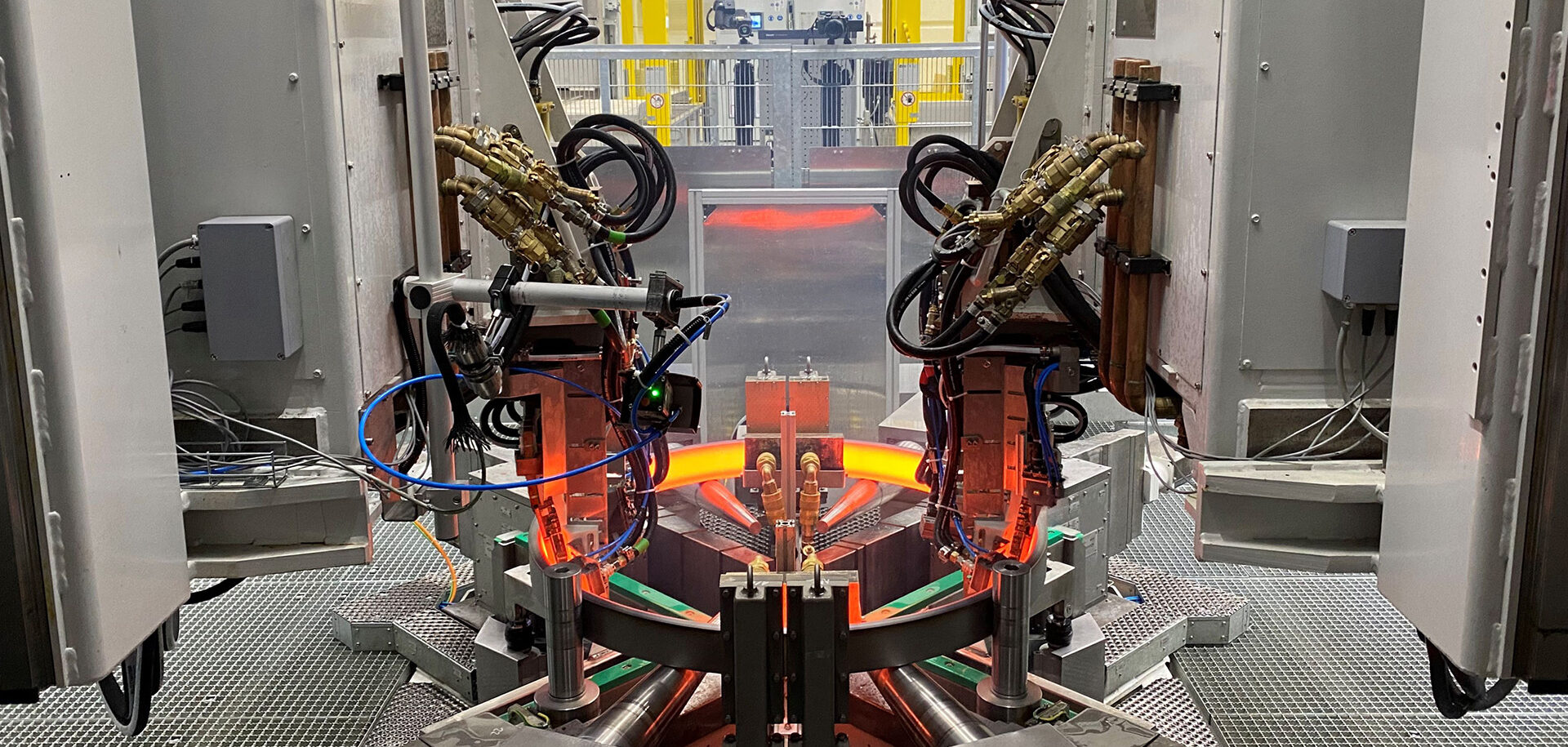
Von der traditionellen zur selektiven Härtung
Eine schnelle und energieeffiziente Härtungstechnologie steht kurz vor ihrer industriellen Reife.
