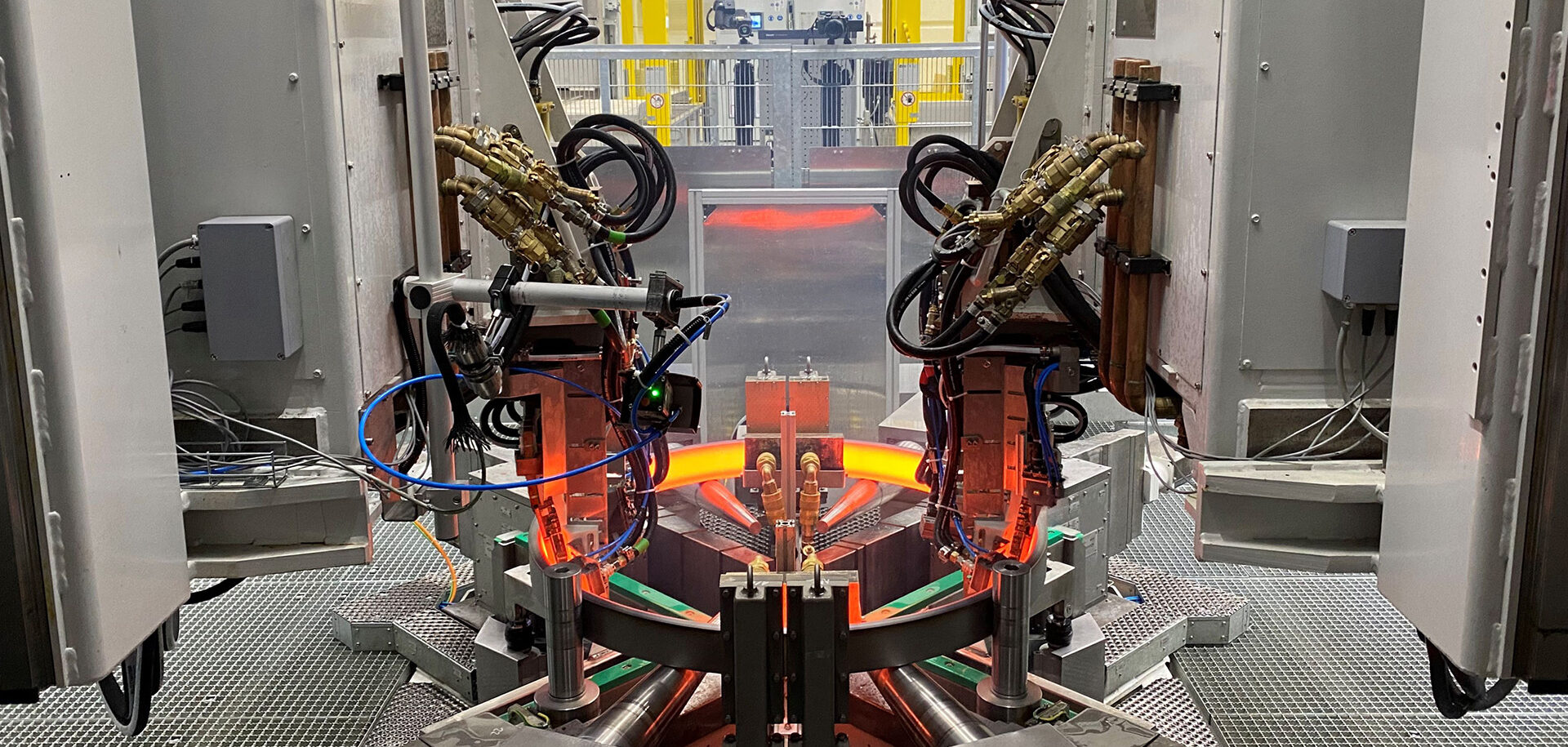
从传统到选择性淬火
快速、节能淬火技术将在工业领域首次亮相
为了实现高性能并延长使用寿命,轴承套圈材料必须同时具备两大相互矛盾的特性。一是必须硬度高,以承受滚动体施加的载荷;二是必须有韧性,以免在压力下出现开裂。为了解决这一棘手的问题,制造商使用相对柔软的材料制造套圈,然后对其进行处理,使其成为坚硬、耐磨的部件,从而在硬度和韧性这两种相互矛盾的特性之间取得平衡。
实施这一工艺可以采用多种方式,但几乎每一种方法都需要耗费大量热量。传统上,淬火在专门的加热炉中进行,但这可能使该过程变得缓慢,耗能极高,而且还会造成污染。对于轴承制造商及其客户来说,这些都是不可取的,因为他们都希望自己的制造过程快速灵活,具有成本效益,同时尽可能减少碳排放。
环境影响至关重要
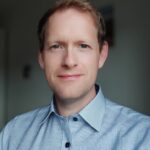
位于德国施魏因富特的SKF感应淬火技术部经理迈克尔·温德尔表示:“我们在可再生能源行业的客户特别关心他们所购买产品对环境的影响,因为他们正在努力避免自己的供应链产生碳排放。”
感应淬火是加热炉的一种替代方案。它使用强大的交变磁场在轴承套圈表面产生热量。感应淬火快速且节能,因为它可以缩短加工时间,实现局部加热,并且在停留期间不消耗能量。该工艺可即时调整,使制造商能够精确控制表面硬化层深度。
感应淬火已广泛应用于轴承生产。直径不超过500毫米的小型轴承套圈使用环形感应线圈加热整个套圈表面,一次性完成淬火工作。对于直径达数米的大型轴承套圈,制造商则采用扫描技术,使用贯穿部件表面的线圈和喷雾淬火系统,每次加热或冷却一小块区域。
