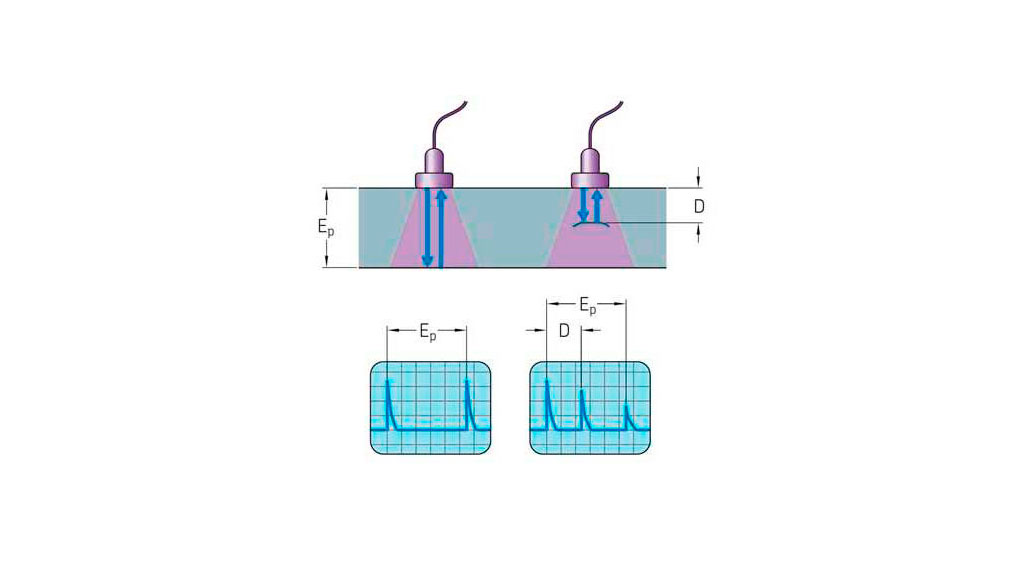
SKF无损检测
SKF借助多种无损检测方法,确保达到符合公司规范要求的高质量水平。
概要
SKF在整个制造过程中实施检测,并致力于保持检测的高可靠性,从而确保制造和修复质量。无损检测是重要的关键检测技术,SKF正不断努力对其进行改进,并实现标准化和技术进步。SKF无损检测可靠性的提高离不开性能优异的设备、详细的规程、训练有素的操作人员和高度自动化。SKF也已准备好充分利用SKF轴承制造全过程中的无损检测测量数据的数字化所带来的新机遇。
如今,SKF在制造、修复和运行中检查等过程中采用现代无损检测技术,以确保产品完整性和可靠性,控制制造过程和降低生产成本,并确保质量水平始终符合SKF规范要求。SKF集团技术开发部(GTD)下辖的质量技术(QT)小组,专注于SKF各工厂所有质量检查工作的标准化和发展。无损检测是该小组推动SKF生产标准化的一个重要领域。
无损检测技术
无损检测可以被定义为在不影响正常使用的情况下,检查、测试或评估材料、部件和组件在材料特性上的不连续性或差异性的过程。换句话说,当完成检查或测试后,部件仍可继续使用。
无损检测方法利用电磁辐射、声音传播和材料固有特性等物理现象,来检查轴承部件等固体试样。无损检测方法有很多种,最常见有:
- 超声波检测
- 电磁检测(涡流检测)
- 磁粉检测
- 射线检测
- 液体渗透检测
- 目视检测
- 声发射检测
- 热/红外检测。
在这些方法中,轴承制造业最常用的是超声波检测和涡流检测这两种技术。以下对它们做详细介绍。
超声波检测
超声波检测是基于超声波在被测物体或材料中传播特性的无损检测技术。在最常见的超声波检测应用中,把中心频率范围为0.1至20兆赫的极短超声脉冲波发射到材料内部,以检测内部缺陷或对材料进行表征。
在实践中,把与诊断仪器相连的换能器与部件接触,从而把超声能引入被测部件。这种换能器的关键零件是压电晶体,它把电能转换为机械能,后者在被测材料中以声音脉冲的形式传播[1]。
这些脉冲在材料不连续的地方发生反射,如炼钢过程中形成的夹杂物和孔隙处等(图1)。
图2列出了换能器的基本零件,以及所得到的声场,此处由声波在水中传播的声压场表示。
涡流检测
涡流检测是无损检测使用的众多电磁检测方法之一,它利用电磁感应来检测和表征钢和铝等导电材料的表面和近表面缺陷。
涡流检测[2]的原理如图3所示。涡流是通过电磁感应现象产生的。当交变电流被施加到铜丝等导体上,会在导体内部和周围产生磁场(a)。在交变电流上升到最大值的过程中,磁场会扩大,在电流减小到零的过程中,磁场会缩小。如果把第二个电导体靠近这个变化的磁场,在该第二导体中就会感应出电流,这种沿着圆形路径(b)流动的感应电流就是涡流。
被测物体的电导率和磁导率的变化以及缺陷的存在,会引起涡流变化,此时可用与探针(c)相连的仪器测量涡流相位和振幅的相应变化。
在制造工艺的各个阶段,SKF使用涡流检测技术对半成品和成品轴承部件进行检测,以表征材料特性,并检测靠近表面的缺陷,如硬加工操作中产生的裂纹和热损伤。
SKF制造中的无损检测
SKF在原材料阶段就努力保证质量。SKF与供应商合作,以确保所有采购的原材料都符合SKF要求。自动化的100%在线无损检测是这些要求的重要组成部分。
SKF的绝大多数无损检测贯穿整个制造工艺。SKF遵守使用SKF轴承的各行业(如航空和铁路)规定的所有行业规范。图4展示了一台对铁路车轮和轴箱轴承进行100%在线检测的设备。
随着客户对可靠性提出更高的要求,汽车和可再生能源等其他行业也越来越多地要求采用无损检测。对于风力发电机所使用的轴承,SKF拥有自己的标准。
修复和先进回用分析
使用中或在试验装置上进行耐久测试的轴承,可以使用各种无损检测方法进行检测。这是为了能更好了解轴承失效根源和轴承退化机制。如果是轴承修复检查,则是检查表面下损伤,查明轴承部件是否还能继续使用。
作为这种失效分析的一部分,SKF使用超声波检测检查表面下疲劳裂纹。图5(左图)显示的超声波C型扫描图像展示了来自轴承滚道圆周附近的表面下裂纹所反射的超声波能量。在进行切片和显微镜检查后,可以把实际表面下损坏与超声信号关联起来,如图5(右图)所示。
自动与手动无损检测
SKF正努力在制造过程中实现高度自动化的无损检测,这样做旨在提升检测的可靠性。多项研究已经证实,即便具有详细的过程说明和熟练的操作人员,所有手动检查都会受人为因素影响而造成较低的生产力[3, 4, 5]。
所有的无损检测方法在本质上都是基于统计分析,它们检测缺陷的能力以概率表示。因此无损检测没有确定性,只有概率。除了检测出存在的缺陷的概率外,还必须考虑没有缺陷但却误报缺陷的概率(即错误拒绝)和未检测出存在的缺陷的概率(即错误接受)[6]。
