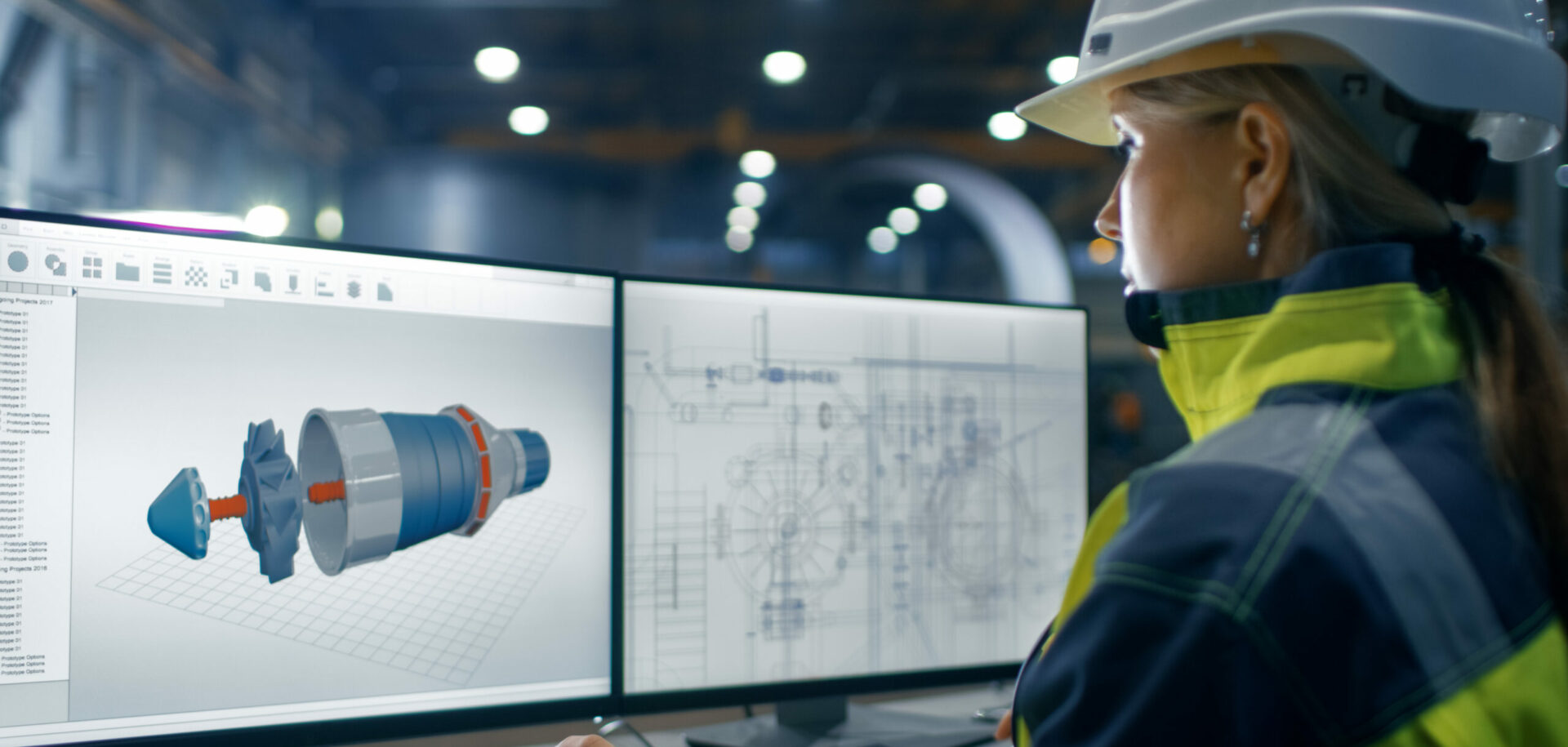
Unifying software for marine propulsion shaft design
ShaftDesigner is an innovative Computer Aided Engineering (CAE) software to support the design, installation, maintenance and repair of marine propulsion shafts. The importance of this new software is that it bridges theory and practice in the field of shaft alignment and mounting. Consequently, it is an extremely useful design tool that helps engineers create optimally functioning shafts.
Summary
Making the complexities of marine propulsion shaft design, installation and repair easier is the aim of new software from Machine Support in the Netherlands. With application potential that spans the life cycle of propulsion shafts, ShaftDesigner can accurately represent all the components of a propulsion train. It has been developed to make shaft engineering and alignment design more precise and easier to perform.
The software has been developed for use in all parts of a ship’s propulsion shaft life cycle. It can accurately represent all the components of a propulsion train so that for each phase, users can reap the benefits of different aspects of the various application modules.
Offered by Machine Support in the Netherlands, it has been developed to make shaft engineering and alignment design more precise and easier to perform. The software has been designed with market needs in mind as a result of close collaboration with classification societies and leading original equipment manufacturers of propulsion train components during its development.
For the first time, designers have access to a single and flexible model that enables all sorts of shaft-related calculations. Plus, it enables the user to analyze different operating conditions, from ballast to laden, cold and warm engine, as well as different states from a simple uncoupled shaft to fully assembled propulsion trains. It avoids previous situations where users had to manage many different data models and files for the many types of calculations and possible operating conditions. It also bridges the gap between software capability and current understanding of propulsion train technology and techniques.
Considerable thought has gone into the user interface, and this is combined with easy 3D modelling features to create a realistic 3D representation of the propulsion train based on the three main techniques of modelling (se bild . 1).
