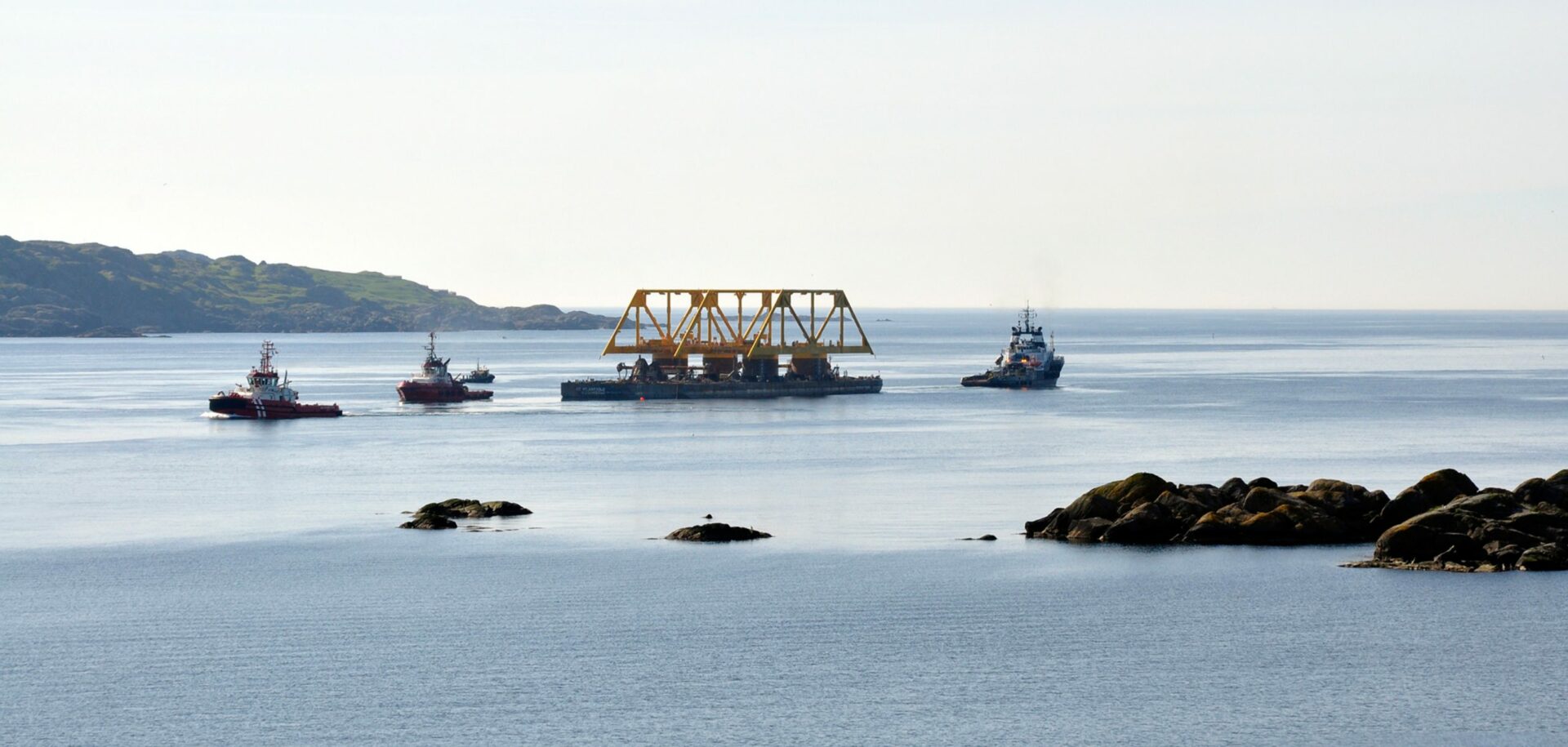
Инновационное решение
Первые в мире подводные газокомпрессорные станции позволяют компании Statoil увеличить газоотдачу пласта, а также сократить расходы и минимизировать негативное воздействие на окружающую среду.
ФАКТЫ
Работа на глубине 300 м
Международная энергетическая компания Statoil запустила первую в мире подводную газокомпрессорную станцию на месторождении Асгард в сентябре 2015 г. Сейчас в эксплуатации находится вторая технологическая нитка в этом же районе Норвежского моря. Эта уникальная технология обеспечивает добычу дополнительных объёмов газа с пластов Мидгард и Миккель этого месторождения, продлевая срок эксплуатации месторождений и повышая газоотдачу.
Statoil
Штаб-квартира в г. Ставангер, Норвегия
Работает в более чем 30 странах мира
22 000 сотрудников по всему миру
Основная деятельность ведётся на континентальном шельфе Норвегии
Зарегистрирована на фондовых биржах Нью-Йорка и Осло
www.statoil.com
Добыча нефти и газа из подошвы пластов-коллекторов была непреодолимой задачей для нефтегазовой отрасли. При излишней сложности добычи компании обычно переключались на другие месторождения. Теперь благодаря новой подводной газокомпрессорной системе Statoil появилась возможность экономичной добычи глубоководной нефти и газа.
