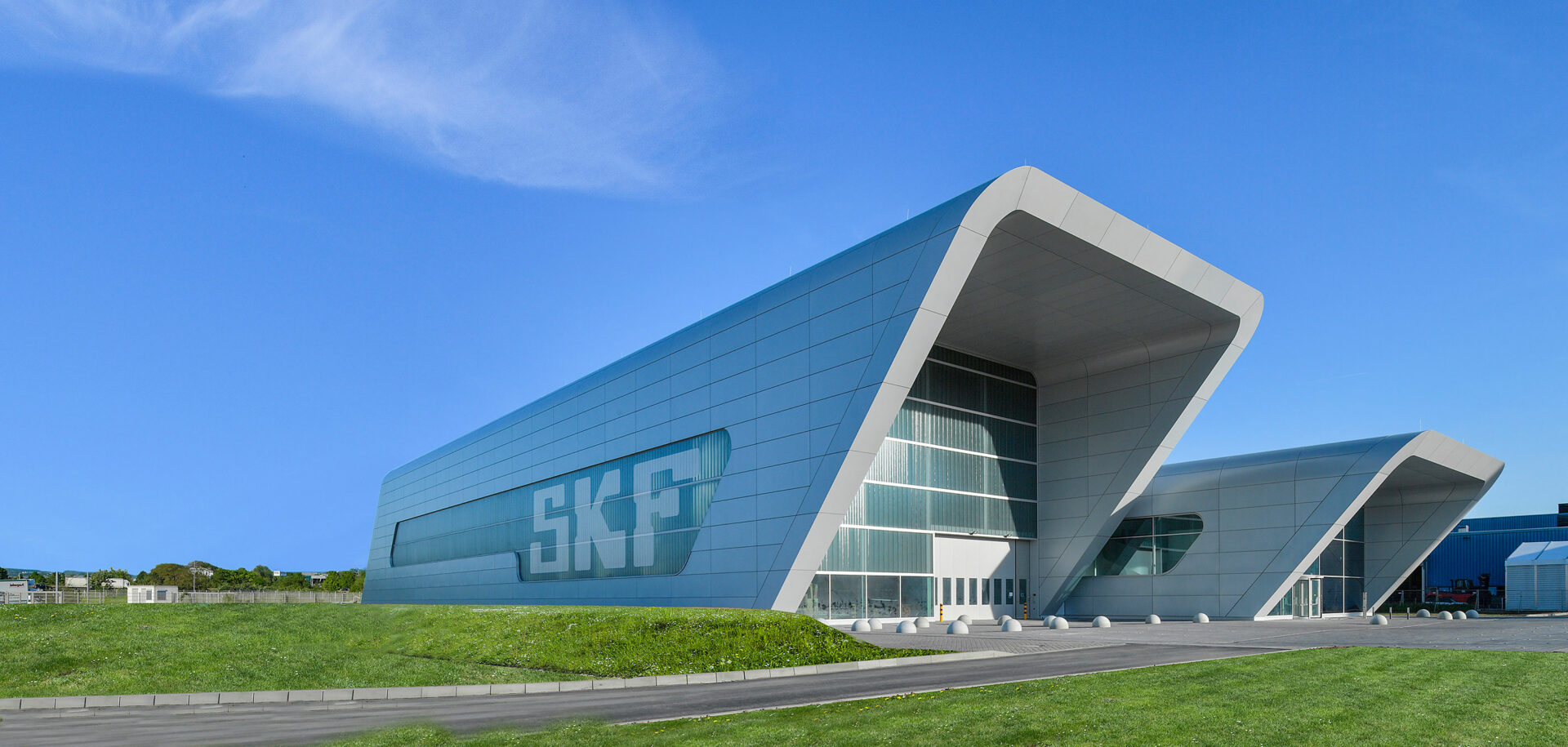
全球首屈一指的
大型轴承测试
中心投入运行
SKF的Sven Wingquist测试中心于近期正式落成启用,这是世界上最强大的大型轴承测试中心。该中心位于德国施韦因富特市,配备两个可在极限状态下测试轴承的全新巨型测试台。该基础技术项目将有助于进一步优化大型轴承设计,实现更高效的制造,并让客户从优化的解决方案中受益。
SKF拥有多种功能极强的软件,用于对所有类型的滚动轴承进行计算和仿真,其中一些高度复杂的系统可以在虚拟环境下研究轴承运行状态。例如,借助SimPro Expert工具,技术娴熟的专家可以根据SKF广泛的轴承寿命理论计算滚动轴承的疲劳寿命。该软件不仅是SKF多年研发的成果,还代表了SKF数十年的轴承运营经验。另一款更强大、被称为“BEAST”的工具亦是如此,SKF工程师使用这款工具来详细模拟轴承内部的动态特性。BEAST是一个虚拟测试台,能在几乎任何载荷条件下,对轴承内部的载荷、力矩等进行研究。
软件有时束手无策
然而,迄今为止,这款软件以及其他任何仿真程序都无法以完全真实的方式再现大型轴承的内部运行状况。经验表明,虽然采用了最细致的计算方式,在设计上增加了额外的安全裕度,并以最高的标准进行制造,但一些大型轴承仍会出现过早损伤和失效。因此显而易见,现有的仿真模型使用的因果算法仍未能完全考虑到实际应用中的某些现象。
总结
目前,世界上没有一个仿真程序能够以完全真实的方式重现大型轴承内的所有动态过程。在德国施韦因富特市,最先进的SKF Sven Wingquist测试中心的两个新测试台可以提供更深入的见解,有助于改进现有的仿真模型,从而使计算结果更贴近现实。此外,从中获得的专业知识将被纳入产品开发中,并将有助于确保未来的大型轴承在各自的应用中获得最大的耐用性,并尽可能降低重量和摩擦。所有这些措施不仅能在测试和生产过程中,也能在未来的SKF大型轴承业务应用中节省资源,对于环境和用户来说都大有裨益。
为了揭示这种损伤背后尚不为人知的根源,SKF投入约4,000万欧元建成了Sven Wingquist测试中心。该中心位于德国施韦因富特市,是世界最强大的大型轴承测试中心。在该中心颇具未来色彩的双子建筑(图1)中,两个新的巨型测试台可以在绝对极限状态下驱动和测试大型轴承。
风力发电机的巨大受力状态
