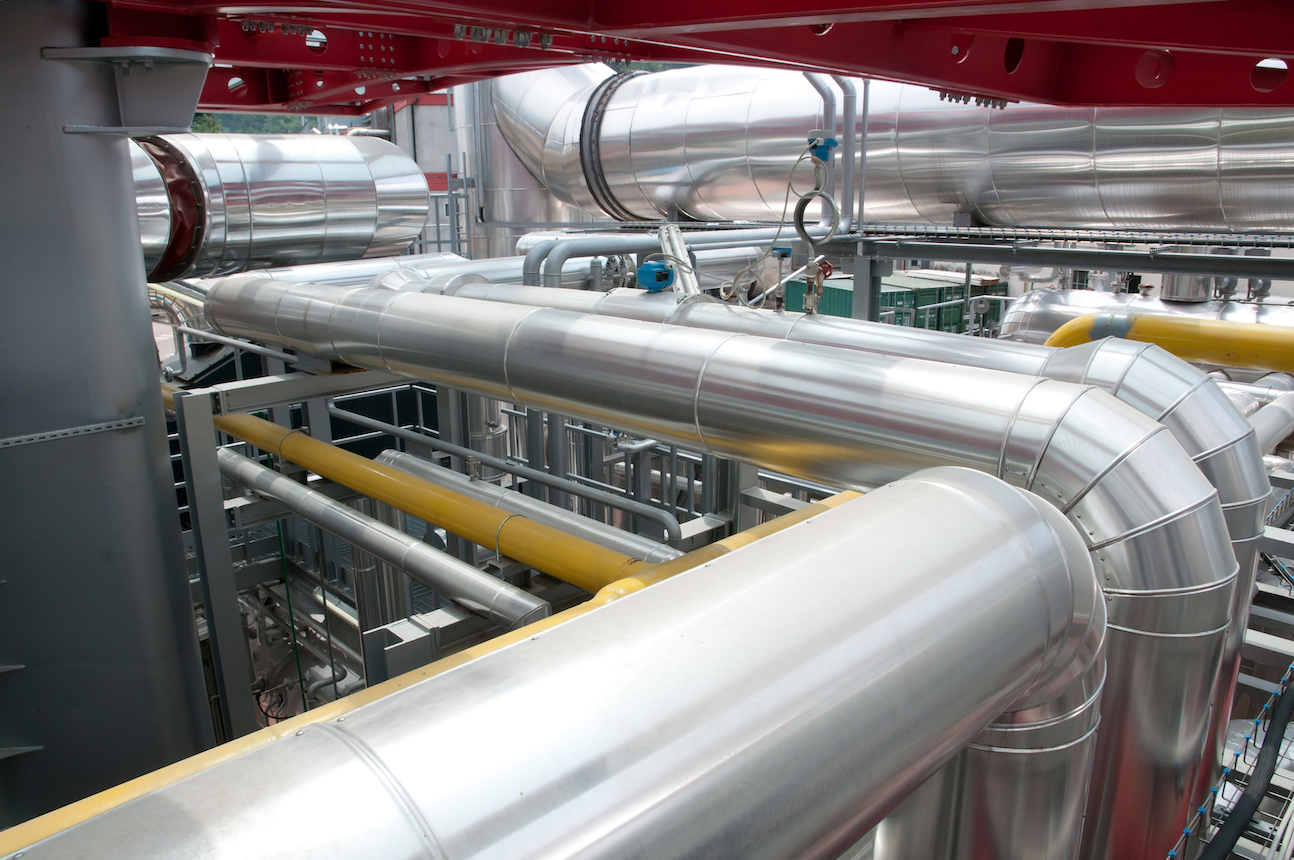
Una collaborazione di valore
SKF fornisce ad Arinox un servizio integrato di ricondizionamento dei cuscinetti dei laminatoi.
