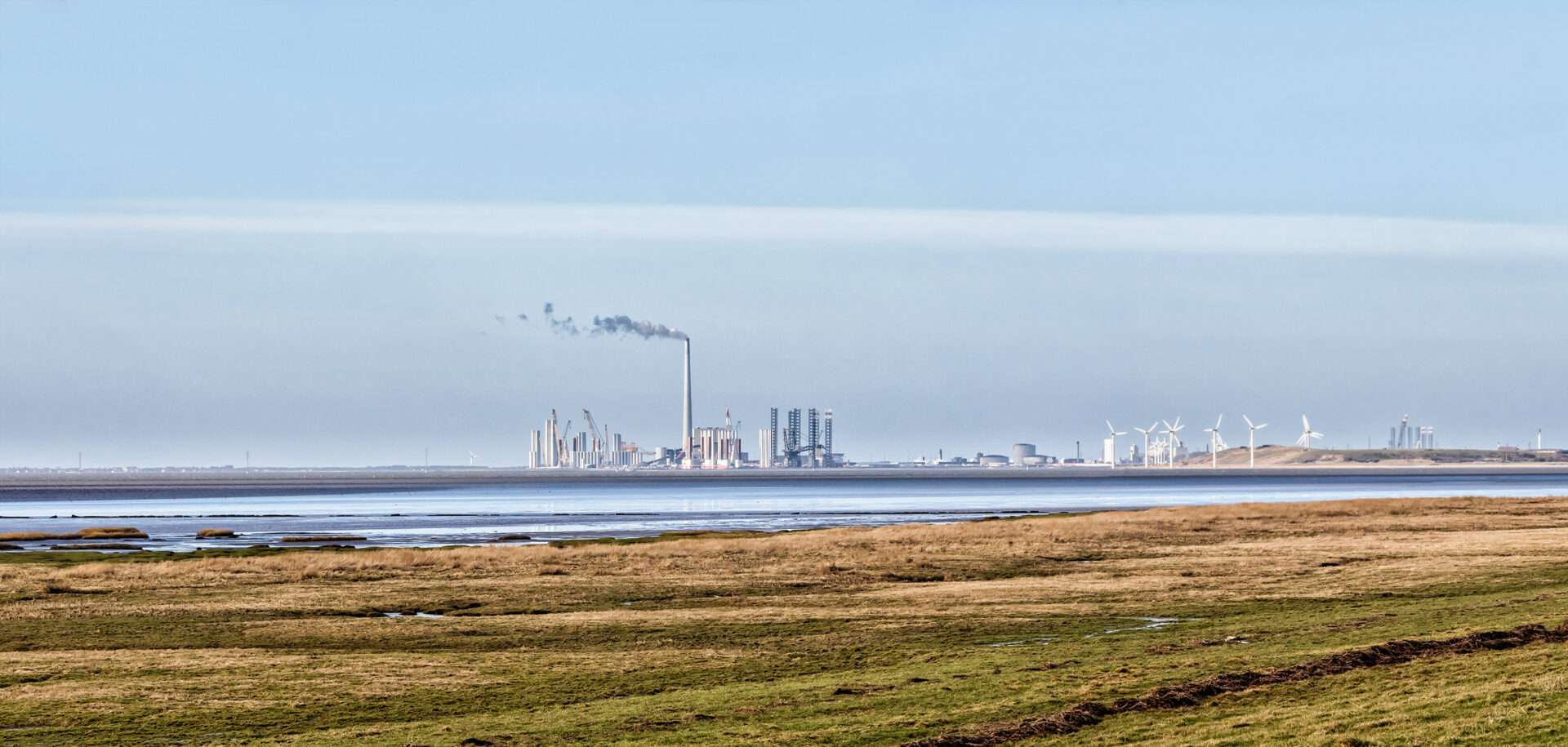
The winds of Danes
For years the Danish port of Esbjerg was known for its ferry connections to England and as an export hub for traditional agricultural exports such as bacon and butter. North Sea oil and fishing were important industries. Today, the wind industry has taken over with a gale force, transforming the port into a centre for activity surrounding sustainable energy.
In addition to being one of Denmark’s largest ports, Esbjerg, situated on the west coast of Jutland, is the undisputed wind capital of Europe.
Strewn around the port are racks of 15-tonne turbine blades, 400-tonne house-sized nacelles and sections of the steel towers that are increasingly dotting landscapes in the hunt for sustainable energy. These locally produced turbine innards are destined both for export throughout the world and for use locally in new offshore wind parks in the North Sea. Hence the fleets of supply, service and 1,500-tonne crane ships in the port.
Roundabouts on the local roads have been cleared in the middle to allow straight passage for the trucks carrying blades 80-metres-long that make their way from nearby factories to the port.