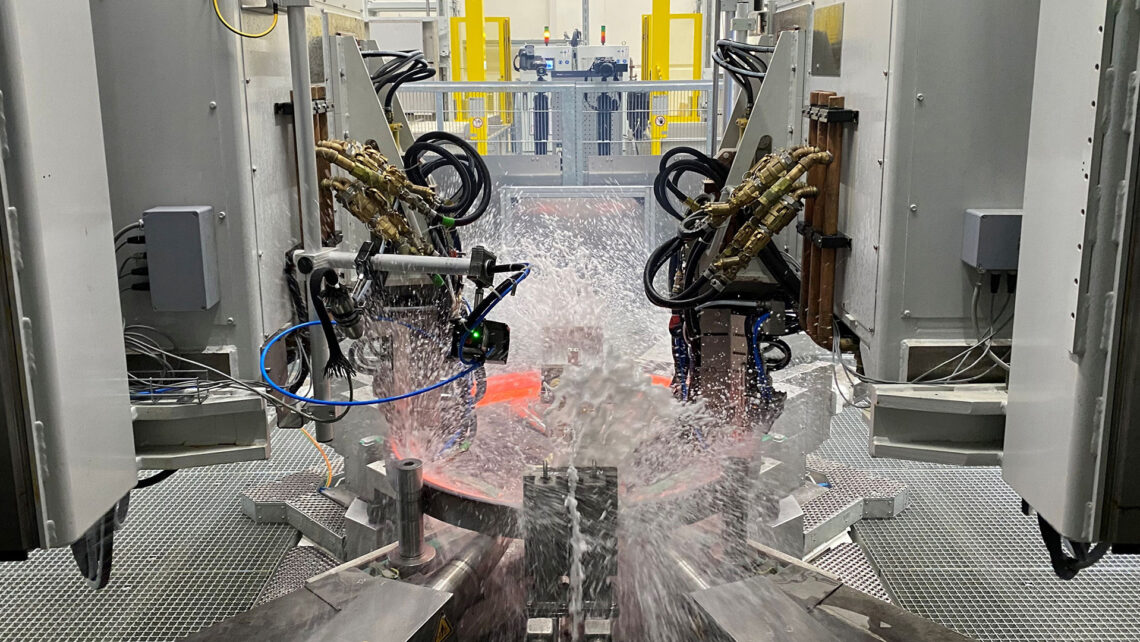
填补空白
然而,直到最近,轴承制造商的感应淬火工艺中仍存在重大空白。直径为500毫米至1.6米左右的中型轴承对于传统的一次性感应淬火技术来说太大了,但对于扫描技术来说又太小了。
自2017年以来,SKF德国施魏因富特的制造发展中心的一个团队一直在寻找填补这一空白的方法。在德国联邦经济事务和气候行动部的资助下,他们的项目已经完成,现在正准备进入下一阶段。
我们在可再生能源行业的客户特别关心他们所购买产品对环境的影响。
迈克尔·温德尔, 位于德国施魏因富特的SKF感应淬火技术部(制造开发)经理
SKF团队研发的系统被称为Induflex,旨在对直径为450毫米至1800毫米的轴承套圈进行一次性表面淬火。套圈被夹在机器上,在快速旋转状态下经过两个感应线圈。两个感应线圈均安装在由计算机控制的传动臂上,传动臂可以不断调整线圈的位置,在套圈受热膨胀时与其保持精确的距离。当套圈表面达到所需温度时,传动臂上的喷淋系统就会启动,对材料进行淬火。
温德尔指出:“与传统的炉内淬火工艺相比,Induflex工艺更清洁、更快速、更节能。使用Induflex系统对一个重512公斤的套圈进行淬火只需几分钟,能耗仅为81千瓦时,比表面渗碳(加热炉处理工艺)至少低两个数量级。”
可再生能源供电
由于Induflex仅使用电加热,因此该工艺可以由可再生能源供电,从而降低碳排放。中型轴承广泛应用于各种工业设备中,当前的主要增长点是可再生能源领域。“风电的转子和齿轮箱都使用这种尺寸的轴承,” 温德尔补充道。
