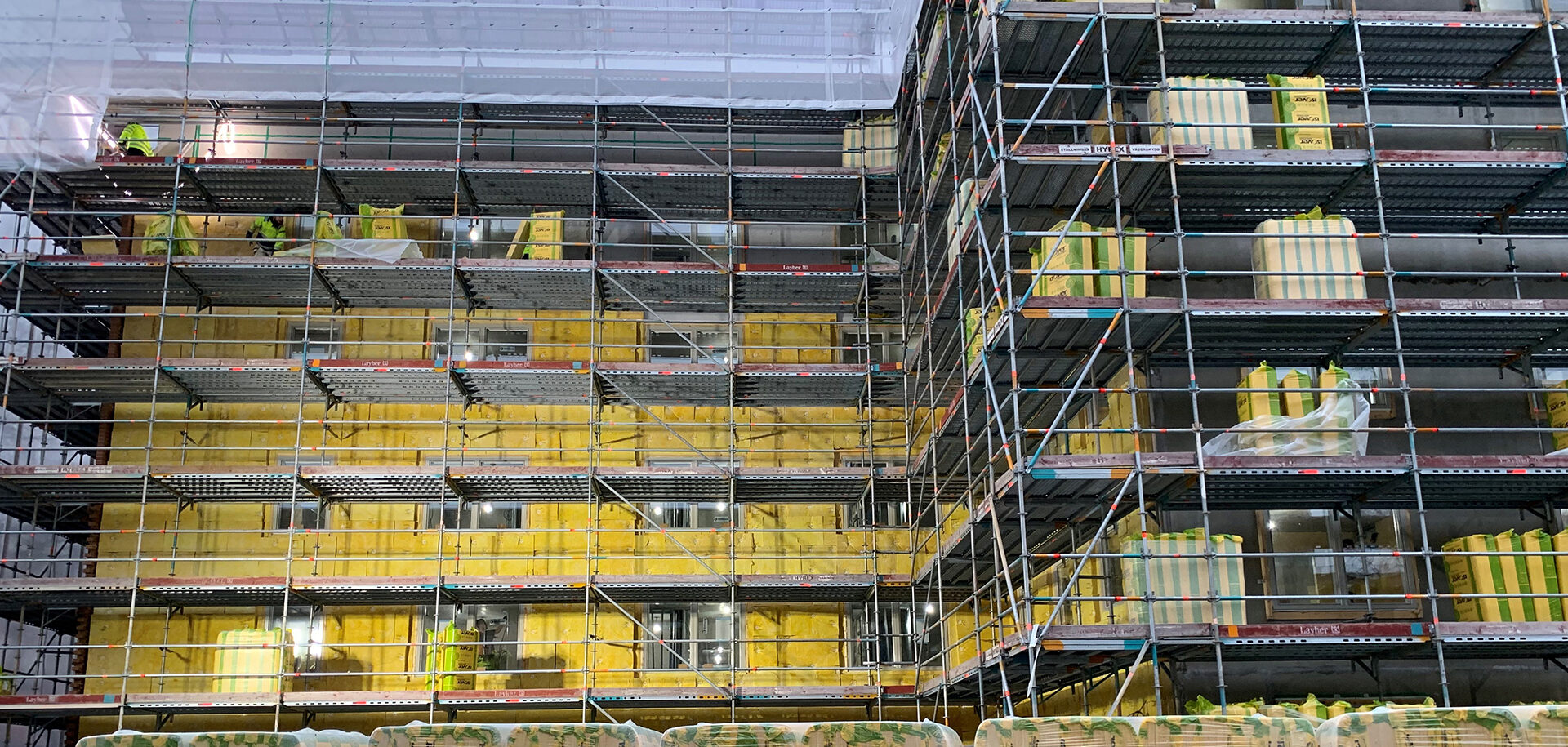
Saint-Gobain Isover, macchine a prova di cedimento
Grazie alla tecnologia digitale, i team di manutenzione di Saint-Gobain Isover ottimizzano la produzione di un materiale che può contribuire a salvare il pianeta.
