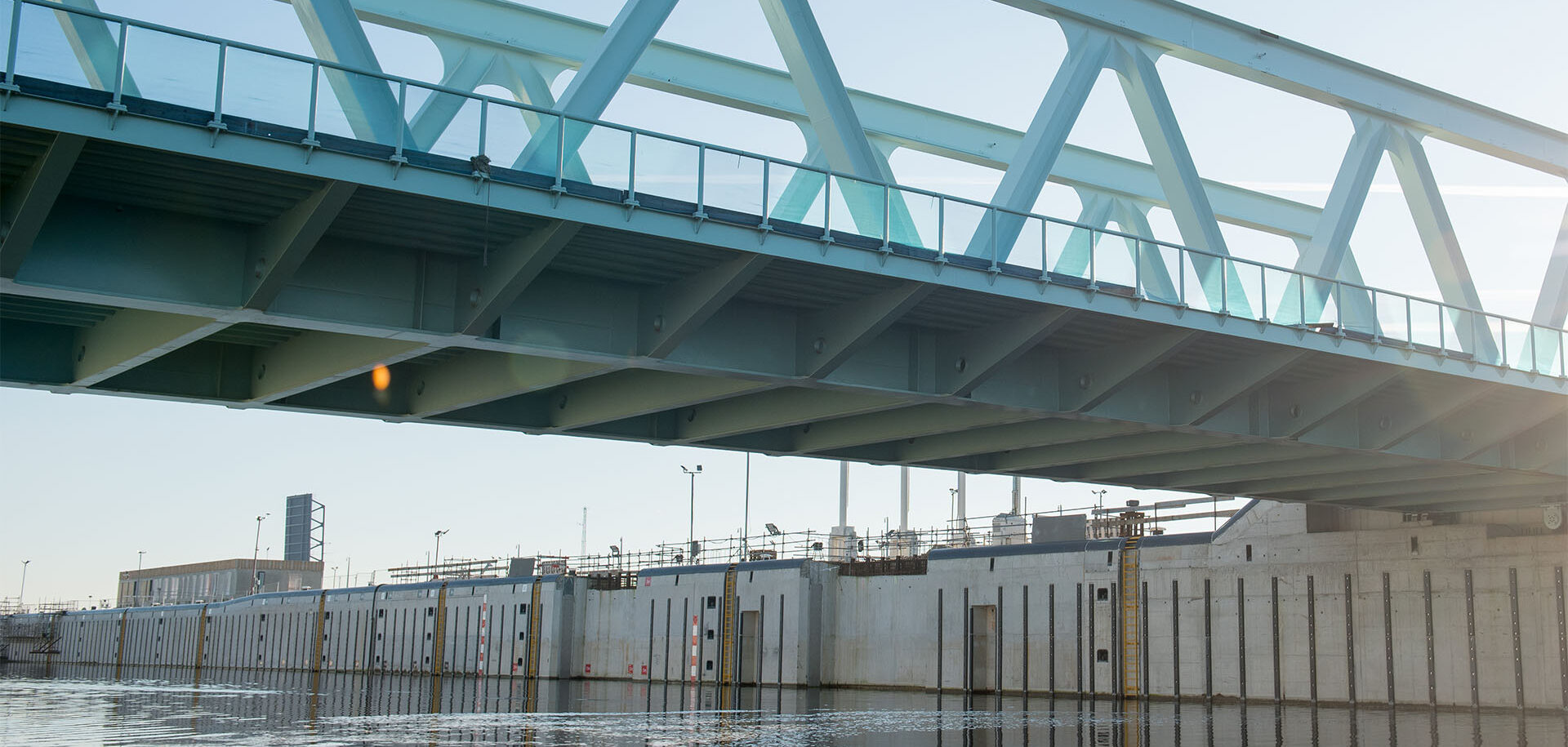
Unlocking progress
A new lock complex, which will allow larger ships to traverse the Terneuzen-Ghent canal, relies in part on SKF bearings that each weigh up to 1.5 tonnes.
Large engineering structures dominate our modern landscape. Whether skyscrapers or a football stadium, they draw the viewer’s eye to their sheer immensity.
“People see hundreds of thousands of cubic metres of concrete, but they don’t see the small stuff,” says Tom op ’t Roodt, a project leader at building contractor Sassevaart. “There’s an incredible amount of detail that goes into these superstructures, and incredibly tight tolerances.”
He is part of a consortium that is building a different superstructure – a new lock on the Terneuzen–Ghent canal. The lock will allow more and larger ships through the ports of Ghent in Belgium and Terneuzen in the Netherlands and involves the construction of two new moveable traffic bridges and four new lock gates. The Flemish-Dutch Scheldt Committee, as a part of the North Sea Locks in Terneuzen, is the client.
