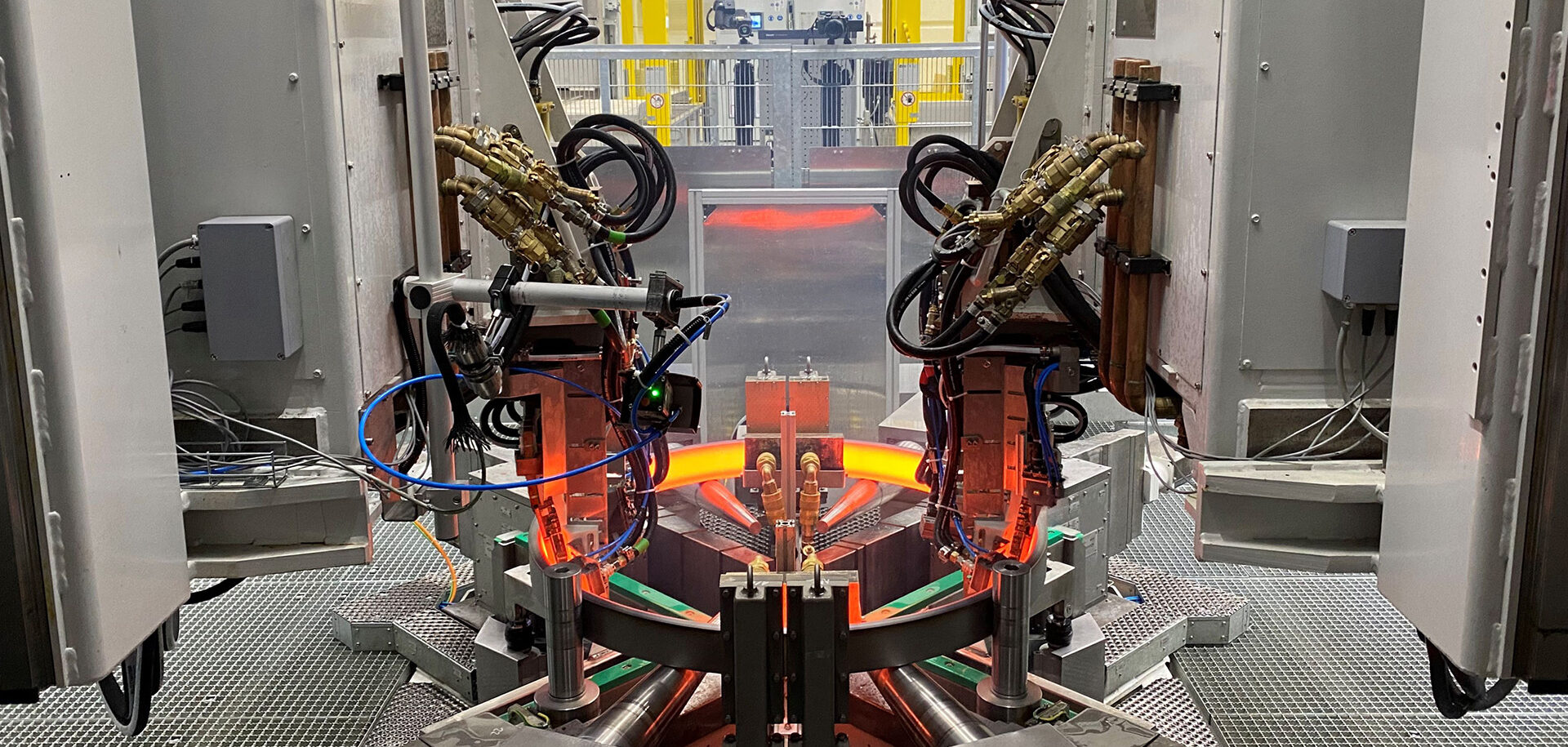
Temple selectivo frente al tradicional
Una tecnología de temple rápida y de elevada eficiencia energética se prepara para su debut industrial.
Para asegurar un alto rendimiento y una larga vida útil, los materiales que componen los aros de los rodamientos deben cumplir objetivos aparentemente contradictorios. Deben ser duros para resistir las cargas impuestas por los elementos rodantes, pero, a la vez, deben ser resistentes, para que no se agrieten bajo presión. Para conseguir ese difícil equilibrio, los aros se fabrican con un material relativamente blando y, posteriormente, son tratados para crear un componente duro y resistente al desgaste, equilibrando las propiedades opuestas de dureza y resistencia.
