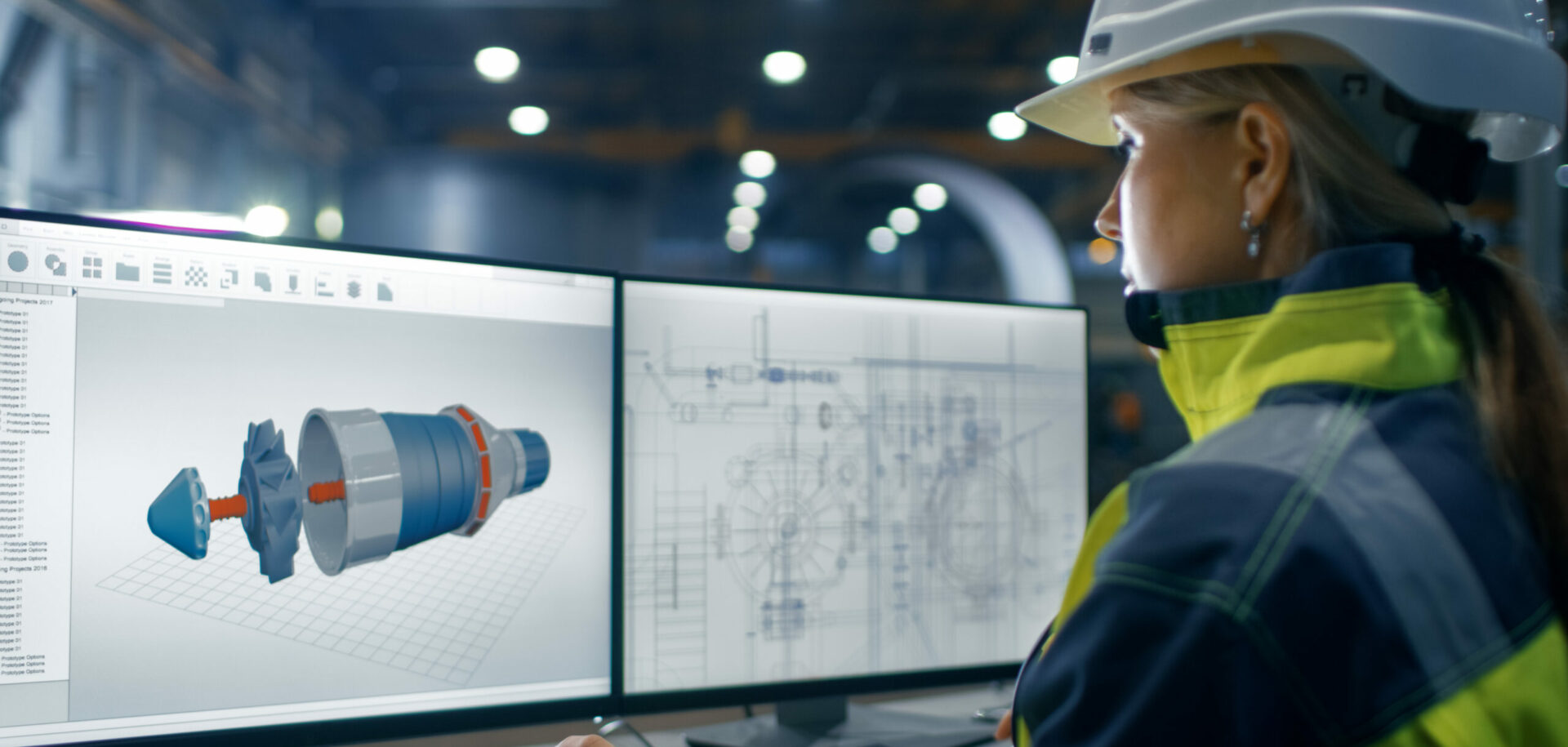
Über den Einsatz modernster Modellierungs- und Simulationsverfahren beim Bau des weltgrößten Aussichtsriesenrads
Es war klar, dass für den Bau des größten Riesenrads der Welt, des „High Roller“ in Las Vegas, nur die allerbesten Bauelemente und technischen Verfahren zum Einsatz kommen sollten. Als sich SKF mit dem Ingenieurbüro Arup und dem Generalunternehmer American Bridge Company zusammentat, um die Hauptachsen- und Radnabenlagerung zu entwerfen, wurden bei SKF die modernsten Analyse- und Konstruktionsverfahren eingesetzt, um einen unterbrechungsfreien Betrieb des Riesenrads bei Tag und Nacht sicherzustellen.