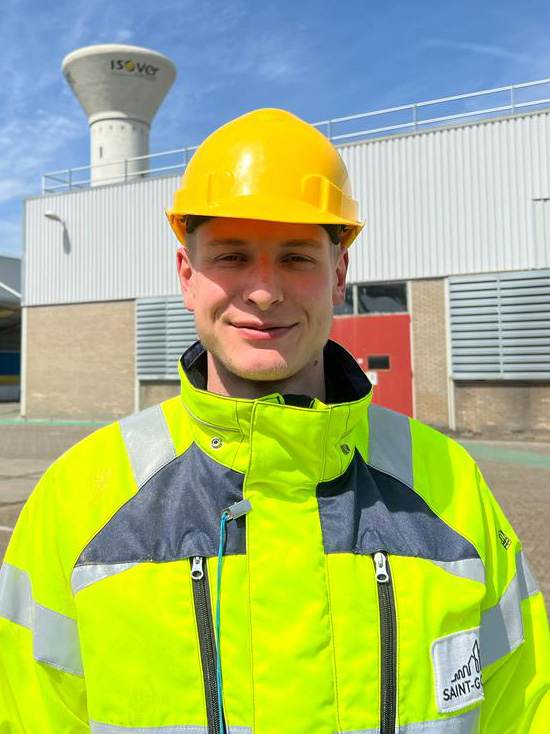
Come stare comodamente a casa e al lavoro senza surriscaldare il pianeta? A livello globale, gli edifici sono responsabili di circa il 40 percento delle emissioni di CO2 relative all’energia, oltre due terzi dei quali sono prodotte con il riscaldamento e il condizionamento.
Per raggiungere gli obiettivi di riduzione dei gas a effetto serra è necessario accelerare la transizione verso edifici più sostenibili ed efficienti. Questo richiederà investimenti in nuove tecnologie, quali pannelli solari e pompe di calore alimentati da fonti rinnovabili. Ma per ridurre l’impatto ambientale degli edifici c’è anche un modo molto efficace, oltre che semplice: l’isolamento termico.
Semplice, conveniente e di comprovata efficacia, l’isolamento termico degli edifici evita le dispersioni di calore attraverso pareti e tetti. Nella maggior parte degli edifici, i costi dell’isolamento aggiuntivo vengono recuperati in pochi anni grazie ai risparmi sulle bollette dell’energia.
Lo stabilimento Saint-Gobain Isover di Etten-Leur, nei Paesi Bassi, opera nel settore dell’efficienza energetica dal 1962. Ogni anno produce circa 45.000 tonnellate di isolanti in lana di vetro, compresi guaine per la coibentazione dei tetti e isolanti sfusi per insufflaggio in intercapedini o sottotetti.
Nello stabilimento di produzione di Etten-Leur ci sono tre linee dedicate alla lana di vetro e una alla fibra di vetro utilizzata come rivestimento per alcuni dei suoi prodotti. Bas Beishuizen è un ingegnere che si occupa della manutenzione dell’impianto. Il suo compito è assicurare il funzionamento affidabile ed efficiente delle apparecchiature correlate. Dato che la produzione di lana di vetro presuppone velocità e volumi elevati e un’alta intensità energetica, il team di manutenzione ha molto di cui occuparsi.
“Nell’impianto ci sono 57 macchine cruciali”, afferma Beishuizen. “Essenzialmente sono pompe e ventilatori, che in genere hanno dimensioni notevoli. I ventilatori più grandi, per esempio, sono azionati da motori da 500 kilowatt”.
Come stare comodamente a casa e al lavoro senza surriscaldare il pianeta? A livello globale, gli edifici sono responsabili di circa il 40 percento delle emissioni di CO2 relative all’energia, oltre due terzi dei quali sono prodotte con il riscaldamento e il condizionamento.
Per raggiungere gli obiettivi di riduzione dei gas a effetto serra è necessario accelerare la transizione verso edifici più sostenibili ed efficienti. Questo richiederà investimenti in nuove tecnologie, quali pannelli solari e pompe di calore alimentati da fonti rinnovabili. Ma per ridurre l’impatto ambientale degli edifici c’è anche un modo molto efficace, oltre che semplice: l’isolamento termico.
