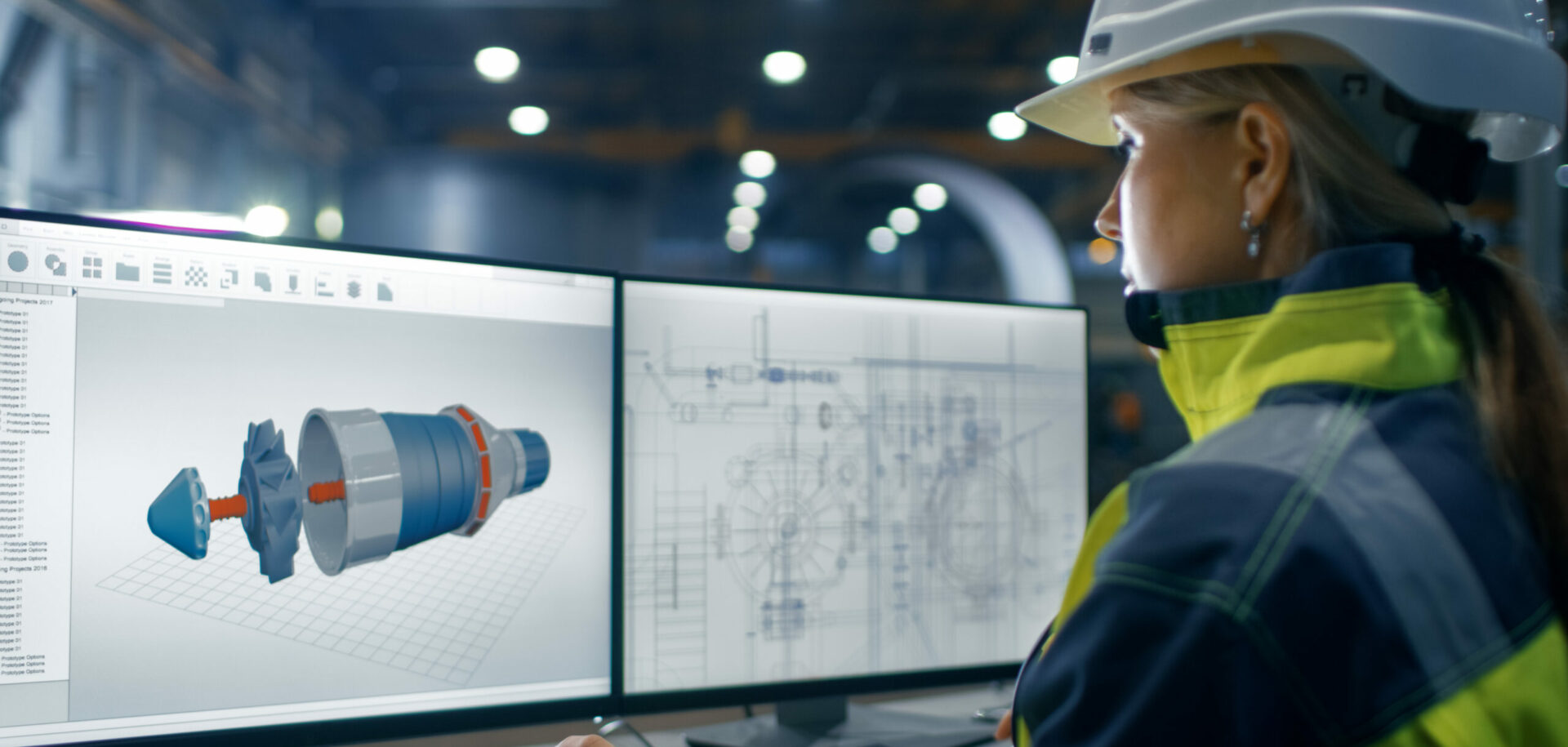
Zuverlässige Wälzlager für die Öl- und Gasindustrie
Die Öl- und Gasindustrie steht unter großem ökonomischen Druck. Der Betrieb der Raffinerien und anderer Anlagen verlangt eine hohe Betriebssicherheit, Effizienz und Kosten-kontrolle. SKF hat große Erfahrungen in diesem Industriebereich – von der Erstausstattung bis zur Wartung und Nachrüstung
Die Öl- und Gasindustrie steht unter großem ökonomischen Druck. Der Betrieb der Raffinerien und anderer Anlagen verlangt eine hohe Betriebssicherheit, Effizienz und Kosten-kontrolle. SKF hat große Erfahrungen in diesem Industriebereich – von der Erstausstattung bis zur Wartung und Nachrüstung
Das kritische Gleichgewichtzwischen Angebot und Nachfrage, beispielsweise in der Raffineriekapazität, wurde über die Jahre zunehmend enger, während gleichzeitig die Bedeutung der Bereitstellung eines extrem hohen Dienstleistungsniveaus zunimmt. Dies schließt nicht nur die Lieferung elementarer Ersatzteile ein, sondern auch die Bereitstellung von Nachrüstsätzen und Neukonstruktionen für sicherheitsrelevante Bauteile zur Erhöhung der Betriebssicherheit.
