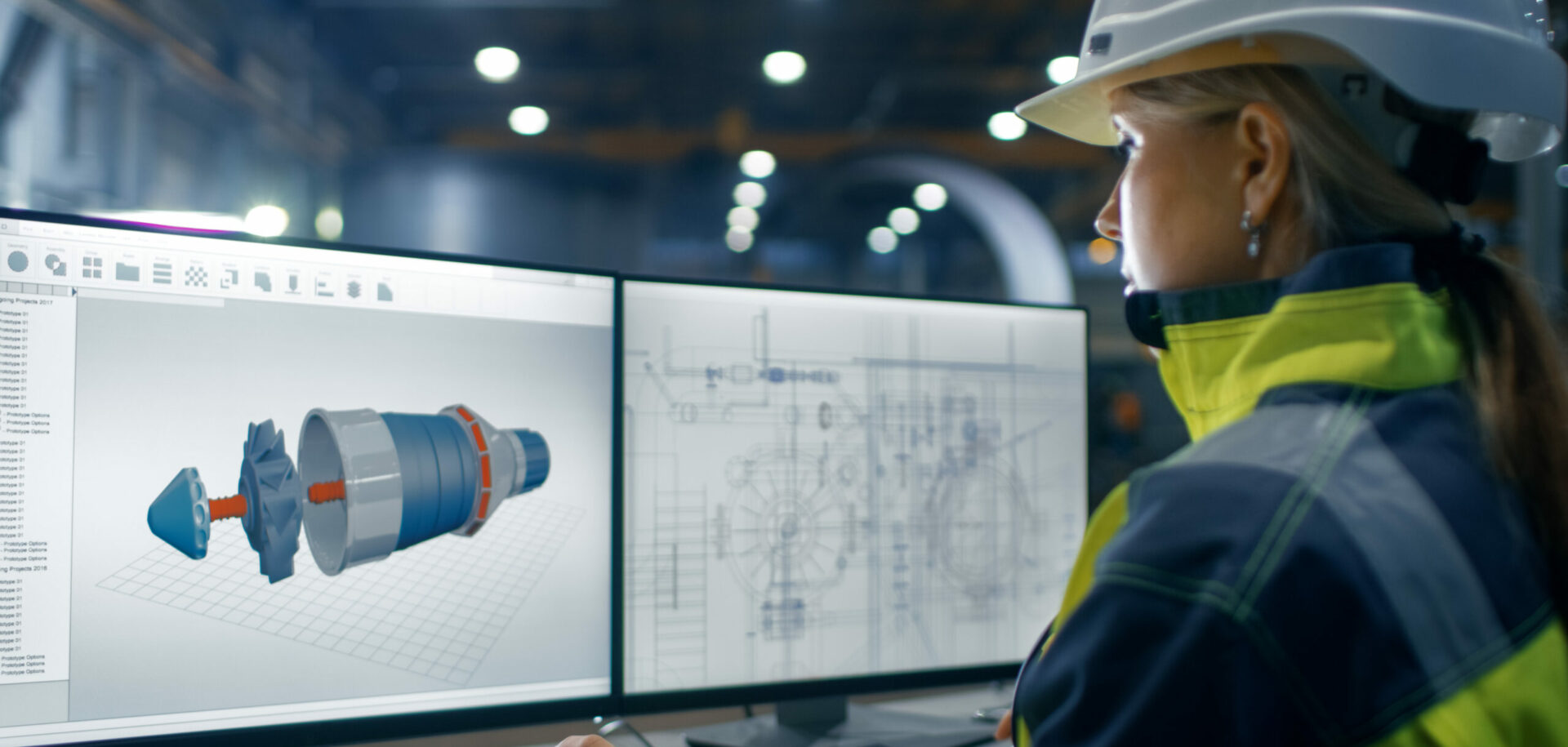
Schadensmechanismen von Eindrückungen in Wälzlagerlaufbahnen
Eindruckmarkierungen in Wälzlagerlaufbahnen sind eine bekannte Ursache für Oberflächenschäden, die eine Verkürzung der Lagergebrauchsdauer zur Folge haben. Die SKF Lagerlebensdauerberechnung berücksichtigt diese Tatsache seit vielen Jahren durch Verwendung des Verunreinigungsbeiwerts ηc. Vor Kurzem hat SKF erweiterte Modelle entwickelt und Versuche durchgeführt zur Vorhersage der Wechselwirkungen zwischen Kratzern, Eindrückungen und dem Schmierstoff auf den Laufbahnen. Diese Wechselwirkungen und der Einfluss des Gleitens werden hier ausführlich erläutert und damit wird verdeutlicht, wie der Schadensprozess seinen Lauf nimmt.
