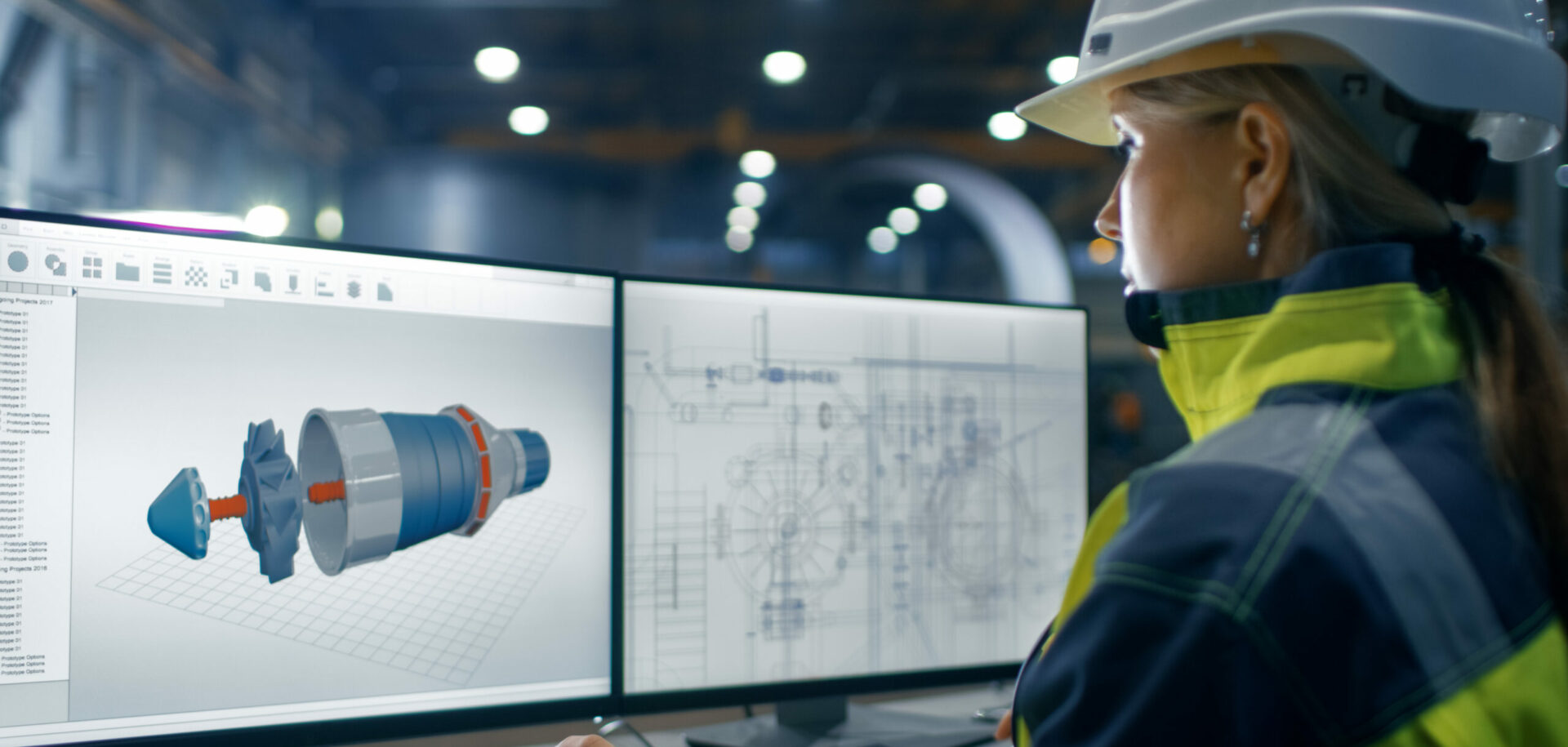
Upgraded SKF Explorer self-aligning roller bearings extend service life
Developments in steel processing technology have given SKF the opportunity to further improve the performance of its SKF Explorer self-aligning roller bearings. Thanks to a patented heat treatment, upgraded SKF Explorer bearings can provide up to twice the service life under harsh conditions with poor lubrication or high contam-ination levels. By improving wear resistance, upgraded SKF Explorer self-aligning roller bearings offer performance benefits in a wide range of challenging industrial applications. When SKF first launched the SKF Explorer performance class in 1999, it set new standards for bearing performance. Now, SKF has further improved the heat treatment for self-aligning roller bearings (fig. 1), so that they are even more wear resistant. Though this upgraded heat treatment can improve uptime for virtually any application where reliability and long service life are key operational parameters, the benefits are most apparent in industrial applications where there are high levels of contamination or poor lubrication conditions. Typical examples include the metals, mining, mineral and cement processing industries, wind power and marine, industrial transmission and material hand-ling applications. The upgraded heat treatment process results in significantly improved wear resistance for upgraded SKF Explorer bearings when compared with original SKF Explorer bearings. Validation testing was carried out at testing centres within SKF and at KTH University (Royal Institute of Technology) in Stockholm, Sweden, to validate the performance improvements. The test results (fig. 2) show the improved wear resistance that upgraded SKF Explorer self-aligning roller bearings provide. The contribution that the improved heat treatment provides, to extend the service life of upgraded SKF Explorer self-aligning roller bearings, is significantly improved wear-resistance, which can result in up to twice the bearing service life under poor lubrication or severe contamination conditions. This opens the opportunity for end users to increase equipment uptime in some of the harshest and most challenging industries, from wind power to metals processing. CARB is a registered trademark of the SKF Group. SKF EXPLORER is a trademark of the SKF Group.
