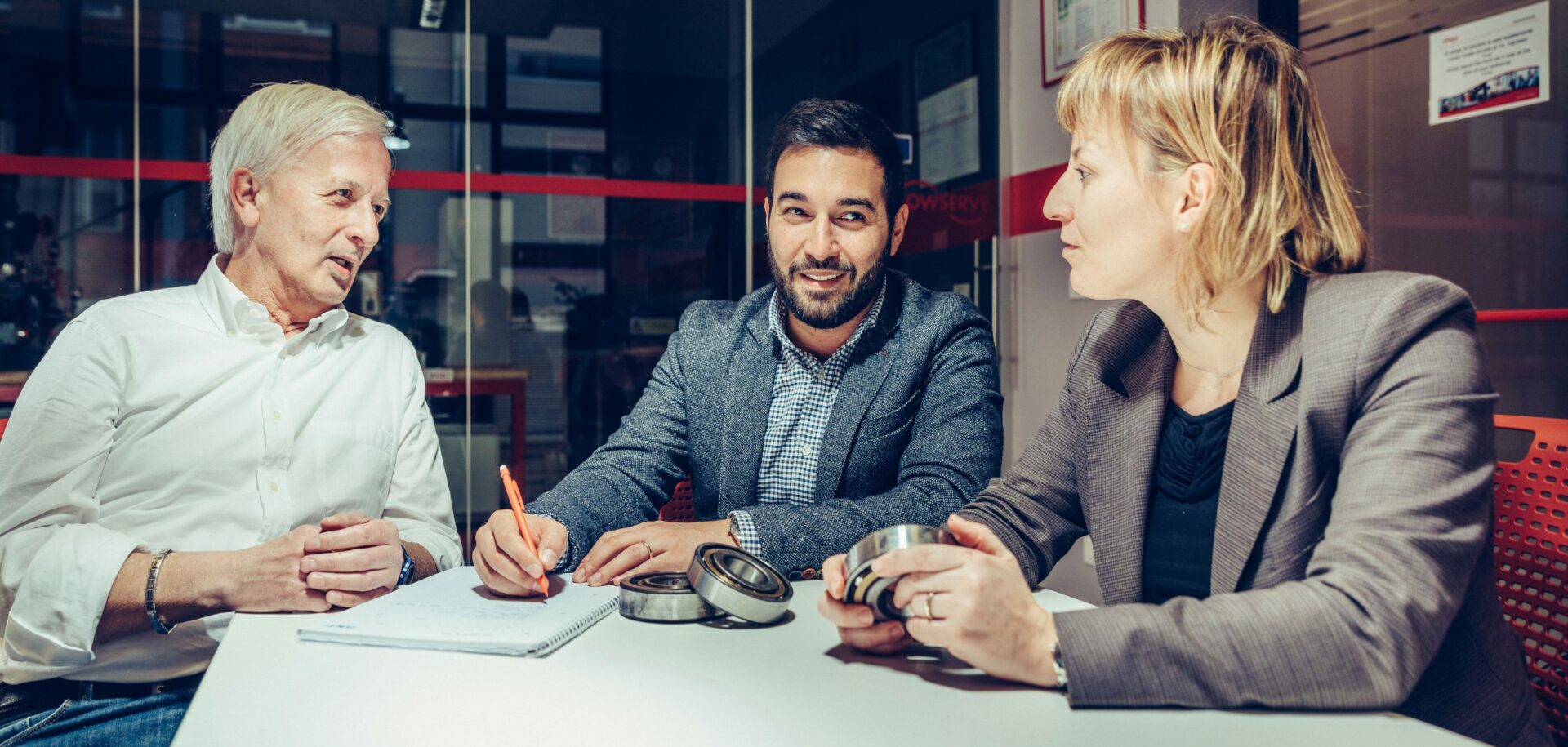
Training to troubleshoot
The oil and gas industry places special demands on pumps in its production and pipeline systems. Reliability and durability are musts, as is the flexibility to deal with difficult fluid movement and control issues.
Ensuring reliability is more than a matter of well-designed equipment and high-quality components. Training is a key factor in good products and good durability. For Flowserve, one of the world’s leading companies in pump production and flow management services, training is an absolute priority.
“We believe strongly in continuous improvement as a lever of success,” says engineer Federico Fella who manages the learning centre in Desio (Milan), Italy, one of Flowserve’s six global training centres.
“Developing our resources is the best way for us to stay competitive.”
The Italian state-of-the-art facility, which was built in 2010, serves employees throughout Europe and flanks the company’s factory for oil and gas pumps. It includes a traditional classroom accommodating up to 20 students and laboratories for both static and dynamic hands-on training.
Some 400 to 500 employees are trained here each year under the direction of Fella. Most trainees take standard courses such as the fundamentals of centrifugal pumps or mechanical seals or pump system analysis.
In addition to these regular offerings, Flowserve also provides customized training courses. These are developed when managers, staff representatives and human resources (HR) personnel agree that a specific need exists for which standard training catalogue courses are not adequate. “For general training, the HR staff and managers make the decision, but for technical courses we ask Federico Fella,” explains Federica Meda, HR representative for the company. “Together we decide what might be needed, and he provides technical input.”
In 2013, the need arose for a course focused on bearings used in Flowserve pumps – specifically, troubleshooting for oil and gas applications. Reliability is paramount, because bearings in these pumps have to withstand excessive heat and vibration levels as well as normal wear and tear. Not only must the correct bearings be selected for the pump application, but they must also be installed properly. Improper installation happens when a technician does not use appropriate tools or lacks sufficient knowledge about the application, lubrication, bearing design, latest bearing developments and exchange rules, etc.
The course, developed jointly by Flowserve and SKF, was designed to address these concerns. Specific attention was paid to assembly, dimension sizing, lubrication and root cause failure analysis. A full section was devoted to actual case studies, the key in troubleshooting. “We would show the participants damaged bearings,” Fella explains. “Divided into groups, the participants were then asked to examine the bearings and present a description of what they thought was the problem and how they proposed to solve it.”
“Photos of damaged bearings are useful, but we want our practitioners to touch and feel the product,” Fella says. When all the presentations were made, the instructor guided the students in a discussion to arrive at the real root cause of the damage.
Courses started in 2013, each with a maximum of 10 participants to ensure that every student had significant time for hands-on experience. Each course lasted two days and most of the participants were field service staff, although a few engineers have also taken the course.
Feedback so far has been excellent, reports HR representative Alessandra Borroni. A test given at the end of the course to evaluate immediate effectiveness was passed by all attendees, with at least 80 percent correct responses to a series of multiple-choice questions. It is still too soon to measure the effectiveness of the training in the field, but, says Meda, “the managers of those who have participated have been very satisfied.”
Hands-on practicality
SKF offers a wide range of courses to customers worldwide – from bearing selection to strategy, reliability to root cause bearing failure analysis. These are deliverable in a variety of formats – at SKF’s own regional centres, on site at client locations or as distance learning options.
SKF’s European training offering on bearings covers general applications, but that was not specific enough to address the needs of Flowserve technicians. So Flowserve and SKF specialists together developed a specific course for pump applications, tailor-made for Flowserve.
The bearings were selected not only from Flowserve pumps but from all oil and gas applications that would be useful for this troubleshooting course. Another customization detail was the inclusion of legal normatives for oil and gas, since that industry was the focus.
The result was a training session superior to a generic course, which could easily be customized to other industrial sectors with applications such as pumps and compressors.