Semplice, conveniente e di comprovata efficacia, l’isolamento termico degli edifici evita le dispersioni di calore attraverso pareti e tetti. Nella maggior parte degli edifici, i costi dell’isolamento aggiuntivo vengono recuperati in pochi anni grazie ai risparmi sulle bollette dell’energia.
Lo stabilimento Saint-Gobain Isover di Etten-Leur, nei Paesi Bassi, opera nel settore dell’efficienza energetica dal 1962. Ogni anno produce circa 45.000 tonnellate di isolanti in lana di vetro, compresi guaine per la coibentazione dei tetti e isolanti sfusi per insufflaggio in intercapedini o sottotetti.
Nello stabilimento di produzione di Etten-Leur ci sono tre linee dedicate alla lana di vetro e una alla fibra di vetro utilizzata come rivestimento per alcuni dei suoi prodotti. Bas Beishuizen è un ingegnere che si occupa della manutenzione dell’impianto. Il suo compito è assicurare il funzionamento affidabile ed efficiente delle apparecchiature correlate. Dato che la produzione di lana di vetro presuppone velocità e volumi elevati e un’alta intensità energetica, il team di manutenzione ha molto di cui occuparsi.
“Nell’impianto ci sono 57 macchine cruciali”, afferma Beishuizen. “Essenzialmente sono pompe e ventilatori, che in genere hanno dimensioni notevoli. I ventilatori più grandi, per esempio, sono azionati da motori da 500 kilowatt”.
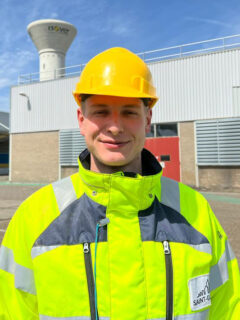
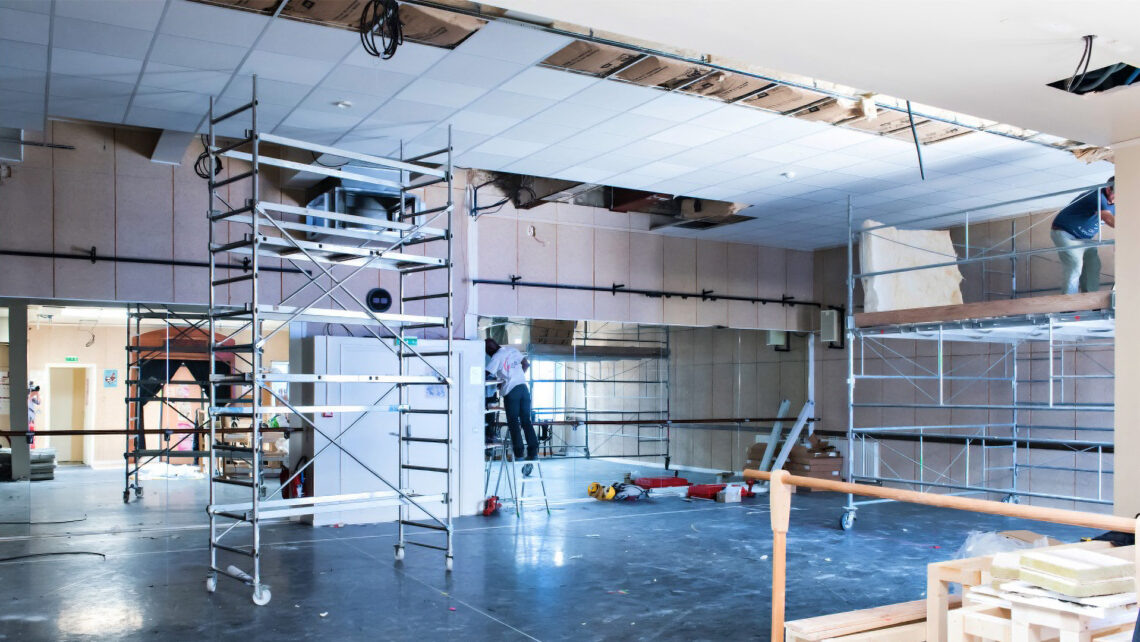
Prevenire gli imprevisti
Il cedimento delle macchine più importanti provoca fermi delle linee, che possono portare a scartare interi lotti di materiale. Ove possibile, il team di manutenzione di Etten-Leur mira ad adottare procedure di manutenzione di tipo preventivo e basate sulle condizioni. “Per ottimizzare la manutenzione dei cuscinetti, abbiamo cominciato con l’utilizzare i sensori portatili SKF QuickCollect. Determiniamo la frequenza con cui misurare le vibrazioni in base all’importanza e alla criticità del componente. Un tecnico effettua le misurazioni e, in collaborazione con SKF, analizza i cuscinetti. I dati ottenuti ci permettono di capire e identificare eventuali problemi”.