Два новых подводных газовых компрессора норвежской энергетической компании – первые представители этого класса оборудования в мире. Компрессоры находятся на месторождении Асгард компании Statoil на глубине 300 м, увеличивая газоотдачу, и в перспективе значительно продлят срок эксплуатации месторождений Мидгард и Миккель.
Мы выбрали SKF, потому что это единственная компания на рынке с такой качественной продукцией.
Торстейн Винтерстё, директор проекта Statoil по месторождению Асгард.
Как ожидается, газоотдача двух пластов-коллекторов в Норвежском море вырастет как минимум на 20 %, что увеличит добычу на месторождении более чем на 300 млн баррелей условного топлива. Без этого нового решения пласты-коллекторы были бы выведены из эксплуатации раньше времени.
Обычно компрессия газа производилась на платформах или на берегу, вдали от месторождения. Размещение компрессора как можно ближе к скважине является энергосберегающей альтернативой. Так экономится место, снижается потребность в техобслуживании, а управлять компрессором можно удалённо, что избавляет от необходимости постоянного надзора и присутствия персонала.
Более того, существенно снижается негативное воздействие на окружающую среду. Подводный компрессор потребляет примерно на 40 % меньше энергии, чем обычные установки, таким образом на месторождении существенно сокращаются выбросы СО2.
«Благодаря новому решению компрессорное оборудование водонепроницаемо – оно располагается в герметичных капсулах, что обеспечивает значительно более надёжную защиту окружающей среды, чем ранее, – утверждает Торстейн Винтерстё, директор проекта Statoil по месторождению Асгард. – На берегу или на платформе оборудование подвержено воздействию осадков, пыли, влажности и колебаний температуры, а дно моря является более стабильной средой – там постоянно +4 оC».
Были приложены значительные усилия, чтобы уложиться в сжатые сроки при ограниченном бюджете, а SKF поддержала нас и сделала всё возможное, работая на результат.
Торстейн Винтерстё, директор проекта Statoil по месторождению Асгард.
Проект по созданию подводной газокомпрессорной станции на месторождении Асгард длился 10 лет, для его выполнения потребовалось, по оценкам, 11 млн человеко-часов. Однако Statoil, по словам Винтерстё, была нацелена на долгосрочные инвестиции. «Использование передовых технологий с целью обеспечения рентабельности и защиты окружающей среды важно для Statoil и наших партнёров, – говорит он. – Мы понимали, что требуется кардинально новый подход к технологиям, и сделали всё возможное для сокращения расходов и снижения выбросов СО2».
По словам Винтерстё, создание подводной системы могло бы не увенчаться успехом без вклада таких поставщиков, как SKF. «Мы выбрали SKF, потому что это единственная компания на рынке с такой качественной продукцией».
Технические специалисты SKF и Statoil тесно сотрудничали в ходе работ над сложной технологией магнитных подшипников, встроенных в корпус компрессора (см. «Факты»). SKF предложила идеи и способы обеспечения требуемого качества.
Обеспечение соответствия технологии множеству требований было длительным процессом, и перед SKF стояла невероятно сложная задача, считает Винтерстё. «Я твёрдо уверен, что SKF проявила мужество, продолжив сотрудничество с нами, – отмечает он. — Были приложены значительные усилия, чтобы уложиться в сжатые сроки при ограниченном бюджете, а SKF поддержала нас и сделала всё возможное, работая на результат».
Теперь, по мнению Винтерстё, пришло время получать преимущества подводной технологии, делиться ей с другими и использовать её на новых объектах.
Магнитные подшипники с длительным ресурсом
Когда Statoil решила построить первую в мире подводную газокомпрессорную станцию, она обратилась к различным поставщикам за технологической поддержкой. SKF была одной из таких компаний.
После пяти лет интенсивных разработок и испытаний, включая моделирование морских подводных условий в течение 6000 часов непрерывной эксплуатации, магнитный подшипник SKF был, наконец, готов к работе на дне Норвежского моря.
Магнитные подшипники встроены в корпус компрессора, благодаря чему не требуется смазочное масло, уплотнения и редуктор. Такие подшипники работают без трения и с более высокими частотами вращения, что позволяет уменьшить размеры компрессорных блоков и упростить инфраструктуру. «Благодаря проекту Statoil мы многому научились и продвинулись в разработке технологий, обеспечив себе конкурентные преимущества», – отмечает Жереми Лепелли, руководитель отдела продаж, Отдел подводных и нефтегазовых разработок подразделения магнитной мехатроники SKF.