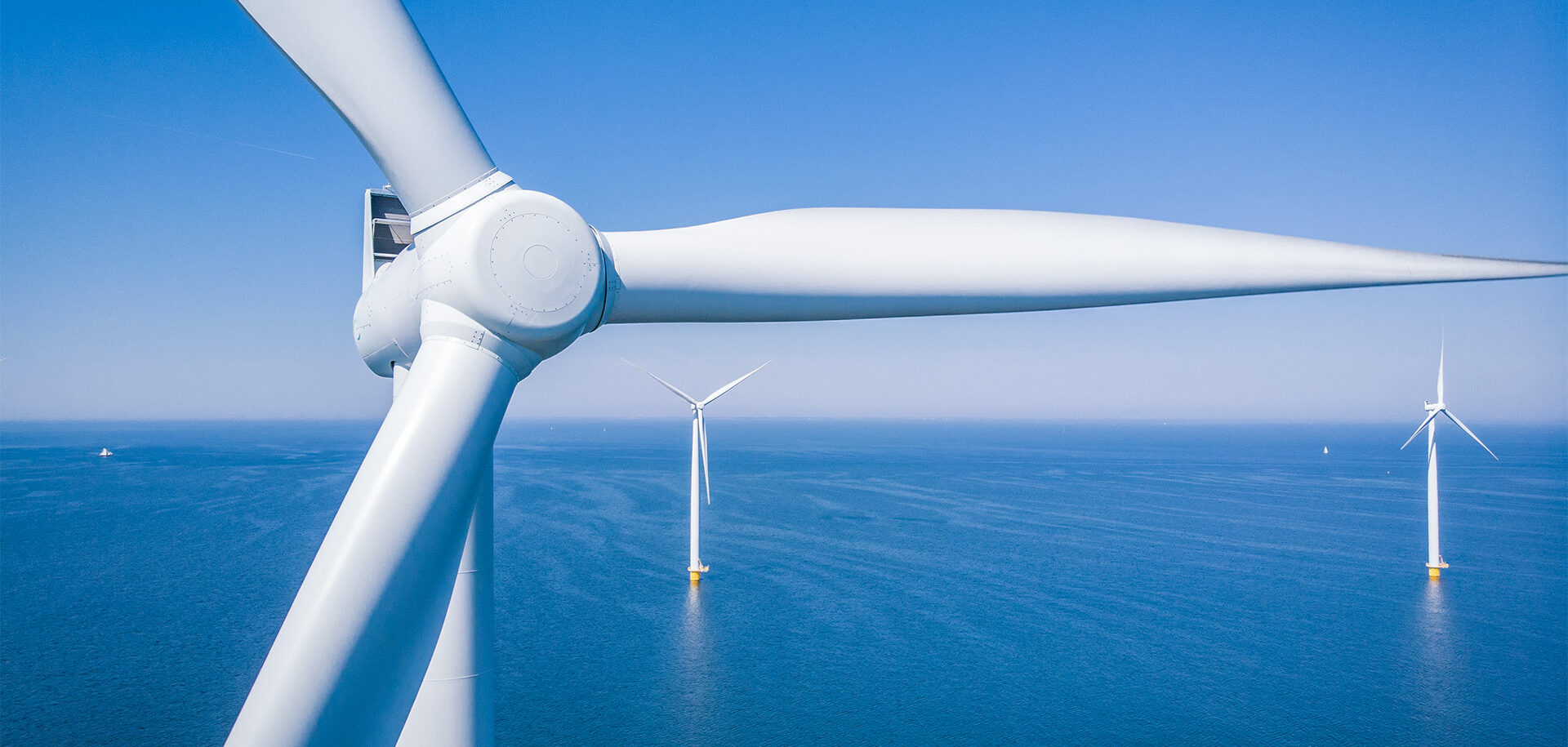
新型风电齿轮箱轴承挑战扭矩密度极限
SKF DuraPro风电齿轮箱轴承现已问世,其优势是具有更长的使用寿命和更高的稳定性。
风电行业一直面临降低平准化能源成本 (LCoE) 的压力,新型传动系统设计于是应运而生。由于塔顶上对重量的限制和最大部件运输尺寸的限制,亟需提高齿轮箱扭矩密度[1]。因此,在不影响实际性能的前提下,就必须进一步缩小包括滚子轴承在内的所有部件的尺寸。
现代风电齿轮箱由两级或多级行星轮组成。为了提高扭矩密度,就需要增加行星轮的数量,以将扭矩分布到更多的齿轮接触面上,从而为减小行星轮和齿圈的直径创造有利条件。这种新的设计趋势将会驱动齿轮箱尺寸的显著减小,但同时也会造成支承行星轮的轴承的安装空间缩小(图 1)。
优化滚子轴承解决方案
进一步减小行星轮尺寸的一种解决方案是使用液体动压滑动轴承。然而,从运行条件、转速、行星轮几何形状(例如宽径比)等方面来看,滚子轴承是一种具有成本竞争力、成熟可靠的解决方案。因此,我们需要能够承受更高载荷和接触应力的新型滚子轴承解决方案,以便为提高扭矩密度创造有利条件。
