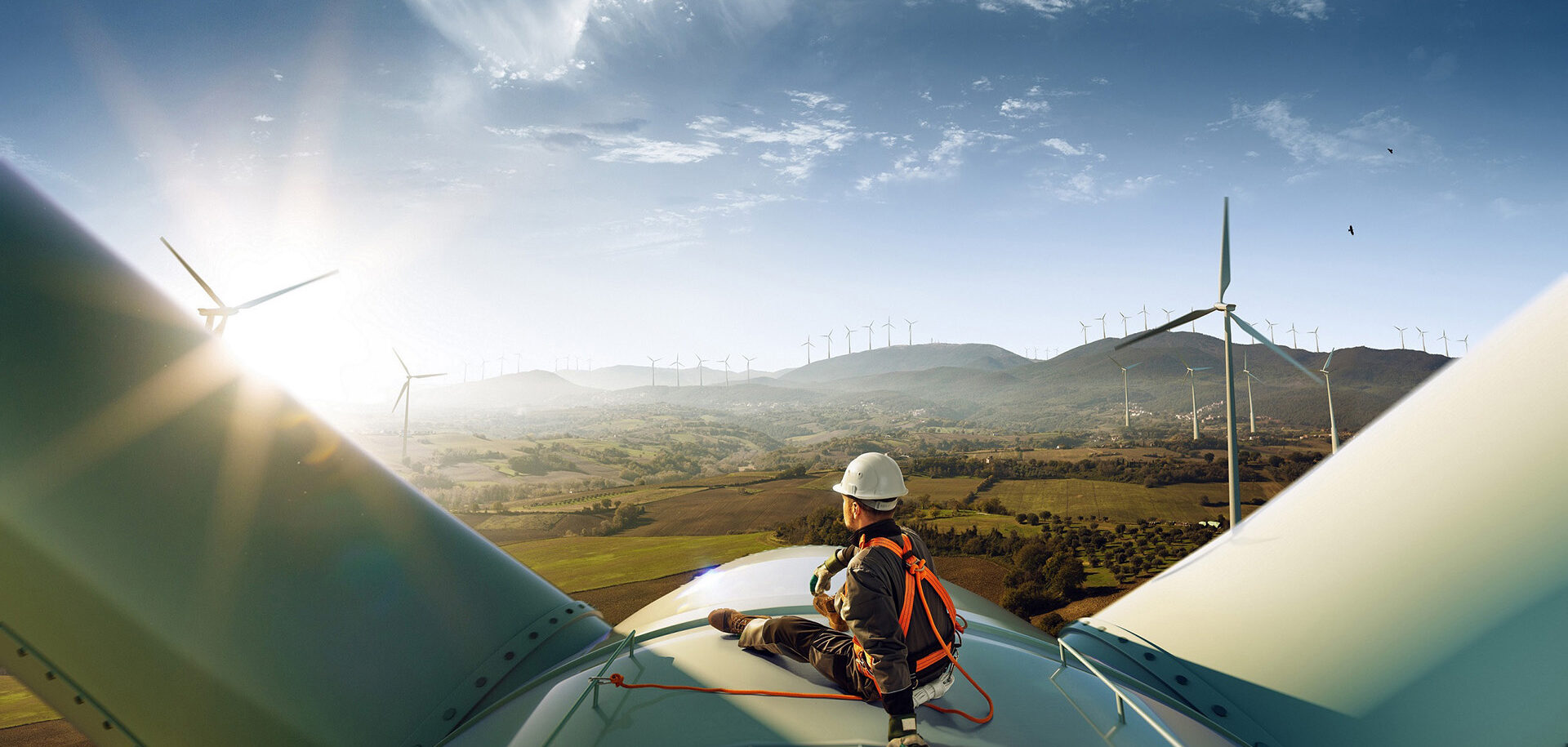
Niedrigere Stromgestehungskosten durch Datenaustausch
Getriebe und Hauptlager sind kritische Komponenten in Windturbinen. Ihr Ausfall zieht häufig Einnahmeverluste, hohe Kosten für Notfallreparaturen und nicht zuletzt höhere Energieerzeugungskosten nach sich. SKF und der Getriebehersteller ZF haben gemeinsam die vorausschauende Instandhaltung von Windkraftgetrieben weiterentwickelt, um Windparkbetreiber zu unterstützen, die Stromgestehungskosten (LCoE) zu senken und erneuerbare Energie zu einem profitableren Geschäft zu machen.
