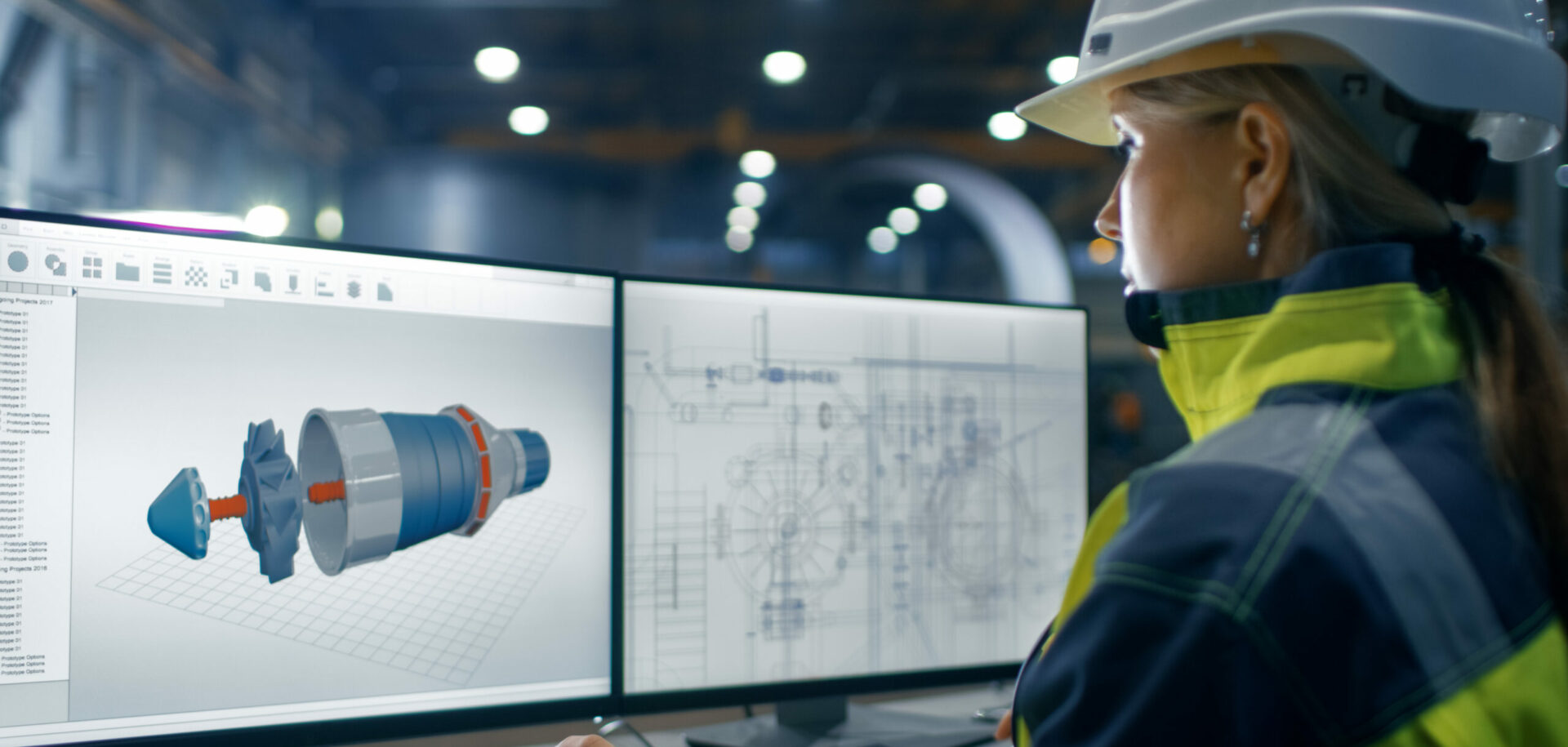
Défaillances prématurées des roulements dans les multiplicateurs d’éoliennes et fissures de phase blanche (WEC)
Les multiplicateurs d’éoliennes sont soumis à des conditions de service extrêmement variées qui peuvent, dans certains cas, pousser les roulements au-delà de leurs limites. Les roulements peuvent alors subir des dommages découlant d’un mode de défaillance prématurée spécifique appelé « fissures de phase blanche » (WEC). Pour désigner ce phénomène, on parle également parfois de matériau cassant, de durée de vie réduite, d’usure précoce, anormale ou à structure blanche (WSF). Cet article traite des mesures permettant de rendre les roulements plus robustes dans ce type de conditions de service.
