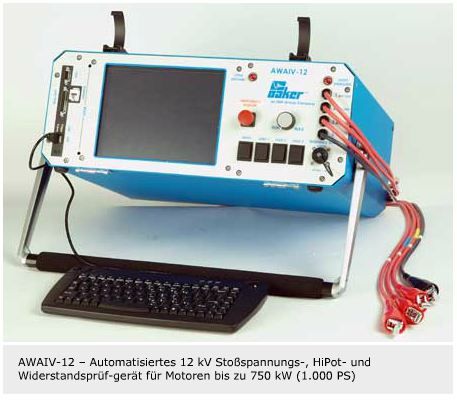
Neu bei SKF: Prüftechnik für elektrische Wicklungen
Mit der Übernahme der Baker Instrument Company stärkt SKF ihre traditionelle mechanische Stärke durch Zufügung von Kompetenzen in der Prüfung elektrischer Motoren
Mit der Übernahme der Baker Instrument Company stärkt SKF ihre traditionelle mechanische Stärke durch Zufügung von Kompetenzen in der Prüfung elektrischer Motoren
Im Juli 2006 erwarb SKFdie Baker Instrument Company, mit Sitz in Fort Collins, Colorado, USA. Diese Übernahme hat die fachliche Kompetenz von SKF außerhalb ihrer traditionellen mechanischen Basis gestärkt. Die in Fort Collins hergestellten Instrumente werden um die Theorie des Elektromotors herum entwickelt und werden an die Motorreparatur- und zustandsabhängige Instandhaltungsindustrie verkauft.
Die Baker Instrument Company wurde von Tom Baker im Jahr 1961 gegründet und hat sich zum Marktführer bei Prüfgeräten für elektrische Wicklungen entwickelt. Bakers Fachkenntnis in dieser Prüftechnik wurde aus wissenschaftlichen Arbeiten entwickelt, die J L Rylander 1926 durchgeführt hatte. Rylander entwickelte frühe Prüfverfahren, wie den Stoßspannungstest, der heute in der Industrie allgemein verwendet wird. Dieser Test misst einen Abfall in der Spannungsamplitude in Kupferwicklungen von Motoren. Wenn eine Schwachstelle festgestellt wird, wird der Instrumentenbenutzer informiert. Dadurch können Maßnahmen zur Korrektur des Problems eingeleitet werden, bevor es zu einer Arbeitsunterbrechung kommt. Die Baker Instrument Company hat die Leistungsfähigkeit der Prüfungen zum Aufdecken von Fehlern bei höheren Empfindlichkeitsstufen ständig vorangetrieben, um so die vorausschauende Natur des Stoßspannungstests zu verbessern. In einigen Wartungskreisen ist der Stoßspannungstest im wahrsten Sinne des Wortes als „der Bakertest“ bekannt.
Zustandsabhängige Instandhaltung wird weltweit in beinahe jedem Industriezweig praktiziert. Lokalisieren, Diagnostizieren und Korrigieren von Problemen sind allgemeingültige Zielsetzungen der zustandsabhängigen Instandhaltung. Die Vorhersage von Motorproblemen erfordert jedoch eine große Menge an Wissen, Erfahrung und die geeigneten Instrumente sowie ein Quäntchen Glück. Elektromotoren haben zahlreiche Komponenten einschließlich Kupferwicklungsdraht, Isolationssystemen, Lagern und andere mechanische und elektrische Besonderheiten. Diese Komponenten bilden zusammen mit Einheiten wie Antrieben, Ansaugpumpen, Kompressoren sowie weiteren Elementen die Industriemaschinen.
Gesundheitscheck für Motoren
Hier kommt die Ausrüstung der Baker Instrument Company voll zum Tragen. Die statischen Prüfgeräte können in Hinblick auf die Gesundheit der Isolationssysteme des Motors maßgebliche Ergebnisse liefern, während die dynamische Instrumentierung das Maschinengesamtsystem im Auge hat.