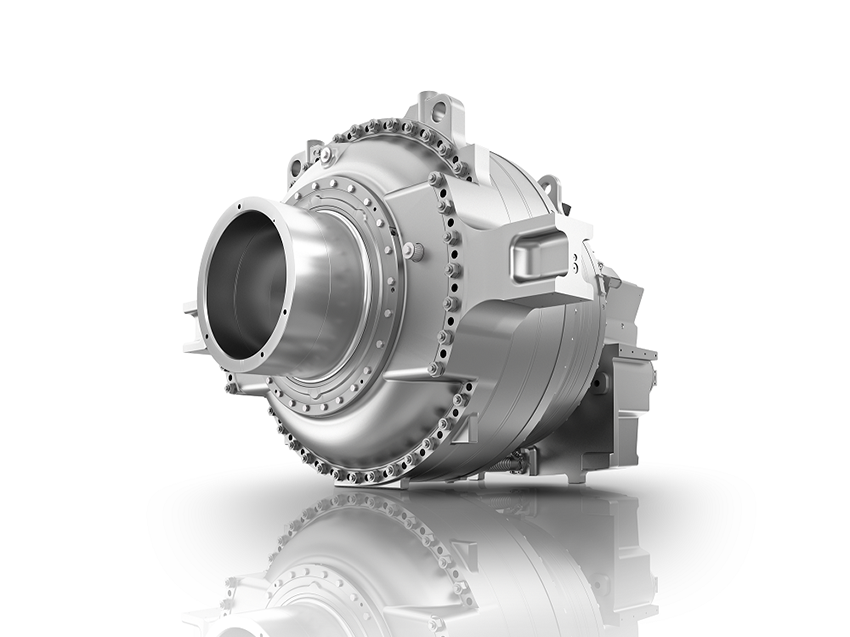
Wenn der Preis für Strom aus Windenergieanlagen wettbewerbsfähig sein soll, müssen sich die Windräder drehen. Das erreicht man unter anderm, indem man die Stromgestehungskosten, Levelized Cost of Energy (LCoE), durch vorausschauende Instandhaltung verringert. Beim LCoE-Konzept werden die Kosten für die Energieerzeugung über die gesamte Lebensdauer der energieerzeugenden Turbine betrachtet. Eine wirksame Verringerung von ungeplanten Wartungsmaßnahmen verbessert die Rentabilität des Energieproduzenten, erhöht aber nicht notwendigerweise die Produktion und sorgt auch nicht für eine stabilere Energieerzeugung. Aber wenn man häufig auftretende Störungen beseitigen kann, lassen sich die Lebenszykluskosten der Turbine senken, und die von ihr über die gesamte Lebensdauer erzeugte absolute Energiemenge nimmt zu.
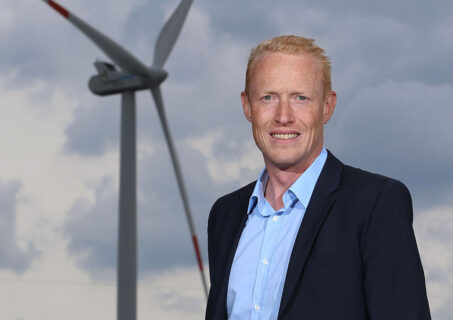
Wir haben auf einen Kundenwunsch reagiert und festgestellt, dass wir gemeinsam einen Mehrwert für den Kunden schaffen können.
