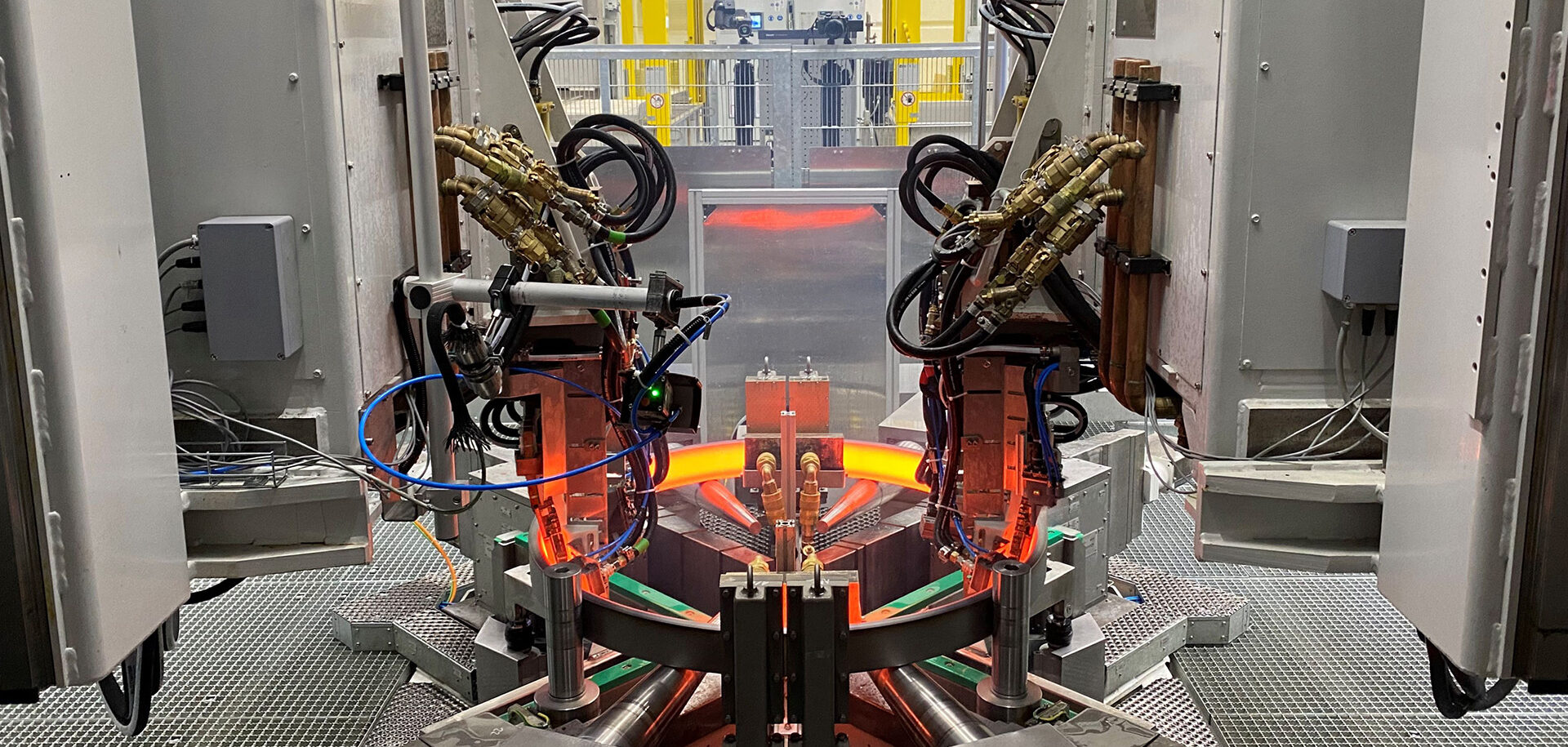
Tempra, da tradizionale a selettiva
Una tecnologia di tempra, rapida e a risparmio energetico, sta per fare il suo debutto industriale.
Per offrire prestazioni elevate e lunghe durate di esercizio, i materiali con cui sono fabbricati gli anelli dei cuscinetti devono soddisfare requisiti diversi. Da un lato devono assicurare durezza per reggere i carichi imposti dai corpi volventi e, dall’altro, tenacità per resistere alle sollecitazioni cui sono sottoposti. Per raggiungere questo delicato equilibrio, i produttori utilizzano un materiale relativamente morbido, che viene sottoposto a un trattamento termico atto a migliorare le proprietà di durezza e resistenza all’usura.