Résumé
L’essor rapide de l’industrie de l’énergie éolienne, l’augmentation de la taille des équipements et de la capacité de production, sans oublier les conditions de service hostiles de ce secteur, tous ces éléments sont autant de défis pour les éoliennes. La compréhension des mécanismes, notamment dans les systèmes de roulements, pouvant conduire à des défaillances prématurées de l’éolienne est capitale pour offrir un équipement qui soit capable de répondre aux besoins en termes de fiabilité de la production et de rentabilité d’exploitation. Les mécanismes de défaillance sont complexes et, pour pouvoir contrer leurs effets, des recherches approfondies mais aussi une collaboration entre tous les partenaires dans ce secteur s’avèrent indispensables.
Liens apparentés
Product information – Black Oxide Bearings (pdf)
L’énergie éolienne est en passe de devenir l’une des principales sources énergétiques. Selon le Conseil mondial de l’énergie éolienne, le GWEC1, la puissance éolienne installée, qui s’établit actuellement à 200 GW, devrait ainsi doubler d’ici trois à quatre ans, ce qui laisse espérer que l’objectif ultime des 1 000 GW sera atteint d’ici 2020.
Même si les éoliennes affichent une disponibilité élevée (> 96 %, en fonction de l’éolienne) et les pièces mécaniques des taux de défaillance relativement faibles par rapport aux composants électriques, les transmissions mécaniques restent sujettes à des défaillances générant des frais de réparation élevés et des pertes de revenus importantes consécutives à de longs arrêts2.
Sur la plupart des éoliennes, un multiplicateur est utilisé pour augmenter la vitesse entre le rotor et la génératrice. Actuellement, la durée de service réelle des multiplicateurs est souvent inférieure à la durée nominale annoncée de 20 ans. Les défaillances surviennent sur différents étages, notamment au niveau des roulements des roues planétaires, de l’arbre intermédiaire et des roulements d’arbre à grande vitesse (Figure 1).
La plupart des avaries prématurées de roulements résultent d’un mode de défaillance qui n’est pas causé par les mécanismes de fatigue de contact classiques (Figure 2). Tandis que ces mécanismes mêlent fatigue sous-jacente et fatigue superficielle et peuvent être prédits grâce à des méthodes normalisées de calcul de la durée des roulements (ISO 281 et ISO/TR 1281-2), les défaillances prématurées par fissuration ne sont pas couvertes par ces méthodes. Des tentatives ont toutefois été menées pour calculer la durée des roulements lorsque des informations détaillées concernant le cas spécifique sont disponibles (effet local de la contrainte circonférentielle par ex.)37.
La norme ISO 15243 décrit les changements d’aspect causés par les mécanismes classiques de fatigue de contact roulant.
Le terme de « phase blanche » fait référence à l’aspect de la microstructure altérée de l’acier après polissage et attaque d’une microsection. Les zones touchées, constituées de particules ultra-fines de ferrite sans carbure nano-recristallisée, apparaissent blanches sur une micrographie en raison de la faible réaction du matériau.
Si certaines applications industrielles, comme les machines à papier, les entraînements à vitesse variable, les systèmes de propulsion marine, les réducteurs de broyeurs ou ceux utilisés dans les portiques de levage, sont connues pour y être sujettes de façon occasionnelle, il semble que la fréquence de ces défaillances prématurées soit plus élevée dans les applications d’éoliennes (fréquence supérieure qui pourrait toutefois s’expliquer par un parc de machines installées plus vaste.) Les fissures précoces apparaissent généralement au cours des trois premières années de service, ou à un stade représentant entre 5 et 10 % de la durée théorique (voir Figure 3).