SKF stellt ein großes Produkt- und Dienstleistungsangebot für die Kohlenwasserstoff verarbeitende Industrie (HPI = Hydrocarbon Processing Industry) sowie Öl- und Gasfeldanlagen zur Verfügung – von Wälzlagern und Schmiersystemen bis hin zur Zustandsüberwachungssystemen und damit verbundenen Leistungen und Analysen.
SKF kann ihren Kunden aufgrund umfangreicher Erfahrungen mit rotierenden Systemen maßgeschneiderte Lösungen anbieten (Bild 2). So kann eine deutlich verbesserte Zuverlässigkeit und Leistung durch den Einsatz anwendungsoptimierter Standardlager erzielt werden. Beispiele sind Hybridlager mit keramischen Wälzkörpern aus Siliziumnitrit, NoWear Lager mit verschleißfester Keramikbeschichtung, INSOCOAT stromisolierte Wälzlager und der Einsatz moderner Käwerkstoffe wie Poyetheretherketon (PEEK) oder einteiliger Messingmassivkäe. Derartige anwendungsoptimierte Lagerlösungen können Korrosion, ungenügende Schmierung, Produktmedienschmierung, Verschleiß, Teilcheneindrücke in den Laufbahnen, Elektroerosion, Fressen und Folgeschäden an Gehäusen und Rotoren verhindern.
Lagersystemnachrüstungen
Die Nachrüstung rotierender Wellensysteme innerhalb der Öl- und Gasindustrie mit neuen anwendungs-optimierten Wälzlagern erfolgt häu aufgrund der Forderung nach höherer Betriebssicherheit, Verfügbarkeit und Prozesssicherheit, verbunden mit enger Kontrolle der Kapitalkosten für neue oder verbesserte Verarbeitungsanlagen. Das Ergebnis sind höhere Erlöse, niedrigere Betriebskosten und eine bessere Kapitalrendite. Einige Ansatzpunkte sind:
Nachrüstung „schlechter Akteure“ – Dies umfasst normalerweise das Ansprechen von Problemen, die sich auf eine oder mehrere Anlagen beziehen, welche für signifikante Produktionsverluste verantwortlich sind, bedingt durch Ausfallzeiten oder häue Fehler, welche hohe Emissionsstrafen nach sich ziehen wie beispielsweise bei kritischen Restgaskompressoren oder chemischen Reaktoren.
Nachrüstung der Ausrüstungsflotte – Hier geht es um Arbeiten, die in größeren Kompressor- oder Pumpenflotten erforderlich sind, die zu häu ausfallen, zum Beispiel bei Kompressor- und Raffineriepumpen-anlagen zur Erdgasförderung. Dies verursacht zusätzliche Wartungskosten und Ertragseinbußen und hindert qualifizierte Ingenieure und Techniker daran, an zukunftsorientierten Betriebsaufgaben zu arbeiten.
Konstruieren auf der Basis der Risikoanalyse – Dies ist eine Möglichkeit, Vorsorgemaßnahmen zur Risikoerfassung bei neuer kritischer Ausrüstung zu treffen, die auf der Liste der „schlechten Akteure“ Platz nimmt, wie Unterwasserboosterpumpen und -kompressoren.