Zusammenfassung
Für die Konstruktion und Montage des bisher größten Wälzlagersystems für das weltgrößte Aussichtsriesenrad hat SKF ihr gesamtes Expertenwissen in den Bereichen Konstruktion und Analyse eingesetzt, um sicherzustellen, dass die Lagerung den außergewöhnlich harten Betriebsbedingungen standhält. Mithilfe einer sorgfältigen Analyse sämtlicher konstruktiver Aspekte mit modernsten Modellierungs- und Simulationsprogrammen konnte das optimale Lagersystem für diese Anwendung entwickelt werden.
Links
Ansprechpartner Verkauf
Randy A. Greaser, Randy.A.Greaser@skf.com
Mit einer Höhe von 168 Metern ist der „High Roller“ in Las Vegas das größte Aussichtsriesenrad der Welt. In seinen 28 klimatisierten Gondeln finden jeweils 40 Passagiere Platz. Die Fahrt dauert 30 Minuten und bietet einen grandiosen Ausblick über die pulsierende Stadt. Das Riesenrad ist Teil des neuen, rund 550 Millionen US-Dollar teuren Vergnügungskomplexes „The Linq“. Es hat die Landschaft verändert und ermöglicht den Besuchern einen neuen Blick auf den Las Vegas Strip. Die Konstruktion des „High Roller“ wurde im August 2011 angekündigt und seine Eröffnung war im März 2014.
Hinter dem ganzen Glitzer und Glamour dieser neuen Attraktion in der Skyline von Las Vegas steckt eine eindrucksvolle technische Spitzenleistung: die Realisierung einer gigantischen Konstruktion, die strenge Sicherheitsvorschriften und anspruchsvolle Betriebsbedingungen erfüllen muss. Der Generalunternehmer American Bridge Company, der das Riesenrad errichtete und auch eng mit den am Projekt beteiligten Bauingenieuren von Arup zusammenarbeitete, von denen die Spezifikation erstellt worden war, hatte SKF mit der Konstruktion, Lieferung und Montage der Lagersysteme auf der Hauptachse beauftragt. Das Ingenieurbüro Arup war auch schon beim Bau des bis dahin weltgrößten Riesenrads, dem „Singapore Flyer“, beteiligt gewesen.
Beim „High Roller“ dreht sich das Rad auf zwei von SKF kundenspezifisch gefertigten Pendelrollenlagern mit einem Gewicht von jeweils rund 8,8 Tonnen. Beide Lager haben einen Außendurchmesser von 2.300 mm, eine Bohrung von 1.600 mm und eine Breite von 630 Millimetern. Die zweireihigen Pendelrollenlager mit 30 Wälzkörpern pro Reihe sind die größten je von SKF im Werk Göteborg gefertigten Lager. Zur Bestimmung der optimalen radialen Lagerluft für diese Anwendung wurde ein Simulationsmodell verwendet. Zu den speziell entwickelten Besonderheiten dieser Lager zählen W26 Schmierbohrungen im Innenring, SKF NoWear beschichtete Rollen und PTFE-beschichtete Bohrungen. Ferner zeichnet sich das Gesamtkonzept durch eine hochentwickelte automatische Schmiertechnik und eine auf die Anwendung abgestimmte Dichtungsanordnung aus.