Con l’aiuto degli esperti SKF, i dispositivi portatili si sono rivelati ben presto molto utili
Bas Beishuizen, maintenance engineer di Saint-Gobain Isover
Con l’aiuto degli esperti SKF, i dispositivi portatili si sono rivelati ben presto molto utili. L’analisi degli spettri di vibrazione ha evidenziato, per esempio, una lubrificazione carente in alcuni cuscinetti. “Approfondendo, abbiamo capito che su alcune macchine i punti di lubrificazione erano nella posizione sbagliata, quindi il grasso non arrivava dove serviva”, spiega Beishuizen. “Ma quando abbiamo individuato la causa, il problema è stato risolto facilmente”.
La misura delle vibrazioni permette di individuare problemi anche in altri punti dell’apparecchiatura, non necessariamente legati ai cuscinetti. “Un problema ricorrente riscontrato da Saint-Gobain Isover è lo squilibrio dei ventilatori”, dice. “La contaminazione che si accumula sulle loro pale li rende meno efficienti e arriva a causarne il cedimento. Misurare le vibrazioni permette al team di manutenzione di collaborare con il gruppo operativo per eseguire, durante i fermi macchina, la pulizia e l’equilibratura dei ventilatori contaminati. Questo riduce i guasti causati dal cedimento di cuscinetti o fissaggi motore dovuti alle forti vibrazioni”.
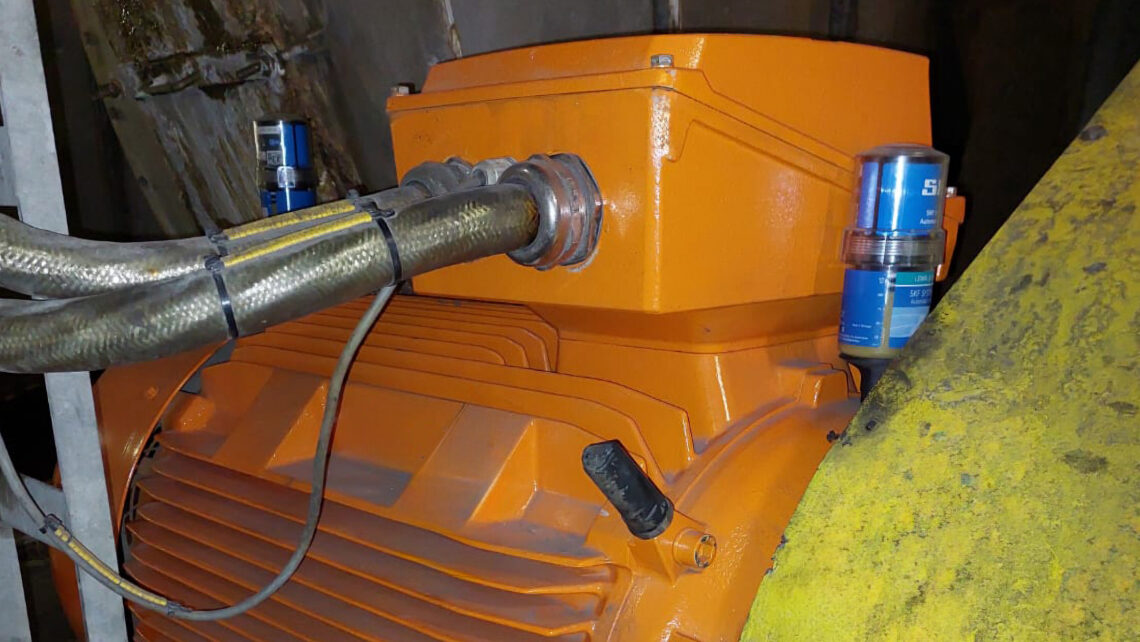
Online
Il risultato positivo ottenuto con la misura delle vibrazioni ha invogliato Beishuizen a fare di più. “Le misurazioni manuali forniscono dati molto utili, ma queste vengono eseguite solo un certo numero di volte all’anno”, commenta. “Al team di manutenzione occorrono più informazioni, quindi occorre intensificare la frequenza delle misurazioni per avere dati più attendibili”.