这种新的设计趋势将会驱动齿轮箱尺寸的显著减小。
为风电齿轮箱开发新型轴承解决方案的另一个重要驱动因素是需要提高可靠性和稳定性,以减少在实际应用中出现诸如白蚀裂纹 (WEC)[2]、微点蚀[4]等常见的轴承过早失效现象。
本文将介绍的 SKF DuraPro风电齿轮箱轴承是一个新型轴承设计研发项目的成果,具有如下特点:
- 延长了轴承的额定寿命,可以缩小轴承的尺寸。
- 提高了稳定性,可减少风电齿轮箱常见的失效现象。
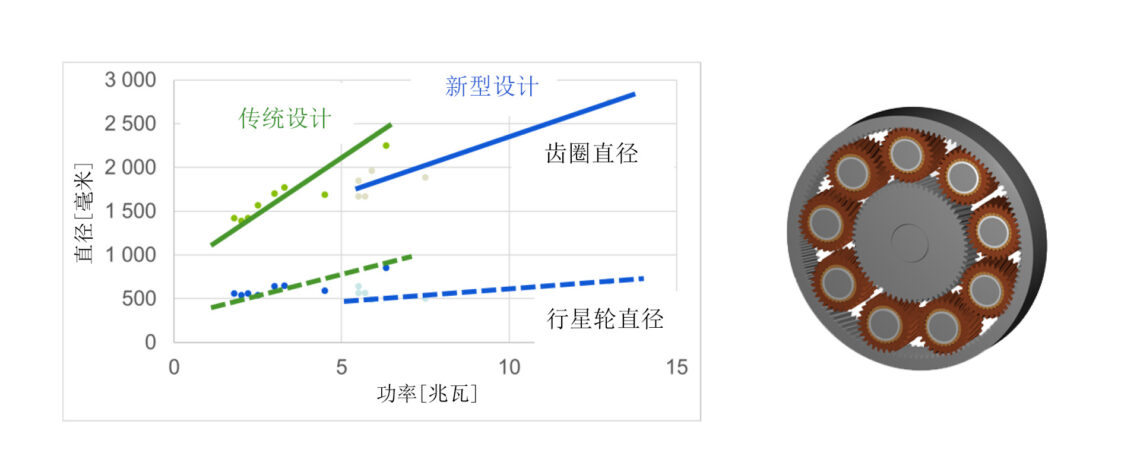
SKF DuraPro风电齿轮箱轴承
开发SKF DuraPro风电齿轮箱轴承旨在满足风电齿轮箱对滚动轴承的苛刻要求。这种轴承采用优质轴承钢制造,并经过了表面化学热处理,实现了轴承部件的表面和次表面的改性。
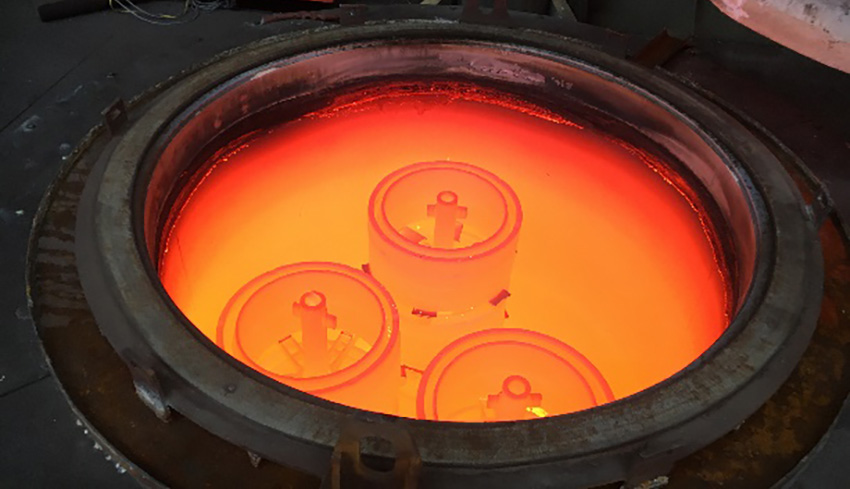
性能评估
轴承寿命试验
SKF进行的一项试验将轴承置于极高载荷、滚道预设压痕、全油膜和润滑不良的条件下。预设压痕模拟表面局部应力集中点,从而降低润滑效果。试验参数总结在表 1 中。
