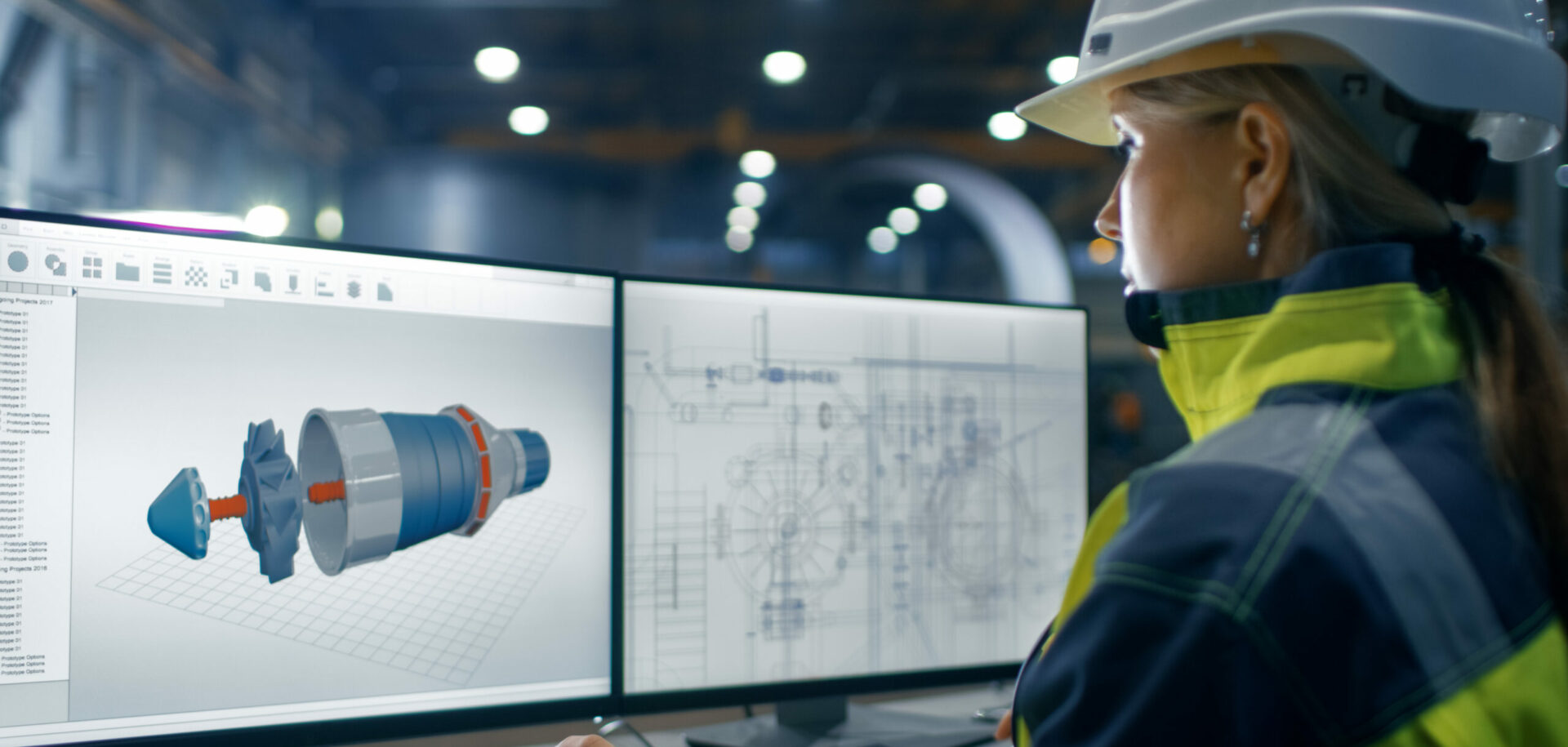
Summary
Research has shown that hybrid bearings can work effectively without using traditional oil lubrication. Designers are looking at the potential benefits of incorporating these bearings in compressors used in large air conditioning and refrigeration systems.
Avoiding the use of oil as a lubricant medium in this application would overcome the need for complicated oil separators and sealing. The incorporation of hybrid bearings in the compressor design would allow the refrigerant itself to be used as the lubricant.