Il team di Etten-Leur è quindi passato alla tecnologia di monitoraggio online, installando sulle principali macchine all’interno dello stabilimento i sensori fissi SKF IMx-1. Questi dispositivi compatti, a batteria, registrano di continuo i dati relativi alle vibrazioni e alla temperatura e li trasmettono tramite una rete mesh wireless a un gateway, che li invia al cloud SKF utilizzando una connessione mobile 4G. “All’interno di Saint-Gobain avevamo già una piattaforma software di gestione della manutenzione, ma grazie alla connessione API tra SKF e la nostra azienda possiamo estrarre tutti i dati sulle vibrazioni e combinarli con gli altri”, dice Beishuizen. “In questo modo tutte le informazioni sono organizzate in un unico punto”.
Il monitoraggio continuo delle vibrazioni offre molteplici vantaggi. Un improvviso aumento delle vibrazioni, per esempio, innesca un allarme che permette agli operatori preposti di avviare un’indagine. La registrazione dei dati nel tempo, invece, consente di individuare le tendenze progressive che indicano un potenziale calo delle prestazioni di una macchina.
“Il team di manutenzione lavora allo sviluppo di un’apposita dashboard per istituire procedure di manutenzione basate sulle condizioni nello stabilimento Isover”, afferma Beishuizen. “La dashboard di dati fornisce una panoramica di tutte le macchine critiche e dà la priorità a quelle che richiedono attenzione.
“Nel corso dell’anno programmiamo vari fermi per ogni linea per eseguire la manutenzione. Ora puntiamo a sapere esattamente, attraverso i dati, quali sono le azioni da intraprendere durante ogni fermo”. Questo ottimizzerebbe la manutenzione e ridurrebbe i tempi di fermo; le ispezioni preventive vengono già effettuate attraverso le analisi.
Ma questo, come sostiene Beishuizen, è solo il passo successivo. Il team di manutenzione ha molti altri obiettivi per supportare la digitalizzazione della manutenzione dell’impianto. “Combinando i dati sulle condizioni con quelli relativi ai processi operativi e alla manutenzione, possiamo delineare un quadro più completo circa le prestazioni delle macchine e le loro modalità e tempistiche di cedimento”, osserva. “Così potremo concentrare i nostri sforzi su progetti mirati a migliorare l’affidabilità e l’efficienza dei processi”.