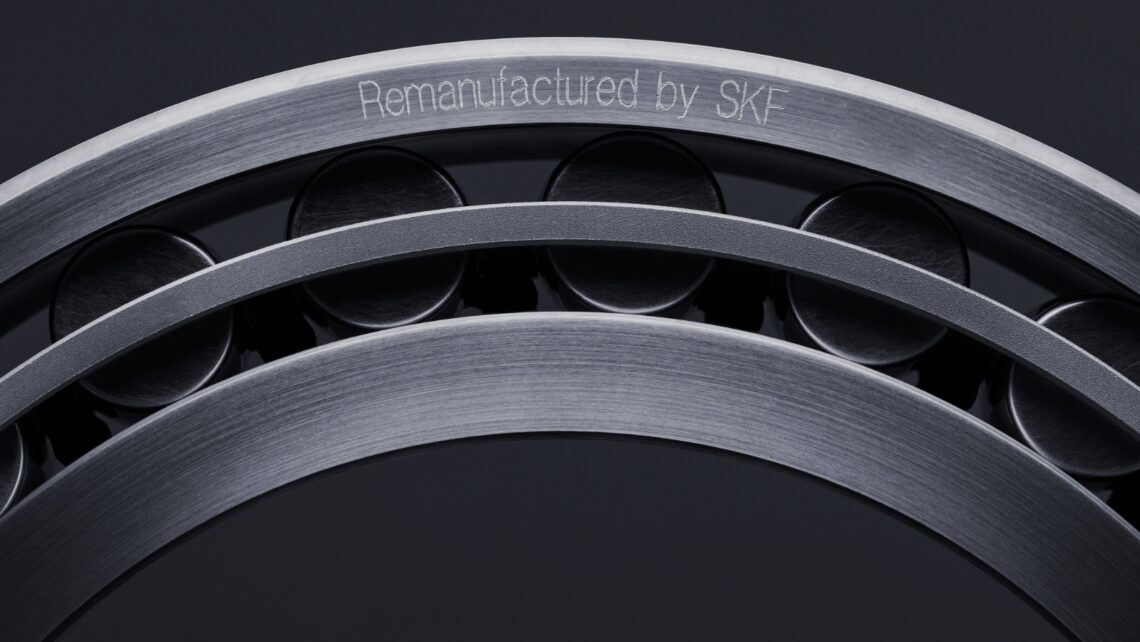
SKF collabora con Arinox fornendo servizi e soluzioni di ricondizionamento dei cuscinetti. Ne parliamo con Mauro Moretti, Direttore Tecnico di Arinox.
Quando è iniziata la collaborazione con SKF?
Lavoriamo con SKF da sempre, da quando l’azienda è stata fondata nel 1990.
Quali sono i prodotti e le soluzioni SKF che utilizzate?
Fin dall’inizio ci siamo rivolti a SKF per il ricondizionamento dei cuscinetti. A partire dal 2005 la collaborazione si è ulteriormente consolidata grazie all’ampliamento dello stabilimento, con la ristrutturazione di 250 metri quadri di capannoni già esistenti, e all’integrazione di nuovi laminatoi.
Siamo passati da 15.000 a 55.000 tonnellate di acciaio inossidabile prodotte all’anno.
Noi siamo specializzati in acciaio extra sottile, sotto il millimetro di spessore.
Abbiamo tre laminatoi Sendzimir a 20 rulli. Ogni laminatoio monta circa 80 cuscinetti, che hanno caratteristiche di geometria e installazione molto specifiche, serve la massima precisione. L’anello interno è fisso, ruota la parte esterna del cuscinetto. Gli alberi sono dotati di fori per la lubrificazione per il cuscinetto. Il processo di lubrificazione prevede l’utilizzo di grandi portate di olio a bassa viscosità.
Oltre al ricondizionamento, SKF ha realizzato per noi un sistema di raccolta dati basato su software dove per ogni cuscinetto – stiamo parlando di circa 900 cuscinetti – è presente un identificativo. Questo ci permette di sapere, per ogni cuscinetto, il diametro, tutte le caratteristiche di misura e la vita operativa. Sono dati molto importanti per noi.
Quali sono i vantaggi del ricondizionamento?
Il ricondizionamento ci permette di avere a disposizione un componente perfetto e rettificato a un costo notevolmente inferiore al nuovo.