Joris Peeters, Leiter Digitalisierung im Geschäftsbereich Wind Power Technology von ZF
Vereinfachung der Prozesse für höheren Mehrwert
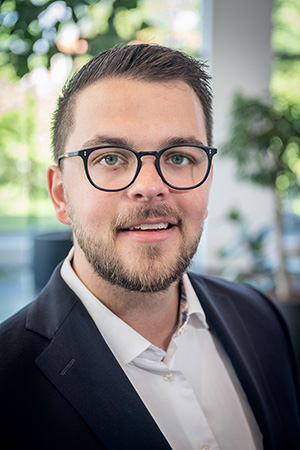
Zustandsfernüberwachung ist für die Windkraftindustrie besonders gut geeignet, weil Windparkbetreiber den Zustand der weit entfernten Anlagen während des laufenden Betriebs stets beurteilen können. SKF und der Getriebehersteller ZF haben nun gemeinsam die vorausschauende Instandhaltung einen Schritt weiter gebracht. Das von ihnen entwickelte Konzept vereinfacht den Prozess für alle Beteiligten erheblich, und es verkürzt die Vorlaufzeit für Reparaturen um bis zu 85 Prozent. Es macht sich die Fähigkeit der Sensoren zunutze, nicht nur in den Lagern, sondern auch im gesamten Getriebe Anomalien zu erfassen.
„Ein Problem war immer, dass große Unternehmen keine Daten teilenׅ“, sagt Dennis Nordmark, Leiter Digitalisierung der Energieindustrie bei SKF. „Zusammen blicken diese beiden Unternehmen auf 150 Jahre Kernkompetenz zurück. Die Integration unseres Wissens ist ein echter Sprung nach vorn.“
Joris Peeters, Leiter Digitalisierung im Geschäftsbereich Wind Power Technology von ZF, erklärt: „SKF und ZF haben den Kunden im Rahmen eines einjährigen Pilotprojekts gezeigt, was wir zusammen erreichen können. Wir haben auf einen Kundenwunsch reagiert und festgestellt, dass wir gemeinsam einen Mehrwert für diesen Kunden schaffen können.“
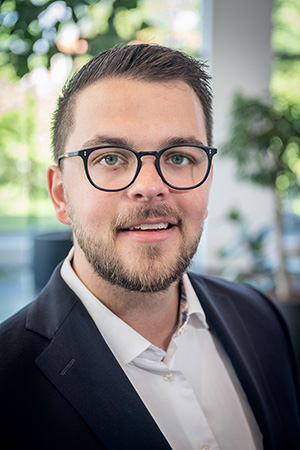
Vereinfachung der Prozesse für höheren Mehrwert
Zustandsfernüberwachung ist für die Windkraftindustrie besonders gut geeignet, weil Windparkbetreiber den Zustand der weit entfernten Anlagen während des laufenden Betriebs stets beurteilen können. SKF und der Getriebehersteller ZF haben nun gemeinsam die vorausschauende Instandhaltung einen Schritt weiter gebracht. Das von ihnen entwickelte Konzept vereinfacht den Prozess für alle Beteiligten erheblich, und es verkürzt die Vorlaufzeit für Reparaturen um bis zu 85 Prozent. Es macht sich die Fähigkeit der Sensoren zunutze, nicht nur in den Lagern, sondern auch im gesamten Getriebe Anomalien zu erfassen.