“By worldwide standards, this is a large project,” op ’t Roodt says. “The lock is comparable in size to those in the Panama Canal.”
The scale of the project creates a formidable challenge. Each bridge spans the entire width of the lock. When the bridge lifts up to let a ship through, it protrudes 69 metres into the air. The bridge weighs around 1,250 tonnes, and the counterweight weighs 1,050 tonnes.
“When we put it in place, we only have a few millimetres of tolerance,” says op ’t Roodt. “The same is true for the lock gates.”
Both bridges were built in China, under the contractor’s supervision, and were moved to Europe on completion. They were stored in the North Sea Port area until they were transported up the canal to the construction site in Terneuzen.
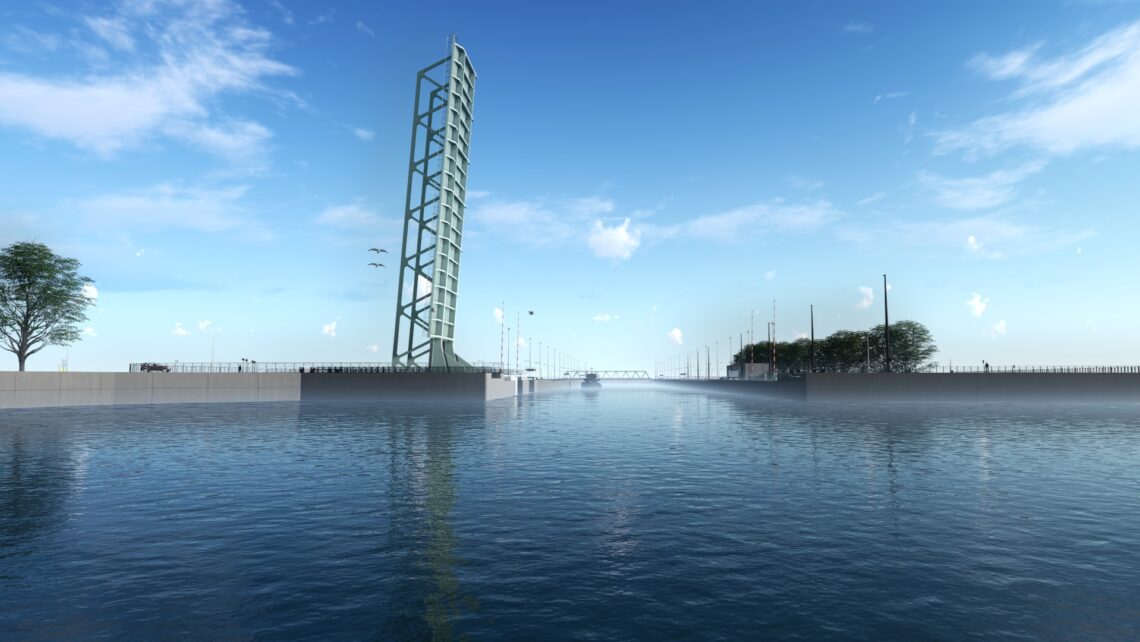
Bearing up
Bearings are critical to the smooth working of the lock complex, including both bridges and all the lock gates and include roller bearings, maintenance-free bearings and various small bearings.
“The bearings are important because they allow everything to move smoothly,” says op ’t Roodt.
SKF supplied eight huge spherical roller bearings for the project, plus eight locking nuts to keep them in place. For most of the bearings in the project, the life expectancy is 25 to 50 years, but, says op ’t Roodt, these main bearings are designed to last 100 years, with maintenance. “This is logical,” he says, “because changing the bearings is so difficult.”
Despite their enormous size, and the criticality of the application, the bearings are standard, available from SKF’s catalogue.
One particular challenge in installing the main bearings was that the operation had to be performed at a height of 12 metres, due to the fact the bridges were stood on jacks at the work site. “We had to find a good way to lift the bearings to the correct height,” op ’t Roodt says. “Because they are bearings, they tend to fall in a certain direction, over which you have no control.”
This meant manipulating the bearings at height and positioning them correctly, with a maximum misalignment of 2 millimetres allowed. There was also a steel housing that fitted above and below the bearing.
SKF solved the tricky problem by designing a special lifting beam to pick up the bearing and align it correctly. After preparations were made on the ground, the bearing was lifted and mounted onto a shaft.
“This initiative came from SKF, because they have experience in this,” says op ’t Roodt. “It allowed a smoother mounting of all the bearings.”
