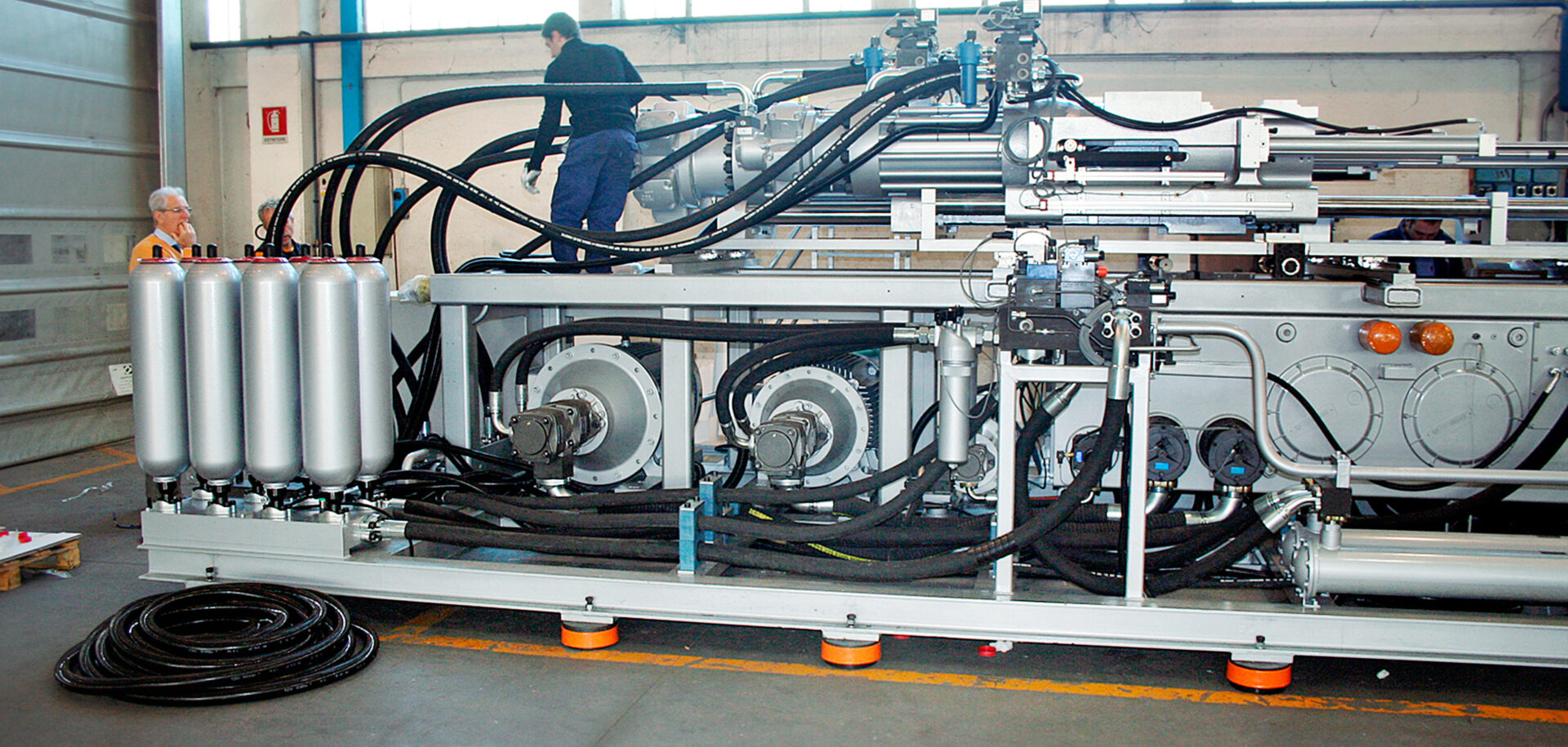
Tecnologia elettrica per la plastica
Un’impresa italiana a conduzione familiare plasma il futuro dello stampaggio a iniezione delle materie plastiche.
Fatti
BMB SPA
- Fondata: 1967, a Brescia
- Direzione: Egidio Bugatti, presidente; Marco Bugatti, amministratore delegato
- Sede: quartier generale a Brescia; uffici commerciali in 30 paesi
- Proprietà privata
- Linee di produzione: macchine per lo stampaggio a iniezione (ad azionamento ibrido, elettrico, idraulico)
- Fatturato 2011: 70 milioni di euro
- Numero complessivo di dipendenti: 180
Link correlati
Contatto vendite
Giuseppe Saroglia, giuseppe.saroglia@skf.com
“Solo una parola … Plastica”. Era il 1967 e la frase del film Il Laureato, diventata famosa, annunciava un futuro promettente. Nello stesso anno, fiduciosi nelle potenzialità della plastica, tre bresciani decidevano di fondare una società. Egidio Bugatti, suo fratello Domenico e il cognato Giuseppe Moreschi diedero vita alla BMB (dalle iniziali dei rispettivi cognomi) e cominciarono a produrre macchine per lo stampaggio delle materie plastiche.
Egidio Bugatti aveva già maturato oltre dieci anni di esperienza nel settore dello stampaggio a iniezione e nella progettazione di sistemi a ginocchiera. I tre soci erano convinti che l’industria della ”plastica” sarebbe cresciuta e che lo sviluppo della loro azienda dipendesse dalla capacità di realizzare macchine più efficienti, più precise e più affidabili di quelle dei concorrenti.