Low-cost-Varianten – Dieser Weg ermöglicht die Verwendung kostengünstigerer Ausrüstungen durch den Einsatz hochzuverlässiger Lager in zuvor nicht in Erwägung gezogenen Anlagen, wie ölgeflutete Schraubenverdichter mit Wälzlagern unter extrem schwefelsaueren Gas- (H2S) Konzentrationen.
Leistungssteigerung – Das Ziel ist, die Leistung und Betriebssicherheit der vorhandenen Anlagen zu erhöhen, indem beispielsweise die Durchsatzleistung erhöht oder neue Prozessbedingungen ermöglicht werden, wie das Verändern der Back-up-Einheit in eine zweite Fertigungseinheit oder die Erhöhung des Druckes oder des Durchflusses bei einer bestehenden Ausführung.
Da SKF bei der Wahl, Entwicklung und Lieferung anwendungsoptimierter Lagerlösungen in all diesen Fällen innerhalb der Öl- und Gasindustrie involviert ist, besteht eine wachsende Referenzliste. Normalerweise wird das „Documented Solution Programme“ (DSP) von SKF für die Kosten-Nutzen-Analyse angewendet, um zu gewährleisten, dass der Kunde aus derartigen Nachrüstungen einen hohen Nutzen hat.
Lager: Werkstoffe, Design und Anordnungen
Lagersysteme bestehen gewöhnlich aus einer „Festlager“ und einer „Loslager“-Position. Die Festlagerposition umfasst vielfach zwei Lager, eines zur Aufnahme der radialen Belastung und eines für die Axialbelastung. Bild 3 zeigt eine typische Anordnung, die in vielen üblichen ölgefluteten Schraubenverdichtern gefunden wird.
Als Festlager für Hochleistungskompressoren, Pumpen und elektrische Antriebe werden normalerweise Kugellager verwendet. Diese sind entweder Schrägkugellager in O-Anordnung, Vierpunktlager oder Rillenkugellager. SKF kann diese Kugellager entweder aus normal durchgehärtetem Wälzlagerstahl liefern oder, für Anwendungen, die hohe Betriebssicherheit verlangen, mit Lagerringen aus durchgehärtetem hochfestem nicht rostendem Stahl.
Ein Loslager ist normalerweise ein Zylinderrollenlager (Bild 3) oder ein oder mehrere Kugellager, die im Gehäuse axial frei beweglich sind. Für eine derartige Anordnung können Zylinderrollenlager mit keramischen Rollen geliefert werden bis zu ziemlich großen Größen, um die meisten heute in ölgefluteten Schrauben-verdichtern verwendeten Lager zu ersetzen. In einigen Fällen wird es aufgrund von Fertigungsbeschränkungen günstiger sein, eine derartige Anordnung mit einem Zylinderrollenlager, das Rollen aus nicht rostendem Stahl mit einer NoWear Beschichtung enthält, neu zu gestalten oder es durch eine axial frei bewegliche Kugellagerausführung zu ersetzen.
Des Weiteren erfand SKF das CARB Toroidalrollenlager, das in Ausführungen eingebaut werden kann, wo Wellendurchbiegung und axiale Verschiebung aufgrund von Längenausdehnung aufgenommen werden müssen. CARB Lager können in einer Rostfreistahlversion mit NoWear Beschichtung der Rollen geliefert werden. Eine geeignete Anordnung könnte zum Beispiel aus zwei CARB Lagern in Kombination mit einem Vierpunktlager bestehen (Bild 4, oben) oder, für kombinierte hohe Axial- und Radialbelastung, einem Paket aus Axial-Schrägkugellagern (Bild 4, unten). Die Einführung einer derartigen Ausführung erfordert jedoch eine enge Zusammenarbeit mit SKF, für die Designvalidierung und um sicherzustellen, ob Fertigungskapazität bereitgestellt werden kann. Für Nachrüstungsprojekte ist eine enge Zusammenarbeit von SKF, ihren Vertragshändlern und den OEMs anzuraten, um eine Kombination aus bester Leistung, Wirtschaftlichkeit und Bereitstellung zu ermöglichen.