Zusammenfassung
Fakten
Im vorliegenden Artikel erläutern SKF Ingenieure ihre theoretischen und experimentellen Arbeiten auf dem Gebiet der Entstehung von Eindrückungen. Sie haben die theoretischen SKF Lagermodelle entscheidend weiterentwickelt. Die Modellbetrachtungen decken sich gut mit Versuchsergebnissen und liefern eine Erklärung für die zugrunde liegenden Ursachen von Oberflächenschäden. Somit wird auch auf die Bedeutung von Sauberkeit, sorgfältiger Lagermontage und geeigneter Schmierung zur Senkung des Risikos von Oberflächenschäden durch Eindrückungen hingewiesen.
Ansprechpartner Verkauf
Guillermo Morales
Das Überrollen von harten Partikeln kann Eindrückungen an der Oberfläche von Laufbahnen in geschmierten Roll-/Gleitkontakten hervorrufen. Es ist bekannt, dass diese Eindrückungen das Risiko von Ausfällen erhöhen. Der Ausfallprozess kann durch den Gleitanteil im Kontakt beeinflusst werden, wobei sich Zahnräder anders verhalten als Wälzlager. Um den Ausfallprozess besser zu verstehen und Vorbeugungsmaßnahmen zu entwickeln, wurde das dynamische Verhalten von Eindrückungen in hoch belasteten, geschmierten Roll-/Gleitkontakten einer eingehenden Analyse unterzogen. Die Auswirkungen von elastohydrodynamischen Drücken, Spannungen und der Oberflächenzerrüttung um die Eindrückungen herum wurden untersucht und die Schadensprognose mit Versuchsergebnissen verglichen. Untersuchungen zum Einfluss der Gleitbewegungen im Kontakt haben gezeigt, dass bei niedrigen Gleit-Roll-Verhältnissen, wie für Wälzlager typisch, der Ausfallprozess von der Abnahme der Schmierfilmdicke und einer möglichen Oberflächenzerrüttung in den Randbereichen von Eindrückungen dominiert wird, während bei hohen Gleitwerten (Zahnräder) eher ein Ermüdungsprozess aufgrund der Überlagerung zweier Druckspitzen wahrscheinlich ist.