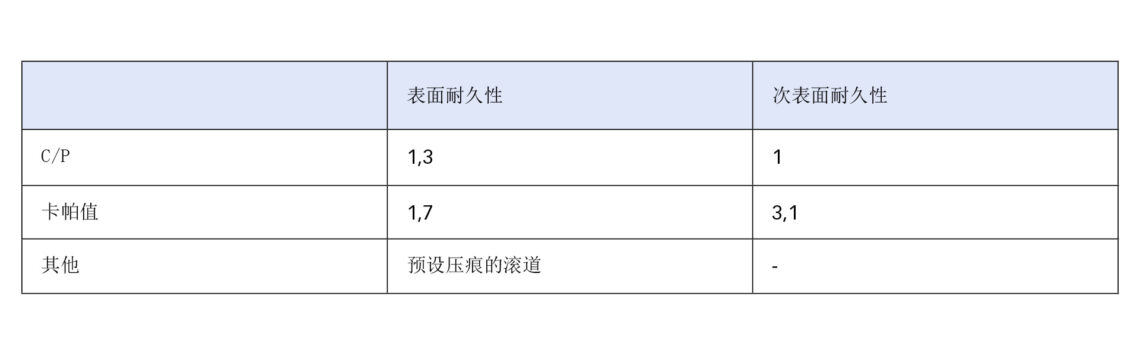
对两种不同的轴承进行了测试。参照轴承是先进的穿透硬化处理系列轴承,并具有 SKF Explorer [3] 特征和黑色氧化涂层,用来与 SKF DuraPro风电齿轮箱轴承进行对比试验。
所有耐久试验结果都汇总在一张单独的归一化威布尔图上,如图 3 所示。从该图可看出, SKF DuraPro风电齿轮箱轴承与参照轴承相比性能显著提升。星点显示的是SKF DuraPro风电齿轮箱轴承的 ISO/TS 16281:2008标准修正寿命(见第 4 节)。模型参数的选择使得额定计算寿命接近 L10h 可靠性区间的下限。
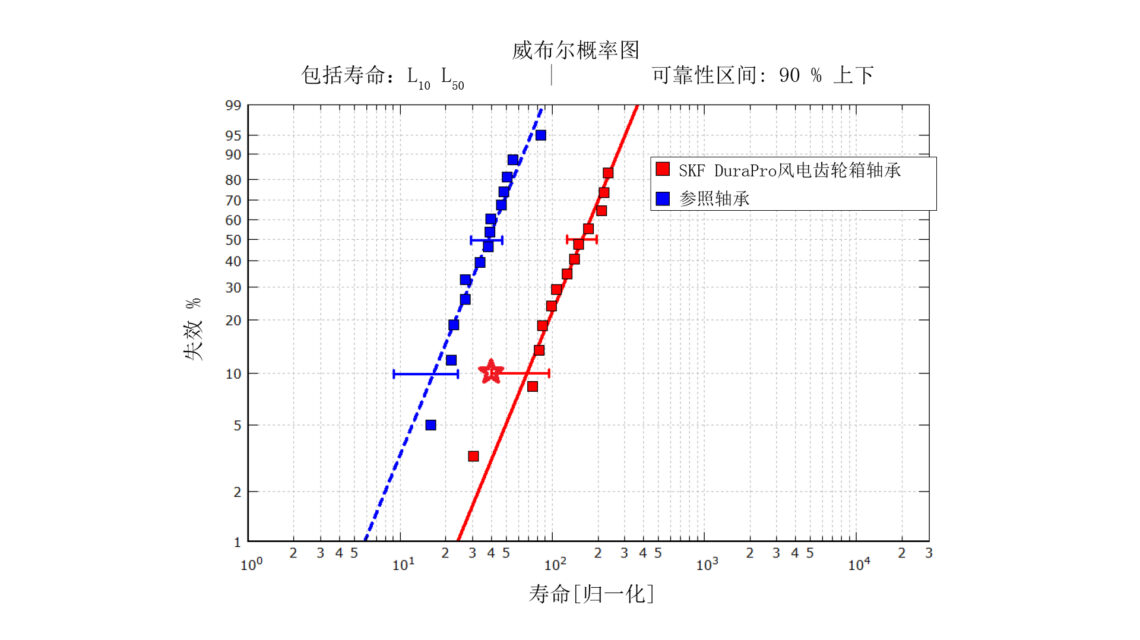
稳定性减少因白蚀裂纹导致的过早失效
尽管采用黑色氧化涂层等提高稳定性的工艺已显著减少了轴承过早失效的发生次数[6],但市场仍需要稳定性更高的解决方案。这一论断对于售后市场和新设计齿轮箱来说都是成立的因为人们尚未完全了解轴承出现过早失效时确切的极限运行条件[6]。
