di soglia in base alla nuova situazione che ha portato all’attivazione dell’allarme. Pertanto, vengono generati nuovi allarmi soltanto nel caso in cui la condizione peggiori. Inoltre, un solo valore dell’indicatore di condizione superiore al valore di soglia non attiva alcun allarme. È necessario che “M di N” degli ultimi valori dell’indicatore di condizione siano superiori al livello di soglia per attivare l’allarme (i valori M e N vengono impostati conformemente alle migliori pratiche). Una volta eseguita la manutenzione, Protean rileva una diminuzione del livello dell’indicatore di condizione e ricalcola automaticamente il livello di soglia per indicare la nuova situazione.
Per dare un’idea, creare la configurazione di un sistema di condition monitoring per un parco eolico di 20 turbine comporterebbe l’impostazione di circa 1.000 indicatori. Eseguire questa operazione manualmente è semplicemente improponibile. Invece, applicando le regole diagnostiche del software SKF @ptitude ed effettuando il collegamento a Protean e al suo motore di intelligenza artificiale, è possibile configurare in modo semplice e rapido il sistema di condition monitoring.
Grazie al software per il condition monitoring di SKF è possibile automatizzare la diagnosi costruendo un modello matematico del sistema di trasmissione della turbina eolica mediante un semplice drag & drop dei componenti, come rotore elettrico, cuscinetti, ingranaggi, ingranaggi planetari, giranti, ecc. (fig. 1). Gli indicatori di condizione tradizionalmente si calcolano come valore assoluto, utilizzando le frequenze significative per il difetto da rilevare e sono progettati per reagire a un determinato difetto in un componente della macchina, come il disallineamento dell’albero, un difetto del cuscinetto, un difetto dell’ingranaggio o lo squilibrio del rotore. In aggiunta a questo, una regola diagnostica combina le ampiezze a determinate frequenze sulla base di dati cinematici; inoltre, il valore dell’indicatore di condizione si può anche calcolare come percentuale del rumore di fondo nella misurazione ed è quindi possibile eliminare il rumore che in precedenza aveva portato a un falso positivo.
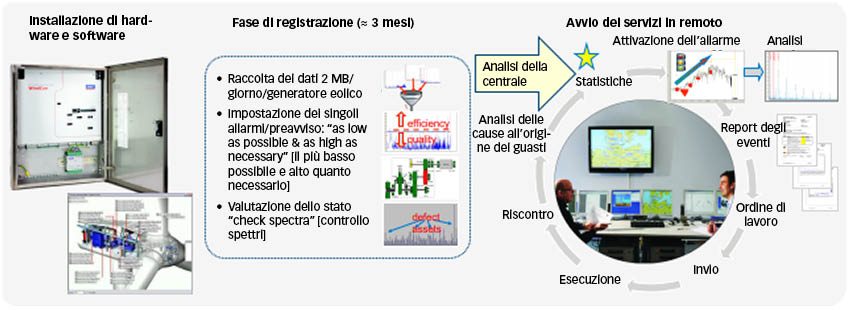
Protean può fare la differenza
Per un potenziale difetto di allentamento in un albero meccanico sono ampiamente utilizzate regole diagnostiche che consentono l’estrazione predefinita degli indicatori di condizione (fig. 3). Tramite l’archivio dei componenti è possibile eseguire la consueta configurazione; l’utente deve semplicemente regolare il livello di allarme e di pericolo oppure scegliere “auto” per lasciare che sia il software a calibrare il livello degli allarmi in base al comportamento della macchina al primo avvio. Se non si utilizza Protean (fig. 4), il sistema evidenzia l’aumento dell’allentamento meccanico, ma sarà necessario un intervento manuale per regolare i livelli di allarme.