Die Konstruktion basiert auf einem verspannten Riesenrad mit einem Durchmesser von 143 Metern und besitzt neben den beiden Lagersystemen von SKF vier Stahlstützen, eine einzelne Verankerungsstrebe, eine feststehende Hauptachse, eine rotierende Radnabe, einen rohrförmigen Radkranz mit einem Durchmesser von 2 Metern und 112 verspannte Seilkonfektionen als Speichen. Die an der Außenseite des Rads montierten Fahrgastkabinen werden einzeln von Elektromotoren gedreht, so dass sie bei jeder vollen Umdrehung in horizontaler Position gehalten werden.
Konstruktionskriterien
Im Hinblick auf das Lagersystem (Bild 1) waren zahlreiche Anforderungen zu erfüllen, wobei es nicht zuletzt darum ging, eine sichere und zuverlässige Lösung zu liefern. Für die Wälzlager waren hohe Belastungen und starke Gehäuseverformungen bei veränderlicher Durchbiegung und Fluchtung der Hauptachse zu berücksichtigen. Laut Spezifikation wirken auf jede Seite des Aussichtsrads Lasten von 1.350 Tonnen. Jedes der unteren 56 radialen Stahlseile unterliegt einer Spannung von 132 Tonnen, bei den oberen 56 Seilen sind es jeweils 47 Tonnen. Die auf die Seile einwirkende Gesamtspannung beträgt in Summe 4.600 Tonnen.
Bei der Dimensionierung der Pendelrollenlager wurde eine Drehzahl von 0,033 U/min angenommen, und dem Berechnungsmodell wurde eine konstante Windlast zu Grunde gelegt. Diese Last wird bei jedem Lager auf die Stirnseite des Außenrings in axialer Richtung aufgebracht. In Simulationen verschiedener Einsatzbedingungen wurden unterschiedliche Windlasten verwendet. Die berechnete Lagerschiefstellung berücksichtigt konstante Windlasten bei unterschiedlichen Betriebsbedingungen, wobei die Simulationen jedoch nicht den Einfluss schwankender Windlasten beinhalteten.
Ein weiterer wichtiger Punkt, den es zu berücksichtigen galt, war die Lagerbelastung beim Einbau. Da ein Lagerausfall mit einhergehender Betriebsunterbrechung äußerst kostspielig sein kann, hat SKF das Projekt von außen als einen Six-Sigma-Prozess von der Auslegung über die Fertigung bis hin zur Montage begleitet. Bei einer so prestigeträchtigen Attraktion war es wichtig, sicherzustellen, dass das Konstruktionskriterium einer langen Lagerlebensdauer erfüllt war. Zu diesem Zweck hat SKF umfangreiche hoch entwickelte, auf dem Best-in-Class-Prinzip aufbauende Analyseverfahren eingesetzt, um zu gewährleisten, dass die Wälzlager und deren Umbauteile die strengen Spezifikationsvorgaben und Leistungsanforderungen erfüllen.
Projektansatz
Der Konstruktions- und Analyseteil des Projekts wurde in vier Phasen eingeteilt, und es wurde umfangreiche Modellierungs- und Analysesoftware benutzt, um sicherzustellen, dass die endgültige Konstruktion den tatsächlichen Betriebsbedingungen gerecht werden würde. Ziel war es, das komplexe Zusammenspiel aller Systemkomponenten zu bewerten und wichtige Leistungsindikatoren festzustellen. Der Zweck des Projekts bestand im Wesentlichen darin, die Systeminteraktion einschließlich des Einflusses von Gehäuseverformungen, der Lastverteilung und der Flächenpressung auf die Lagerlaufbahnen zu untersuchen. Dabei wurde der Bewertung der Einflüsse von Belastungen und Verformungen auf die Lager-Performance in Form von Kräften und Bewegung besondere Aufmerksamkeit geschenkt.
SKF verfügt über moderne, speziell für Wälzlageranwendungen entwickelte Simulationsprogramme, mit denen die vielfältigen Faktoren, die das Systemverhalten beeinflussen, wie Lagerspiel, Schiefstellungen und Flexibilität der Stützkonstruktion, unter verschiedenen Grenzbedingungen bewertet werden können.