目前已经明确了白蚀裂纹导致过早失效的几个因素[4]。SKF设计了不同的试验方式来验证轴承解决方案的稳定性。在SKF所用的试验台上,通过加载高强度拉应力来模拟过早失效 [7] 。在实际应用中,配合不当、轴的径向跳动或轴承位变形,都可能会产生高强度拉应力。在该试验台上,轴承安装在人为加工成有波度的轴上,从而使得滚道在波峰处产生高强度拉应力(图4)。即使在约1.5GPa的滚动接触应力下(即风电齿轮箱的正常运行条件),经过相对较短的试验时间后也会产生过早失效,其外观与在现场看到的失效非常相似(图4)。
图5中的柱状图显示,6个SKF DuraPro风电齿轮箱轴承在相同条件下进行了测试,无一失效。所有试验至少进行了1,600小时。采用标准轴承钢和热处理过的轴承平均在运行178小时后失效(图5)。
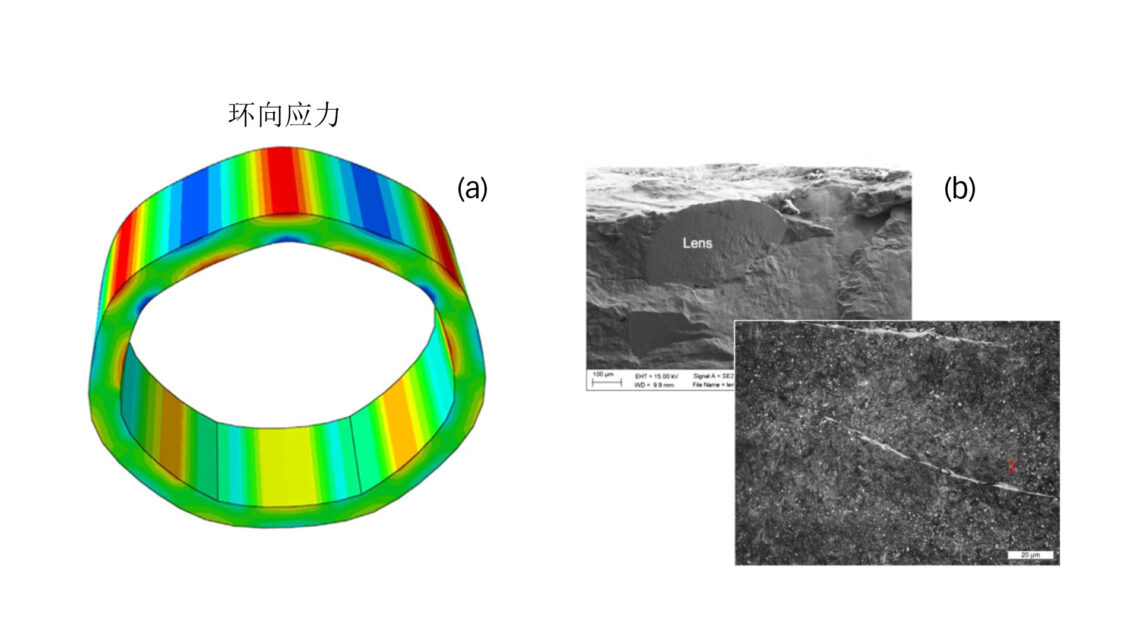
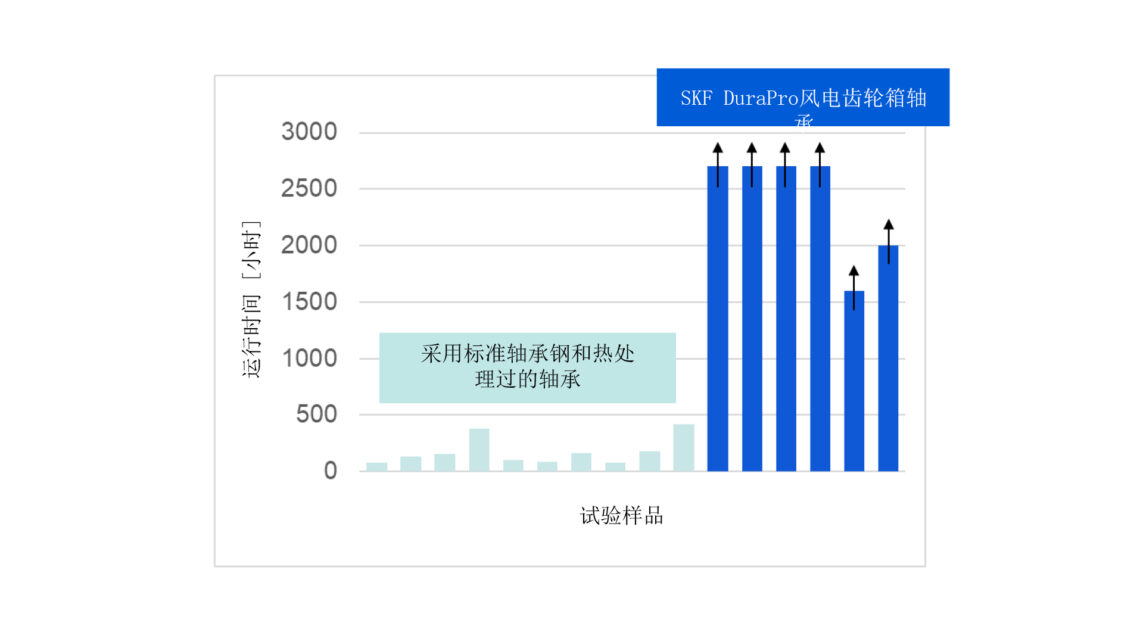
SKF DuraPro风电齿轮箱轴承的新额定寿命模型