Le plus souvent observées sur la bague intérieure, comme illustré sur la Figure 4, ces fissures présentent différents aspects : des fissures droites (« fissures axiales ») à celles qui s’accompagnent d’un écaillage léger ou avancé. D’après l’expérience terrain de SKF, les défaillances précoces par fissuration ne sont liées à aucun type de roulement (Figure 5), ni aucun traitement thermique (Figure 6) en particulier6, 7, 8, 9, 10.
Leur aspect en revanche dépend du traitement thermique (champ de contraintes résiduelles par ex.), du stade de la défaillance et très probablement des conditions de service ou de la position du roulement (champ de contraintes issu des charges appliquées). Comme le montre la Figure 6, une fissuration précoce au sein de l’application étudiée se traduit par une propagation rectiligne des fissures dans le matériau pour des bagues en acier martensitique (aspect de fissures « axiales » droites, comme sur la Figure 6a), tandis que pour les bagues en acier bainitique (Figure 6b) et les bagues cémentées, les fissures présentent un schéma de propagation circonférentiel sous les pistes (qui explique l’aspect écaillé visible sur la Figure 6c par exemple). À un stade de défaillance très avancé, les pistes de la bague intérieure apparaissent souvent très écaillées, quel que soit le traitement thermique.
Défis posés par les conditions de service des multiplicateurs d’éoliennes
Ils sont soumis à une grande variété de conditions de service qui peuvent parfois pousser les roulements au-delà de leurs limites (en termes de charge, vitesse, lubrification et combinaisons de tous ces facteurs). L’industrie de l’énergie éolienne doit allonger la durée des roulements et réduire les défaillances prématurées tout en cherchant par ailleurs à minimiser le coût global de l’énergie.
De nombreux avis font état de liens entre des conditions de service difficiles et des défaillances prématurées. Voici un aperçu des conditions en cause :
- périodes de charges dynamiques/couples élevés entraînant des vibrations et des variations rapides des charges (contraintes transitoires au niveau des pistes supérieures à 3,1 Gpa, charges élevées de 15 000 par an, chocs)6, 7, 11, 12, 13, 14, 15, 17, 18 ;
- selon le type d’éolienne, des forces radiales et axiales peuvent être générées par le rotor, le déplacement axial de l’arbre principal, entraînant des charges dynamiques, des contraintes supérieures exercées sur les pièces du multiplicateurs, notamment au niveau du premier étage19, 20 ;
- connexions/déconnexions occasionnelles au réseau électrique, causant des inversions de couple et d’effets rebond (pouvant générer des couples entre 2,5 et 4 fois supérieurs au couple nominal, ainsi que des chocs)12, 15, 21 ;
- accélérations/décélérations rapides et déplacements associés des arbres des multiplicateurs13, 15 ;
- défaut d’alignement, déformations structurelles (moyeu de la nacelle, logements)11 ;
- compromis à trouver au niveau de la lubrification entre les besoins des engrenages et des roulements, mais aussi entre des phases à faible et haute vitesse, qualité de l’alimentation en huile, respect des vidanges22 ;
- conditions environnementales difficiles : variations importantes de la température qui accentuent les écarts thermiques entre la bague intérieure du roulement et le logement au démarrage, poussière, climat froid, exploitation offshore, humidité23 ;
- fonctionnement au ralenti, se traduisant par des charges faibles avec un risque de glissement (usure par adhésion)23 ;
- conflits entre des exigences de conception : augmenter la taille des éléments roulants dans le but d’accroître la capacité de charge peut avoir pour effet par exemple d’augmenter le risque de glissement des rouleaux6, 7, 17, 23.