最大的测试台(图2)开业界先河,不仅可以测试单个风力发电机轴承(外径最大为6米),而且能测试包括配套的客户部件在内的完整轴承组件。该巨型测试台总尺寸约为9×11×8米,重约700吨,配备了多达64个径向和轴向排列的液压缸,可产生数兆牛顿的动态载荷。
液压缸初始作用在测试台内部旋转的超大钢盘(图3)上。这个巨大的圆盘直径达7米,重达125吨。 圆盘通过一个适配器将液压缸产生的力传递到和适配器另端联接的被测轴承。
使用圆盘将产生的力传递到被测轴承的方法具有显著优势:作用在试样上的力不受限于施加载荷内部轴承的固有稳定性。相反,由液压缸和圆盘组成的系统可以在各个方向上施加载荷,这些载荷的总和比过去最强大的测试装置也要高好几倍。此外,考虑到被测轴承的尺寸,新的SKF测试台也实现了非常高的转速。
几周内再现20年
这个集动力学、最大的力、弯矩以及转速于一体的独特组合,最终有助于提升客户的关键经济效益。为了确保风力发电机的盈利能力,发电机上安装的大型轴承应当能无故障运行20年以上。20年的时间,包括这段时间内所有可能的载荷,在几个星期内就可由加速程序在新的测试台上非常逼真地再现出来。
这不仅节省了大量的时间和金钱,而且节约了能源。另外,测试台产生的热量可通过热回收系统,用于测试中心建筑和相邻的大型轴承工厂,从而节省了更多能源。由于对能源的高效利用,巴伐利亚州经济事务、媒体、能源和技术部为这个巨型测试装置提供了约190万欧元的资助。
掌控的力
为了确保测试台能以高度可控的方式将其巨大的力施加于被测轴承上,其下壳体段用大约200个预紧力达几兆牛顿的M80螺栓固定在其基座上。这些螺栓固定的基座是3000吨重底座的一部分。底座与开放和通风的测试中心建筑的其余部分分开,以避免与建筑物本身发生任何扰动性相互作用。
底座非常牢固,而基座和外壳接触面的精密加工更令人叹为观止:在约10米的距离上,接触表面的平整度偏差仅为零点几毫米(图4)。
较小的测试台更灵活、更快速
相比之下,两个新的SKF测试台(图5)中较小的测试台看起来不那么雄伟, 但也颇为强大。其130吨测试头配有四个轴向液压缸和两个径向液压缸,可通过使用内圈和外圈紧定套对多种大型轴承进行加载。被测轴承可用于造船、采矿和钢铁、纸浆和造纸以及水泥行业。因此,这个测试台用途极为广泛。它一方面具备灵活性,同时也是一个超大型机电一体化设备,重约300吨。