“Dovevamo fare meglio”, dice Bugatti, ricordando momenti di concorrenza spietata. Partendo da questo presupposto, la giovane azienda riuscì ad aggiudicarsi ordini da clienti come Olivetti, Bic e Coster – aziende primarie, che richiedevano velocità, precisione e controllo integrato della qualità. “Hanno contribuito alla nostra crescita e al nostro posizionamento nella fascia alta di mercato”.
Negli anni settanta la BMB registrò una crescita costante facendo leva su alcuni principi imprescindibili: qualità, precisione e integrità. L’azienda registrò il suo primo brevetto nel 1980, diventando il primo costruttore di macchine per lo stampaggio con elettronica integrata.
Sempre nel 1980, l’azienda si trasferì dalla sede originaria, ormai divenuta troppo piccola, a quella attuale, nella zona industriale alla periferia di Brescia. Ampliato nel corso degli anni, lo stabilimento consta oggi di tre edifici contigui che ospitano gli uffici amministrativi, quelli tecnici e tre unità di produzione (dedicate rispettivamente a macchine fino a 400 tonnellate, tra 450 e 3.500 tonnellate e superiori a 3.500 tonnellate). La struttura, che si estende su una superficie di 30.000 metri quadrati, appare linda e modernissima.
La BMB continuò a crescere anche negli anni ottanta, producendo macchine per lo stampaggio a iniezione di tipo tradizionale, caratterizzate da elevate prestazioni e affidabilità costante. A parte alcune macchine vendute all’estero, l’ambito nel quale l’azienda operava ed era conosciuta rimaneva essenzialmente quello italiano.
Le cose cominciarono a cambiare negli anni novanta, quando Marco, figlio di Bugatti, entrò in azienda. Laureatosi al Politecnico di Milano, maturò un’esperienza lavorativa per la BMB nel Regno Unito e, nel 1994, fece il suo ingresso nell’impresa di famiglia. Esortò a rivedere la struttura commerciale dell’azienda, auspicando una maggiore attenzione verso i mercati esteri. Attualmente, l’85 percento della produzione è esportato, in particolare in America Latina, con una recente apertura anche in Nord America.
Sorprende ancora di più il cambiamento nella gamma dei prodotti. Non più tardi di otto anni fa, tutte le macchine prodotte dalla BMB erano azionate idraulicamente. Oggi solo il 20 percento è di tipo idraulico. Le macchine completamente elettriche, introdotte per la prima volta dalla BMB nel 2005, rappresentano il 35-40 percento della produzione annuale, mentre quelle ibride, introdotte nel 2007, ne formano il 40–45 percento.
Le macchine elettriche per lo stampaggio erano state adottate in Giappone già nel 1983. Tuttavia, nonostante gli indubbi vantaggi – costi energetici ridotti, maggiore precisione, compatibilità ambientale, ingombri relativamente contenuti e minori costi del ciclo di vita – gli elevati costi di partenza avevano scoraggiato i clienti fuori dal Giappone. Il forte aumento del costo dell’energia ha decisamente mutato questo atteggiamento. A fronte di un costo iniziale superiore del 30-40 percento, il costo totale del ciclo di vita di una macchina elettrica risulta inferiore del 40 percento, oltre a offrire altri vantaggi.
La BMB costruì il primo prototipo elettrico nel 2002 e passò ai modelli ibridi quando la clientela cominciò a chiedere macchine più grandi e più veloci, da impiegare per i prodotti a pareti sottili e difficili da movimentare che le macchine elettriche non potevano processare. Ne è un esempio la macchina ibrida eKW70PI/7000, introdotta nel 2008, che produce vasetti di yogurt in stampi con cavità 16+16.Utilizza la tecnologia elettrica per tutte le funzioni tranne che per l’effettiva iniezione della plastica, per la quale è azionata da un sistema accumulatore idraulico che permette di raggiungere le velocità di riempimento necessarie.
Sia Egidio sia Marco Bugatti sono convinti che il futuro di questa industria consista esclusivamente nella tecnologia elettrica. Per Egidio Bugatti, “c’è ampio spazio di crescita nel settore dello stampaggio della plastica. E intendiamo rimanere tra i protagonisti di questo sviluppo”.
Gigante elettromeccanico
Nel 2004, quando la BMB cominciò a concentrare l’attenzione sulle apparecchiature elettriche, si rivolse alla SKF. “Sapevamo che la SKF aveva esperienza nelle viti a rulli e nelle macchine elettriche per lo stampaggio. Volevamo che fossero nostri partner nello sviluppo di macchinari elettrici che supportassero cicli di quattro secondi ad alte velocità”, dichiara il presidente della BMB, Egidio Bugatti.
Per soddisfare questi severi requisiti, la SKF ha realizzato un apposito assortimento di viti a rulli satelliti, con capacità di carico estremamente elevate. La nuova macchina BMB per lo stampaggio a iniezione da 1.700 tonnellate, ad azionamento ibrido, presenta un meccanismo a ginocchiera che è il più ampio mai realizzato con la tecnologia elettromeccanica, il quale richiede pressioni elevate che comportano un alto rischio di disallineamento. Le viti a rulli satelliti SKF sono progettate per evitare questi problemi e i conseguenti tempi di fermo. Inoltre, come fa notare Giuseppe Saroglia, Manager dell’SKF Mechatronic Business, “le viti riducono drasticamente la quantità di olio idraulico e, di conseguenza, le esigenze di raffreddamento”.