BASE MODEL FOR ALL CALCULATIONS
The software is described as a multi-project, multi-shaft and multi-state 3D CAE system for ship propulsion train calculations. It uses a base model to calculate shaft alignment, whirling vibration, bending (lateral) vibration, axial and torsional vibration.
Being a multi-shaft system, the software can be used for the design of anything from a single shaft line to complete propulsion trains with multiple shaft lines, engines and other components. In addition, each application can hold a number of propulsion train states (se bild 2).
One of the strengths of the ShaftDesigner is that all the calculations are formed from a single base model. Once created, any changes are automatically incorporated across the applications. As the software operates in a 3D graphical environment, these changes can be checked visually, and this minimizes the chance of errors due to human entry (se bild . 6).
THREE MODELLING TECHNIQUES
The software incorporates three modelling approaches. These are:
-
free drag and drop modelling with subsequent object position correction
-
drag and drop modelling using snapping to prior-created object positions
-
group placing by distance from an assigned origin position.
Any modelling error can be easily corrected using an “undo/redo” function or the “history” window.
SHAFT ALIGNMENT CALCULATIONS
The aim of shaft alignment calculations is to determine the location of shaft line bearings during alignment or to optimize the bearing load of shaft lines. This enables safe oper-ation of the vessel’s propulsion train under all specified operating conditions.
The location of the shaft line bearing axis is defined by vertical and horizontal offsets of the bearing bush centre point, and by the angles between the base reference line and the bearing bush axis. Shaft line deflections are calculated automatically when the software is operating (se bild . 3).
The application model is automatically constructed from the base model. Any changes in the base model update the shaft line’s deflections immediately. Shaft alignment techniques supported by ShaftDesigner are direct calculation, offset exploration, geometric alignment, catenary alignment and strain gauge alignment. Thanks to the reverse-engineering capabilities of the software, it is also possible to calculate alignments based on measured bending loads, bearing stress, jack loads, sag & gap and shaft deflections.
The application model can be further developed to meet specific application requirements. The user can add additional objects such as concentrated forces, temporary supports and jacks in order to verify theoretical alignments in practice. Placing additional supports and forces starts an immediate automatic shaft line deflection recalculation.
VIBRATION CALCULATIONS
Five application modules are available for use with the base model covering the various types of vibration, i.e., whirling, bending, axial, torsional and coupled vibration.
The main result of the whirling vibration calculation is the list of critical speeds for forward and backward whirling (se bild . 4). Excitation of a first order corresponds to synchronous whirling. The results are presented in a resonance table and graphically as a Campbell diagram.
For bending, the vibration application calculates free vibration characteristics such as natural frequencies, mode shapes as well as resonance speeds. The results are given in the form of a Campbell diagram and a resonance table.
The axial vibration module includes free vibration as well as forced vibration calculation possibilities. There are many options to set excitation and damping parameters in forced vibration calculations. The results are presented in a resonance table and as a graph showing the vibrations at various rotational speeds.
Torsional vibration calculations are performed from the mass-elastic model created with the graphical editor and also include both free and forced vibrations (se bild . 5). The results are presented as a graph showing the vibrations at various rotational speeds and in a resonance table. For torsional vibration though, it is more efficient to manually enter values instead of relying on the base model, as specific data are required for torsional vibrations. The coupled vibration application calculates the axial-torsional vibration parameters for the installations with directly coupled diesel engines. All these calculations are integrated into a single solution.
Results are presented in detailed, customizable reports as XML documents so they can be easily exported to different formats. Machine Support has used the software in more than 120 projects worldwide. Future development work is hoped to lead to additional software updates, including the ability to import 3D projects and models from third-party 3D CAD programs.
LIFE-CYCLE APPLICATION
As already indicated, ShaftDesigner is a useful application throughout a vessel’s life cycle – be it the design phase, during construction or when maintenance and repair is involved. During the design phase – from an engineering point of view – ShaftDesigner is the design tool of choice to explore offsets, optimizing the propulsion train components’ positions based on user-set acceptance criteria. This functionality, used at an early stage, provides a good bearing load distribution and thus safe shaft line operation and helps avoiding time-consuming and costly (re-) alignment problems later on. At the same time and in the same manner, the various vibration software modules enable the calculation of potential harmful vibrations based on a specific propulsion train layout, which creates the possibility of exploring various layout options and their consequences.
During construction and when there is no model available from the design phase, ship builders can still reap significant benefits from modelling the propulsion train prior to the actual shaft alignment. Exact measurements can be easily entered into the ShaftDesigner software, automatically updating the model every time a new entry is made. The program provides the necessary data for various shaft alignment techniques including jack load, laser alignment and strain gauge alignment, which can be used at various stages of the shaft line’s installation (se bild . 7).
Finally, for maintenance and repair purposes, by calculating the alignment and possible vibrations of the shaft, issues that could influence the state of the shaft line’s components can be identified at an early stage. For instance, bearing stress points can be recognized and checked for wear, avoiding costly vessel downtime in case of failure. Using ShaftDesigner, it is also very easy to assess and evaluate shaft alignment following an incident.
MACHINE SUPPORT
Machine Support is a provider of chocking and mounting materials, as well as a service provider for alignment and mounting solutions for machines. The company, which was acquired by SKF in 2000, has more than 25 years of experience in providing complete solutions for the mounting and alignment of machines. At this time, Machine Support’s 50-person staff offer their expertise in the marine field to ship owners, operators, shipbuilders, ship repair organizations and OEMs throughout the world.
www.shaftdesigner.com
www.machinesupport.com