与传统的淬火技术相比,感应淬火还具有其他环保优势——比如,不需要使用氮气、天然气、甲醇或氨等工艺气体或化学品。温德尔说:“这也简化了供应链。最近,这些介质的价格出现了波动,而且货源紧缺,供应链因此成为日益重要的考量因素。”他补充道,感应淬火还可以使用二氧化碳排放更低、成本效益更高的低合金轴承钢。
Induflex承诺为制造商提供更简便的工艺流程。只需按下按钮,就能重新设置控制感应线圈的计算机传动臂,以适用于不同尺寸和外观的轴承套圈。这样,工厂无需专用工具,就可以实现小批量生产,在产品之间无缝切换。
四年来,温德尔和他的团队一直在改进Induflex工艺,并对样品材料进行严格测试。“我们已经取得了重大成果,”他说,“采用该工艺处理的套圈表面具有优异的特性,如微观结构精细、具有残余压应力以及硬度高等。这将赋予轴承套圈更出色的耐用性,防止裂纹萌生和裂纹扩展。”
准备就绪
现在,这项工作已经进入完整轴承原型的生产。这些零部件正在组装成轴承并进行大量的测试。温德尔介绍说:“到目前为止,轴承测试结果非常乐观。”2023年,内部测试将继续进行,SKF还将与部分客户合作,以确认经Induflex工艺处理的轴承是否适用于其应用。
与此同时,该工艺的全面批量化工作正在进行中。“第一台Induflex机器是为开发工作而建造的,” 温德尔解释道,“它带有在生产型机器上所不需要的额外控制和仪器,其设计目的也不是为了集成到快速移动的工厂环境。”
开发工作将于2024年初完成。届时,完全批量化的Induflex机器将在世界各地的SKF生产基地车间中占有一席之地。温德尔说:“我们正准备在为可再生能源行业生产轴承的SKF工厂中全面推广该项技术。”
轴承套圈表面处理技术:从氮化到选择性淬火
获得德国政府支持
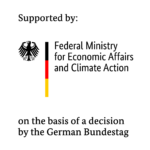