Auch gibt es verschiedene radiale und axiale Lageranordnungen mit Achsschenkel- oder Kippsegmentlagern, manchmal kombiniert mit Wälzlagern zur Aufnahme der Axialkräfte. Bei Anwendungen mit stark schwefelhaltigen Gaskonzentrationen bietet sich ein Austausch der herkömmlichen Lagerausführungen gegen Hybrid-Schrägkugellager mit hochfestem nicht rostenden Lagerstahl an.
Für Tiefst- und Hochtemperaturanlagen hat SKF eine speziell wärmebehandelte Variante des hochfesten nicht rostenden Stahls entwickelt. Dieser hat eine verbesserte Langzeit-Formbeständigkeit bei niedrigen (kryogenen) und hohen Temperaturen sowie eine höhere Härte bei höheren Temperaturen. Dieser Stahl wird in einem eigens entworfenen SKF Lager für Kryopumpen verwendet und eignet sich für Produktmedienanwendungen, die unterschiedliche Flüssiggase, wie Propan (LPG), Ethylen (LEG), Erdgas LNG) und Wasserstoff (LH2) verarbeiten. Nachrüstungen bei durchgehend arbeitenden Kryopumpen (Bild 1) verzeichnen eine Verlängerung des mittleren Ausfallabstands von mehr als 300%, verglichen mit dem, was heute mit konventionellen Wälzlagern ganz aus nicht rostendem Stahl erreicht werden kann.
Zustandsüberwachung und sicherheitsrelevante
Instandhaltung
Die Öl- und Gasindustrie hat eine Vielzahl von Anwendungen, bei denen Wälzlager in Prozessanlagen wie Pumpen, Kompressoren und chemischen Reaktoren eingebaut sind. Die Rolle derartiger Ausrüstungen variiert von relativ einfachen Anlagen mit Back-up-Einheiten bis hin zu prozesskritischen Anlagen in extrem schwierigen Einbausituationen, wo kein Back-up möglich ist. Beispielsweise werden Pumpen unter ziemlich stabilen Raffineriebedingungen verwendet bis hin zu kritischen Unterwasser-Boosterpumpen oder ununterbrochen laufenden Kryopumpen in LNG Terminals, Gas- und chemischen Anlagen. Durch SKF Reliability Systems verfügt das Unternehmen über umfangreiches Wissen zum Erkennen anstehender Probleme mithilfe der Zustandsüberwachung. Zustandsüberwachung an rotierender Ausrüstung kann über Signaltrends in Kombination mit moderner Frequenzanalyse mit Filtern usw. erfolgen, um bestimmte Signale von Lagerkomponenten oder anderen Ausrüstungsteilen oder prozessbezogene Signale zu verstärken.
Diese Information kann eine Wartungsmaßnahme auslösen, um ernsthafte Folgeschäden an der Ausrüstung zu vermeiden. Das Beispiel in Bild 5 zeigt den Schwingungstrend eines gleitenden Schaufelkompressors für Naphtha-Gase aus einer südamerikanischen Ölfeldproduktionsanlage, die gemeinsam von Chevron und PDVSA betrieben wird. Durch Überwachung des Kompressors konnte die SKF Mannschaft vor Ort Wartungsmaßnahmen ergreifen, bevor ein gefährliches Niveau erreicht war, und so konnte die Reparatur effizienter geplant werden und die Reparaturkosten fielen deutlich niedriger aus.
Zusätzlich führt SKF Risikoanalysen durch und leitet die Durchführung von sicherheitsrelevanten Instandhaltungsprogrammen für Prozesseinrichtungen über ihre in der Öl- und Gasindustrie aktiven Dienstleistungsunternehmen. Zur Unterstützung dieser Arbeiten und zur Verbesserung der Betriebssicherheit bei ihren Kunden, führen die Anwendungsingenieure der SKF, zu deren Aufgaben Wartungsfragen zählen, Lagerschaden-, Schmierungs- und Lagereinbauanalysen durch und beraten in Fragen der Lagermontage usw. und handeln deshalb als wichtige Partner in der Fehlerursachenanalyse und bei Optimierungsprogrammen.