Eine Beschädigung in der Oberflächengeometrie (z. B. durch Kratzer, Eindrückungen etc.) ist eine bekannte Schadensursache in hoch belasteten, geschmierten Roll-/Gleitkontakten. Bei diesen Kontakten herrschen sowohl elastohydrodynamische (EHD)-Schmierbedingungen als auch Mischreibungsbedingungen vor. Diese Kontakte sind in vielen Maschinenelementen anzutreffen, einschließlich Zahnrädern und Wälzlagern. Fehlerhafte Oberflächen können lokale Filmdicken- und Druckschwankungen hervorrufen, die zu Spannungskonzentrationen führen. Die aufgrund von geometrischen Merkmalen in Hertz’schen (EHD-) Kontakten hervorgerufenen oberflächennahen Spannungen wurden in der Vergangenheit von vielen Forschern mit numerischen, experimentellen und semi-analytischen Verfahren untersucht. Die derzeit in der Industrie vorherrschenden Trends zum Downsizing, zur Minimierung des Energieverbrauchs und zu immer höheren Betriebstemperaturen führen zu einer tendenziellen Zunahme der an der Oberfläche von Wälzlagern liegenden Spannungen. Geringere Filmdicken, höhere (oder sehr niedrige) Drehzahlen und hochdynamische Belastungen sind bei Wälzlagern üblich. All diese Faktoren dürften dazu beitragen, das Lagerausfallrisiko aufgrund von Laufbahnfehlern wie beispielsweise Eindrückungen zu erhöhen. Eine wichtige Rolle bei der Maximierung der Ermüdungsfestigkeit von Lagern spielt die Ölreinheit. Aus diesem Grund ist die Schmierstoffreinheit ein Eingangsparameter bei den Lagerlebensdauerberechnungen nach dem SKF Lagerlebensdauermodell [1] und der ISO-Norm 281 [2]. In einem früheren Artikel [3] wurden die Auswirkungen der Schmierstoffreinheit und ihr Einfluss auf die Lagerlebensdauer diskutiert; im nachfolgenden Text werden die Eindruckmarkierungen und Schmierbedingungen im Lagerlaufbahnkontakt genauer beschrieben.
In der Vergangenheit haben sich viele Autoren mit diesem Thema beschäftigt und dabei sowohl geschmierte als auch trockene Kontakte bei niedriger und hoher Gleitbeanspruchung untersucht; wobei sich ein recht undeutliches Gesamtbild des Ausfallmechanismus ergab. Cheng et al. [4] führten eine experimentelle Untersuchung zur Rissentwicklung im Bereich künstlich erzeugter Eindrückungen in Roll-/Gleitkontakten wie z. B. Dellen und Furchen unter EHD-Schmierbedingungen bei Gleit-Roll-Verhältnissen von S = ±0,24, d. h. S =2 (u2-u1)/(u2+u1) durch. Ergänzt wurde die Analyse durch einige numerische Simulationen mit einer nicht-Newton’schen Flüssigkeit, wobei sich zeigte, dass das Gleiten die Lage und Stärke der Druckschwankung um die Eindrückungen herum verändert; diese wird im vorderen Bereich der Eindrückung (Vorderrand) höher, wenn sich die mit Eindrückungen versehene Oberfläche langsamer bewegt als die unbeschädigte Oberfläche und umgekehrt (siehe Bezeichnungen in Bild 1). Nélias und Ville [5], Ville und Nélias [6] haben zahlreiche experimentelle Untersuchungen und numerische Simulationen von Eindrückungen in EHD-Kontakten unter reinen Rollbedingungen und Roll-/Gleitbedingungen durchgeführt. Die numerischen Simulationen bei Nélias und Ville [5] mit Newton’schen Flüssigkeiten zeigten, dass eine Zunahme der Gleitgeschwindigkeit die maximale Schubspannung unterhalb des Kontakts erhöht (bei Newton’schen Flüssigkeiten erhöht sich die Reibung mit ansteigenden Gleitwerten). Dabei wurde festgestellt, dass mit der Zunahme des Gleitanteils im EHD-Kontakt die Höchstschubspannungen unterhalb der Laufbahnoberfläche zunahmen und somit eine Verkürzung der Lebensdauer um den Bereich der Eindrückung. In Ville und Nélias [6] wurden weitere Versuche und Simulationen mit S = ±0,015 durchgeführt. Diese Versuche bestätigten frühere Schlussfolgerungen, die besagten, dass der bevorzugte Ort für die Entwicklung von Ausbrüchen von der Reibrichtung abhängig ist. Bei einer mit Eindrückungen versehenen langsameren Oberfläche kommt es eher zu Ausbrüchen am Vorderrand einer Eindrückung, während eine mit Eindrückungen versehene schnellere Oberfläche eher Ausbrüche am hinteren Rand der Eindrückung entstehen lässt. Bei reinen Rollbedingungen wird behauptet, dass sich die Ausbrüche auf beiden Seiten bilden könnten. In Versuchen mit nicht geschmierten Kontakten (Xu et al. [7]) hat man beobachtet, dass sich die Ausbrüche im hinteren Bereich der Eindrückung (Hinterrand) auf der Antriebsoberfläche zeigen; daher sind Xu et al. zu dem Schluss gekommen, dass die an der Oberfläche wirkende Reibkraft der ausschlaggebende Parameter ist, der die Entstehung von Ausbrüchen auf den mit Eindrückungen versehenen Oberflächen fördert.