Este proceso puede llevarse a cabo de varias maneras, pero casi todos los métodos exigen la aplicación de calor significativo. Tradicionalmente, el temple se realiza en un horno especializado. Sin embargo, los procesos pueden ser lentos, sucios y consumir mucha energía, características poco deseables en un mundo en el que los fabricantes de rodamientos –y sus clientes– buscan una producción rápida, flexible, rentable y con la mínima cantidad de emisiones de carbono.
El impacto ambiental es importante
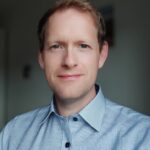
“A nuestros clientes del sector de las energías renovables les interesa, especialmente, el impacto ambiental de los productos que compran, ya que quieren descarbonizar sus propias cadenas de suministro”, afirma Michael Wendel, gerente de Induction Hardening Technicum en SKF, con base en Schweinfurt, Alemania.
Una alternativa al horno es el temple por inducción. Esta técnica utiliza un potente campo magnético alterno para generar calor en la superficie del aro. El temple por inducción es rápido y energéticamente eficiente; los tiempos de proceso son cortos, el calentamiento producido es localizado y no consume energía durante los períodos de espera. Y al ser regulable al instante, el proceso permite a los fabricantes lograr un control preciso de la profundidad de la capa superficial dura.
El temple por inducción ha sido adoptado ampliamente en la producción de rodamientos. Los aros pequeños, hasta unos 500 milímetros de diámetro, se templan en un solo paso, utilizando una bobina de inducción envolvente para calentar simultáneamente toda la superficie del aro. En el caso de los aros más grandes, con diámetros de varios metros, los fabricantes utilizan una técnica de escaneo. Se trata de un sistema con bobina de inducción y temple por aspersión que recorre la superficie de la pieza, calentando y enfriándola por segmentos.
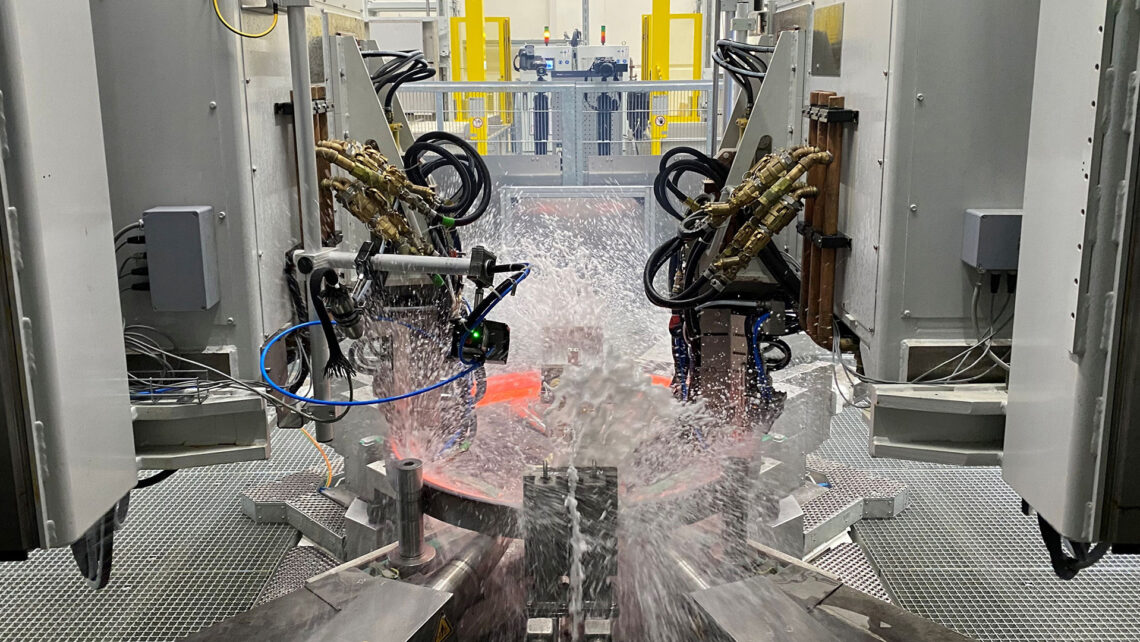
Cubrir los tamaños medios
Sin embargo, hasta hace poco, en la caja de herramientas que los fabricantes de rodamientos tienen a su disposición para el temple por inducción, faltaba algo importante. Los rodamientos de tamaño medio, con diámetros comprendidos entre 500 milímetros y 1,6 metros, son demasiado grandes para la tecnología convencional de temple por inducción en una sola operación y demasiado pequeños para el escaneo.