Die Projektphasen wurden wie folgt durchgeführt:
Phase 1 – Projektdefinition basierend auf Design for Six Sigma
- Projektdefinition
- zentrale DfSS-Dokumente
- Datensammlung
Phase 2 – Simulationsanalyse
- starres Lagermodell mit Punktlasten
- Durchbiegungen und Verformungen als Eingabedaten
- flexibles Modell einschließlich Naben- und Achskomponenten
- Aufbringung der Belastung in Form von Seilspannung (4 Simulationen)
Phase 3 – Analyse des Lagerverhaltens
- Einflüsse von Änderungen der Grenzbedingungen
- Überprüfung der inneren Lagerkonstruktion
- Parameterstudie der inneren Lagergeometrie
- FE-Analyse des Käfigs
Phase 4 – FE-Analyse der Drive-up-Montagekräfte
- FE-Modellerstellung
- FE-Analyse der Aufschiebekräfte ohne Seillasten
- FE-Analyse der Aufschiebekräfte mit Seillasten
Phase 1 beinhaltete die genaue Definition des Projekts und die Zusammenstellung aller erforderlichen Informationen und Dokumente für einen Design for Six Sigma(DfSS)-Ansatz. Teil der DfSS-Methodik ist die Durchführung einer FMEA (Failure Mode and Effects Analysis), mit der die Entwicklung technischer Aktivitäten und Lösungen angestoßen wird. Die durchgeführte FMEA half dem Design-Team, potenzielle Fehlerursachen aufgrund von früheren Erfahrungen zu ermitteln und diente als Maßstab für die Auswahl von Konstruktionsmerkmalen, Simulationen und Empfehlungen. Die FMEA wurde von einem Team bestehend aus Vertretern von Arup, der American Bridge Company und SKF vorbereitet.
In der Praxis war der Ausgangspunkt für die Erstellung der zentralen DfSS-Dokumente unter anderem die Feststellung der die Ermüdungslebensdauer eines Lagers beeinflussenden Parameter (Bild 2) zwecks Erzeugung eines „Boundary Diagram“ (Darstellung aller Randbedingungen und Auswirkungen), das die Interaktionen des Lagersystems mit seiner Umgebung einschließlich der Eingabedaten und dem gewünschten Output definiert. Ein weiteres Diagramm, das „P-Diagram“ (Parameter-Diagramm), dient zur Feststellung aller maßgeblichen Auslegungsparameter sowie der Geräuschfaktoren, die sich nachteilig auf das gewünschte Ergebnis, d. h. die Lager-Performance, auswirken.
Danach wechselte SKF über in Phase 2, wo es um die Erstellung und Auswahl eines Entwurfs ging. Es wurde eine Analyse der Lagerleistung mit den oben genannten Simulationsmodellen im Hinblick auf eine Lagerkonfiguration durchgeführt. Dabei wurde das SKF Simulator (Orpheus) Softwareprogramm genutzt, das als komplett integriertes System zur Untersuchung von Wälzlageranwendungen entwickelt wurde. Mit Orpheus kann das statische und modale Verhalten von Lageranwendungen analysiert werden. Zuerst wird ein Modell hergestellt, indem sämtliche Maschinenkomponenten wie Lager, Wellen, Zahnräder und Gehäuse miteinander verbunden werden. Eine beliebige Kombination aus Kräften, vorgeschriebenen Verschiebungen und Drehzahlen kann zur Definition der auf die Komponenten einwirkenden Lasten verwendet werden. Die Komponenten selbst können im SKF Simulator als spezielle (nichtlineare) Elemente (d. h. Wälzlager) definiert sein, aber auch als beliebige Elemente wie Wellen und Gehäuse. Letztere müssen ein lineares Verhalten aufweisen und ihre Steifigkeit und Dämpfungseigenschaften werden mithilfe der Finite-Elemente-Methode ermittelt. Spezielle Reduktionsverfahren werden (auf die ursprünglichen Finite-Elemente-Modelle) angewendet, um die Anzahl der Freiheitsgrade zu reduzieren und damit die Berechnungszeit für Analysen zu verkürzen. Bei diesem Projekt wurden für die Analyse vier unterschiedliche Lastbedingungen gewählt.