Durch unterschiedliche Partikel hervorgerufene Eindrückungen
Die Form einer Eindrückung ist in Bild 2 idealisiert dargestellt. Wird ein Partikel im Kontakt eingeschlossen (sehr große Partikel werden nicht eingeschlossen und sehr kleine Partikel passieren den Schmierfilm, ohne Eindrückungen zu hinterlassen), dann entstehen unterschiedliche Formen von Eindrückungen, die von der Härte und Geometrie des Partikels als auch der Härte des eingedrückten Werkstoffs abhängig sind. Sehr große (ø) oder sehr tiefe (hp) Eindrückungen mit breiten Rändern (sp) sind am gefährlichsten. Bild 3 zeigt verschiedene Eigenschaften von Partikeln und deren Auswirkung auf Laufbahnen. Weiche oder verformbare (duktile) Partikel (aus Fasern oder Metall) hinterlassen flache Eindrückungen mit Rändern. Spröde, harte Partikel zersplittern in viele kleinere Partikel und hinterlassen eine Ansammlung von kleinen Eindrückungen. Brüchige und zähe Partikel führen zu einer großen Ansammlung von Material, das Eindrückungen auf dem Stahl und scharfkantige Ränder hinterlässt.
Wechselwirkungen zwischen den Eindrückungen und dem Schmierstoff
Um die Wechselwirkungen zwischen den Eindrückungen und dem umgebenden Schmierstoff in hoch belasteten Kontakten besser zu verstehen, hat SKF erweiterte Modelle entwickelt und Versuche durchgeführt [8, 9], um die mit dieser Problematik verbundenen Phänomene zu untersuchen. Zunächst wird beschrieben, wie es im Kontakt zu einer Eindrückung kommt.
Eintritt einer geometrischen Oberflächenstörung in einen hoch belasteten Schmierkontakt
Sobald eine Oberflächenstörung bzw. Eindrückung in den EHD-Kontakt eintritt, entstehen zwei unterschiedliche Druckspitzen bzw. Filmdickenschwankungen. Bei der ersten Fluktuation handelt es sich um eine durch die stationäre elastische Verformung der Eindrückung im EHD-Kontakt hervorgerufene Druckspitze. Diese Spitze wird von einer entgegengesetzten Schmierfilmdickenschwankung begleitet und bewegt sich im Kontakt mit der gleichen Geschwindigkeit fort wie die Oberfläche, die sie hervorruft (z. B. u2, die Oberfläche mit der Eindrückung); sie wird „bestimmtes Integral“ genannt. Die zweite Fluktuation wird durch die eindrückungsbedingte geometrische Störung am Eingang des Kontakts hervorgerufen, da jede geometrische Störung auf einer der Oberflächen wie ein Strömungsventil wirkt, das den Schmierstoffstrom, der in den Kontakt fließt, verändert. Diese Fluktuation besitzt Filmdicken- und Druckschwankungskomponenten, die sich im Kontakt mit der durchschnittlichen Schmierstoffgeschwindigkeit ( ū = (u2+ u1)/2) ausbreiten. Als „Ergänzungsfunktion“ bezeichnet, stellen die finalen Druck- und Filmdickenschwankungen die Kombination dieser beiden Komponenten dar (Bild 4).