Nachrüstung von Schwefelgasanlagen
Im nördlichen Alberta, Kanada, gibt es mehrere sehr große Entwicklungsanlagen zur Ölsandgewinnung, Anreicherung und Raffination zu schwefelfreien Blends. Eines der größten Projekte auf diesem Gebiet ist das Syncrude Joint Venture mit einer Tagesförderleistung von 315.000 Barrel. Die schweren Kohlenwasserstoffe, die aus dem Ölsand gewonnen werden, enthalten Schwefel. Durch Wasserstoffkracken werden diese zu leichteren Kohlenwasserstoffen aufgewertet, aber auch dieser Vorgang erzeugt Schwefelwasserstoff (H2S). Die Entfernung des Schwefelwasserstoffs ist sehr wichtig. Das geschieht mit Wasserabscheidern. Es bleibt jedoch ein „Restgas“ über, das vor einer weiteren Behandlung verdichtet werden muss. Beim Syncrude Verfahren sorgt ein ölgefluteter Schraubenverdichter, der dem Gasstrom gewachsen ist, für die Gasverdichtung. Diese Ausführung hat viele technische und wirtschaftliche Vorteile, verglichen mit anderen Kompressoralternativen, wie Kolbenverdichter und Trocken-schraubenverdichter mit ihren hohen Anschaffungskosten, unhandlicher Wartung und komplizierter Ausfallart. Aufgrund einer Verfahrensänderung wurde die Schwefelwasserstoff-konzentration des Restgases auf etwa 30 bis 40% deutlich erhöht. Hierdurch traten bei dem Schraubenverdichter ernsthafte Funktionsstörungen aufgrund von Lagerschäden auf, die durch Spannungsrissbildung an Laufbahnen und Wälzkörpern verursacht wurden. Diese Lagerschäden führten bei der Raffinerie zu kostspieligen Betriebsstörungen aufgrund von Kompressorversagen, durch Schwingungen verursachte Fehler, und schließlich zu Lagerausfällen.
Die Syncrude Ingenieure schauten also nach potenziellen Verbesserungen im Lagersystem und den Prozessbedingungen. In Zusammenarbeit mit SKF und dem SKF Vertragshändler BC Bearings wurde beschlossen, eine kundenspezifische Lösung anzubieten, die die Einführung einer Reihe neuer Werkstofftechnologien für Lager beinhaltete, die bei SKF in der Entwicklung stehen. Diese Lösung beinhaltet neue hochfeste nicht rostende Lagerstähle und größer dimensionierte Zylinderrollenlager und Vierpunktlager in Hybridausführung.(Bild 6). Außerdem hat sie ein sehr gutes Verhalten bezüglich Lagerlebensdauer (mittlerer Ausfallabstand verlängerte sich von 3.800 Stunden auf mehr als 23.000 Stunden ohne Ausfälle) und Schwingungsniveau gebracht, und zusätzlich, Robustheit gegenüber Schmierölunterbrechungen. Diese Maßnahme erhöhte signifikant die Betriebssicherheit und Verfügbarkeit des Veredelungs- und Raffinerieprozesses und verringerte deutlich die Schwefeldioxid (SO2) Emission beim Abfackeln.
Es muss angemerkt werden, dass es sich bei der Schwefelgasanlage um eine anwenderoptimierte Nachrüstung handelt, mit einer Kompressoranlage mit maßgeschneiderten Lagern für die Maschine und die Ersatzteile. In vielen anderen Fällen wird es möglich sein, bereits vorhandene SKF Lagerlösungen zu verwenden (zum Beispiel SKF Explorer Lager, PumPac Lager mit einem 40° und 15° Duplexpaar, INSOCOAT elektrisch isolierte Lager, PEEK Käe usw.) für Pumpen, Kompressoren und Antriebe, oder Hybridlager mit Ringen aus konventionellem Lagerstahl oder NoWear Ausführungen von Standardlagern. In vielen Fällen werden auch Fragen gestellt über die Einführung optimaler Verfahren mit Blick auf Dienstleistung, Vorgehensweise und Wartungswerkzeuge sowie Optimierung der Ersatzteile, die alle regulär von SKF geliefert werden und das weltweit. So ist SKF gut gerüstet, um Lösungen für die Öl- und Gasindustrie zu liefern, die den steigenden Anforderungen nach hoher Betriebs-sicherheit, Verfügbarkeit und Sicherheit gerecht werden.