Il trattamento di tempra superficiale può essere eseguito con vari metodi, ma tutti di norma richiedono un notevole apporto di calore. Tipicamente vengono impiegati forni di carbocementazione, che però tendono a rallentare il processo, oltre a essere piuttosto inquinanti e poco efficienti in termini energetici. Una serie di fattori indesiderabili per i produttori di cuscinetti – e i loro clienti – che vogliono una produzione rapida, flessibile, economica e a basso impatto ambientale.
L’impatto ambientale conta
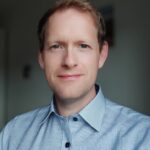
“I clienti che operano nel settore delle rinnovabili sono particolarmente attenti all’impatto ambientale dei prodotti che acquistano, poiché mirano a decarbonizzare le proprie catene di fornitura”, dichiara Michael Wendel, manager, Induction Hardening Technicum di SKF, che ha sede a Schweinfurt, in Germania.
Un’alternativa all’impiego dei forni è la tempra a induzione, che sfrutta un potente campo magnetico alternato per riscaldare la superficie dell’anello. Più conveniente in termini di tempi e risparmio energetico grazie al rapido riscaldamento di zone specifiche e limitate del componente da trattare, la tempra a induzione è un processo regolabile all’istante, che permette di avere un controllo preciso sulla profondità di tempra.
Il suo impiego è stato ampiamente diffuso nella produzione di cuscinetti. Gli anelli di piccole dimensioni, con diametri fino a circa 500 millimetri, vengono temprati in un’unica soluzione (one shot) tramite un induttore che abbraccia completamente l’anello e ne riscalda l’intera superficie. Per gli anelli di grandi dimensioni, con diametri di svariati metri, si utilizza una tecnica di tempra a scansione. Viene usato un sistema costituito da induttore e doccia di raffreddamento lungo la superficie del componente, che permette di riscaldare e raffreddare progressivamente piccole sezioni.
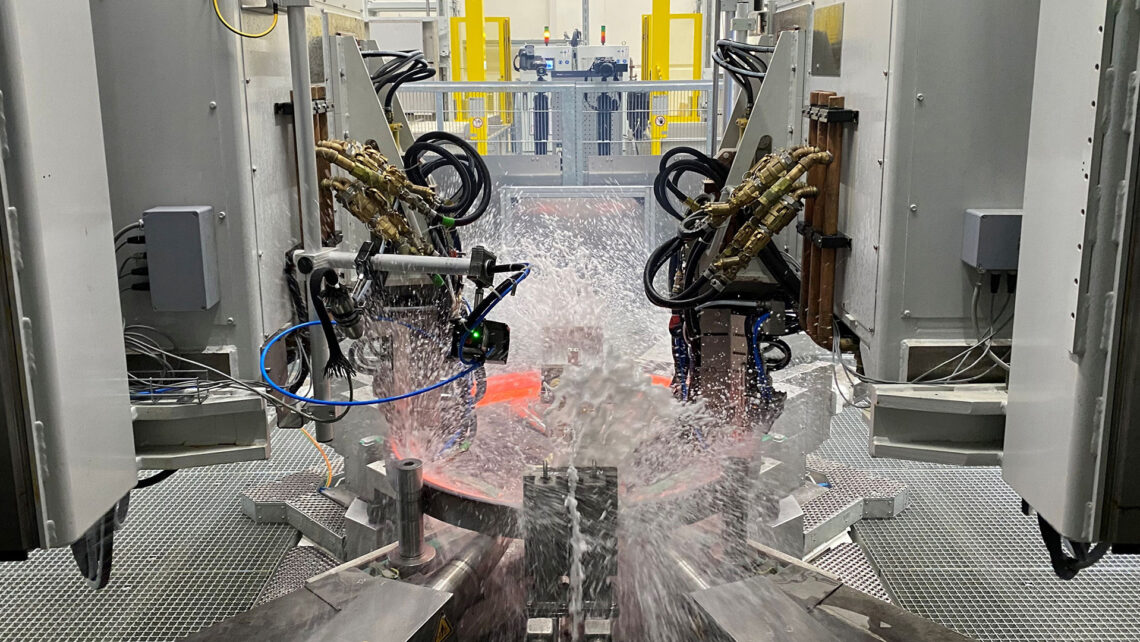
Colmare la lacuna
Fino a poco tempo fa, tuttavia, per i produttori la tempra a induzione aveva un limite dato dal fatto che i cuscinetti di dimensioni medie, con diametri da 500 millimetri a circa 1,6 metri, sono troppo grandi per la cosiddetta tempra one-shot e troppo piccoli per quella a scansione.
I clienti che operano nel settore delle rinnovabili sono particolarmente attenti all’impatto ambientale dei prodotti che acquistano
Michael Wendel, manager, Induction Hardening Technicum di SKF, che ha sede a Schweinfurt, in Germania.