Geometrische Oberflächenstörung in Roll-/Gleitkontakten bei niedrigen Gleitgeschwindigkeiten (Wälzlager)
Niedrige Gleitwerte sind typisch im Bereich der maximalen Hertz’schen Spannung in Wälzlagerlaufbahnkontakten (S < 0,05). Mit dem erweiterten SKF Modell kann man den Durchlauf einer Eindrückung im hoch belasteten Schmierkontakt simulieren und somit die sich verformende Mikrogeometrie im Inneren des Kontakts als auch die sich daraus ergebenden Druckschwankungen berechnen. Bild 5 zeigt eine angenommene „Modell“-Eindrückung auf einer der sich kontaktierenden Oberflächen, das dazugehörige Mittellinienprofil der verformten Eindrückung und die sich daraus im Kontaktmittelpunkt ergebende Druckschwankung; berechnet unter reinen Abrollbedingungen. Bei einer zusätzlichen Überlagerung eines geringen Gleitanteils in die eine oder andere Richtung (-0,05 < S < 0,05) verändern sich die Ergebnisse signifikant. Bild 5 zeigt, im vorderen Bereich der Eindrückung (Vorderrand) einen Zusammenbruch der Filmdicke. Im hinteren Bereich der Eindrückung (Hinterrand) ist eine leicht erhöhte Druckspitze zu erkennen. Dies lässt folgende Schlussfolgerung zu: Bei guten Schmierfilmbedingungen wird die Oberfläche eher im hinteren Bereich der Eindrückung beschädigt, da dort die Drücke höher sind, und nicht aufgrund des metallischen Kontakts im vorderen Bereich der Eindrückung. Bei unzureichender Schmierung muss allerdings am Vorderrand der Eindrückung mit Verschleiß und eventuell mit Oberflächenzerrüttung gerechnet werden. Dieses Ergebnis deckt sich sehr gut mit den Versuchsergebnissen (Bild 6), die im SKF Engineering & Research Centre mit künstlich erzeugten Eindrückungen auf den Laufbahnen in Kugellagertests erzielt worden waren. Hier kann im hinteren Teil der Eindrückung ein Bereich mit Oberflächenzerrüttung (Mikroausbrüche) festgestellt werden, während erheblicher Verschleiß am Vorderrand der Eindrückung auftritt, der möglicherweise durch den Zusammenbruch des lokalen Schmierfilms verursacht wurde.
Geometrische Oberflächenstörungen in Roll-/Gleitkontakten bei moderaten Gleitgeschwindigkeiten (Zahnräder)
Moderate Gleitwerte (S ~ 0,1) können in Zahnradkontakten vorkommen. Mit dem erweiterten SKF Modell das nicht-Newton’sche Flüssigkeiten berücksichtigt (eine Erhöhung des Gleitwerts bewirkt keine Zunahme der Reibung) kann eine Eindrückung beim Durchlaufen eines Schmierkontakts unter diesen Gleitbedingungen simuliert werden. Bild 7 zeigt die normalisierten isolierten Druckschwankungen, die Filmdicke und die unter der Oberfläche vorhandenen von Mises-Spannungen, die für einen hoch belasteten Kontakt mit zwei unterschiedlichen moderaten Gleitwerten berechnet wurden (S = 0,1 – die untere unbeschädigte Oberfläche bewegt sich schneller als die obere Oberfläche mit Eindrückungen und S = -0,1 – die untere unbeschädigte Oberfläche bewegt sich langsamer als die obere Oberfläche mit Eindrückungen). Man kann deutlich erkennen, dass bei diesen moderaten Gleitbedingungen die Umkehrung des Vorzeichens des Gleit-Roll-Verhältnisses die Lage der maximalen Druckspitze und somit die Lage möglicher Ausfälle / Oberflächenzerrüttung umkehrt. Dies erklärt möglicherweise einige offensichtlich widersprüchliche Versuchsergebnisse in der Fachliteratur.