Comme il a été évoqué, des roulements peuvent présenter des défaillances même lorsque les normes de pratiques d’excellence24, 25 et autres pratiques basées sur l’expérience sont appliquées. Des évaluations statistiques réalisées sur un nombre limité d’éoliennes offshore2 indiquent clairement une corrélation entre taux de défaillance, vitesse du vent et charges élevées et fluctuantes. La tendance actuelle aux éoliennes toujours plus grosses avec des rapports poids-puissance toujours plus bas conduira immanquablement à des structures support plus flexibles11 qui, à leur tour, influeront sur la répartition des charges et leur distribution à l’intérieur des roulements et sur d’autres composantes de la chaîne cinématique. D’après la référence 26, dans des applications « récentes » fortement chargées, un cycle de conception du produit extrêmement novateur et des expériences suffisantes font souvent défaut pour assurer une robustesse optimale de la machine. Quels que soient les fabricants de l’éolienne et du multiplicateur, la présence de fissures sur le roulement est parfois interprétée comme le signe d’un comportement cinématique incontrôlé19, 27.
Causes possibles de « fissuration superficielle par fatigue de roulement » et revue des hypothèses
Les défaillances prématurées sont l’objet de nombreux débats au sein de l’industrie éolienne et de recherches menées de façon indépendantes par les fabricants d’éoliennes, les fabricants de multiplicateurs et les fabricants de roulements, sans oublier les universités et organismes tiers. Il n’existe hélas aucune théorie solide à l’heure actuelle. La présentation détaillée de toutes les hypothèses qui circulent concernant les causes des défaillances par fissuration WEC sort du cadre de cet article.
Toutefois, bon nombre des théories peuvent être résumées brièvement comme l’illustre la Figure 7. De nombreux écrits (référence 10) mettent en cause dans ces défaillances une variation locale de la microstructure du matériau du roulement sous l’influence de certains facteurs.
Parmi ces facteurs sont souvent mentionnés :
- le matériau :
microstructure, traitement thermique, teneur naturelle en hydrogène, propreté (différents types d’inclusions), contraintes résiduelles, etc. - les charges :
surcharges, pics de charges, chocs, inversions de couple, vibrations, glissement, contraintes structurelles, courants électriques, etc. - l’environnement :
lubrifiant, additifs, corrosion, effets tribochimiques, génération d’hydrogène, écarts de température, contamination (eau, par ex.), etc. - autres :
montage (rayures), transport, questions de qualité, etc.
Pour compliquer le tout, la plupart des facteurs d’influence sont en outre corrélés.
Ainsi, sous l’effet d’un facteur unique ou de plusieurs facteurs combinés, des zones de phase blanche WEA se développent localement dans la matrice en acier du roulement. Ces zones se comportent ensuite en sites noyaux à partir desquels des fissures se propagent vers la piste du roulement. Il s’ensuit une défaillance du roulement par écaillage ou WSF (écaillage à structure blanche).
Les hypothèses les plus courantes peuvent être classées selon les catégories suivantes : développements de fissures WEC amplifiés28,29,30 par la présence d’hydrogène, développements de fissures WEC liés principalement aux charges/contraintes favorisées par certaines inclusions31, 32 ou combinaison de plusieurs raisons33.
Certains des mécanismes de défaillance indiqués ci-dessus semblent influer sur certaines applications comme :
- les machines à papier (présence d’eau dans l’huile par ex. ; action corrective basée sur la surveillance de l’état du lubrifiant)34 ;
- les systèmes de propulsion navale (contraintes excessives par ex. ; action corrective basée sur un acier propre trempé à cœur spécial et sur la réduction des contraintes)32, 34 ;
- les roulements d’alternateur et de génératrice (courant causant des dommages par ex. ; action corrective basée sur l’utilisation de graisses spéciales et/ou de roulements hybrides, d’aciers spéciaux)6, 35, 36.
Néanmoins, de manière générale, la pertinence des hypothèses courantes concernant les défaillances précoces des multiplicateurs d’éoliennes dues aux fissures WEC reste floue pour le moment.