这个名为“David”的测试台产生的力超过六兆牛顿(大约相当于土星5号运载火箭的一台发动机的推力),转速达200转 /分以上。即使作为这两个新SKF测试台中的“老二”,兼具高载荷和高速度的David测试台在全球也无与伦比。凭借其独特的功能,这个测试台可以发掘大型轴承生产中节省能源和材料的巨大潜力。正因如此,德国联邦环境、自然保护、建筑和核安全部将该测试台纳入环境创新计划,并为其提供约160万欧元的资助。
极限条件下的润滑
David测试台还具有另一个不寻常的特点:它配备了SKF润滑系统部门提供的特殊润滑设备(图6)。 通常,SKF解决方案可确保对不同应用中的轴承,以最优的方式在恰当的时间供应适量润滑剂。 然而,专门为测试中心改造的这个专用润滑设备却完全相反,在测试时,它可将被测轴承置于润滑不足的边界状态,这样测试结果可以为进一步改进大型轴承的耐用性提供重要的发现。
该润滑设备的润滑油箱约6米宽、1.6米深,能容纳重达7.2吨的3,000升润滑油。该设备所采用的技术源自纸浆和造纸业,但SKF润滑系统专家根据测试中心的具体要求对其进行了全面的改造。值得一提的是,该设备还具有卓越的光学设计和防噪措施。
温度至关重要
为了能让被测轴承同时在极端载荷和极端润滑条件下运转,SKF设计出了油温范围可达传统解决方案大约两倍的系统,这可对被测轴承在非常高的摩擦应力下进行测试。
为了避免润滑系统本身在与被测轴承的“热战”中损坏,安装了基于板式换热器的冷却系统。
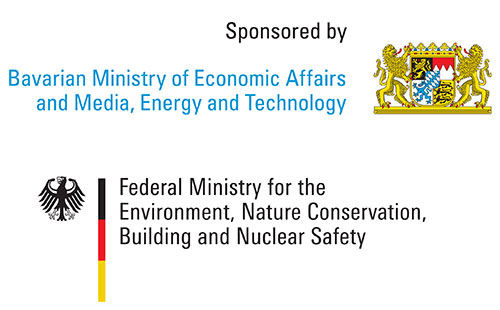
Sponsored by
巴伐利亚州经济事务、媒体、能源和技术部为两个测试台中较大的测试台提供约190万欧元的资助,德国联邦环境、自然保护、建筑和核安全部将较小的测试台纳入环境创新计划,为其提供约160万欧元的资助。
精确测量
系统通过12条线路将润滑油从供应站泵送到被测轴承。相互连接的配油控制台可精确测量每条线路和注油点的油量,因此,测试台可以在各种载荷条件下产生最苛刻的润滑条件。此外,由于润滑量可变、注油点众多,可以实现对被测轴承内油分布或内部流动的细微局部检查。为此,夹持被测轴承的适配器配备有全套辅助传感器。这些传感器不仅可以检测局部温度及其变化趋势,而且可以检测关键部件的振动、载荷和位置。最终,SKF专家可以查明轴承内发生了哪些动态效应,它们在何处发生以及在哪些条件下发生。
SKF工程师正尽一切努力,确保这个基础测试项目能不负期望,揭示出大型轴承中隐藏的秘密。目前,他们正致力于测试台大型硬件的验证,以及敏感测量技术的校准工作。