Geometrische Oberflächenstörungen in Roll-/Gleitkontakten bei hohen Gleitgeschwindigkeiten (Zahnräder)
Hohe Gleitwerte (S > 0,1) sind im Bereich der maximalen Hertz’schen Spannung von Lagerlaufbahnen nicht vorzufinden, allerdings in Zahnradkontakten schon. Mit dem erweiterten SKF Modell, welches nicht-Newton’sche Flüssigkeiten berücksichtigt und somit ein realistisches Verhalten des Schmierstoffs (eine Erhöhung des Gleitwerts bewirkt keine Zunahme der Reibung), kann eine Eindrückung beim Durchlaufen eines Schmierkontakts unter diesen Gleitbedingungen simuliert werden. Bild 8 zeigt die isolierten Druck- und Filmdickenschwankungen in Abhängigkeit von der Zeit bei einem hohen Gleit-Roll-Verhältnis (S = –0,5 – die untere unbeschädigte Oberfläche bewegt sich schneller als die obere Oberfläche mit Eindrückungen).
Aus Bild 8 wird deutlich, dass die ursprüngliche Position der Eindrückung dem Minimalwert der Druckschwankung (Δp) folgt; allerdings aufgrund des hohen Gleitwerts separieren sich die beiden Wellenkomponenten (Druck- und Filmdickenschwankungen) mit der Zeit voneinander. Zum spätesten Zeitpunkt (Δt) hat die am Eingang des Kontakts generierte Filmdickenschwankung (Δh) den Kontakt bereits verlassen, während sich die Druckschwankung noch immer im Kontakt befindet. Hier ist eine mögliche Schädigung innerhalb des Kontakts davon abhängig, wie sich die Druckwellen in den vielen Ermüdungszyklen überlagern und vereinen. Daher könnte sich eine Schädigung auch in einiger Entfernung von der Eindrückung zeigen.
Oberflächenzerrüttung im Bereich von Eindrückungen in Wälzlagern
Wie in Bild 6 dargestellt, zeigt sich eine Oberflächenzerrüttung (Mikroausbrüche) bei Wälzlagern oft um die Eindrückung herum (Randbereich / Materialüberhöhung). Gewöhnlich zeigt sich eine Oberflächenzerrüttung zuerst in dem Bereich, in dem die Druckschwankung am höchsten ist. Bei guter Schmierung zeigt sich eine Oberflächenzerrüttung erst nach sehr langer Zeit oder nie. Ist die Schmierung unzureichend, kommt es allerdings sehr schnell zu einer Oberflächenzerrüttung. Das von SKF entwickelte Oberflächenzerrüttungs modell (zur Simulation der Wechselwirkung von Rauheiten in Mischreibungskontakt) [9] lässt sich auch für Oberflächeneindrückungen verwenden. Das Modell berechnet die hydrodynamischen Drücke wie in diesem Artikel beschrieben und ist soweit modifiziert, um auch Mischreibungszustände zu berechnen (Bereiche mit metallischem Kontakt). Die durchgeführten Simulationen zeigen, dass die Oberflächenzerrüttung, die sich um Eindrückungen herum entwickelt, die gleiche physikalische Grundlage hat wie Oberflächenzerrüttung (z. B. Graufleckigkeit), die sich normalerweise auf Laufbahnen bei Mangelschmierung zeigt. Die Ergebnisse der Versuche und Simulationen sind in den Bildern 6 und 9 dargestellt. Bild 9a zeigt die nach 2.250 Mio. Überrollungen erhaltenen Versuchsergebnisse. In Bild 9b ist das dazugehörige Druckprofil und eine Übersicht über die unter der Oberfläche vorhandenen Spannungen entlang der x-Achse dargestellt. In Bild 9c ist der Schaden durch die Oberflächenzerrüttung nach 750 Mio. Überrollungen simuliert dargestellt. Bild 9d zeigt das Fortschreiten der Oberflächenzerrüttung wie vom Modell für diesen Fall nach 2.250 Mio. Überrollungen prognostiziert. Ein Vergleich mit Bild 6 zeigt eine gute Übereinstimmung mit den Ergebnissen.
