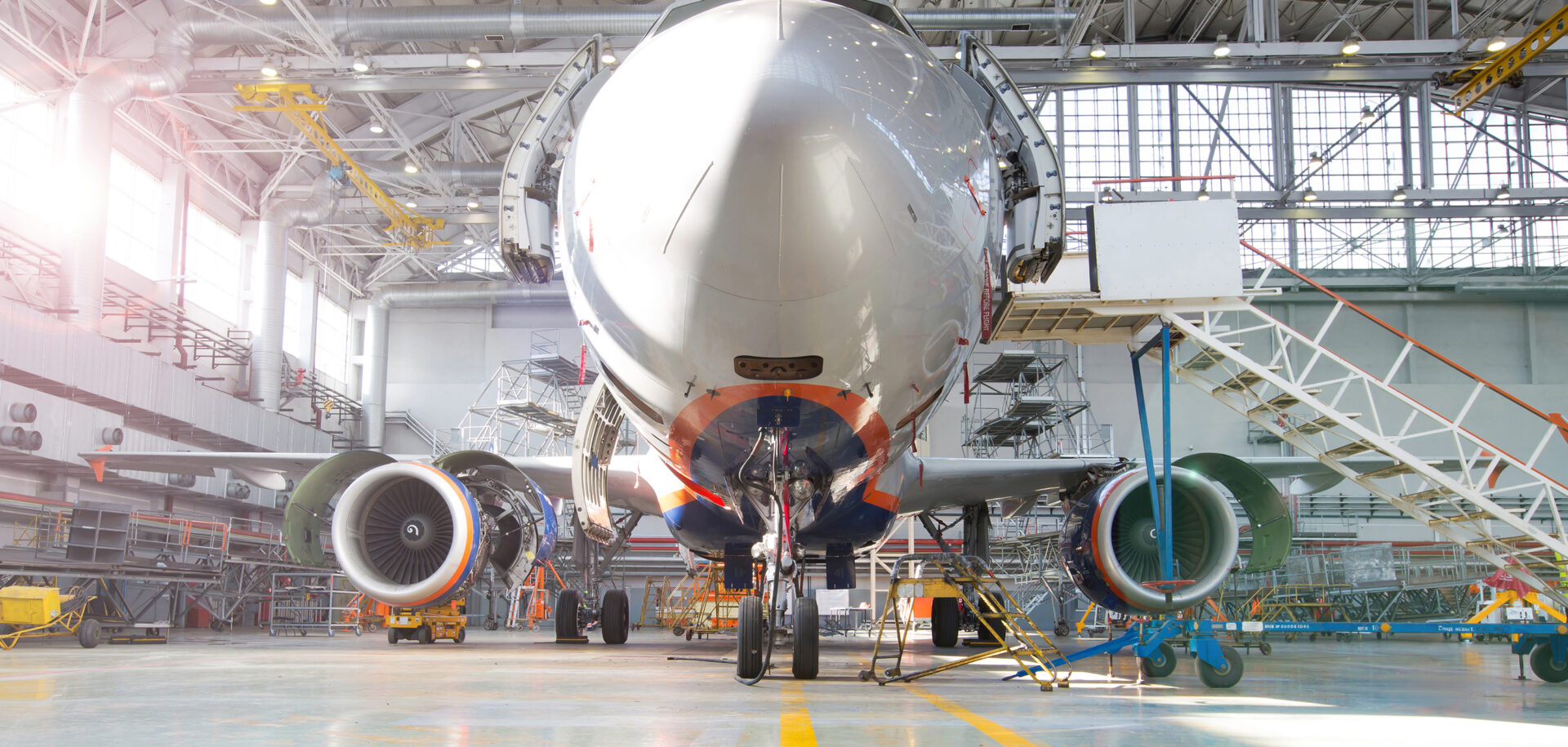
SKF黑色设计
目前,如何减轻重量可谓航空航天业面临的一大挑战。在竞争激烈的市场中,提高性能或减少排放能够为制造商赋予重要的优势。复合材料的应用为所有这些领域创造了大好机会。
当涉及到接口零件时,通过采用复合材料来减轻重量是一大挑战,原因在于平面外负荷的影响。为了避免成本增加,功能集成必不可少。SKF解决方案有助于实现这些目标,这要归功于两项面向未来的主要技术 —— SKF黑色设计和SKF轴承集成。
1. SKF黑色设计是指使用纤维增强材料制造高性能、承受平面外负荷的零件。复合材料技术一旦能够成熟地应用于接口零件中,通过这种轴承的功能集成,它将开创一个新的应用领域。
2. SKF轴承集成可高效地将轴承嵌入复合材料部件中,采用的方法是为滚动轴承外圈提供功能强大的接口,或将球面滑动轴承集成到复合材料轴承座中。
复合材料技术能够解决多种问题:
- 将现有金属部件整合成一个复合材料解决方案,从而减轻其重量
- 实现传感器解决方案等新功能的功能集成
- 解决周期性承载零件的疲劳问题
- 使用耐受腐蚀性环境的材料,以避免腐蚀
- 通过提高刚度、转移重心或嵌入减振系统,从设计上降低噪音和振动
重点之一:采用SKF黑色设计,开发复合材料结构件
SKF黑色设计挑战重力
借助此技术,能够设计和制造嵌入复合材料的结构接口零件。在飞机制造业中,复合材料的用量急剧增加,然而传统的设计技术只能带来结构性能上的有限改进。这限制了可以使用复合材料解决方案的应用场合。SKF成功克服技术挑战,制造出轻量化、高性能的复合材料零件,替代传统的金属结构接口零件。多年研发取得的这项成果被称为SKF黑色设计。SKF改变了复合材料零件工程设计的范式,从而取得了这一卓越成果。
在复合材料而非金属中采用传统零件设计(“黑色金属”方法)只会使性能略有改善,零件仍存在易于开折和分层的缺陷。而在SKF黑色设计中,将基底(树脂)材料用于能发挥其最佳性能的条件下,即处于压缩状态下。为了实现这一点,SKF工程师开发出全新形式、形状和零件几何形状,旨在确保在承受平面外负荷的区域,树脂在整个层压厚度上保持压缩状态。
这提高了抗剪切应力,消除了开折效应。使用半球形垫圈以避免复合材料的任何穿孔倾向,同时实现了压缩状态,这是实践证明可以显著提高零件强度的一个出色解决方案范例。
这些设计还加入了复杂的波纹形状,并仔细平衡了散状和连续增强材料的使用。SKF复合材料中心运用这些工程知识,为合作伙伴提供帮助。
飞机减重的目的是降低油耗和对环境的影响,最新一代商用飞机中复合材料的用量增加了50%。然而,复合材料零件采用传统设计得到的结构性能制约了这种材料在飞机中的更广泛应用。SKF黑色设计将现有碳纤维增强复合材料(CFRP)与创新设计技术相结合,从而获得了所需的结构性能。SKF黑色设计拓展了复合材料解决方案的应用范围,使其适用于一些结构件,与当前的金属解决方案相比,其质量成本比颇具竞争力。