Cause possible de fissuration WEC dans les multiplicateurs d’éoliennes
D’après l’expérience de SKF, la plupart des défaillances prématurées de roulements sont en rapport avec la lubrification ou la surface et peuvent en partie être évaluées à l’aide du modèle avancé de calcul de la durée des roulements développé par SKF. Les recherches menées en interne par SKF ont révélé que de nombreux modes de défaillance de roulements, quelle que soit leur position dans le multiplicateur, sont amorcés en surface ou à proximité de la surface (0-150 µm), puis la propagation dans le matériau s’effectue sous l’influence d’un processus de fatigue par corrosion6, 7, 16.
Plusieurs éléments peuvent soutenir cette hypothèse :
Les roulements utilisés dans les multiplicateurs d’éoliennes sont de relativement grande dimension et pour les roulements, le mécanisme d’amorçage et de propagation des fissures peut différer par rapport à des roulements de petite dimension6, 16. Par exemple, une fissuration radiale plus profonde est observée sur les roulements de grande taille sous des charges modérées en raison des contraintes résiduelles et d’une contrainte circonférentielle supérieure37.
Dans le cas de défaillance prématurée des roulements du multiplicateur, sa survenue présage une propagation rapide des fissures. La propagation rapide des fissures par ramification et étalement peut s’expliquer par la présence d’éléments chimiques comme l’oxygène et de résidus de vieillissement du lubrifiant au niveau des flancs/extrémités des fissures6, 16, 38. Dans un réseau de fissuration exclusivement interne, nous sommes en présence de conditions de vide et le développement des fissures est nettement plus lent et résulte d’une fatigue purement mécanique38. En d’autres termes, dès un stade précoce, les fissures et réseaux de fissures doivent être reliés à la surface pour que l’oxygène et le lubrifiant y pénètrent.
La fatigue favorisée par l’hydrogène peut avoir des effets similaires28, 33 ou entraîner une fatigue par contact roulant classique accélérée6, 35, 36. Cela supposerait toutefois un environnement hautement corrosif par exemple ou le passage d’un courant électrique continu à haute fréquence. La présence d’eau libre conduit, de la même manière, à un environnement extrêmement corrosif34, mais les fabricants d’éoliennes assurent maîtriser la teneur en eau des lubrifiants. Les études menées par SKF ne font généralement pas état d’une corrosion humide dans les multiplicateurs d’éoliennes. Si ce facteur peut être exclu, les tribocouches de passivation régénérative, à condition qu’elles soient continues et intactes, procurent en outre généralement une barrière contre la corrosion et l’absorption d’hydrogène dans l’acier. La pénétration d’hydrogène dans l’acier est en effet néfaste. Il existe toutefois relativement peu de preuves de l’intervention de ce mécanisme de défaillance dans des multiplicateurs d’éoliennes.
Néanmoins, des études réalisées par SKF sur le plan tribochimique confirment la génération localisée d’hydrogène dans des contacts roulants avec frottement élevé. Pour que de l’hydrogène soit généré en continu, des surfaces métalliques neuves en interaction sont nécessaires. Cela pourrait conduire à un effet d’affaiblissement localisé de la surface favorisant l’apparition de fissures superficielles. Toutefois, dans les multiplicateurs d’éoliennes, il est rare d’observer sur les pistes du roulement défectueux une usure sévère au point d’entraîner une perméabilité à l’hydrogène. Par conséquent, la pénétration d’hydrogène à travers les pistes de roulement (sans autre facteur additionnel) semble peu probable. Les huiles agressives utilisées dans les multiplicateurs d’éoliennes, éventuellement en combinaison avec des contaminants, pourraient constituer un facteur additionnel potentiel39, 40, 41. D’après SKF, les performances de ces huiles peuvent être dissociées des mécanismes de défaillance amorcés en surface39 (micro-fissuration de la surface par ex.). Actuellement, le rôle de la génération d’hydrogène est considéré comme un effet local causé dans les réseaux de fissuration par la pénétration de lubrifiant conduisant au mécanisme de fissures de fatigue par corrosion (CFC)6, 16.