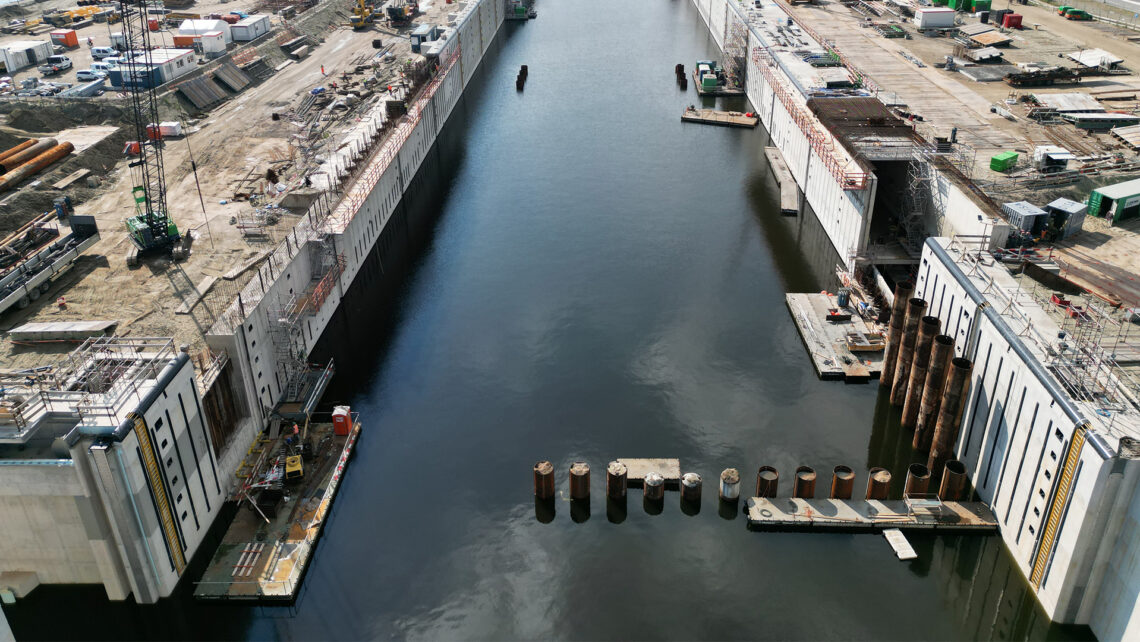
Shrink fit
However, getting the bearing onto the shaft was only part of the challenge. Then the shaft had to be inserted into the bridge structure, with yet more attention to detail and fine tolerances.
“For a bridge and shaft of this size, it’s hard to grasp,” says op ’t Roodt. The answer was to construct the bridge without shafts. It was almost impossible to ensure that everything, such as the welded structure and its turning points, lined up, he explains. Instead, the elements of the bridge were built with a tolerance during the construction phase.
“When we finished construction, we measured the whole bridge, and only then did we make a hole for the shaft,” op ’t Roodt says. “That way, we knew they would be aligned.”
Inserting the shaft into the bridge was the most nerve-racking part of the project. It involved drilling a large, circular hole in the bridge structure. The shaft was then inserted into the hole. To ensure a tight fit, the shaft was cooled to around -40 °C using dry ice, while the hole itself was heated. This created a “shrink fit”, meaning the shaft and bridge would then be impossible to separate.
“This was so critical,” op ’t Roodt says. “If we’d made a mistake and had a shaft that was not aligned or perpendicular to the bridge, we would not have been able to fix it. It had to be right first time.”
Being right the first time involved lots of upfront testing, to make sure there were no mistakes. Time was also a critical factor in this final stage. “When you take a shaft out of the freezer you have one or two hours to mount it into the heated hole,” he says.
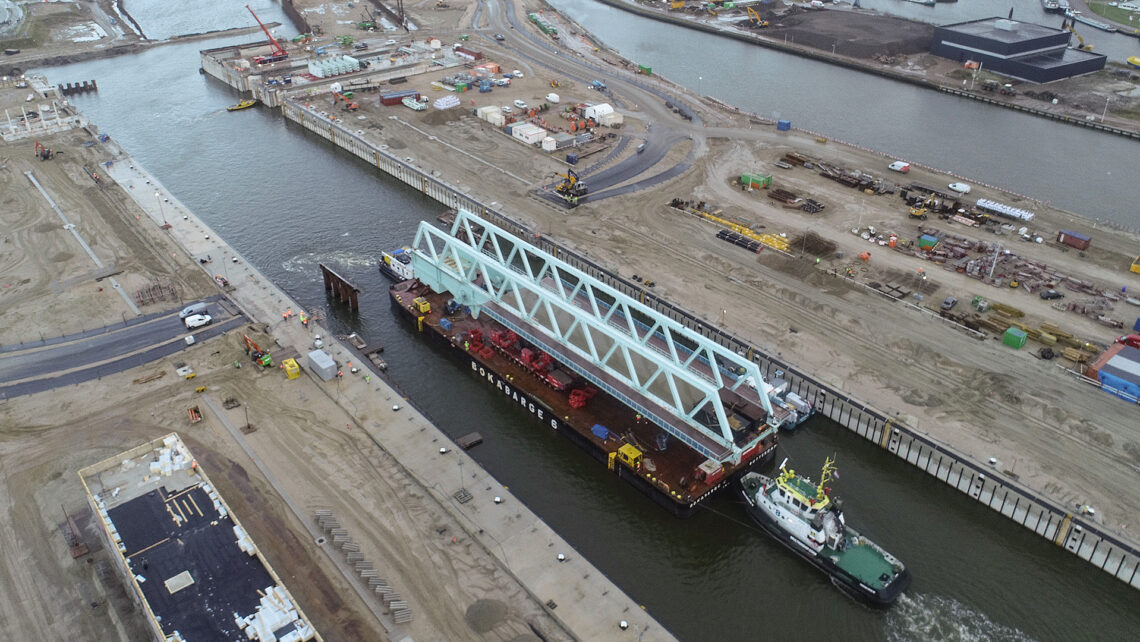
Testing times
The project has now edged into its final phase. The lock gates have been fully tested for complete movement; substantial testing on the bridges has also taken place.