Diskussion und Schlussfolgerungen
Eindrückungen in hoch belasteten, geschmierten Roll-/Gleitkontakten stellen ein beträchtliches Risiko für die Gebrauchsdauer von Maschinenelementen, wie beispielsweise Wälzlager, Zahnräder etc., dar. In der vorliegenden Studie wurden Simulationen durchgeführt, um Versuche an vollständigen Lagern zu analysieren und die Auswirkungen von elastohydrodynamischen Druckschwankungen bei Eindrückungen besser zu verstehen. Die Ergebnisse liefern eine gute Erklärung für die Entstehung von Glättungen im vorderen Bereich einer Eindrückung (vgl. Bild 6 und Bild 5). Die starke Oberflächenzerrüttung im hinteren Bereich der Eindrückung stimmt ebenso mit der Modellprognose in Bild 5 (mit S = 0) überein. Tatsächlich ist in allen berechneten Fällen die höchste Druckspitze immer im hinteren Bereich der Eindrückung zu finden. Es wurde auch festgestellt, dass bei reinem Abrollen (Gleitanteil = null) keine Glättungen im vorderen Bereich der Eindrückung vorhanden sind. (Siehe Bild 6 in Referenz [8].) Stattdessen zeigt sich eine leichte Form von Mikroausbrüchen. Erklärbar durch Mikroschlupf, hervorgerufen durch die mikroskopisch kleine elastische Verformung der sich berührenden Körper, der in der Praxis auch im Fall von Hertz’schen Kontakten bei reinem Abrollen nicht vermieden werden kann. Bei elastohydrodynamischer Schmierung als auch partieller EHD-Schmierung (Mischreibung) ist aufgrund der piezoviskosen Eigenschaften des Schmierstoffs und der Grenzreibung dieser mikroskopisch kleine Schlupfanteil ausreichend, um eine Oberflächentraktion/-reibung zu generieren, die die Voraussetzung dafür ist, Oberflächen-zerrüttung (Graufleckigkeit) zu erzeugen. Die Berechnung der mit der Anzahl von Überrollungen fortschreitenden Oberflächenzerrüttung in einem Wälzlager ist in Bild 9 dargestellt. Hier ist ersichtlich, dass die Simulationsergebnisse gut mit den experimentellen Untersuchungen übereinstimmen. In diesem Artikel werden nur einige wenige experimentelle Ergebnisse mit Eindrückungen gezeigt. Sie stehen für zahlreiche Tests, deren Ergebnisse alle mit den aufgeführten Beispielen übereinstimmen. Daher stellt die gute Übereinstimmung zwischen den modellbasierenden Simulationen und den ersuchsergebnissen eine gut fundierte Validierung dar.
Aus den obigen Beobachtungen lassen sich folgende Schlussfolgerungen ziehen:
- Die Modellierung der Ermüdungslebensdauer durch Berücksichtigung besonderer Oberflächenmerkmale und extremer Rauheitswerte, wie beispielsweise verursacht durch Kratzer und Eindrückungen, erfordert eine Beurteilung der dynamischen Drucküberhöhungen/-schwankungen und der damit zusammenhängenden lokalen Filmdicke im Bereich einer Eindrückung, die einen Hertz’schen Kontakt durchläuft. Das vorliegende nicht-Newton’sche Modell ist ein effizientes Werkzeug, um dieses Phänomen besser zu verstehen.
- Bei den im Hertz’schen Kontakt von Kugel- und Rollenlagern anzutreffenden niedrigen Gleitwerten (S << |0,1|) ist der maximale Überrolldruck immer im hinteren Bereich einer Eindrückung. Im vorderen Bereich einer Eindrückung ist die Möglichkeit von Verschleiß dominierend. Innerhalb dieser Schlupfgrößenordnungen nimmt der Überrolldruck im Bereich der Eindrückung [8] mit Zunahme des Schlupfanteils nur unerheblich zu. Das Risiko einer Oberflächenzerrüttung im Bereich der Eindrückung wird daher hauptsächlich durch die Anzahl der Überrollungen bestimmt.