Dal 2017 un team dell’SKF Centre for Manufacturing Development di Schweinfurt è impegnato a colmare questa lacuna. Il progetto, completato con il sostegno finanziario del Ministero tedesco per gli Affari Economici e l’Azione per il Clima, è pronto per la fase successiva.
Induflex, così si chiama il sistema messo a punto dal team SKF, è stato concepito per eseguire la cementazione in un’unica soluzione di anelli con diametro compreso tra 450 e 1.800 millimetri. Un anello viene bloccato sulla macchina e fatto ruotare rapidamente accanto a due induttori, ciascuno montato su un braccio attuatore controllato da un computer. Il braccio regola continuamente la posizione dell’induttore, mantenendo una distanza precisa dall’anello mentre si riscalda e si espande. Quando la superficie raggiunge la temperatura desiderata, un sistema a doccia sui bracci si attiva per raffreddare il materiale.
“Rispetto alla tipica cementazione in forno, il processo Induflex è più pulito, più veloce e molto più efficiente dal punto di vista energetico”, commenta Wendel. “Temprare un anello da 512 chilogrammi con i sistemi Induflex richiede solo pochi minuti e 81 kWh di energia, ossia una riduzione di almeno due ordini di grandezza rispetto al trattamento in forno”.
Alimentato da fonti rinnovabili
Utilizzando solo il riscaldamento elettrico, il sistema Induflex può essere alimentato da fonti rinnovabili, il che consente di ridurre l’impronta di carbonio. Pur trovando impiego in un’ampia gamma di macchine industriali, i cuscinetti di medie dimensioni assumono oggi una rilevanza crescente nel settore delle energie rinnovabili. “I cuscinetti di queste dimensioni sono utilizzati per i rotori e i riduttori delle turbine eoliche”, osserva Wendel.
Il processo a induzione offre anche altri vantaggi ambientali rispetto alle tecnologie tradizionali. Non richiede gas di processo o sostanze chimiche come azoto, gas naturale, metanolo o ammoniaca. “Questo semplifica anche la catena di approvvigionamento, un aspetto sempre più importante data la recente volatilità dei prezzi e le difficoltà di reperimento di questi prodotti”, afferma Wendel. La tempra a induzione consente inoltre l’uso di acciai bassolegati per cuscinetti, che sono più vantaggiosi economicamente e hanno un minore impatto ambientale.
Induflex promette di semplificare le cose per i produttori. I bracci computerizzati che controllano gli induttori possono essere riconfigurati premendo un pulsante per adattarsi ad anelli con dimensioni e profili diversi. Questo rende superfluo l’uso di attrezzi specifici e consente la produzione di piccoli lotti, passando senza problemi da un prodotto all’altro.
Negli ultimi quattro anni, Wendel e il suo team hanno perfezionato il sistema Induflex e sottoposto i prototipi di materiali a test rigorosi. “Abbiamo ottenuto ottimi risultati”, dichiara. “Le superfici presentano proprietà eccellenti, quali una microstruttura raffinata, tensioni residue di compressione ed elevata durezza. Questo permette di realizzare anelli più robusti e resistenti alla formazione e alla propagazione di cricche”.
Pronti a cominciare
Si è ora passati alla produzione di prototipi di cuscinetti completi, che vengono assemblati e sottoposti a rigorosi collaudi. “I risultati dei test sui cuscinetti finora ottenuti sembrano molto promettenti”, sostiene Wendel. Le prove interne continueranno per tutto il 2023; SKF è al lavoro con un gruppo selezionato di clienti per testare l’idoneità dei cuscinetti trattati con Induflex alle loro applicazioni.
Nel frattempo, si lavora per industrializzare completamente il processo. “È stata costruita la prima macchina Induflex per il lavoro di sviluppo”, dice Wendel. “Ha controlli e strumentazione aggiuntivi, che non sarebbero necessari su una macchina di produzione, e non è nemmeno stata progettata per integrarsi in un ambiente di fabbrica in rapido movimento”.
Una volta ultimato il lavoro di sviluppo, all’inizio del 2024, le macchine Induflex completamente industrializzate troveranno impiego nei siti produttivi SKF di tutto il mondo. “Ci stiamo preparando alla messa in opera di questa tecnologia nei nostri stabilimenti che producono cuscinetti per il settore delle energie rinnovabili”, afferma Wendel.
Tecniche di trattamento superficiale degli anelli: dalla nitrurazione alla tempra selettiva
Con il sostegno del governo tedesco
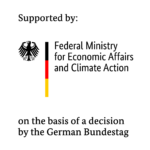