Summary
By combining material, design and manufacturing improvements, SKF engineers and scientists were able to maximize the effect of lubrication and minimize the effects of friction, wear and contamination. The result: a performance class of bearings that provided higher load carrying capacity and extended bearing service life. The superior behaviour of this performance class has been confirmed and validated by leading certification bodies, certificate 72736 dated 10/05/2006 from Germanischer Lloyd and CPN-1441-1 dated 10/05/2006 from Det Norske Veritas.
From a materials perspective, SKF Explorer self-aligning roller bearings were characterized by an extremely clean and homogenous bearing steel that underwent a unique heat treatment process. The purity of the steel gave SKF Explorer bearings their exceptional strength and durability. The heat treatment created the optimal combination of hardness and dimensional stability.
These improvements in material performance were built into a new bearing concept with improved surface structures and refined internal geometry tolerances. SKF also made significant investments in its manufacturing processes.
The result was a highly reliable range of self-aligning roller bearings, with low friction, high load carrying capacity and minimized stresses.
Since the introduction of SKF Explorer spherical roller bearings, the SKF Explorer performance class has expanded to include other bearing types including tapered roller bearings, cylindrical roller bearings, deep groove ball bearings and angular contact ball bearings. Today, all standard spherical roller bearings, CARB toroidal roller bearings and most spherical roller thrust bearings are manufactured to SKF Explorer performance class specifications.Heat treatment adds performance
To reach this new level of performance, SKF engineers were able to adjust the heat treatment process and increase hardness by up to 2 HRC (depending on bearing size) while maintaining or improving toughness.
This is particularly important for medium- and large-size bearings used in process equipment.
The improved toughness provides more time from when the first signs of damage are identified, until the bearing becomes unserviceable. This additional time enables end-users an opportunity to track the condition of the bearing as they prepare for repairs, virtually eliminating unplanned downtime and reducing the additional costs typically associated with it.Validation testing
Other tests, conducted at the SKF Engineering and Research Centre, to verify the service life gain of upgraded SKF Explorer self-aligning roller bearings under poor lubrication conditions (fig. 3), indicate that these bearings can last up to twice as long as original SKF Explorer bearings. For contaminated conditions, endurance tests (fig. 4) similarly indicate a possible doubling in service life for upgraded SKF Explorer bearings, when compared with the original SKF Explorer bearings.
To verify the extended failure mode of upgraded SKF Explorer self-aligning roller bearings, through-fracture tests were performed on the rings. In these tests, upgraded SKF Explorer bearings were compared with original SKF Explorer bearings.
The results shown in fig. 5 indicate that the average radial crack depth at through-fracture, for rings in upgraded SKF Explorer bearings, is deeper than for original SKF Explorer bearings. This shows that medium- and large-size upgraded SKF Explorer bearings can further extend the time from initial spalling to through-fracture. The extended failure mode, when part of a proactive maintenance programme, can virtually eliminate unplanned downtime.
The flange strength of upgraded SKF Explorer spherical roller thrust bearings was tested against original SKF Explorer bearings (fig. 6). After the flanges on original SKF Explorer fractured, the upgraded SKF Explorer bearings ran twice as long and had only developed spalls.
Even though bearings in process equipment are not run to through-fracture, these tests show that once bearing damage has been detected, upgraded SKF Explorer bearings continue to operate longer, providing more time to plan, order parts and prepare for a shutdown; thereby reducing downtime and its related costs.Conclusion