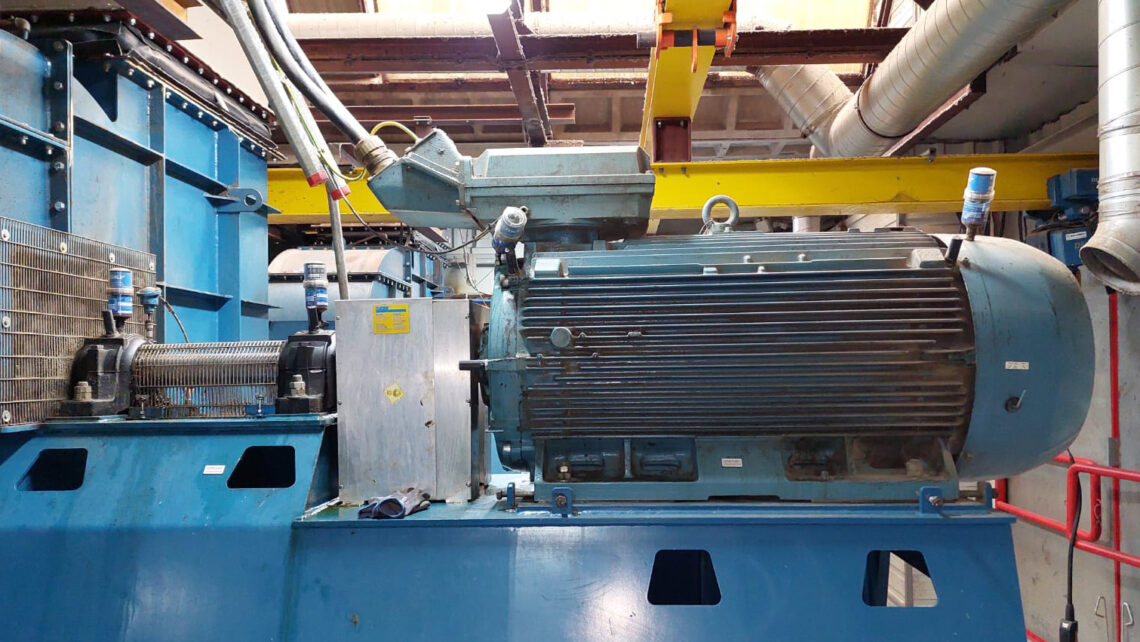
Come zucchero filato
La produzione della lana di vetro ricorda un po’ quella dello zucchero filato, dove la rotazione delle macchine trasforma lo zucchero liquido in una soffice nuvola dolce, anche se le temperature di processo e i volumi di produzione sono molto più elevati.
Le materie prime vengono prima miscelate e poi portate a fusione in un forno a circa 1400 °C. Di solito si impiegavano i componenti base del vetro, ossia sabbia, carbonato di sodio e calcare. Ma oggi circa la metà della miscela utilizzata nei forni Isover è costituita da vetro riciclato. Questo permette di ridurre il consumo di materie prime vergini e di energia, poiché il vetro fonde a una temperatura inferiore rispetto alla sabbia.
Il vetro fuso viene pompato attraverso un sistema di centrifughe, che lo trasformano in fibre dello spessore di un capello. Per conferire al prodotto finito il formato desiderato, come rotoli o pannelli, sulle fibre viene spruzzato un apposito legante. Il prodotto ottenuto viene quindi convogliato in un forno di polimerizzazione, dove viene compresso fino allo spessore finale. Il legante polimerizzato tiene unite le fibre nel punto di intersezione, dando vita a un materiale resistente che può essere ridotto a un decimo del suo volume per il trasporto. Una volta disimballato, ritorna a grandezza naturale. A seconda dell’applicazione finale, sui pannelli può essere incollato un rivestimento in fibra di vetro per aumentare ulteriormente la durata e la facilità di movimentazione.
La perfetta quantità di lubrificante
Dopo aver sperimentato gli effetti di una lubrificazione carente delle macchine strategiche, nello stabilimento di Etten-Leur è stata adottata un’ulteriore tecnologia SKF. “Sappiamo che per sei mesi di funzionamento un cuscinetto può richiedere 50 grammi di grasso”, afferma Bas Beishuizen, maintenance engineer di Saint-Gobain Isover. “Se il lubrificante viene aggiunto tutto in una volta, tuttavia, non si ottengono prestazioni migliori; inoltre non è sempre facile capire se il cuscinetto sia stato davvero lubrificato”.
Di qui la scelta di installare un sistema con lubrificatori per singolo punto SKF TLDD. Questi dispositivi erogano da un apposito serbatoio piccole dosi di lubrificante per ciascun cuscinetto, a intervalli regolari e a un ritmo predeterminato. I dispositivi segnalano il loro stato al cloud SKF attraverso una rete wireless e un gateway per rete mobile 4G. Il team di manutenzione può quindi sapere se i cuscinetti sono stati lubrificati, se un’unità deve essere riempita e se il flusso di lubrificante è stato interrotto.