The advantages of eliminating oil lubrication include removing many compressor failure modes associated with oil-based compressor lubrication systems in chillers, reducing the number of components, avoiding problems associated with oil lubrication and refrigerant mixing together, and potentially more efficient and reliable operation. In addition, the system would be more environmentally friendly, as oil can be potentially damaging to the environment.
In future, compressors used in air-conditioning and refrigeration systems could be designed to avoid the use of oil for lubrication. The incorporation of hybrid bearings in compressor designs could allow the refrigerant itself to be used as the lubricant.A challenge with hybrid bearings is the development of cost-effective manufacturing technology for high-quality ceramic rolling elements. With technological advances, the cost of ceramic balls has come down significantly over the past 10 years, and it is anticipated that ceramic rollers will follow the same development. The design of the surface texture and curvature of the steel raceways, the quality of the ceramic components and the design of the bearing cage are other important considerations in the development of a hybrid bearing to be used in pure refrigerant lubrication.
Researchers at the SKF Engineering and Research Centre carried out studies in the early 1990s to test the implications of diluting lubricant oils with refrigerants in conventional all-steel bearings. In compressors of present design, it is difficult to avoid dilution of the oil by the refrigerant, and it is important to understand how the dilution affects bearing performance. It was found that conventional all-steel bearings started to exhibit signs of inadequate lubrication at dilution levels of 20 % to 30 %. This led to the investigation of alternative bearing designs to improve bearing operation and life under these low-lubricant situations. The studies showed that it was difficult to find a limiting dilution ratio for the hybrid bearings. Finally, in 1996, hybrid bearings were run in pure refrigerant, and the bearings were in as-new condition at the end of the test. This was a critical test result, which opened up the possibility to use refrigerant as a lubricant for hybrid bearings.
In recent analytical studies, it has been found that refrigerants can actually form an elasto-hydrodynamic lubricant film. This is possible because refrigerants such as oils increase their viscosity under the very high pressure developed in the contact areas between the rolling elements and the bearing raceways. The increase is not as significant as with lubricating oils, but is sufficient to produce a very thin lubricant film. In conventional all-steel bearings, this thin film would be inadequate for lubrication, but the ceramic/steel material combination and other features of the hybrid bearings allow for reliable operation with this very thin film of refrigerant. Previously it was not thought possible to use refrigerants as lubricants because of the low viscosity of most refrigerants.
Promising application
One application for refrigerant-lubricated compressors is in chillers, which produce cold water for use in large air conditioning systems and industrial processes. Chillers use refrigerant to cool water, which is then used as a cooling medium in an industrial process or to provide air conditioning in a building.
Large capacity chillers, above 500 tonnes of refrigeration, are typically equipped with centrifugal compressors. Normally there is a single compressor for each chiller. Centrifugal compressors have one or more rotating impellers. The speed of rotation of the impeller is determined by the impeller peripheral speed. Large direct-driven impeller shafts rotate at 3,000 rpm or 3,600 rpm, while gear-driven high-speed impeller shafts rotate at speeds in excess of 10,000 rpm. The operating conditions of the bearings present difficult lubrication problems.
Traditional compressor designs have separation systems to separate out the oil mixed with the refrigerant so that the oil can be used as a bearing lubricant. Since refrigerants are typically very good solvents, it is difficult to avoid dilution of the oil by the refrigerant.
Chiller compressor types
There are three main compressor types used in chillers – scroll compressors for small chillers, screw compressors for medium sizes, and centrifugal types for large chillers. Centrifugal compressors are either direct-drive or gear-drive designs. In direct-drive designs the rotor of the drive motor is mounted directly onto the same shaft as the impellers. In gear-drive designs, the impeller shaft drive is through a speed-increasing gear.
In screw compressors, oil is used not only to lubricate the bearings, but is also injected into the compression cavity to cool the refrigerant gas and to seal leakage passages between the screws and the housing. The oil injected into the compression cavity becomes diluted by the refrigerant. Even with the use of an oil separator, the refrigerant cannot be completely removed before the oil is fed to the bearings.
If refrigerant-lubricated hybrid bearings were to be used in screw compressors, the oil injection into the compression cavity may be replaced by injection of liquid refrigerant or the compressor may be designed for high-speed operation, to minimise internal leakage.