Hohe Leistung und lange Lebensdauer – dafür müssen die Werkstoffe von Lagerringen gegensätzliche Anforderungen erfüllen. Sie müssen hart sein, um den von den Wälzkörpern übertragenen Lasten standzuhalten, aber gleichzeitig auch eine so hohe Zähigkeit aufweisen, dass sie unter Druckeinwirkung nicht brechen. Diese komplizierte Mischung erreicht man, indem man die Ringe aus einem relativ weichen Material fertigt und sie dann entsprechend behandelt, um daraus harte, verschleißbeständige Komponenten mit dem richtigen Gleichgewicht zwischen Härte und Zähigkeit zu machen.
Die Herstellung lässt sich auf unterschiedliche Weise durchführen, aber fast alle Verfahren erfordern ein hohes Maß an Wärme. Das Härten in den üblicherweise dafür eingesetzten Spezialöfen ist oft ein langsamer, schmutziger und extrem energieintensiver Prozess – höchst unerwünscht in einer Welt, in der Lagerhersteller und deren Kunden schnelle, flexible und kostengünstige Produktionsmethoden mit minimalem CO2-Ausstoß nachfragen.
Umweltbelastung wichtig
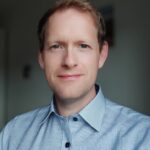
„Unsere Kunden aus dem Bereich der erneuerbaren Energien sind ganz besonders an den Umweltauswirkungen der Produkte, die sie kaufen, interessiert, weil sie ihre eigenen Lieferketten dekarbonisieren wollen“, sagt Michael Wendel, Leiter Induction Hardening Technicum bei SKF mit Sitz in Schweinfurt.
Eine Alternative zur Ofenhärtung ist die Induktionshärtung. Dabei werden Lagerringe einem kraftvollen, wechselnden Magnetfeld ausgesetzt, um eine Erwärmung an der Oberfläche der Ringe zu erzeugen. Die Induktionshärtung ist ein schnelles und energieeffizientes Verfahren, weil es kurze Bearbeitungszeiten und eine selektive Erwärmung ermöglicht und im Stillstand keine Energie verbraucht. Hinzu kommt, dass dieses Verfahren sich innerhalb kürzester Zeit anpassen lässt. Dadurch erhalten Hersteller Kontrolle über die Tiefe der gehärteten Oberflächenschicht.
In der Lagerfertigung ist die Induktionshärtung weit verbreitet. Kleine Ringe bis zu einem Durchmesser von circa 500 Millimetern werden in einem One-Shot-Prozess gehärtet. Die dafür verwendete Induktionsspule ist eine Rundspule, mit der die gesamte Oberfläche des Rings erhitzt werden kann. Für sehr große Ringe mit Durchmessern von mehreren Metern wird ein Abtastverfahren genutzt. Die dazu benötigte Spule einschließlich der Vorrichtung zum Besprühen und Abkühlen wird über die Werkstückoberfläche geführt, wobei jeweils nur ein kleiner Bereich erhitzt und wieder abgekühlt wird.