I rulli all’interno delle gabbie hanno geometrie diverse, quindi bisogna effettuare un importante calcolo della gabbia per il dimensionamento dei cuscinetti e dei parametri operativi. In questa prospettiva, ricondizionare significa mantenere i cuscinetti in vita per diversi anni.
Inoltre, grazie al database realizzato da SKF abbiamo sempre sotto mano le caratteristiche, la vita e lo stato di salute di ogni singolo cuscinetto.
Ricorrere al ricondizionamento ci ha permesso di ottimizzare la durata dei componenti, generando quindi un grande risultato anche in termini di riduzione del carbon footprint.
Qual è il valore aggiunto che SKF offre ai clienti?
A SKF riconosciamo l’attenzione nei nostri confronti, il team è sempre presente e disponibile, questo permette un interscambio tecnico costante e continuativo.
Quali sono oggi le caratteristiche e i trend dell’industria siderurgica?
Un trend molto importante è la riduzione dell’impatto ambientale. Per quanto riguarda il gruppo Arvedi, di cui Arinox è parte integrante, la sostenibilità è un valore fondamentale. Questo si traduce nella riduzione costante delle emissioni di CO2 e nella produzione di energia da fonti rinnovabili.
Lo definirei un impegno quotidiano, che riguarda oggi tutti gli stabilimenti del gruppo, compreso il nostro.
Quali sono le attività messe in campo da Arinox per la diminuzione dell’impatto ambientale?
Sono numerose le iniziative che abbiamo realizzato e stiamo realizzando per ridurre l’impatto ambientale. L’area industriale dove si trova il nostro stabilimento ospitava fino agli anni ’80 la Fabbrica Italiana Tubi (FIT), che all’epoca era un’azienda altamente inquinante. Abbiamo fatto un importante lavoro di bonifica e riconversione.
Il nostro è un lavoro di ottimizzazione continua su tutta la catena, siamo un’azienda certificata ISO 50001.
Per quanto riguarda le iniziative in corso, abbiamo installato un impianto fotovoltaico da 3 megawatt che entrerà in funzione a breve.
La riduzione dell’impatto ambientale riguarda tutte le fonti energetiche, dall’elettricità all’idrogeno fino al gas e al metano.
Abbiamo in cantiere un progetto per produrre idrogeno, dal 2023 entrerà in attività e saremo in grado di produrre 300 metri cubi di idrogeno all’ora. Non sarà idrogeno “green”, ma ci permetterà in ogni caso di ridurre le emissioni di CO2.
La nostra è un’industria che consuma molte materie prime, come l’acqua. Per questo lavoriamo con interventi mirati per ottimizzare costantemente l’utilizzo delle risorse. Oltre all’acqua, per esempio, abbiamo progetti mirati per l’efficienza dell’aria compressa, dei sistemi di aspirazione dei fumi dei laminatoi, della manutenzione degli impianti elettrici. Abbiamo sostituito quasi tutte le lampade del capannone con lampade a led.
Abbiamo inoltre installato un software che ci permette di verificare l’equivalente di tonnellate di CO2 risparmiate grazie alle attività in corso.
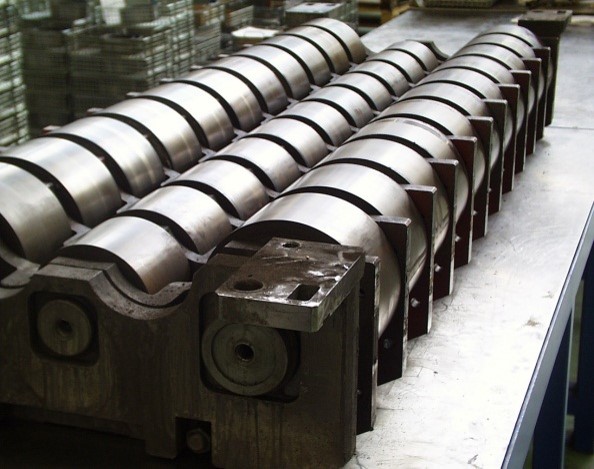