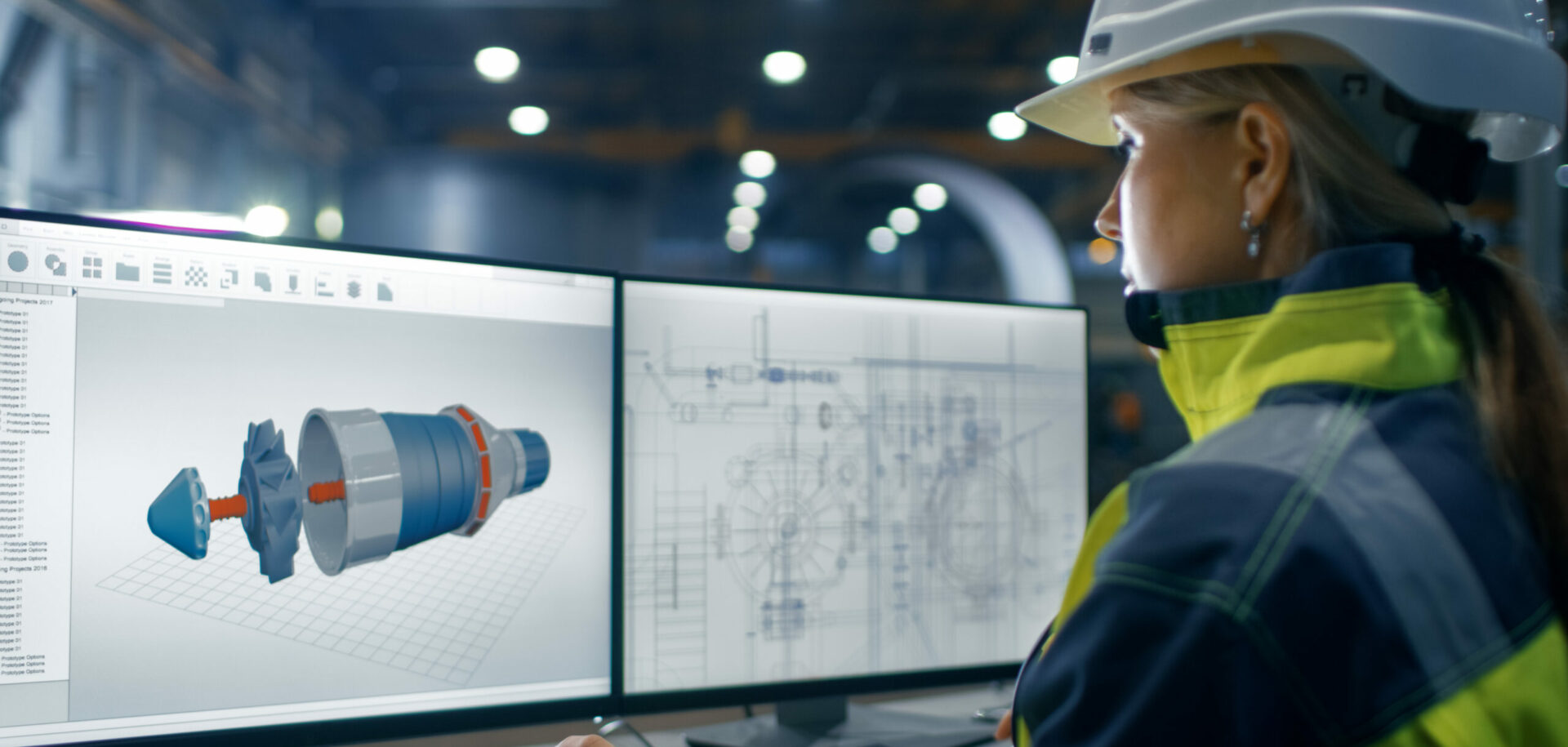
At the boundary between lubrication and wear (part 1)
To be continued in the next issue of Evolution.
Summary
For more than 100 years, researchers have looked at the factors that contribute to successful bearing operation through lubrication. We now know that the lubrication film required for good lubrication characteristics is extremely thin when compared with the roughness of the surfaces that are being separated. To ensure that moving surfaces can work in a stable mode without wear or spalling, running conditions have to be ideal for each point on the lubricated surfaces at all times. This means that lubrication analysis has to take place at the actual region of contact between surfaces, elastically and plastically flattened to take a load. This is the asperity level.
It is not possible to predict the behaviour of a lubricated, elastically deformed region just by knowing the mean oil thickness and the mean contact pressure.
It is also necessary to know the local pressure, temperature, shear stress and lubricant rheology.