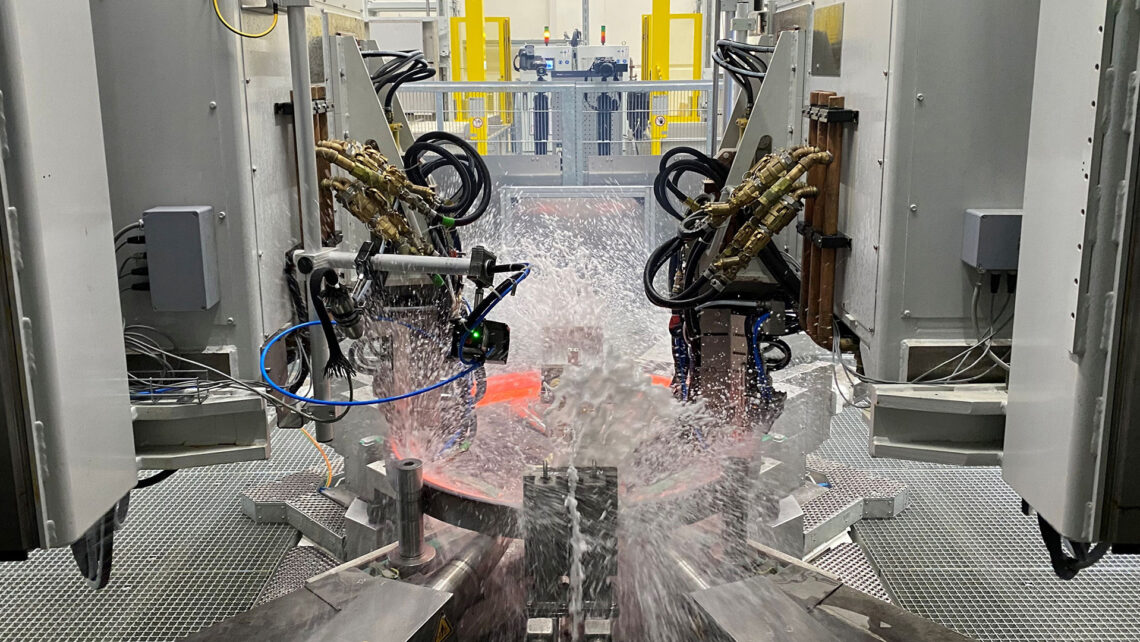
Lücke bald gefüllt
Bis vor kurzem hatte die Toolbox für das Induktionshärten jedoch eine wesentliche Lücke: Lager mittlerer Größe mit Durchmessern von 500 Millimetern bis etwa 1,6 Metern sind zu groß für herkömmliche One-Shot-Induktionshärtungsverfahren, aber zu klein für Scanning-Anlagen.
Unsere Kunden aus dem Bereich der erneuerbaren Energien sind ganz besonders an den Umweltauswirkungen der Produkte, die sie kaufen, interessiert.
Michael Wendel, Leiter Induction Hardening Technicum bei SKF mit Sitz in Schweinfurt
Ein Team im SKF Center for Manufacturing Development in Schweinfurt befasst sich seit 2017 damit, diese Lücke zu füllen. Inzwischen steht das vom Bundeswirtschaftsministerium sowie von Climate Action subventionierte Projekt kurz vor dem Eintritt in die nächste Phase.
Das vom SKF Team entwickelte System mit der Bezeichnung Induflex ermöglicht One-Shot-Oberflächenhärtung von Lagerringen mit einem Durchmesser von 450 bis 1.800 Millimetern. Ein Ring wird auf eine Maschine gespannt und rotiert dann mit hoher Geschwindigkeit an zwei Induktionsspulen vorbei, die jeweils auf einem rechnergesteuerten Führungsarm montiert sind. Der Führungsarm passt kontinuierlich die Position der Spule an und sorgt so für einen exakten Abstand zum Ring, während dieser erhitzt wird und expandiert. Wenn die gewünschte Oberflächentemperatur erreicht ist, wird ein auf den Führungsarm befindliches Sprühsystem aktiviert, um den Werkstoff abzukühlen.
„Verglichen mit konventioneller Oberflächenhärtung in einem Ofen ist das Induflex-Verfahren sauberer, schneller und wesentlich energieeffizienter“, erklärt Wendel. „Das Härten eines 512 Kilogramm schweren Rings mit dem Induflex-System dauert nur wenige Minuten und verbraucht 81 Kilowattstunden – mindestens zwei Größenordnungen weniger als bei der Ofenhärtung.“
Erneuerbare Energiequellen für den Induflex-Prozess
Da die Erwärmung bei Induflex ausschließlich elektrisch erfolgt, können erneuerbare Energien genutzt werden, so dass der CO2-Fußabdruck des Verfahrens gering ist. Mittelgroße Lager werden in vielen Maschinen und Anlagen eingesetzt, aber eine besonders wichtige Wachstumsbranche ist zurzeit die Sparte für erneuerbare Energien. „Windturbinen arbeiten mit Lagern dieser Größenordnung in ihren Rotoren und Getrieben“, verdeutlicht Wendel.