A nuestros clientes del sector de las energías renovables les interesa, especialmente, el impacto ambiental de los productos que compran
Michael Wendel, gerente de Induction Hardening Technicum en SKF, con base en Schweinfurt, Alemania.
Desde 2017, un equipo del Centro de Desarrollo de Fabricación de SKF en Schweinfurt ha estado buscando una solución. Ahora, su proyecto, gracias al apoyo financiero recibido del Ministerio Federal de Economía y Protección del Clima de Alemania, está listo para pasar a la fase siguiente.
El sistema de SKF, conocido como Induflex, está diseñado para permitir el temple en una sola operación de aros de rodamientos con diámetros comprendidos entre 450 y 1800 milímetros. El aro se sujeta a una máquina y se hace girar rápidamente entre dos bobinas de inducción, cada una de ellas montada en un brazo actuador controlado por computadora. El brazo regula continuamente la posición de la bobina, manteniendo una distancia precisa respecto del aro a medida que este se calienta y se dilata. Cuando la superficie alcanza la temperatura deseada, se activa un sistema de rociado en los brazos para enfriar el material.
“Comparado con el temple convencional en un horno, el proceso Induflex es más limpio, más rápido y ofrece una eficiencia energética muy superior”, afirma Wendel. “Un aro de 512 kg se templa en el sistema Induflex en pocos minutos y consume 81 kWh de energía, es decir, al menos dos órdenes de magnitud menos que el temple por cementación [tratamiento en el horno]”.
Energía de fuentes renovables
Y, como Induflex solo utiliza calefacción eléctrica, el proceso puede alimentarse con fuentes renovables para mantener una huella de carbono baja. Los rodamientos de tamaño medio se utilizan en un amplio espectro de máquinas industriales, pero están experimentando un crecimiento importante en el sector de las energías renovables. “Las turbinas eólicas utilizan rodamientos de este tamaño en sus rotores y cajas de engranajes”, explica Wendel.
El método de inducción ofrece beneficios ambientales adicionales frente a las tecnologías de temple convencionales. No requiere gases ni productos químicos de proceso, como nitrógeno, gas natural, metanol o amoníaco. “También simplifica la cadena de suministro, un factor de importancia creciente dada la reciente volatilidad de los precios y los problemas de disponibilidad de estos medios”, afirma Wendel. El temple por inducción también podría permitir el uso de aceros de menor aleación y más rentables para los rodamientos, con una huella de CO2 más baja, añade.
Induflex promete simplificar los procesos para los fabricantes. Los brazos controlados por computadora que manejan las bobinas de inducción pueden reconfigurarse con solo pulsar un botón para trabajar con aros de distintos tamaños y perfiles. De este modo, se elimina la necesidad de herramientas especializadas y permite a las fábricas producir lotes pequeños, pasando fluidamente de un producto a otro.
Desde hace cuatro años, Wendel y su equipo han estado perfeccionando el proceso Induflex y sometiendo los materiales de los prototipos a pruebas rigurosas. “Los resultados han sido muy buenos”, afirma. “El proceso produce superficies con propiedades excelentes, que incluyen una microestructura refinada, tensión residual de compresión y una dureza elevada. Con ello, los aros son más robustos frente a la iniciación y crecimiento de fisuras”.
Listos para trabajar
Actualmente, se ha pasado a la producción de prototipos completos de rodamientos. Estas piezas se ensamblan en rodamientos y se someten a pruebas exhaustivas. “Hasta ahora, los resultados son muy prometedores”, afirma Wendel, y agrega que las pruebas internas continuarán durante 2023. SKF también está trabajando con un grupo selecto de clientes para confirmar la idoneidad de los rodamientos tratados con Induflex para sus aplicaciones.
Mientras tanto, el equipo está volcado en la industrialización íntegra del proceso. “La primera máquina Induflex se construyó en el marco de su desarrollo”, explica Wendel. “Cuenta con controles e instrumentos adicionales que no serían necesarios en una máquina de producción; tampoco fue diseñada para integrarse en un entorno de fabricación, donde prima la agilidad”.
Cuando finalice el trabajo de desarrollo a principios de 2024, las máquinas Induflex totalmente industrializadas se instalarán en centros de producción de SKF de todo el mundo. “Estamos preparando una implementación global de esta tecnología en todas las fábricas que producen rodamientos para el sector de las energías renovables”, concluye Wendel.
Técnicas de tratamiento de superficies para los aros: desde la nitruración hasta el temple selectivo
Respaldado por el gobierno federal
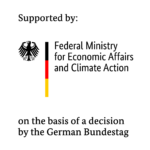