风电行业要求使用ISO/TS 16281:2008来评估轴承额定寿命[10],但ISO/TS 16281:2008和ISO 281:2007不允许使用最新的轴承解决方案提供的轴承计算寿命。因此,SKF开发出一种新的方法,将SKF DuraPro风电齿轮箱轴承的性能加入 ISO/TS 16281:2008修正后的额定寿命计算中,把额定动载荷的增加和寿命修正系数αISO的增加结合起来考虑。
根据 ISO 281:2007,αISO计算如下:
如Ioannides等人论文[11]所示,在αISO中添加适当的特征系数,以便在ISO模型中体现先进的热处理和改进表面光洁度的有利影响。为了体现SKF DuraPro风电齿轮箱轴承的性能改进,将反映Explorer的影响系数Ψbrg和反映改进钢材和热处理的附加影响系数ΦHDB加入 αISO 中:
根据前面介绍的耐久性试验,可以确定并调整 Ψbrg 和 ΦHDB的函数关系。
SKF DuraPro风电齿轮箱轴承的表面和次表面材料特性得到改进。因此, SKF 通用轴承寿命模型 (GBLM) [8]最能真实地反映其性能的提升,该模型将表面影响和次表面影响分离开来(见图 6)。 SKF 通用轴承寿命模型的基本公式可以写为:
公式中由体积积分表示的次表面项可以使用成熟的滚动接触疲劳方法求解[8]。 由面积积分表示的表面项则说明了与表面疲劳相关的失效模式。表面项在SKF 长寿命风电齿轮箱轴承的应用中,还包含了提高表面强度的轴承设计特征的计算模型。这种方法已经成功地应用于混合陶瓷轴承的额定寿命计算 [9] ,并将推广到越来越多的SKF产品中。
一旦根据上述寿命试验确定了新额定寿命模型的不同因素,便可以评估 SKF DuraPro风电齿轮箱轴承的额定寿命。
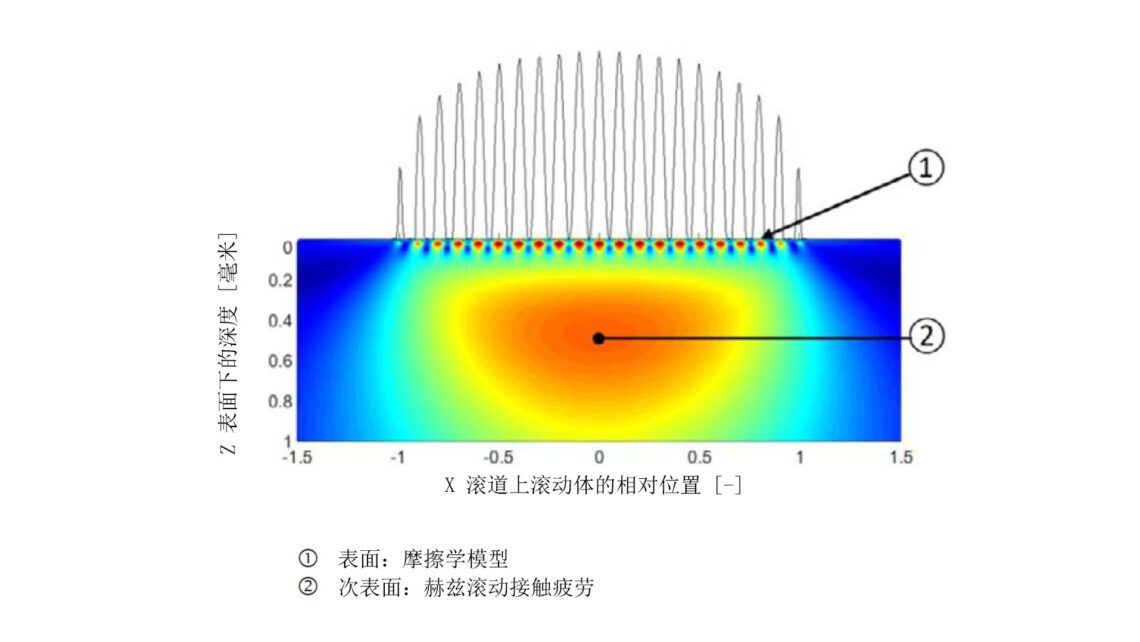
针对SKF DuraPro风电齿轮箱轴承,修正的ISO/TS 16281:2008额定寿命和SKF 通用额定寿命模型的更新和验证过程已成功通过挪威船级社DNV审核。
轴承额定寿命的延长取决于实际运行条件。图 7显示了在典型齿轮箱中,不同级轴承平均寿命延长的几个计算实例,这些寿命都延长了四倍以上。由于表面和次表面性能的整体改进,在多种运行条件下都能显著延长额定寿命。
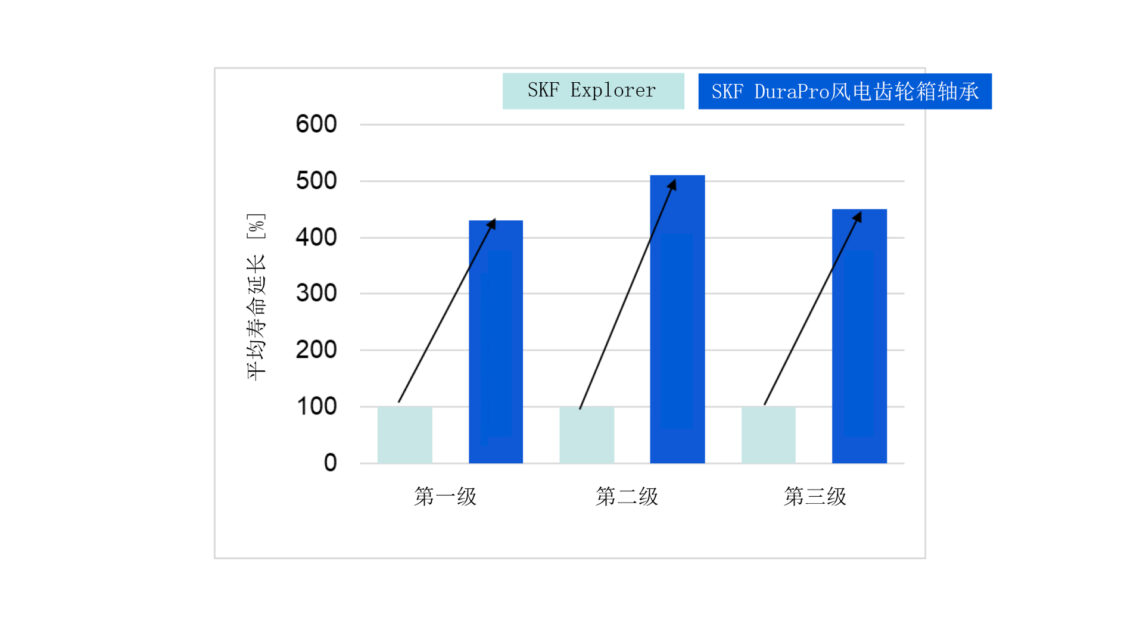
SKF DuraPro风电齿轮箱轴承是如何提高扭矩密度的呢?