- Sobald sich das Gleit-Roll-Verhältnis auf Werte um S > |0,1| erhöht, oder bei geringen Filmdicken, kann sich bei negativem Gleiten eine Änderung in der Lage der maximalen Druckspitze ergeben, hin zum vorderen Bereich der Eindrückung. Dies erklärt auch die Versuchsergebnisse anderer Forscher von Ausfällen/Oberflächenzerrüttung im vorderen Bereich der Eindrückung.
- Bei weiterer Erhöhung der Gleitwerte, d. h. bei hohen Gleit-Roll-Verhältnissen (S ≈ 0,3 – 0,5) wie sie bei Zahnrädern vorkommen, ist der Ermüdungsprozess im Bereich der Eindrückungen komplexer, da sich die beiden verursachten Druckspitzen und Filmdickenschwankungen zeitlich voneinander separieren. Die Lage der maximalen Druckspitze ist abhängig von der Zeit, der Hertz’schen Kontaktgröße und den jeweiligen Betriebsbedingungen.
- Die Betriebsbedingungen und die somit daraus resultierenden elastohydrodynamischen Drücke bestimmen die sich ergebenden lokalen maximalen Druckspitzen, die beim Überrollen einer Eindrückung entstehen. Bei Lagerlaufbahnen wird das Oberflächenzerrüttungsrisiko im Bereich einer Eindrückung eher von den sich einstellenden lokalen Druckspitzen bestimmt als vom Wert des Gleit-Roll-Verhältnisses oder der Richtung der wirkenden Reibkräfte. Allerdings kann die Richtwirkung der Gleitbeanspruchung sehr wohl eine Rolle in der Ausbreitungsphase der sich um die Eindrückung herum bildenden Mikrorisse spielen.
Möglichkeiten zur Senkung des Risikos von Eindrückungen – drei Hauptmaßnahmen:
- Reinhaltung des Schmierstoffs sicherstellen (durch gute Partikelfiltration bei Schmieröl, saubere Schmierfette, unbeschädigte Dichtungen)
- SKF Montageempfehlungen genauestens einhalten (sonst können evtl. Eindrückungen auf Laufbahnen entstehen)
- Guten Schmierfilmaufbau im Lager sicherstellen (Schmierstoff mit geeigneter Viskosität wählen)
Literatur
[1] SKF Hauptkatalog, Druckschrift 6000/I DE, August 2008.
[2] Internationale Norm: Wälzlager – Dynamische Tragzahlen und nominelle Lebensdauer, ISO 281
[3] Gabelli, A., Morales-Espejel, G.E., Ioannides, E.: Auswirkungen von Schmierung und Verunreinigungen auf die Lagerlebensdauer, Teil 2, SKF Evolution #3 2010.
[4] Cheng, W., Cheng, H.S. und Keer, L.M. (1994): Experimental Investigation on Rolling/Sliding Contact Fatigue Crack Initiation with Artificial Defects, Tribology Transactions, 37, pp. 1-12.
[5] Nélias, D. und Ville, F. (2000): Detrimental Effects of Debris Dents on Rolling Contact Fatigue, Journal of Tribology, 122, pp. 55-64.
[6] Ville, F. und Nélias, D. (1999): Early Fatigue Failures in EHL Contacts Due to Dents in EHL Contacts, Tribology Transactions, 42, pp. 795-800.
[7] Xu, G., Sadeghi, F. und Hoeprich, M. R. (1998): Dent Initiated Spall Formation in EHL Rolling/Sliding Contact, Journal of Tribology, 120, pp. 453-462.
[8] Morales-Espejel, G.E., Gabelli, A. (2011): The Behaviour of Indentation Marks in Rolling-Sliding Elastohydrodynamically Lubricated Contacts, Tribol. Trans., vol. 54, pp. 589-606.
[9] Morales-Espejel, G.E., Brizmer, V. (2011): Micropitting Modelling in Rolling-Sliding Contacts: Application to Rolling Bearings, Tribol. Trans., vol. 54, pp. 625-643.