No oil
In centrifugal compressors, there is no oil injection into a compression cavity. Oil is only used for bearing lubrication. In gear-drive designs, however, oil is used for lubrication of the gears. In centrifugal compressors, it appears that the direct-drive design is more suitable for refrigerant lubrication, as there is no requirement to lubricate the gears.
The ability to eliminate the need for oil lubrication would simplify designs and offer cost savings. Specific advantages of eliminating oil lubrication include removing many chiller failure modes associated with oil-based chiller lubrication systems, reducing the number of components, problems associated with oil and refrigerant mixing together and potentially more efficient operation.
Contamination of refrigerant by oil is also a factor in the heat transfer taking place in the heat exchangers used in the chiller. Oil tends to reduce heat-transfer efficiency. This means that an oil-free compressor could mean that higher chiller efficiencies are obtained, or, for a given efficiency, the heat exchanger could be of smaller size.
There is also an environmental benefit in not using oil, since the oil charge in a chiller can be lost during chiller repair, and oil would in one way or another end up contaminating the environment.
Ceramic elements
Hybrid bearings use ceramic rolling elements made of silicon nitride. The manufacturing process involves making a blank of silicon nitride powder that is compressed under very high pressure and baked in an oven to sinter the powder into a homogeneous material. The blank is then ground to a high-precision ball or roller. Porosities or embedded contaminants are not allowed. Because of the high hardness of the blank, the grinding has to be done with industrial diamonds. The grinding time can be several hundred hours. Grinding defects or surface marks from the grinding process cannot be allowed in refrigerant-lubricated hybrid bearings.
Typically, ceramic rolling elements are 60 % less dense, have a modulus of elasticity 50 % higher, expand only 30 % as much as an all-steel bearing and have a coefficient of friction in the order of 20 % of that of comparative all-steel types.
The low density of ceramic rolling elements significantly reduces the centrifugal force acting on the rolling elements in operation. This reduces internal bearing loads and facilitates better internal load distribution. The higher modulus of elasticity reduces friction and makes the bearing stiffness higher. Low friction and high stiffness allow for high operating speeds. The combination of ceramic rolling elements and hardened steel rings is a material combination that prevents metal smearing or galling, also known as adhesive wear.
Smaller contact areas
The higher modulus of elasticity also means that the contact areas between the rolling elements and the raceways will be smaller, since the ceramic material deflects less under load. This means that special raceway curvatures have to be used to optimise the balance between contact stresses and bearing friction.
One of the main challenges in compressor design is to ensure that, with the compressor’s working fluid acting as a lubricant, sufficient fluid is available for lubrication under all operating conditions. Hydrodynamic bearing solutions would not have been capable of operation under brief moments of interrupted supply of lubricant or delayed supply of lubricant at start up. The work at SKF’s Engineering and Research Centre shows that when using hybrid bearings with the refrigerant as lubricant, a thin elasto-hydrodynamic film exists between the ceramic rolling element and the raceways. Even if the ceramic rolling element does make momentary contact with the steel raceways across the refrigerant film, the fact that these components are made from dissimilar materials reduces the susceptibility of these bearing types to weld together, as all-steel bearings are prone to.
It is important when delivering the refrigerant to the bearing for lubrication that it is entirely in the liquid state. This is to ensure correct film formation and to avoid the potential situation where a percentage of the refrigerant may flash to gas state, starving the lubrication. The rate at which the refrigerant flows to the bearing location has to be controlled to ensure proper lubrication and cooling.
The prospect of chiller compressors using hybrid bearings offers performance, efficiency, cost and environmental advantages. Hybrid bearings for such applications have to be designed with the right material combinations, quality specifications, internal geometry and surface texture.
The concept of oil-free operation can also be used in other applications, such as product-lubricated pump bearings. For example, in oil-refinery operations, the use of bearings lubricated by the petrochemical being pumped offers the possibility of simplifying pump design and improving performance reliability and safety.
Hans H Wallin,
compressor, technology business manager,
SKF USA, Kulpsville, PA, USA
and Guillermo Morales Espejel,
project leader, Tribology, SKF Engineering and Resear