航空航天业中最常用的复合材料通过堆叠预浸碳纤维层而制成。树脂能够传递纤维之间的负荷并确保各层之间的黏合。这项技术适用于机身、机翼、机架和桁条,因为层压板主要承受平面内负荷。
对于这些几何形状,碳纤维在纤维方向上提供了较高的强度和刚度。然而,在垂直于纤维平面的方向上,材料的机械性主要由树脂决定。树脂是粘合剂,与碳纤维相比强度较差(约是碳纤维强度的1/50)。因此复合材料的使用仅限于承受平面外负荷的结构件,如T形配件和夹板等结构接口零件(图1)。采用传统几何形状,金属配件和夹板容易出现折叠/开折现象。在形状相同的复合材料配件中,由于树脂中存在层间应力,相同的负荷模式可导致90˚角处的碳纤维增强复合材料层分离。这种现象称为分层,在非常低的负荷水平下发生,可导致零件不可用。
复合材料行业已研究了3D编织和高性能树脂等新技术,并结合传统零件几何形状(“黑色金属”方法),力求解决此问题。然而,这种方法在机械性能和成本竞争力方面表现出了明显的局限性。
SKF黑色设计的另一种应用
SKF黑色设计建立在多个理念的基础之上,通过调整零件几何形状来解决平面外负荷的难题。
第一个理念包括设计部件的几何形状和层片叠压,以使零件在应用场合中承受负载时,保持树脂的压缩状态。树脂在压缩状态下可承受的应力要远远大于拉伸状态,而且压缩状态也能改善树脂的剪切应力能力。纵观整个土木工程史,这种设计理念通常用于拱门、桥梁等结构,要求结构部件保持受压状态。
图2显示了树脂在拉伸状态下强度之弱,以及压缩状态对树脂剪切应力能力的影响。
SKF设计出半球形垫圈和碳纤维基底,在结构配件上将这一理念付诸实践。这种设计自然地会在平面外负荷区域压缩树脂(图3)。而且,局部压缩程度随零件负荷的增加成比例增加,这有助于解决90˚角处的分层问题。
在拉力作用下(图4),半球形垫圈对碳纤维增强复合材料局部施加压应力,从而使树脂保持压缩状态。
在压缩状态下(图5),基底呈夹紧形状,局部压缩碳纤维增强复合材料。基底允许根据应用场合的尺寸和安装要求来调整配件底座的几何形状。
因此,半球形垫圈和配件基底互相配合,在垂直于安装平面施加的拉应力和压应力(即平面外负荷)下都能使树脂保持压缩状态。配件的失效不是由树脂的机械性能所决定的,因此SKF黑色设计配件能够在给定的几何形状和重量条件下实现更高的机械性能。
SKF黑色设计的第二个理念包括使用特定形状,使配件具备机械稳定性和刚度。圆形形状可以防止相对尖锐的90˚角,例如金属配件中的夹角。圆形形状将碳纤维沿适当方向对齐,以推迟开折现象的发生,为配件赋予机械稳定性和刚度。这个理念适用于夹板,且优势明显(图6)。