Bei den starren (statischen) Modellsimulationen wird das Lager als einzelnes Pendelrollenlager modelliert, wobei vier unterschiedliche Lastzyklen auf den Außenring wirken. Der Innenring war in sämtlichen Freiheitsgraden ideal festgesetzt, während der Außenring in allen Freiheitsgraden frei beweglich war. Es wurde eine relative Schiefstellung zwischen dem Innen- und Außenring in positiver und negativer Richtung zugewiesen (Bild 3).
Nach dieser Analyse wurde die Modellierung fortgesetzt, indem man den Einfluss der strukturellen Flexibilität auf die Lagerlebensdauer untersuchte. Dabei wurden die Nabe und die Achse dem Modell als voll flexible Komponenten hinzugefügt, bevor weitere Simulationen auf Basis der vier Fallstudien durchgeführt wurden.
Ein wichtiger Aspekt des Konstruktionsprojekts war sicherzustellen, dass die Lagerung die in der Realität zu erwartenden Betriebsbedingungen erfüllt. In Phase 3 wurde daher die Lagerempfindlichkeit gegenüber Änderungen der Grenzbedingungen und der inneren Geometrie untersucht. Diese Analysen dienen zur Bewertung der Lagerauslegung unter Anwendungsbedingungen. Zu diesem Zweck führte SKF weitere Analysen durch, darunter auch eine zur Beurteilung des Lagerverhaltens gegenüber Änderungen der Grenzbedingungen und der inneren Geometrie. Ferner wurde eine FE-Käfiganalyse durchgeführt. Die Analyse der inneren Lagergeometrie führte dazu, dass das ursprünglich in dieser Analyse verwendete Rollenprofil der Wälzkörper geändert wurde.
Die ersten Optimierungsläufe zeigten die Möglichkeit auf, dass eine Veränderung des Rollenprofils und der Achs-/Nabensteifigkeit Lebensdauerverbesserungen bewirken könnte. Die optimale Konstruktion wurde gewählt und anschließend wurden weitere Simulationen der verschiedenen Lastbedingungen ausgewertet.
Lebensdaueranalyse
Wie bereits erwähnt, müssen die Lager des „High Roller“ eine lange Lebensdauer und hohe Zuverlässigkeit erreichen. Um dies sicherzustellen, hat SKF zwei wichtige Lebensdauerberechnungsverfahren angewendet: zunächst einmal das Verfahren nach DIN ISO 281 und dann auch die SKF AFC(Advanced Fatigue Calculation)-Methode.
In Betracht gezogen wurden die Werte der Lagerermüdungslebensdauern L10 und L3 und die Analyse der resultierenden Simulation. Die Definition der Lagerlebensdauer L10 besagt, dass 90 % der Lager die berechnete Lebensdauer erreichen oder überschreiten. Dies bedeutet eine Ausfallwahrscheinlichkeit von 10 %. Eine Ermüdungslebensdauer mit geringerer Ausfallwahrscheinlichkeit kann mithilfe einer Weibull-Verteilung mit einem Formfaktor von 1,5 und einem entsprechend gewählten Reduktionsfaktor berechnet werden. Der Lebensdauerwert L3 wurde gewählt, um die Ausfallwahrscheinlichkeit auf 3 % zu reduzieren und somit die Zuverlässigkeit des Lagersystems zu erhöhen.