支承行星轮的轴承尺寸往往决定了行星轮的最小尺寸。因此,若能减小该轴承的尺寸,将直接影响行星轮的尺寸,进而影响齿圈的尺寸,最终影响齿轮箱的扭矩密度。
本节通过一个应用案例来展示SKF DuraPro风电齿轮箱轴承如何在不影响轴承额定寿命的前提下,通过缩小行星轮轴承尺寸,为提高扭矩密度创造有利条件。本案例基于一个先进的6兆瓦风电齿轮箱,它由4列圆柱滚子轴承支承,外圈滚道集成在齿轮中。客户要求达到30年的额定寿命,并满足风电机组设计标准第4部分:风电齿轮箱设计标准(IEC 61400-4) [10] 的要求,同时外圈滚道直径要最小化。
图 8显示了如何在保持轴承额定寿命不变的前提下减小轴承尺寸。第一柱显示最初所选轴承的额定寿命。第二柱显示如果将此轴承更换为SKF DuraPro风电齿轮箱轴承后额定寿命的增加。第三柱显示使用SKF DuraPro风电齿轮箱轴承优化轴承设计后的额定寿命。在这里,外圈滚道直径减少了25%,从460毫米减少到350毫米,而额定寿命仍然满足客户的要求。
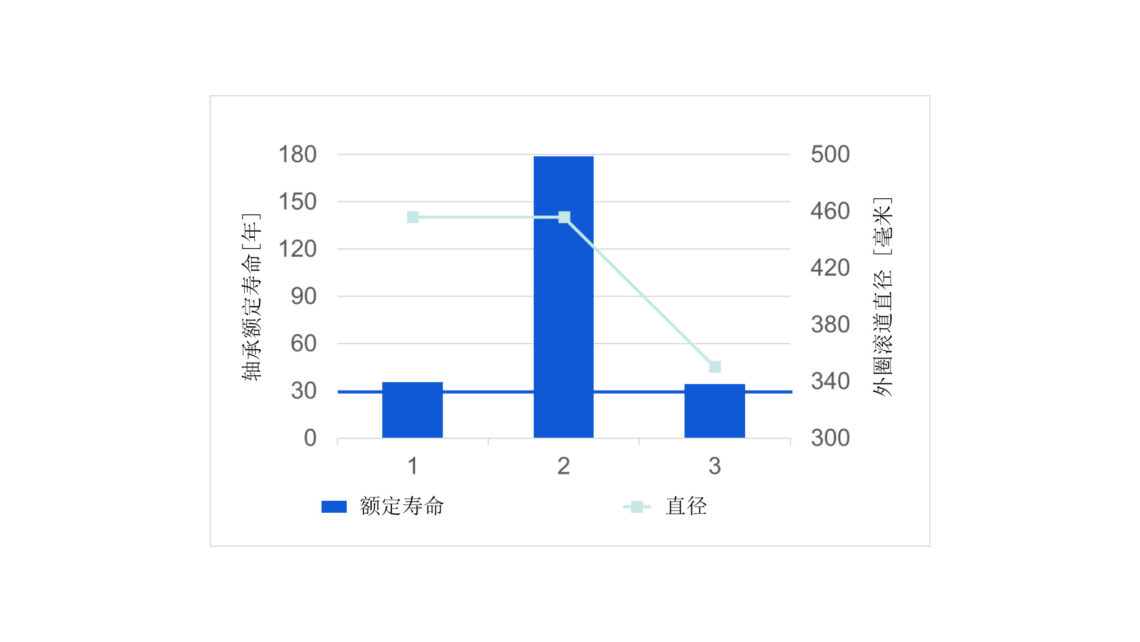
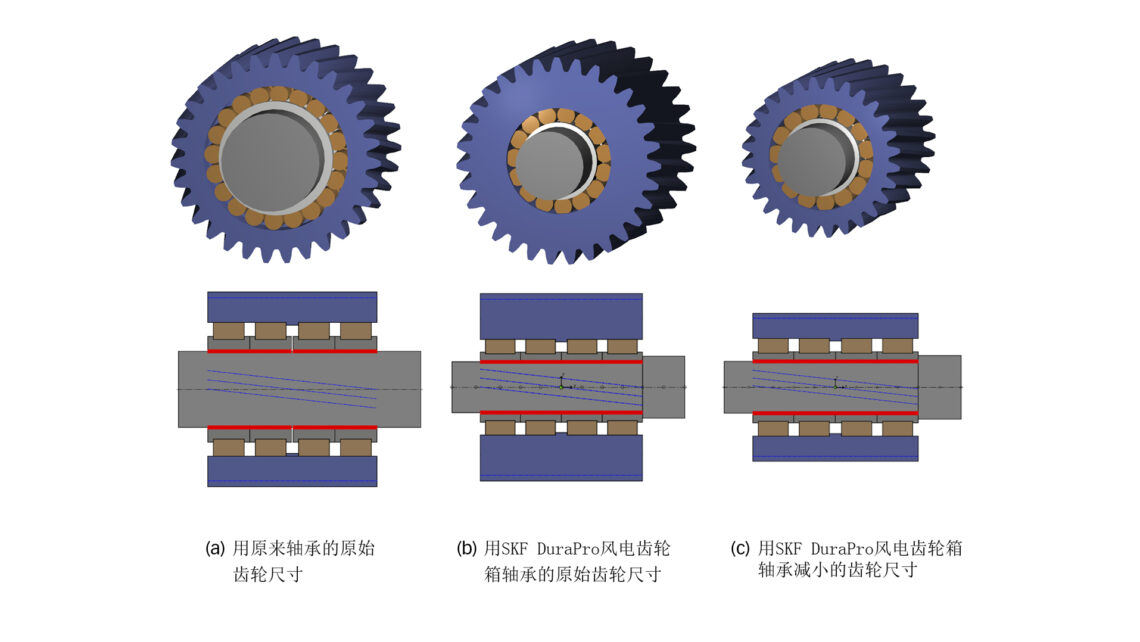