„Ein Problem war immer, dass große Unternehmen keine Daten teilenׅ“, sagt Dennis Nordmark, Leiter Digitalisierung der Energieindustrie bei SKF. „Zusammen blicken diese beiden Unternehmen auf 150 Jahre Kernkompetenz zurück. Die Integration unseres Wissens ist ein echter Sprung nach vorn.“
Joris Peeters, Leiter Digitalisierung im Geschäftsbereich Wind Power Technology von ZF, erklärt: „SKF und ZF haben den Kunden im Rahmen eines einjährigen Pilotprojekts gezeigt, was wir zusammen erreichen können. Wir haben auf einen Kundenwunsch reagiert und festgestellt, dass wir gemeinsam einen Mehrwert für diesen Kunden schaffen können.“
SEHEN-DENKEN-HANDELN
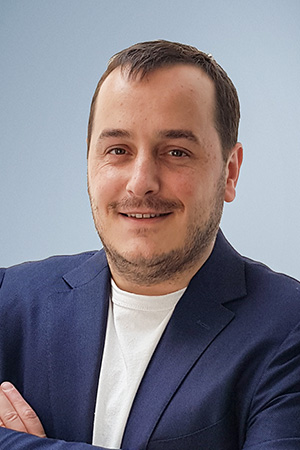
Joris Boeye, Ingenieur für Datenanalyse bei ZF, erklärt, das System arbeite nach dem Prinzip SEHEN-DENKEN-HANDELN. „Das Zustandsüberwachungssystem erfasst eine Abweichung, und nach einer Analyse durch SKF erhalten wir eine Warnmeldung. Wir verfügen über die Herstellungsdaten und die Systemkenntnis, um diese Warnmeldung zu bearbeiten – das ist der Teil SEHEN. Dann ermitteln wir, um welche Art von Fehler es sich handelt, wo sich die Turbine befindet und wie viel Zeit bis zu ihrem Ausfall bleibt – das ist die Phase DENKEN. Schließlich organisieren wir den entsprechenden Einsatzauftrag, die geeigneten Techniker und die richtigen Ersatzteile – das nennen wir HANDELN. “
Nordmark verdeutlicht: „Unsere Kernkompetenz zum Thema Lagerschwingungen mit der Kernkompetenz der Datenwissenschaftler von ZF zu kombinieren, war eine echte Herausforderung. Die Daten müssen in einem Kontext stehen, sonst sind sie einfach nur Daten und keine Informationen.“
Die Analyse von Abweichungen sei die Wissensdomäne von SKF und ZF in ihren jeweiligen Fachbereichen, so Nordmark. „Wie bei einem Auto, das über ein Schlagloch fährt, registrieren die Sensoren des Zustandsüberwachungssystems eine ‚Unregelmäßigkeit‘, wenn in einem Teil des Getriebes ein Problem auftritt. Natürlich ist es weitaus schwieriger, winzige Abweichungen in der Lagerschwingung zu erfassen als das Aufschlagen eines Fahrzeugs nach dem Überfahren eines Schlaglochs, aber das Prinzip ist ähnlich. Über die Reifen und die Federung des Fahrzeugs nehmen wir eine Abweichung wahr. Unsere Erfahrung als Fahrer sagt uns, dass wahrscheinlich ein Straßenschaden die Ursache ist. Auf vergleichbare Weise verändern sich die Schwingungsmuster von Lagern etwa bei einem Wellenversatz. Gemeinsam können die Analysten von SKF und ZF mit ihrer jeweiligen Fachkompetenz ermitteln, was die Schwingungsabweichungen bedeuten, auf welche Getriebekomponente sie wahrscheinlich zurückzuführen sind und welche Art von Reparaturmaßnahme wann durchgeführt werden muss.“
„Das Ziel ist, potenzielle Störungen vorauszusehen, bevor sie zu einem ungeplanten Stillstand führen. Und jede Stunde zählt. Legt man einen Strompreis von 60 Euro pro Megawattstunde zugrunde, kann der Verlust pro Tag bei einer 3,5-Megawatt-Turbine 1.800 Euro betragen. Bei einem vierwöchigen Stillstand der Turbine verursacht eine solche ungeplante Betriebsunterbrechung Umsatzeinbußen von 55.000 Euro.“
