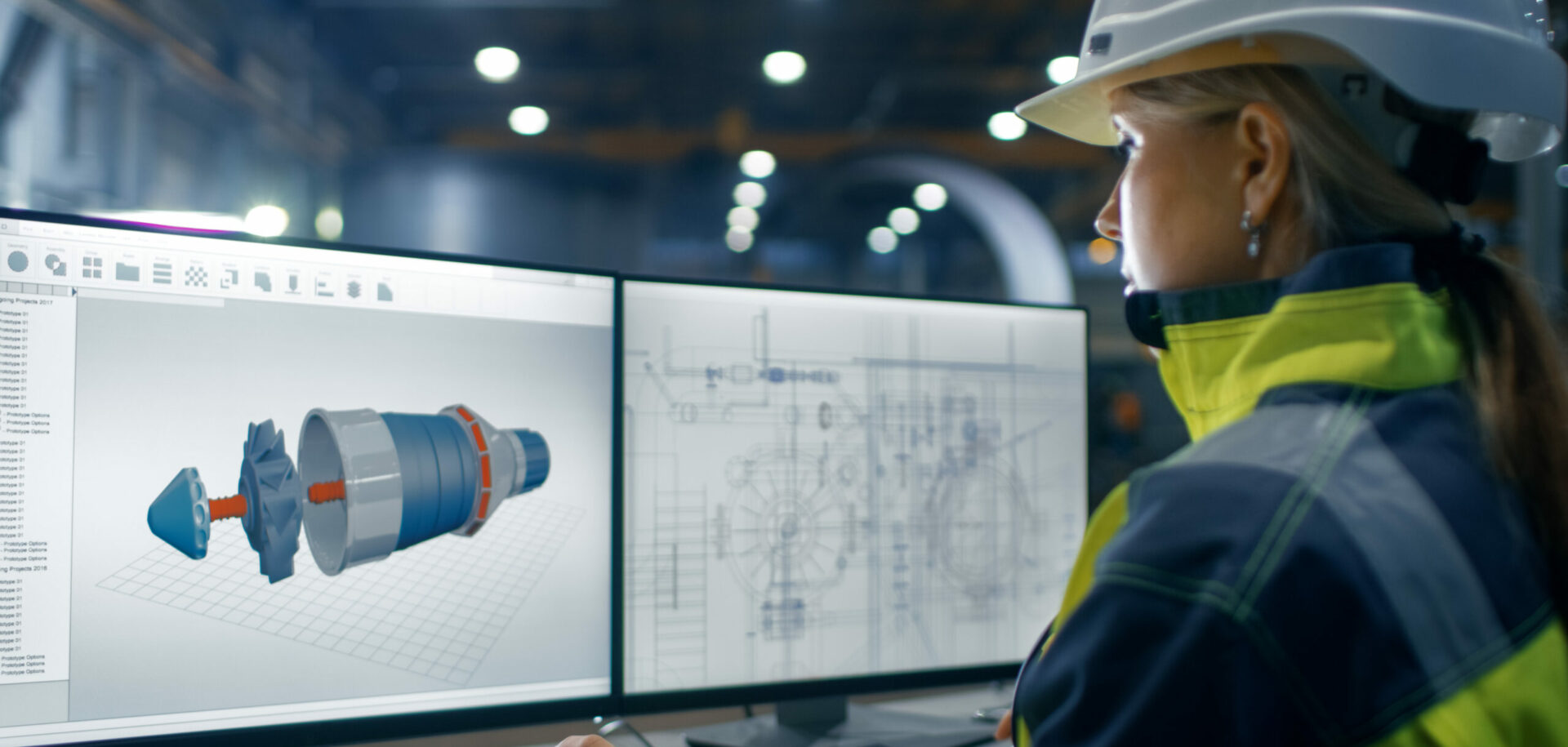
Wheel flange lubrication for railway systems
Willy Vogel AG, part of the SKF Group, offers wheel flange lubrication system solutions to reduce friction. Friction is a particular problem when train wheels encounter curves, as friction occurs between the wheel flanges and the inner sides of the rails.
Willy Vogel AG, part of the SKF Group, offers wheel flange lubrication system solutions to reduce friction. Friction is a particular problem when train wheels encounter curves, as friction occurs between the wheel flanges and the inner sides of the rails.