Les conditions de charge ordinairement modérées des roulements de multiplicateurs, l’absence d’accumulation de contraintes de compression résiduelles (dans la zone de la contrainte équivalente de von Mises maximale) ainsi que la diminution de l’élargissement de la ligne de diffraction des rayons X à proximité des pistes sur des roulements défaillants (en raison par exemple de contraintes mixtes de frottement-cisaillement et de vibrations) mises en évidence par des analyses de la réponse des matériaux corroborent l’idée selon laquelle le mécanisme de défaillance est amorcé en surface ou à proximité immédiate de la surface6, 7, 16. On sait, enfin, que non seulement des conditions de lubrification inappropriées, mais aussi certains phénomènes vibratoires à des fréquences élevées, sont capables de réduire l’épaisseur du film lubrifiant et, par conséquent, de favoriser l’apparition d’un frottement mixte local42, 43.
D’après la référence 44, les pressions hertziennes influent moins sur l’apparition des réseaux de fissures WEC pour lesquels les facteurs les plus déterminants se situent en surface. Le rôle souvent discuté de la génération, au niveau d’inclusions, de papillons, qui se présentent sous forme d’une microstructure altérée similaire à celle observée avec les fissures WEC, est considéré comme faisant partie du mécanisme de fatigue classique largement pris en compte dans le modèle de calcul de durée des roulements7, 44, 45. Il existe peu de preuves expérimentales d’une propagation d’ailes de papillons débouchant sur des réseaux de fissures WEC10.
Une densité élevée d’ailes de papillons est le signe de contraintes excessives ou de très fortes charges (>3 Gpa), mais les fabricants d’éoliennes affirment que les surcharges excessives sont inexistantes, ce que des essais HALT normalisés de multiplicateurs semblent confirmer. Un essai HALT (Highly Accelerated Life Test) est une méthodologie d’essai sous contrainte employée pour optimiser la fiabilité des produits au cours du processus d’ingénierie. Lors de ces essais, les investigations menées sur le plan métallurgique montrent souvent un nombre élevé de formations d’ailes de papillons sur les roulements en raison des fortes charges appliquées pour l’essai. Sur le terrain, en revanche, les roulements défaillants ne présentent généralement aucune augmentation significative de ces formations6,7. Sur l’étage à grande vitesse notamment, les charges sont généralement modérées, mais les roulements peuvent malgré tout connaître des défaillances par fissuration/WEC en l’absence d’une population significative, voire d’exemplaires individuels, d’ailes de papillons6, 7. Il semble que les essais HALT normalisés de multiplicateurs ne nécessitent aucune autre adaptation pour refléter les mécanismes de défaillance précoces rencontrés sur le terrain.
Néanmoins, on ne peut complètement écarter l’éventualité d’avaries32 de roulements imprévues induites par des contraintes internes élevées également dans des zones d’inclusions, tant que la contribution exacte de conditions de fonctionnement transitoires n’est pas parfaitement comprise. La détermination de la charge exacte exercée sur les roulements de multiplicateurs d’éoliennes sur le terrain est en grande partie basée sur des simulations, réduites par la suite à des hypothèses de charge quasi-statique. On estime que les charges sur les roulements sont modérées aux conditions nominales. Des conditions de fonctionnement en état non stable doivent être prises en compte, ce que fait de plus en plus l’industrie éolienne.
Mécanisme possible de propagation des dommages
Il est généralement admis que ce ne sont pas les conditions de fonctionnement nominales des multiplicateurs d’éoliennes mais plutôt les conditions transitoires, en partie inconnues, qui entraînent parfois des altérations de la cinématique, la charge et la lubrification des roulements. On estime que des concentrations de contraintes élevées en surface sont possibles sous l’effet par exemple d’un frottement mixte local d’origine vibratoire6, 16, 47, d’un défaut d’alignement ou d’autres facteurs précédemment mentionnés. Dans certaines zones de lubrification limite au niveau d’aspérités, la concentration des contraintes de traction peut augmenter et conduire à une fissure sous des cycles répétés (zones de contraintes élevées juste en dessous de la rugosité)48, 49.