Das Isolationssystem besteht aus einer dünnen Schicht über einer Kupferwicklung oder einem Magnetdraht und der Erdungswandisolation, die den Magnetdraht im Inneren der Nuten im Stator eines elektrischen Motors schützt. Um ein besser abgerundetes vorausschauendes elektrisches Instandhaltungsprogramm zu erhalten, ist es wichtig, statische Tests nicht nur an der Kupferisolation, sondern auch an allen weiteren Isolationssystemen innerhalb des Motors durchzuführen. Standardisierte Tests schließen den Isolationswiderstandstest, Megohm-, Polarisationsindex (PI), Hochspannungsprüfungstest (HiPot) und den Stoßspannungstest ein. Der Isolationswiderstandstest misst den Widerstand des Kupferdrahts im Motorstromkreis, während der Megohmtest geerdete Motoren untersucht. Der Megohmtest ist auch bei der Untersuchung feuchter oder verschmutzter Motoren sinnvoll. Der PI-Test ähnelt sehr dem Megohmtest, er wird aber über einen längeren Zeitraum durchgeführt. Dieser Test schaut bei der Nutisolation nach Feuchtigkeit und Verunreinigungen. Der HiPot-Test bestimmt die Gültigkeit der Erdungswandisolation und kann auf unterschiedliche Weise durchgeführt werden. Ähnlich wie beim Stoßspannungstest wird der HiPot-Test bei einer höheren Spannung als die Betriebsspannung durchgeführt, um die Umgebungsbedingungen beim Start eines Motors zu simulieren. Drehende Ausrüstungen können bei jedem Start den bis zu fünffachen Netzspannungswert fühlen, da der Einschaltstoßstrom an dieser Stelle größer ist. Dieser Einschaltstoßstrom erzeugt innerhalb der Kupferwicklungen Bewegungen, die über einen längeren Zeitraum die Isolation aufreiben und eine Schwächung verursachen. Unentdeckt entwickelt sich eine derartige Schwächung zu einem Kurzschluss, wobei Wärme erzeugt wird, die Motorausfälle herbeiführt. Dies ist der Bereich des Stoßspannungstests. Selbst geringe Isolationsschwächen können vor einem Versagen entdeckt und rechtzeitig repariert werden, wodurch beachtliche Einsparungen möglich werden.
Auf der anderen Seite der elektrischen Prüfung von Motoren steht der dynamische Motormonitor. Seit seiner Markteinführung 1998 ist dieses Gerät aufgrund seiner nicht-intrusiven Natur und der Fähigkeit zur Ausgabe von Informationen zu einem begehrten Werkzeug geworden. In den meisten Fällen ist ein Motor Teil eines Maschinensystems, das drei Größen umfasst: die Qualität der Eingangsleistung, der Motor selbst sowie die über den Motor angetriebenen Geräte. Dieses dynamische Werkzeug kann subtile Probleme innerhalb der mechanischen und elektrischen Systeme definieren, die häu undiagnostiziert bleiben. Häu werden Motoren repariert oder ausgetauscht und wieder in Betrieb genommen, ohne dass die Grundursache des Problems erkannt wird. Wenn das der Fall ist, wird der Motor höchstwahrscheinlich auf dieselbe Art und Weise ausfallen, wodurch eine Wiederholung der teueren Stillstandszeit herbeigeführt wird. Probleme wie Oberschwingungen, Niedrig- oder Hochspannungsschwankungen, Spannungsunsymmetrie, Läuferstabprobleme, Lagerprobleme und Ausrichtungsfehler sind nur einige der Probleme, die identifiziert werden können. Alle diese Punkte können das Motorsystem negativ beeinflussen, wobei sie die Betriebskosten erhöhen und die Effizienz des Gesamtbetriebs vermindern.
Bedeutung der elektrischen Prüfungen
Ausfälle von Elektromotoren haben vielerlei Ursachen. Nach einer Studie des Electric Power Research Institutes, Kalifornien, USA, verursachen Lager etwa 41% aller Motorausfälle, während 36% die Ursache beim Stator haben. 80% der Statorausfälle gehen von einem elektrischen Problem aus und etwa 29% aller Elektromotorfehler haben direkten Bezug auf ein elektrisches Problem.
Viele Ausfälle innerhalb dieser 29% können durch periodische Kontrollen oder Überwachung des Motors vermieden werden. Ungeplante Ausfallzeiten können Kosten in Höhe von mehreren Hunderttausend Euro je Stunde verursachen, wenn kritische Motoren ausfallen. Die Vermeidung dieser Ausfälle ist das Hauptziel jedes zustandsabhängigen Instandhaltungsprogramms.
Schließen der Lücke
Mit der von Baker Instrument Company angebotenen Ausrüstung besitzt SKF ein ergänzendes Angebot hinsichtlich der Überwachung und „Gesundheitsprognose“ industrieller Kapitalanlagen. Durch die Integration dieser beiden Kerntechnologien hat der Benutzer die Möglichkeit, die Vorteile in bisher unbekanntem Maße zu genießen. Aufgrund der angebotenen Dienstleistungen oder der erworbenen Ausrüstungen werden die gesammelten Daten bisherige Verfahren übertreffen und so das Gesicht der zustandsabhängigen Instandhaltung wirksam verändern.
Die Kombination der elektrischen mit der mechanischen Technologie wird die Zukunft der zustandsabhängigen Instandhaltung stark verändern. Indem ein größerer Teil aus der Werkzeugkiste der zustandsabhängigen Instandhaltung angeboten wird, kann SKF eine Mehrzahl der Motorprobleme am industriellen Arbeitsplatz identifizieren und wird so zu einer führenden Kraft auf dem Gebiet der Betriebseffizienz.