The railway industryis gaining stronger focus and momentum worldwide. There are many reasons for this, including environmental challenges, availability of energy and the growing congestion in major cities. The cost of investments in road infrastructure is also contributing to an increasing awareness of the capabilities that rail transport can offer to support a sustainable world.
SKF provides a range of solutions to support the railway industry. This includes, for example, pre-lubricated and sealed bearing units with sensors, wheelset packages of axleboxes and bearings, traction motor bearing solutions, lubrication systems, high-performance plain bearings and bearing service facilities.
In terms of sustainability, major contributions from Vogel are solutions comprising wheel flange and railhead lubrication systems for railway vehicles. The friction at the contact area between the wheel flanges of railway vehicles and the rails determine wheel and rail wear. Vehicle and track maintenance intervals are strongly determined by this wear process and dramatically influence the life-cycle cost of the total vehicle and the track. Therefore considerable energy savings can be achieved by reducing the friction in these contact areas. This friction has to be considered consolidated, as it occurs on all wheel flange contacts in a train, on every journey and every day. An additional envir-onmental topic is noise reduction. The wear process is often accompanied by a squealing sound that is unacceptable, especially for residential areas close to railway lines. Moreover, the danger of derailment also grows when wheel flanges are left unlubricated.
Selective, precise application of lubricant to the wheel flange faces of locomotives, multiple units, suburban trains, metros and tramways contribute not only to the friction properties of these wheels, but also to all the following wheels of, for example, passenger or freight cars.
The lubricant, sprayed on the wheel flanges of the first axle in the direction of travel, is transferred to the rail face, thus lubricating the following wheel flanges. Optimally configured wheel flange lubrication systems can supply as many as 250 axles. A large number of motor cars with wheel flange lubrication provide the requis-ite lubrication for the rail network. This is the basis on which wheel flange lubrication systems can achieve the desired effect.
The service life of wheelsets and tracks can be considerably extended using suitable lubrication solutions. Travel of up to 500,000 km before the wheelsets have to be reprofiled or remachined is no longer a rarity.
A wheel flange lubrication system often pays back for itself in just one year. And that doesn’t include the savings that result from longer rail track life, above all in curves. Thanks to their high reliability, combined with significant technical developments in control and monitoring techniques, Vogel’s wheel flange lubrication systems can be adapted to any type of powered rail vehicle. Vogel has developed various designs of wheel flange lubrication tailored to specific application requirements.
The main benefits of wheel flange lubrication can be summarized as:
-
Noticeable reduction of downtime and increased operational reliability and readiness
-
Reduced wear, thereby significantly lengthening the intervals for reconditioning and exchange of wheelsets and rails
-
Increased safety through reduced risk of derailment by, for example, wheel “climbing” on the rail
-
Reduction of noise emissions
-
Reduction of impact on the environment through use of rapidly biodegradable greases
-
Proven quality system, like Deutsche Bahn AG certificate Q1
-
Control of the wheel flange lubrication systems, using curve sensor technology.
Single-line systems EasyRail single-line system
In a single-line system, the lubricant is already metered in the piston pump. The lubricant is transported by compressed air to the nozzles via a distributor. From there it is sprayed onto the wheel flange. Thus only one line, carrying both the lubricant and compressed air at the same time, is installed. This is a simple configuration that means less installation time and expense. In many cases it is possible to install the wheel flange lubrication system on low-floor vehicles without having to dismantle the panelling.
The EasyRail system (fig. 3)consists of a piston pump with a reservoir, a flow divider and the respective spray nozzles, used to apply the lubricant to the wheel flange. All moving parts were brought together in the unit consisting of a piston pump with reservoir. This means the components are highly accessible and easy to service or replace. Moreover, neither the flow divider nor the spray nozzles have any moving parts, which considerably reduces maintenance time and expense. The air/lubricant mixture in the flow divider is split up into equal parts when the flow conditions prevailing in the outlet branches are similar.
EasyRail City airless single-line system
The EasyRail City lubrication system (figs. 4 and 5) is used mainly on suburban trains and metros where the supply of air is a problem. The system works without an air supply unit, using electromagnetic pumps with an integrated spray nozzle that can be heated.
From a tailor-made reservoir, the lubricant (oil or fluid grease) feeds the electromagnetic pump unit. The integrated spray nozzle meters the right quantity of lubricant to the wheel flange. This solution is a technical alternative to the stick lubricator.
Benefits of airless single-line systems include:
-
Compact design
-
Simple configuration
-
No pressurized air supply unit
-
Easy installation.