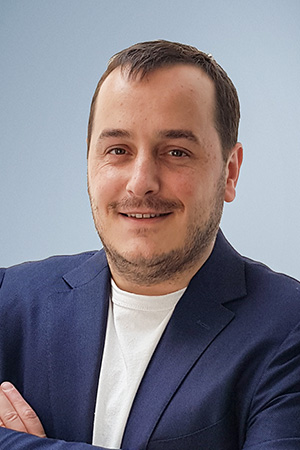
SEHEN-DENKEN-HANDELN
Joris Boeye, Ingenieur für Datenanalyse bei ZF, erklärt, das System arbeite nach dem Prinzip SEHEN-DENKEN-HANDELN. „Das Zustandsüberwachungssystem erfasst eine Abweichung, und nach einer Analyse durch SKF erhalten wir eine Warnmeldung. Wir verfügen über die Herstellungsdaten und die Systemkenntnis, um diese Warnmeldung zu bearbeiten – das ist der Teil SEHEN. Dann ermitteln wir, um welche Art von Fehler es sich handelt, wo sich die Turbine befindet und wie viel Zeit bis zu ihrem Ausfall bleibt – das ist die Phase DENKEN. Schließlich organisieren wir den entsprechenden Einsatzauftrag, die geeigneten Techniker und die richtigen Ersatzteile – das nennen wir HANDELN. “
Nordmark verdeutlicht: „Unsere Kernkompetenz zum Thema Lagerschwingungen mit der Kernkompetenz der Datenwissenschaftler von ZF zu kombinieren, war eine echte Herausforderung. Die Daten müssen in einem Kontext stehen, sonst sind sie einfach nur Daten und keine Informationen.“
Die Analyse von Abweichungen sei die Wissensdomäne von SKF und ZF in ihren jeweiligen Fachbereichen, so Nordmark. „Wie bei einem Auto, das über ein Schlagloch fährt, registrieren die Sensoren des Zustandsüberwachungssystems eine ‚Unregelmäßigkeit‘, wenn in einem Teil des Getriebes ein Problem auftritt. Natürlich ist es weitaus schwieriger, winzige Abweichungen in der Lagerschwingung zu erfassen als das Aufschlagen eines Fahrzeugs nach dem Überfahren eines Schlaglochs, aber das Prinzip ist ähnlich. Über die Reifen und die Federung des Fahrzeugs nehmen wir eine Abweichung wahr. Unsere Erfahrung als Fahrer sagt uns, dass wahrscheinlich ein Straßenschaden die Ursache ist. Auf vergleichbare Weise verändern sich die Schwingungsmuster von Lagern etwa bei einem Wellenversatz. Gemeinsam können die Analysten von SKF und ZF mit ihrer jeweiligen Fachkompetenz ermitteln, was die Schwingungsabweichungen bedeuten, auf welche Getriebekomponente sie wahrscheinlich zurückzuführen sind und welche Art von Reparaturmaßnahme wann durchgeführt werden muss.“
„Das Ziel ist, potenzielle Störungen vorauszusehen, bevor sie zu einem ungeplanten Stillstand führen. Und jede Stunde zählt. Legt man einen Strompreis von 60 Euro pro Megawattstunde zugrunde, kann der Verlust pro Tag bei einer 3,5-Megawatt-Turbine 1.800 Euro betragen. Bei einem vierwöchigen Stillstand der Turbine verursacht eine solche ungeplante Betriebsunterbrechung Umsatzeinbußen von 55.000 Euro.“
Senkung der Stromgestehungskosten (LCoE)
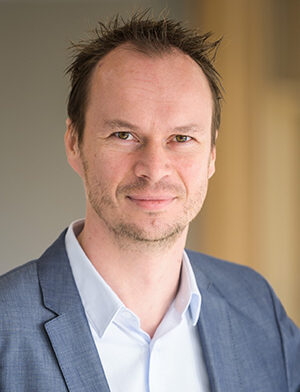
Das Pilotprojekt in einem Windpark mit mehreren Hundert Windturbinen hat gezeigt, was möglich ist: Das Ergebnis war ein Rückgang der Vor-Ort-Besichtigungen um 60 Prozent, eine um 85 Prozent verkürzte Vorlaufzeit für Reparaturen und ein Anstieg der jährlichen Energieerzeugung um 0,4 Prozent. Für 2021 ist die kommerzielle Einführung des Konzepts geplant.