无损检测方法的可靠性可以表示为,在特定条件下,对于检测一个限定部分中特定尺寸缺陷的能力的定量统计度量。无损检测方法的可靠性取决于许多因素,包括是手动还是自动检测、设备性能和操作者的技能。制造工艺中的无损检测过程的可靠性可用检测概率曲线(POD)来表示。图6显示了检测概率曲线的原理。图7显示了SKF改进检测概率曲线和无损检测技术可靠性的目标,具体实现方法是实现自动检测、培训娴熟的操作人员、制定清晰的操作规程,以及采用高性能设备。
数字化
数字化是把能实现数字化的一切事物都转化成数字以及把信息转换成数字格式的过程。在SKF的制造工艺中,数字化是工业转型(被称为工业4.0)的一部分。在整个制造过程中实施的无损检测所得数据的数字化,也为这种转型提供支持。
传统上,无损评估(非破坏性评估)数据通常在检测完成后随即被丢弃,这样就无法了解零件是如何随时间变化的。即便保存了数据,通常由于缺乏互连性,很难把单个数据纳入零件的完整数据中[7],更难以利用从数据获得的知识改进制造工艺。互联互通的数字检测数据将为轴承制造带来新的机遇,例如实现生产过程的快速反馈和控制。
建模
为了加快开发,并减少耗费资源和时间的物理检测,SKF正着眼于使用无损检测专用的分析工具和仿真。图8的例子是对一个轴承圈的声场压力建模所获得的结果。
SKF与世界一流的外部伙伴合作
为了确保获得无损检测领域的最新进展,SKF不断评估与顶尖大学、研究机构和供应商合作的机会。
其中一项举措是SKF为无损评估研究联盟(RCNDE)[8]提供资助。该联盟是工业界与学术界成功合作的一个典范,它的另一个赞助者是英国工程和物理科学研究委员会(EPSRC)。该联盟的成员包括石油和天然气、航空航天、核能和制造等领域的国际工业企业,以及英国的多所大学,如曼彻斯特大学、伦敦帝国学院、诺丁汉大学、华威大学、斯特拉思克莱德大学和布里斯托大学。这些大学除了开展核心研究项目,解决行业常见的一般性难题,还就SKF面临的具体挑战进行针对性研究。
SKF最近还与新加坡先进修复技术中心(ARTC)签署了会员合作协议[9]。这个中心在技术准备水平为4至6(即相关环境中的新技术)的制造和修复技术的开发方面为SKF提供支持。该中心的核心实力是开发用于修复部件的产品验证和制造检验的无损技术。
SKF还是瑞典钢铁工业的分支机构Jernkontoret的成员[10]。Jernkontoret的一个研究委员会专门研究无损检测。该委员会的职责是发起和指导无损检测研究项目,这些项目由瑞典政府机构资助,在瑞典大学和研究机构开展。
参考文献:
[1] ASNT Handbook Non-destructive testing Volume 7 – Ultrasonic testing, 2007
[2] ASNT Non-destructive testing Handbook Volume 5 – Electromagnetic testing, 2004
[3] Marija Bertovic Human Factors Approach to the Acquisition and Evaluation of NDT Data, 18th World Conference on Non-destructive Testing, 16-20 April 2012, Durban, South Africa.
[4] Harris, D. H. and Chaney, F. B. Human Factors in Quality Assurance. (1969). New York, John Wiley and Sons.
[5] Drury, C. G. and Fox, J. G. Human Reliability in Quality Control. (1975). London, Taylor & Francis, Ltd.
[6] Guidelines to Minimize Manufacturing Induced Anomalies in Critical Rotating Parts, DOT/FAA/AR-06/3 – AIA Rotor Manufacturing Project (RoMan) Report October 24th, 2006.
[7] S. Holland, E. Gregory, T. Lesthaeghe Toward Automated Interpretation of Integrated Information: Managing “Big Data” for NDE, ASNT Research Symposium 24 March 2014.
[8] Research Centre in Non-Destructive Evaluation. https://www.rcnde.ac.uk/
[9] Advanced Remanufacturing & Technology Centre, Singapore. https://www.a-star.edu.sg/artc.
[10] Jernkontoret http://www.jernkontoret.se/en/research-education/.