“Nowhere else is the dramatic transition to sustainable energy production as palpable as it is in Esbjerg,” says Lars Buhrkall, manager of Vattenfall’s onshore wind park operations in Esbjerg. “The Danish government wants 50 percent of Denmark’s energy consumption to come from renewable energy sources within a few years, compared with 42 percent today. This is big business.”
Vattenfall, or “Waterfall”, is a household name across Scandinavia. The company is owned by the Swedish state and dates back to the days of damming big Swedish rivers for energy. Today, Vattenfall is one of Europe’s largest producers and retailers of electricity and heat, with sales of some 13.3 billion euros in 2017 and 20,000 employees. It operates more than 1,300 wind turbines (a total capacity of 2,200 MW) across Germany, the Netherlands, the UK, Denmark, Sweden and Finland. A stated company goal is to work towards a fossil-fuel-free world.
“This is also a growing business for SKF,” says Peter Scheibner, country manager, renewable energy, at SKF Denmark. “Wind turbine manufacturers and utilities such as Vattenfall all want the same thing – trouble-free operations for as long as possible, which is about 25 years or more.”
A new standard of excellence
The SKF 240/710 BC spherical roller bearing being developed for the onshore and offshore wind turbine markets is a new standard of excellence in both bearing performance and precision manufacturing. Amongst the benefits are low speed capability, high thrust capability and an improved internal geometry. In addition, the soft brass has been replaced by a much harder cast iron cage. This important design change has proven to cut down on wear and to solve previous lubrication problems.
SKF has traditionally been an important bearing, lubricant and system supplier for onshore wind turbines, the ones most commonly seen from roadsides. But the real growth area, as evidenced by the flurry of activity in the port of Esbjerg, is in the offshore sector where SKF has a growing presence.
“Bigger turbines, gearboxes, generators and heavier loads place new demands on bearing systems, and this is something we are very experienced with,” says Scheibner. “For this reason, we are collaborating very closely with Vattenfall on a number of key offshore wind projects.”
According to Scheibner, standard catalogue spherical roller bearings used in wind turbine main shafts have a good and proven track record, with some lasting up to 20 years, given proper service intervals. But there are limits.
In collaboration with wind turbine manufacturers, SKF closely analysed the technical features of offshore wind applications and developed a new range of spherical roller bearings specifically for wind applications. One of these new bearings has been in operation in Denmark since February 2016, on an NM 80 land-based turbine at the Tjæreborg Enge wind park situated 10 kilometres south of Esbjerg. SKF and Vattenfall are closely following the performance of this bearing from the SKF monitoring centre and the Vattenfall monitoring centre in Esbjerg. This is the heart of the maintenance operation in Esbjerg. A bank of monitors can, at the click of a mouse, show the running condition of wind parks in detail, down to a single turbine. It is a complex task where early prediction is essential in order to bundle upcoming interventions for main components; crane vessels are expensive.
To keep track of onshore and offshore turbines, Vattenfall in Esbjerg uses SCADA (supervisory control and data acquisition) and CMS (condition monitoring systems), online systems that monitor actual production, wind speed, wind direction, gearbox lubrication, oil temperature and pressure and generator cooling-water temperature and pressure. These data can indicate changes in the running conditions of the components involved and can be used to predict time to failure.
The solution involved a redesign and optimization of the SKF spherical roller bearing internal geometry. A novel design process has been developed in this work that iteratively modifies the internal geometry, simulating the performance of thousands of feasible internal geometries of the bearing to finally find the optimal design for the bearing to better accommodate the application loads. As a consequence, the cage is also redesigned in terms of both of geometry and material, as the brass material was replaced by cast iron. “Cast iron is stiffer and harder than brass,” says Scheibner.
Several internal metal sliding contacts were eliminated to reduce friction and wear. In addition, with the reduced contact pressures, the calculated bearing life was extended by an average of 60 percent. Furthermore, the weight of these new bearings was reduced by 4 percent on average, and the lubrication features were improved.
What ensued was a combination of advanced modelling, simulation studies and field validations.
It’s a win-win where SKF helps us with their resources.
Lars Buhrkall
manager
As is often the case, SKF stepped up its problem-solving resources as an investment in customer relations with Vattenfall. The goal was 100 percent availability throughout the 25-year design life of the turbine.
“If you want long-term improvements you have to participate short-term in the testing of our bearings,” Scheibner says. “This kind of cooperation with Vattenfall is vital for us to run tests and equally important for Vattenfall. We are confident that the new spherical roller bearing will be the main bearing for wind turbine applications.”
Lars Buhrkall, manager of Vattenfall’s onshore wind park operations in Esbjerg, adds, “It’s a win-win where SKF helps us with their resources, and we come as close as possible to trouble-free operation.”