“We tried a temporary way to open the bridge, without the complete drivetrain, and it opened smoothly,” op ’t Roodt says.
The project has since progressed to more extensive testing of the bridge, to answer questions such as “What if there is an emergency stop?”
Both bridges, in their down positions, are being used by road traffic. (Ships are using other locks so are not currently passing this way.) “To have a lock complex that’s completely active, we’ll also need the control logic to be working perfectly,” he says.
This is yet another part of the testing phase, after which will come a site integration test, which must be performed before any ships can be let through. “The complete testing phase will be finished by the summer of 2024, and the lock complex will then open at the end of 2024,” says op ’t Roodt.
Canal traffic
Canals may seem a quaint, old-fashioned form of transport, but they remain a vital way of moving goods from place to place. Not only can they transport higher volumes than road traffic, but they can do it with fewer emissions.
It’s vital that the road and canal traffic do not affect one another, however. With the completion of the Terneuzen-Ghent canal project, the bridges will allow road traffic to keep flowing, while the locks will allow ships to pass up and down the canal continuously.
The North Sea Locks at Terneuzen comprise three locks – west, middle and east. The old middle one, the smallest, has been demolished and replaced with the new, larger lock. Ships can pass through any of the locks. When the new lock opens, which is scheduled for the end of 2024, it will allow larger ships to pass and reduce waiting times for both sea and inland shipping there.
The project, costing a little over 1 billion euros, is funded by the Dutch and Flemish governments.
Behind the scenes
With bearings playing such a central part in the huge new lock, SKF also played a vital, if behind the scenes, role. “During the customer’s engineering phase, we strongly recommended being at the table so we could create a safe, efficient working procedure for mounting the bearings,” says Wim Nieborg, business manager for engineering projects at SKF. “This was also necessary because the customer demanded substantial warranty over the delivered bearings and their functionality.”
Once this was accepted, SKF could extend its scope and introduce services such as 3D alignment measurement and also apply its specific knowledge of mounting bearings.
These included:
- Aligning services (3D);
- Mounting all eight bearings using the specially designed lifting device;
- Offering support during the final positioning of both bridges; and
- Delivering and installing all lubrication systems.
“In this project we were able to provide valuable multi-disciplinary services, which the customer had not expected us to supply,” he says.
Top 10 bridge trivia
- The Tower Bridge in London, UK, consists of around 31 million bricks.
- China’s Beipanjiang (or Duge) Bridge is the world’s highest bridge, with a road deck 565 metres above the Beipan River.
- The Beaufort Sea Road in Alaska, at 109 kilometres, is the world’s longest ice bridge.
- The towers that support the Akashi-Kaikyo Bridge in Japan stand some 282.9 metres above the water.
- The Bosphorus Bridge in Istanbul, Turkey, is one of the few bridges in the world that connect two continents, spanning the Bosphorus Strait and linking Europe and Asia.
- There are seven main bridge designs. The beam bridge is the most common. The world’s longest beam bridge is the Danyang-Kunshan Grand Bridge in China, which is 164 kilometres long.
- The Leonardo da Vinci Bridge in Norway is a pedestrian bridge and was designed based on a sketch by artist and inventor Leonardo da Vinci.
- The tallest tower of the Millau Viaduct in France is 343 metres, taller even than the 330-metre Eiffel Tower.
- The new 1915 Çanakkale Bridge in Turkey opened in 2022 and, at 2,023 metres, is the record holder for the longest suspension bridge span in the world.
- From July 2022 to June 2023, 16,345,972 vehicles crossed southbound on San Francisco’s Golden Gate Bridge.