Verglichen mit herkömmlichen Härtungsmethoden bietet das Induktionsverfahren noch weitere Umweltvorteile. Prozessgase oder Chemikalien wie Stickstoff, Erdgas, Methanol oder Ammoniak sind beim Induktionshärten nicht erforderlich. „Das vereinfacht auch die Lieferkette, was angesichts der jüngsten Preisschwankungen und Verfügbarkeitsprobleme bei diesen Stoffen immer wichtiger wird“, erklärt Wendel. Er fügt hinzu, Induktionshärtung könnte zudem die Verwendung von kostengünstigeren, niedriger legierten Lagerstählen mit geringerem CO2-Fußabdruck ermöglichen.
Induflex verspricht Herstellern eine Vereinfachung der Prozesse. Die rechnergestützten Führungsarme zur Steuerung der Induktionsspulen lassen sich auf Knopfdruck neu konfigurieren und so an verschiedene Ringgrößen und -profile anpassen. Dadurch entfällt die Notwendigkeit für eine spezielle Werkzeugausstattung. Fertigungsbetriebe haben die Möglichkeit, kleine Losgrößen herzustellen und nahtlos zwischen verschiedenen Produkten zu wechseln.
Wendel und sein Team haben das Induflex-Verfahren in den letzten vier Jahren weiterentwickelt und die Prototyp-Werkstoffe strengen Tests unterzogen. „Wir haben sehr gute Ergebnisse erzielt“, betont er. „Induflex erzeugt Oberflächen mit ausgezeichneten Eigenschaften, darunter eine verfeinerte Mikrostruktur, Druckeigenspannung und eine hohe Härte. Damit dürfte sich die Widerstandsfähigkeit von Lagerringen gegen Rissbildung und Risswachstum deutlich verbessern.“
Bereit für den Einsatz
Die Arbeit ist inzwischen so weit fortgeschritten, dass komplette Prototyp-Lager gefertigt werden können. Die einzelnen Komponenten werden zu Lagern zusammengesetzt und umfassend geprüft. „Bisher sehen die Ergebnisse der Lagertests äußerst vielversprechend aus“, so Wendel. Die werksinternen Prüfungen werden noch bis Ende 2023 fortgesetzt. Parallel dazu arbeitet SKF mit einer ausgewählten Gruppe von Kunden, um die Eignung der mit Induflex behandelten Lager für deren spezifische Anwendungen nachweisen zu lassen.
Gleichzeitig bemüht sich SKF um eine vollumfängliche Industrialisierung des Prozesses. „Die erste Induflex-Maschine wurde für unsere Entwicklungsarbeit gebaut“, erklärt Wendel. „Sie ist mit zusätzlichen Steuerungsfunktionen und Instrumentierungen ausgestattet, die für eine Produktionsmaschine nicht erforderlich wären. Sie wurde auch nicht für den Einsatz in einem Fertigungsumfeld mit raschen Betriebsabläufen konzipiert.“
Wenn die Entwicklungsarbeit Anfang 2024 abgeschlossen ist, werden Induflex-Maschinen für den industriellen Einsatz ihren Platz in den Werkshallen von SKF Produktionsstätten weltweit finden. „Wir bereiten uns darauf vor, diese Technologie in allen SKF Fabriken einzuführen, die Lager für die Branche der erneuerbaren Energien fertigen“, schließt Wendel.
Verfahren zur Oberflächenhärtung von Lagerringen: vom Nitrieren bis zur selektiven Härtung
Staatliche Subventionen
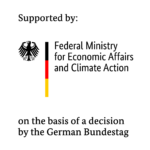