New evidence shows that good lubrication of gears and bearings requires only a very thin layer of lubricant separating the moving surfaces.Recent experiments with very smooth ball bearings have shown that a separating oil film is present between each of the balls and rings, even when the calculated oil film thickness is much lower than the combined root mean square roughness of the lubricated surfaces. This indicates that calculated oil film thickness can be 20 times smaller than the peak-to-valley roughness of the surfaces, and still the surface roughness peaks do not penetrate the oil film.
Attempts to understand the behaviour of lubricated bearings have been going on for more than 100 years. Before Beauchamp Tower published his findings regarding pressure distribution in journal bearings, it had been assumed that the pressure was constant and equal to the load divided by the projected bearing area, just as if the journal had been floating on a 180° hydrostatic bearing.
Later work allowed the calculation of real pressure distribution for simple bearing geometries, analysis of the lubrication of gear teeth and elastic deformations of lubricated surfaces. Gradually this type of analysis was refined to give accurate calculations for both complex geometries and different types of mathematically described rheologies for lubricants.
At least two different size scales are important to the behaviour of the lubricated contact – the size of the macro-Hertzian contact and the size of the asperities on the surface. The macro-Hertzian contact size combined with the surface velocities gives the time available for compression of the asperities and their re-emergence into the oil film during passage through the Hertzian contact. The size and height of each single asperity gives information about the local pressure variation and pressure gradients. This, in turn, provides insight into local shear stresses in the lubricant when the motion of the surfaces and the lubricant film thickness is known.
When bearings and gears are run, occasional surface peaks penetrate the oil film and make direct metal-to-metal contact. This results in high local stresses, and controlled wear or plastic deformation at the asperity level takes place until the surfaces are run-in and separated by a continuous lubricant film. This run-in state is only valid for one specific running condition, where the highest asperity tops just stop touching each other through the oil film.
If the load or speed is changed, new asperities will come into contact and require some more running-in before the surfaces are totally separated by a continuous oil film again.
Non-smooth surfaces
Computer modelling of elastohydrodynamic, EHL, lubricating films and dry contacts is now possible down to the level of single surface roughness asperities, using power computers and modern numerical techniques.
It has become evident that, just as for dry contact, the Newtonian lubricant models produced very spiky pressure distributions. In fact, the variation in pressure became almost a mirror image of the local roughness pattern, magnified by some orders of magnitude. The resulting surface roughness on the deformed lubricated surfaces amounted to only a few percent of the oil film thickness, reflecting the variation in the compression of the lubricant in the high-pressure region. For lubricating oils compressed into the solid glassy state, the compressibility is only 3-5% per gigapascal (GPa), giving an oil film thickness variation of the order of ± 4% for a pressure variation of ± 1 GPa superimposed on the normal elastohydrodynamic pressure distribution.
Such a spiky pressure distribution induces shear stresses in the lubricant. These are proportional to the pressure gradients and the local oil film thickness for pure rolling contacts. When some sliding motion is superimposed on the rolling, such as the kinematic sliding in deep groove ball bearings and spherical rolling bearings, high stresses in the lubricant are also induced in the direction of slip.
Elastohydrodynamically lubricated gears and bearings have, until now, shown the effect of running-in. The surface structure is changed by the running and, if that change is slow and well controlled, the surfaces will run-in until they have become smooth enough not to wear any more. To a large extent this light wear determines the functionality of the surfaces as long as the running conditions do not change. If the load, speed or temperature are changed so that the asperity tops again touch each other through the oil film, running-in will start again. The running-in continues until there is no more direct asperity contact for a given running condition, indicating that the real minimum oil film thickness between the highest roughness peaks will be very close to zero.
If the forces, stresses and/or generated temperatures during running-in are too large, the surface contacts on the asperity level will damage the surface and increase the roughness. This leads to higher local contact pressures between the asperities and to a progressively more severe contact condition, making the surfaces increasingly rough while the wear rate remains high. This results in a bifurcation point at which the surfaces can either run-in and become smooth or become rougher and rougher, depending on some small variation in one or few of the contact parameters.
When the peak-to-valley surface roughness is very much larger than the existing oil film thickness, a major part of the load on the contact will be carried by direct solid contact between the asperity tops and the opposite surface. As the reduced radius of curvature of the asperity contact is usually very small, the local asperity contact pressures will be very high and plastic deformation takes place. Such deformation is the result of high normal pressure and because of the large tangential stresses caused by tangential motion of the two surfaces relative to each other. The sharper the contact points, the lower the force needed to reach the limit for plastic deformation and the level required for break-up of the protective oxide layers on the contacting surfaces. The steeper the asperity slopes, the more difficult it is to generate a separating oil film, so large asperity slopes are bad for co-operating surfaces, both from the stress and lubrication points of view.
Heavy loads
For heavily loaded lubricated contacts, the total shear deformation of the oil in the high-pressure region gives stresses well above the limit for Newtonian behaviour of the lubricant. This means that stresses and lubricant flows in two perpendicular directions in the oil film will be coupled to each other via the limited shear strength of the oil. A pressure gradient in one direction will also influence the flow in the perpendicular direction, much the same as for dry friction between solid bodies.