Für dieses Projekt wurden sämtliche Lebensdauerberechnungen mit dem erweiterten Simulationsprogramm SKF Simulator durchgeführt. Bei modernen, qualitativ hochwertigen Lagern kann die tatsächliche Gebrauchsdauer die berechnete nominelle Lebensdauer in bestimmten Anwendungen erheblich übersteigen. Die Lebensdauer einer bestimmten Anwendung hängt von einer Vielzahl von Einflussfaktoren ab, z. B. der Schmierung, dem Grad der Verschmutzung, der Schiefstellung, dem richtigen Einbau, den Umgebungsbedingungen, konstruktiven Verformungen, Stillstandschwingungen und elektrischen Entladungen.
Beim SKF AFC-Lebensdauerberechnungsverfahren wird die Wälzkörper-Kontaktspannung über die gesamte Rollenlänge berücksichtigt. Der Einfluss dieser auftretenden Spannungen im beanspruchten Lagerringvolumen wird hinsichtlich Materialermüdung ausgewertet. In die SKF AFC-Lebensdauerberechnung fließt auch der Zustand des Schmierstoffs ein, wobei die Betriebsschmierfilmdicke und die Verschmutzung bei jedem Kontakt individuell betrachtet werden.
Infolge des DfSS-Prozesses und der daraus resultierenden Simulationsanalyse konnte SKF die Lebensdauer L3 erheblich erhöhen. Der berechnete Lebensdauerwert verbesserte sich um mehr als 10 % aufgrund der Veränderung des standardmäßigen Wälzkörperprofils, der Erhöhung der Nabensteifigkeit, der zusätzlichen reibungsarmen NoWear Beschichtung der Rollen und infolge der Spezifikation eines automatischen Schmiersystems. Im Gegensatz zu den meisten Lagern, die für eine Vielzahl von Anwendungen geeignet sein sollen, wurde das Lager speziell für diesen Anwendungsfall entwickelt. Das Rollenprofil wurde von SKF dahingehend optimiert, dass es den niedrigen Drehzahlen und hohen Lasten dieser Anwendung gerecht wird.
Aufgrund der in verschiedenen Simulationen gewonnenen Daten konnte SKF bei den technischen und finanziellen Überlegungen Empfehlungen hinsichtlich der optimalen Naben- und Achssteifigkeit abgeben. Die sich einstellende Flächenpressung zwischen Wälzkörper und Laufbahnen ist direkt abhängig von der Steifigkeit der Nabe und Radachse. Die Kosten für die Erhöhung der Naben- und Achssteifigkeit korrelierten mit der erwarteten Verbesserung der Lebensdauer L3. Auf der Grundlage dieser Studien wurde somit die Entscheidung getroffen, die Steifigkeit der Naben- und Achskomponenten zu erhöhen. Die Anforderungen an die Lebensdauer wurden unter allen Bedingungen übertroffen.
Schließlich wurden die Simulationsergebnisse dazu genutzt, die für die Montage erforderlichen Verfahren und Ausrüstungen festzulegen. Die Montagesimulationen waren fast identisch mit dem tatsächlichen Zusammenbau vor Ort. Für den ordnungsgemäßen Einbau der Lager benötigte man, wie vorauszusehen war, hydraulische Unterstützung. Die axiale Verschiebung, die zur Erzielung der endgültigen Lagerluft im eingebauten Zustand erforderlich war, lag innerhalb von 2 % des errechneten Wertes. In Anbetracht der Komplexität der Nabenkonstruktion war dies sehr beeindruckend.
Schlussfolgerung
Aufgrund des Six-Sigma-Projektansatzes und des gleichzeitigen Einsatzes von Simulationsprogrammen war SKF in der Lage, eine Nabenlagerung zu entwickeln, die nicht nur die technischen Projektanforderungen erfüllte, sondern auch die Vorgaben hinsichtlich Fertigung, Transport, Konstruktion und Kosten. Die von SKF konzipierten Systemlösungen wurden rechtzeitig geliefert und blieben innerhalb des vorgegebenen finanziellen Rahmens.
NoWear ist eine eingetragene Marke der SKF Gruppe.