Comme le montre de façon schématique la Figure 8, des conditions transitoires peuvent déclencher la formation de fissures superficielles, susceptible de s’accélérer sous l’effet de phénomènes tribochimiques6, 16, 39, 40, 41, ou bien des fissures en sous-couche peuvent atteindre la piste lorsque leur point de départ se trouve dans des zones sensibles telles que des inclusions à proximité de la surface (<150 µm)6.
Il peut s’agir d’inclusions de MnS tendre ou d’oxydes durs naturellement présents dans n’importe quel acier pour roulements. En outre, des petites lignes de MnS sur les pistes peuvent parfois être dissoutes par le lubrifiant et exercer une action similaire à des fissures superficielles potentielles6, 16 et/ou des fissures de corrosion. Les Figures 9 et 10 fournissent des exemples de fissures superficielles peu profondes qui nécessitent souvent une certaine expérience et des efforts significatifs pour être détectées à un stade précoce6, 7, 16.
Les fissures représentées sur les Figures 10 et 11 sont générées par un contact de roulement-glissement dans une application automobile en présence de pressions de contact et de traction élevées, proches des situations de charge que l’on peut trouver dans le secteur éolien, de l’ordre de 3Gpa18.
Une fois la piste de roulement localement endommagée, le lubrifiant à forte teneur en additifs EP pénètre dans la fissure. Selon l’orientation de la fissure, sa propagation peut être favorisée par des phénomènes hydrauliques46. Comme l’indique la Figure 12, à l’intérieur du matériau, le lubrifiant (souvent usagé et/ou contaminé par de l’eau) réagit au contact des flancs de fissures métalliques. En d’autres termes, un processus de propagation des fissures de fatigue par corrosion, CFC, est déclenché.
Il s’ensuit une transformation de la microstructure, induite par l’hydrogène dégagé par des produits de décomposition de l’huile (additifs et contaminants) au contact du métal brut des faces des fissures, qui vient également accélérer la propagation des fissures6, 7, 16. Cette conclusion est également corroborée par la détermination spatiale de la teneur en hydrogène des bagues de roulements endommagées qui confirme que l’absorption d’hydrogène se produit à un stade tardif du processus d’endommagement7, 16. Comme le montre la Figure 13, une étude fractographique de la face de la rupture brute ouverte préparatoire à proximité de la fissure de la bague intérieure révèle une microstructure intercristalline qui indique une fragilisation du matériau causée par l’hydrogène libéré par les produits de décomposition du lubrifiant6, 7, 16, 41, tandis qu’à distance de la fissure CFC, une face normale de rupture largement transcristalline peut être observée. Une autre indication d’un tel mécanisme CFC est fournie par l’analyse EDX du lubrifiant et des résidus d’additifs au sein du système de fissures ouvertes6, 7, 16.
Au sein du réseau de fissures, le mécanisme CFC entraîne ensuite une transformation locale de la microstructure en zones blanches qui conduit à l’aspect typique d’un réseau WEC irrégulier (Figures 2, 6, 14 par ex.). Les fissures WEC sont ainsi considérées comme secondaires, comme un produit dérivé du mécanisme CFC, dans la mesure où l’hydrogène libéré et l’énergie dissipée au niveau des flancs des fissures entraînent une modification locale de la microstructure qui confère cette apparence de fissures de phase blanche.
La distribution et l’intensité de cet effet visuel de fissures WEC sont soumises à des lois relativement complexes. Elles dépendent en grande partie de la distribution des résidus du lubrifiant à l’intérieur du réseau de fissures, de l’effet de frottement local au niveau des flancs des fissures et des champs de contraintes équivalentes locales.