Dual-line systems SP8 dual-line high-pressure system
The SP8 wheel flange lubrication system (figs. 6 and 9) is a dual-line, high-pressure system that is used mainly on larger locomotives. The maximum distance between wheelsets is 20 m and the max-imum length between the pump and spray nozzle is 10 m. The spray nozzles supply lubricant to the wheel flanges on the leading axle and/or the wheel flanges of the respectively leading axle on a bogie. The lubricant is transferred from the wheel flange to the rail face, where it reduces friction between the following wheel flanges and rail face as well.
The pump feeds the lubricant to the grease control valve. From the grease control valve the lubricant is directed to the spray nozzles for the first axle in the appropriate direction of travel. The lubricant is metered in the spray nozzles in volumes typically 0.03 or 0.05 cm³/spray and sprayed onto the wheel flanges with compressed air with a system pressure of a maximum of 100 bars. The high system pressure enables operation even under extreme operating envir-onments like low temperatures (down to -40°C). The system can be used for bi-directional operation.
SP9 dual-line low-pressure system
The SP9 wheel flange lubrication system (fig. 7) is used mainly for multiple units and smaller locomotives up to 5 m between the reservoir and spray nozzle. The spray nozzles supply lubricant to the wheel flanges on the leading axle and/or the wheel flanges of the respectively leading axle on a bogie. The lubricant is transferred from the wheel flange to the rail face, where it reduces friction between the following wheel flanges and rail face as well.
The compressed air for the pressure reservoir is enabled when the rail vehicle is made up. The lubricant is fed to the spray nozzles and is constantly available in the form of a column. The metering of the lubricant takes place in the spray nozzles. The spray nozzles are actuated by compressed air, and the compressed air is controlled by the valve block. The grease reservoir is de-pressurized when the rail vehicle is shut down.
Benefits of dual-line systems include:
- Compact design
-
No separate grease pump
-
Separate expendables feed
-
Precise spray-nozzle metering
-
System independent of the vehicle length.
Tram dual-line system with compressed air supply
The tram system (fig. 8) is specially designed for streetcars and trams and is equipped with double nozzles for each wheel. An on-board tailor-made compressor supplies compressed air. The compressor can use either AC or DC current. There is the possibility of combining wheel flange with railhead lubrication. The pneumatically operated grease pump provides lubricant to the metering distributor and the mixing block with the spray nozzles.
The applications areas for this lubricant system are in vehicles without compressed air supply, preferably used on urban rail vehicles or where a combined wheel flange with railhead lubrication is possible.
Benefits of this design include:
-
Compressed air supply unit
-
Versatile capability
-
Variable metered quantities of piston distributors
-
Combined wheel flange with rail-head lubrication possible, dramatically reducing squealing noise emission.
Curve sensor CS200
As curves increase friction and wear, Vogel has developed a system that can help improve lubrication when a train enters a curve. The CS200 curve sensor, used for all wheel flange lubrication systems, offers a comprehensive range of functions and customer values. It is used to control wheel flange lubrication systems for optimizing the sprayed lubricant quantity. Two spray nozzles are actuated, the lubrication taking place in curve-, time- or distance-dependent modes.
Lubrication is triggered after a certain number of previously specified pulses are received. In the case of curve-dependent lubrication, it is possible to specify whether lubrication is to take place on both sides or only on the respective outside curve, depending on the direction of travel. Curves are detected via an integrated sensor with adjustable sensitivity.
Lubricants
Lubricant quality has a decisive influence on the effectiveness of the lubrication applied to the wheel-rail interface. Ultimately, it determines the friction, wear and noise level. In the past few years attempts have been made to achieve optimal surface smoothness and minimal wear with the help of increasingly higher percentages of solid additives.
Regardless of the fact that a certain amount of wheel flange wear is necessary for proper functioning of the wheel-rail interface (undesirable growth in the diam-eter of the wheel flange likewise increases the danger of derailment) solid particles in the lubricant are only good if they do not lead to clogged systems, which can jam the wheel flange lubrication installation. Vogel offers an assortment of suitable wheel flange lubricants for all kind of applications.
The Vogel wheel flange lubrication systems have a long record of excellent performance. Leading railway rolling stock suppliers like Alstom, AnsaldoBreda, Bombardier, Siemens and Stadler equip vehicles for major train operators with these systems.