Raf Kerkhofs, Leiter der Geschäftsentwicklung Wind Operation & Maintenance bei SKF, sieht ein enormes Potenzial. „Sowohl SKF als auch ZF erhalten Einblicke in den Betrieb ihrer Produkte und können ihren Kunden helfen, proaktiv über Lösungen und Upgrades nachzudenken“, meint er.
Peeters von ZF ergänzt: „Wir wenden zurzeit die neue Lösung auf vorhandene Zustandsüberwachungssysteme an. Als Nächstes soll sie in neue Installationen integriert werden. Wir könnten die Einstellungen für Warnmeldungen verbessern, und am Ende könnten wir sogar autonome Antriebsstränge haben, die es der Fabrik ermöglichen würden, ihre eigenen Reparaturmaßnahmen einzuleiten.“
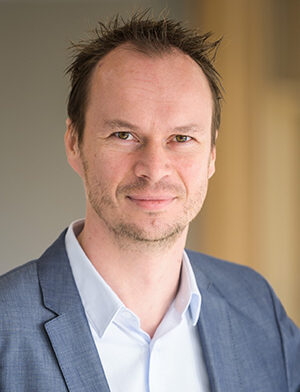
Senkung der Stromgestehungskosten (LCoE)
Das Pilotprojekt in einem Windpark mit mehreren Hundert Windturbinen hat gezeigt, was möglich ist: Das Ergebnis war ein Rückgang der Vor-Ort-Besichtigungen um 60 Prozent, eine um 85 Prozent verkürzte Vorlaufzeit für Reparaturen und ein Anstieg der jährlichen Energieerzeugung um 0,4 Prozent. Für 2021 ist die kommerzielle Einführung des Konzepts geplant.
Raf Kerkhofs, Leiter der Geschäftsentwicklung Wind Operation & Maintenance bei SKF, sieht ein enormes Potenzial. „Sowohl SKF als auch ZF erhalten Einblicke in den Betrieb ihrer Produkte und können ihren Kunden helfen, proaktiv über Lösungen und Upgrades nachzudenken“, meint er.
Peeters von ZF ergänzt: „Wir wenden zurzeit die neue Lösung auf vorhandene Zustandsüberwachungssysteme an. Als Nächstes soll sie in neue Installationen integriert werden. Wir könnten die Einstellungen für Warnmeldungen verbessern, und am Ende könnten wir sogar autonome Antriebsstränge haben, die es der Fabrik ermöglichen würden, ihre eigenen Reparaturmaßnahmen einzuleiten.“
Das Zustandsüberwachungssystem SKF IMx
SKF IMx ist die nächste Generation von leistungsstarken, kostengünstigen Lösungen speziell für die Zustandsüberwachung von Windturbinen. Die robuste Messeinheit ist für den Einbau in Onshore- und Offshore-Windparks geeignet.
Die dynamischen Signaleingänge des Systems sind für eine Vielzahl von Sensoren konfigurierbar. Zusammen mit der SKF @ptitude Observer Software bietet SKF IMx eine komplette Lösung für die Fehlerfrüherkennung und -vorbeugung. Sie generiert automatische Vorschläge zur Behebung von vorhandenen oder drohenden Zuständen und für qualifizierte zustandsbasierte Instandhaltungsmaßnahmen, um die Zuverlässigkeit, Verfügbarkeit und Leistung zu verbessern.