Pour finir, la propagation/développement par ramification rapide des fissures dans les trois dimensions combinée aux retours de fissures conduit à une défaillance rapide des surfaces du roulement concernées.
Conclusion et stratégie de prévention SKF
L’essor rapide du secteur de l’énergie éolienne ainsi que la tendance aux éoliennes de plus en plus grosses installées sur des sites soumis à des conditions de vents turbulents posent de véritables défis pour les roulements du système d’entraînement. Cette évolution de ce secteur relativement récent a eu pour conséquence notamment des défaillances prématurées des roulements des multiplicateurs. Au fil des ans, les discussions sur ce sujet au sein de ce secteur ont été principalement axées sur l’influence des matériaux et des traitements thermiques. Depuis peu, on reconnaît que des conditions de vent spécifiques peuvent entraîner des perturbations au niveau de la cinématique, des charges et de la lubrification des roulements. En d’autres termes, la cause de défaillance ne doit pas être recherchée uniquement à l’intérieur du roulement. Ce sont toutes les interfaces au sein de l’application entre le roulement et le multiplicateur/la turbine qui doivent être prises en compte.
Les recherches menées par SKF révèlent que les modes de défaillance par fissuration concernant les roulements à certains emplacements critiques au sein des multiplicateurs d’éoliennes sont amorcés, de façon très probable, en surface ou à proximité immédiate de la surface. Les fissures se propagent ensuite dans le matériau sous l’influence d’un processus de fatigue par corrosion.
Compte tenu du degré de complexité d’une éolienne et de la grande disparité de roulements pouvant être affectés, il est très peu probable qu’une seule condition d’application soit en cause. On peut toutefois affirmer que toute condition entraînant une perturbation de la cinématique du roulement, comme des niveaux vibratoires élevés et un frottement par glissement important, doit être évitée dans le but de réduire la micro-usure et d’éviter de fortes contraintes de traction.
Pour soutenir efficacement l’industrie éolienne, SKF axe ses efforts sur des modifications des roulements afin de réduire le risque de défaillances prématurées de ces derniers et à accroître leur robustesse dans les conditions spécifiques aux applications de multiplicateurs d’éoliennes. La stratégie s’appuie principalement sur l’hypothèse énoncée, mais tient compte également des théories courantes concernant la fissuration WEC.
La plupart des stratégies de prévention des défaillances ont été validées par des recherches internes et par l’expérience de SKF. Voici un aperçu des mesures les plus avancées actuellement mises en œuvre dans la prévention des défaillances :
- Passivation spécifique à SKF :
- stabiliser la microstructure près de la surface ;
- rendre le roulement plus résistant aux attaques chimiques et à l’hydrogène ;
- réduire le micro-frottement sous les pics de charges ;
- améliorer le rodage.
- Acier propre spécial SKF pour les pièces soumises aux contraintes les plus élevées :
- réduire encore la quantité d’inclusions susceptibles de favoriser les concentrations de contraintes dans le matériau ou en surface.
- Procédé SKF de renforcement de la surface sur les pièces soumises aux contraintes les plus élevées (prototypes) :
- permettre un conditionnement de la pièce (accommodation : la charge nominale en condition de vent est relativement modérée) ;
- accroître la résistance à l’amorçage des fissures en surface et à leur propagation interne.
Pour résumer, un roulement modifié comme décrit ci-dessus permet de réduire les défaillances prématurées mais doit être associé à d’autres améliorations de la conception globale en fonction des conditions réelles de l’application. Par conséquent, une collaboration entre tous les partenaires lors du processus de conception est nécessaire et des outils de calcul modernes doivent être utilisés pour analyser les conditions de service dans le but d’identifier les conditions critiques et d’éliminer celles qui sont potentiellement néfastes. Des efforts redoublés en matière d’essais des pièces combinés à des essais dynamiques grandeur nature (au sein d’instituts de recherche tels que le NREL, le NAREC et Fraunhofer, etc. par ex.) doivent permettre de reproduire les conditions de service dommageables et de tester des solutions potentielles.