By 1941, it was shown that liquids of the same type as lubricating oils transformed to solids at pressures much below the pressures found in lubricant films between the load-carrying parts of a ball bearing. These were static experiments. As the high viscosity/solid behaviour inside an EHL contact is only present for a millisecond or a fraction of a millisecond, the behaviour on that time scale is even more solid-like. This type of oil behaviour in the central high pressure part of an EHL point contact was used in calculations of oil film thickness distribution in a circular contact. To obtain computer input data, the shear strength of the solidified oil and the pressure at which it solidified is measured.
Subsequent measurements showed that typical liquid lubricant converts to glassy solids at pressures ranging from 0.5 GPa to above 2.2 GPa, depending on the temperature and molecular structure of the lubricant. As soon as the lubricant is compressed into the solid state, even very low sliding speed superimposed on the rolling speed will introduce high shear stresses in the direction of the surface sliding. These stresses, superimposed on the stresses emanating from the pressure distribution in the contact, drive the lubricant into a strongly non-Newtonian state. When the limiting shear strength of the lubricant is approached, a motion of the surfaces in one direction will directly influence the lubricant flow perpendicular to it.
This is demonstrated through the study of an oil film in a sapphire disc machine where a sliding vibration perpendicular to the rolling entrainment velocity had a major influence on the formation of the oil film. For a Newtonian lubricant, the small sideways vibration with an amplitude of 0.1 mm should have no influence on oil film build-up. However, experiments show that the central film thickness in the inlet decreased almost to the same level as the film thickness in the side-lobes of the elastohydrodynamic contacts. The oil was already non-Newtonian far out in the inlet region, causing a back-flow to occur when the sideways sliding was superimposed on the rolling motion. This means that not only the stresses but also the flow of lubricant inside the high pressure region of the EHL contact are strongly affected by the non-Newtonian behaviour of the lubricant. So, the asperity behaviour in a heavily load-lubricated contact will be quite dependent on the presence or absence of a sliding motion component superimposed on the main rolling velocity component.
If no sliding is present, the oil can behave like a Newtonian liquid, building up high local pressures on the asperity tops by squeeze motion which pushes them down and makes the lubricated surfaces conform much more than outside the Hertzian contact. The composite surface roughness of the two contacting surfaces becomes almost zero, and the lambda value (the film thickness to surface roughness ratio) becomes large. This ideal condition is quickly disturbed if some sliding is introduced between the load carrying surfaces. The sliding motion in one direction uses all of the available strength of oil in that direction. It makes it very easy for local pressure variations within the contact to push the oil down into the valleys of the surface structure, allowing the asperity tops to reach through the oil film and collide. The interaction between the surface asperity behaviour and the lubricant rheology determines the state of lubrication.
Mixed lubrication
Depending on the local rheology of the lubricant in the EHL contact and the surface structure of the contacting surfaces, the asperities will be more or less elastically deformed in the high-pressure zone by the local pressure variations. For pure squeeze or rolling motion, the shear strength of the oil is high enough to deform the surfaces elastically so that they become totally conforming and need only a very thin oil film to avoid metallic contact.
For pure sliding motion, the shear stresses in the high-pressure zone of the contact reach the lubricant shear strength. No strength is left to keep the oil from flowing out sideways from the asperity contacts and a mean oil film thickness large enough to prevent the high tops of the asperities from colliding is necessary. Depending on the details of the surface structures of the co-operating surfaces and the kinematics of the contact, a very large variation can be found in the lambda value needed to lubricate the contact without breaking through the oil film. Lambda values as high as 20 can give occasional asperity contacts, while for well run-in surfaces, lambda as low as 0.3 can stop all metallic contact.
It all depends on the lubrication of the asperities and on whether the local pressure hills can elastically make the contacting surfaces more conformable inside the Hertzian contact areas compared with the roughness they have outside the contact.
The lubricated asperity behaviour inside the Hertzian contact zone is mainly a function of the surface roughness slope, wavelength, contact pressure, rolling and sliding velocities and the time it takes for an asperity to move through the Hertzian contact. Calculations show that even when an asperity was 10 times higher than the central oil film thickness in the contact, virtually no trace of it could be seen in the converged numerical solution. The asperity built up its own pressure spike so that it was almost flattened and pushed into the surface. For a non-Newtonian lubricant model in sliding, the asperity was scraping away the lubricant and left a zero film thickness trace behind it.
To be continued in the next issue of Evolution.
Bo Jacobson,
professor of machine elements at Lund Institute of Technology, Sweden,
formerly with SKF Engineering & Research Centre
B.V. (ERC) in Nieuwegein, the Netherlands