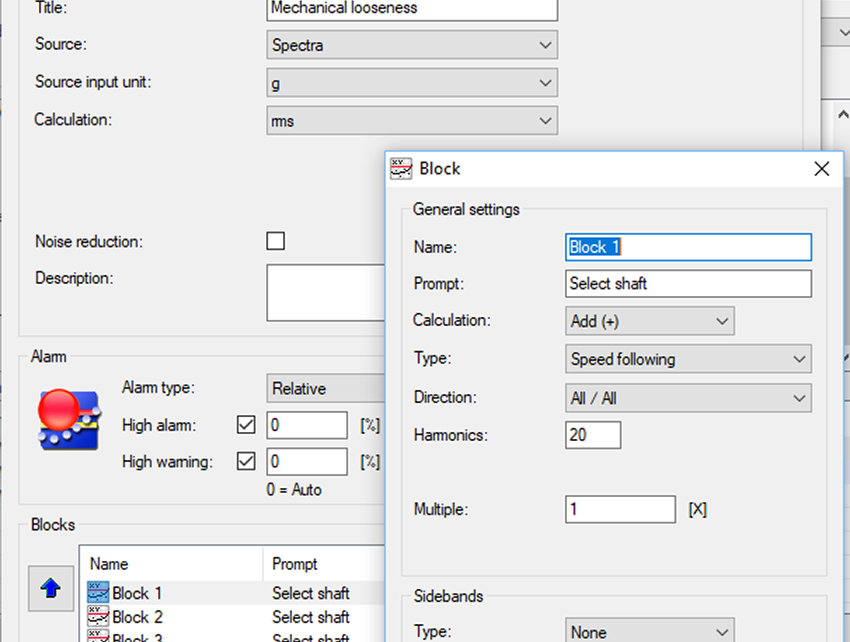

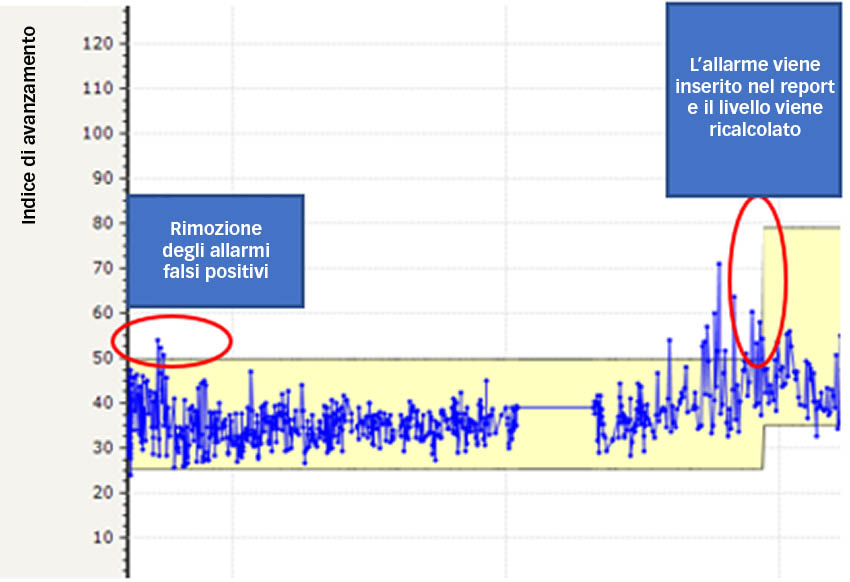
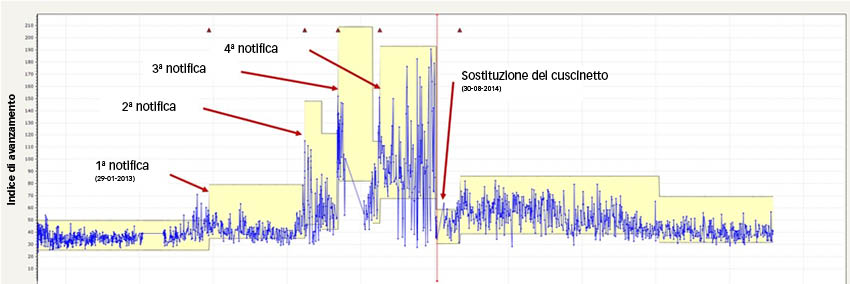

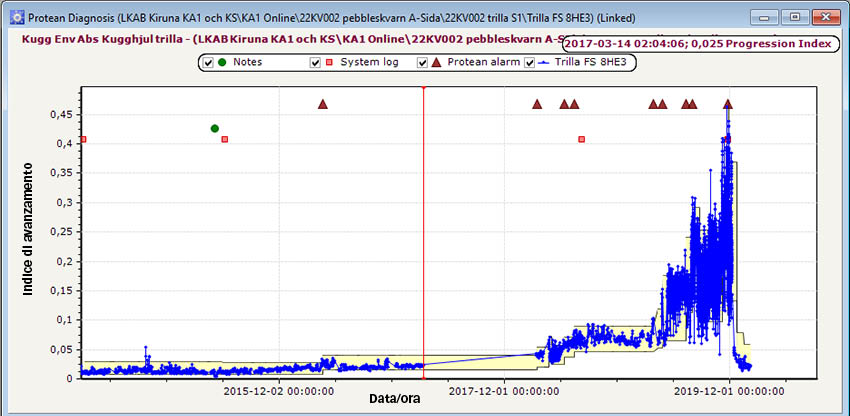
Protean è una soluzione di autodiagnosi molto affidabile, che offre una riduzione significativa dei falsi allarmi senza aumentare il rischio che i difetti non vengano rilevati. Evita ai tecnici responsabili del sistema di condition monitoring di svolgere attività noiose e ripetitive e consente loro di concentrarsi sui casi più problematici. Supporta e ottimizza i benefici di un sistema di condition monitoring efficiente in grado di rilevare i guasti e altre condizioni indesiderate in una fase precoce; consente di pianificare ed eseguire azioni correttive in modo tempestivo e con il livello di qualità richiesto ed evita danneggiamenti consequenziali alle macchine.
Per SKF Protean rappresenta un importante passo avanti nel miglioramento della rilevabilità, dell’accuratezza e dell’efficienza dei sistemi di condition monitoring delle macchine, non soltanto per le turbine eoliche ma per qualsiasi tipo di macchinario rotante. Sviluppi continui e nuovi strumenti sono essenziali perché i sistemi di condition monitoring possano diventare una tecnologia più intelligente e aiutare i clienti a eseguire i processi operativi e gli interventi di manutenzione in modo più efficiente.