在齿轮箱的不同位置可实现类似的尺寸减小:
- 根据不同的齿轮级,齿轮箱制造商对减小尺寸的要求集中在减小直径或轴承宽度(主要针对高速轴)。
- 在高速轴上,使用SKF DuraPro风电齿轮箱轴承来减小尺寸将有助于降低与打滑损伤相关的风险,其中滚子的惯性起着重要作用。
结论
SKF DuraPro风电齿轮箱轴承采用的优化轴承钢和热处理工艺带来了以下业已证实的好处:
- 表面和次表面疲劳寿命延长至原来的5倍,从而在相同载荷下,可将轴承和齿轮尺寸缩小 25%。
- 满足不断提高的设计可靠性要求和 30 到 40 年的设计寿命要求,轴承额定寿命水平处于行业前沿,轴承额定寿命的延长已加入ISO/TS 16281:2008的修正计算方法中,不久也会加入到SKF 通用轴承寿命模型计算方法中,并成功通过了挪威船级社DNV审核。
- 针对风电齿轮箱的恶劣工况提高了稳定性,从而增加了运行可靠性。
此外,SKF DuraPro风电齿轮箱轴承凭借更高的稳定性,能够减少风电齿轮箱轴承常见的失效现象,从而减少风电机组的非计划停机和维修费用。提高风场运行的可靠性是一种避免轴承过早失效的解决方案。