此外,以上SKF黑色设计理念可以在一个接口零件中组合使用。例如,使树脂保持压缩状态的理念以及特定的加强形状均可应用于T形配件的设计,如图7所示。此外,以上SKF黑色设计理念可以在一个接口零件中组合使用。例如,使树脂保持压缩状态的理念以及特定的加强形状均可应用于T形配件的设计,如图7所示。
为了验证这些理念,在拉伸和压缩测试台上对缩小尺寸及全尺寸夹板和配件进行了测试,如图8所示。
这些理念的发展引发了对不同复合材料结构接口配件的研究和验证。SKF将结果与等同的金属结构配件进行了比较。与具有相同机械性能的金属部件相比,采用SKF黑色设计的复合材料解决方案可减重40%以上。
结论
SKF黑色设计实现了轻量化、高性能结构接口件的设计和制造,这些由碳纤维增强复合材料制成的零件为特定应用场合而设计,以支撑平面外负荷。SKF正在开发机械模型和数字仿真工具,以便对航空航天业的复合材料结构配件进行通用设计和分析。
重点之二:轴承集成
SKF的这项技术能够将轴承直接集成到复合材料结构件中。SKF作为滚动轴承和滑动轴承设计和制造领域的全球领导者,能够生产复合材料结构的接口零件是SKF专业能力自然而然的发展。SKF正在开发接口解决方案,以在复合材料零件中创建嵌入式接头。该接头可以是球轴承、滑动轴承或球面滑动轴承,具体取决于应用场合的要求。
两种系列的接口解决方案正在开发中:
- 采用专有解决方案将滚动轴承高强度集成到复合材料结构中,以创建可靠的接口,适用于宽温度范围、重载和高速应用。
- 内圈与复合材料表面直接滑动接触,主要用于球面滑动轴承,以及在磨损、摩擦和可靠性方面具备高性能的解决方案。
这些技术具有突破性和颠覆性:它们可在服役环境中提供显著的减重可能性,而且还提供了接头的集成,因为模具内作业省去了模制后的步骤并简化了制造过程。
功能集成的优势
在减重方面,推广高性能复合材料的使用经常遇到成本障碍,在分散部件层面实施这种改变时尤其如此。
为了应对这种影响,系统的整合现在成为一种公认的解决方案。由于省去了装配步骤而且整合了制造次数,因而可显著降低初始成本。然而,如果不将其推向更高层次,这种方法很快就会遇到限制。
如果整合只是单纯将所有部件集中在一起,各个部件仍保持相同的性能级别,往往会导致复合材料的潜力利用不足、材料浪费和不必要的高成本。一种更有效的方法是综合考虑单个部件的性能、成本、工艺和应用可能性的各个方面。
以刚度为例,若要实现各个部件所需的刚度,可能需要在某些部件中广泛使用碳纤维,而在其他部件中,使用玻璃纤维就足够了。这会导致更高的材料成本,甚至可能使功能集成变得不可行。然而,如果能重新分配系统刚度功能,则可以找出与系统性能匹配但成本较低的分布方式。该方法可将诸如刚度、质量和阻尼等多种功能的要求合并,实现优化设计。
这正是SKF黑色设计功能集成的优势:基于复合材料的功能集成,实现最佳系统性能。