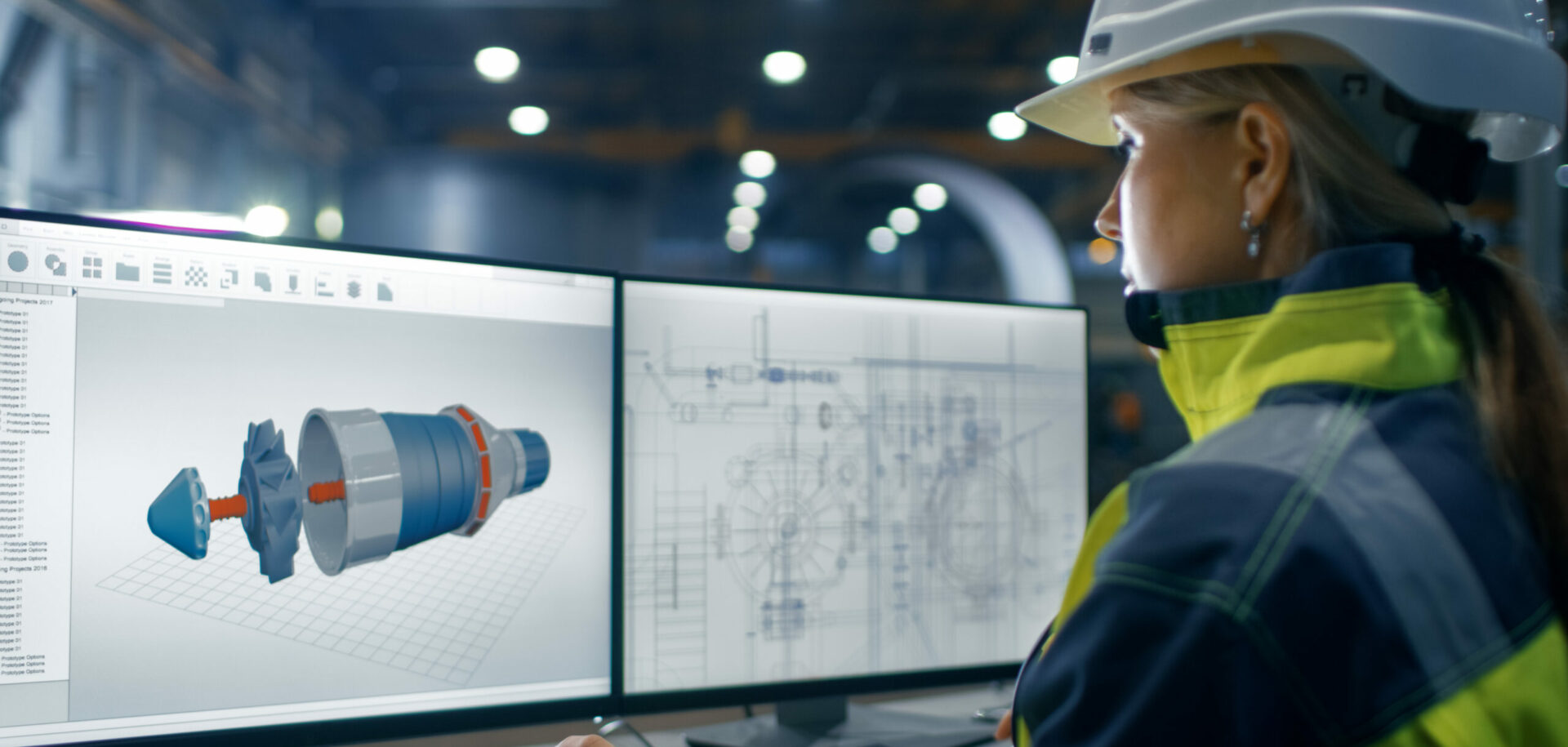
Split bearing units for continuous casting machines
The driven rollers have the task of drawing the strand or slab through the transition from the vertical to the horizontal roller bed. The high specific loads and the demand for minimal deflection require the use of multiple supported rollers. In the case of the one-piece rollers normally found in this application, multiple support can only be achieved by means of split bearing units. Common sizes of roller diameters in these applications range from 160 mm to 350 mm, with the bore diameter of bearing in the range 75 mm to 180 mm.
Within the steel industry rapid developments in continuous slab casting machines have led to demands
for more efficient bearing systems, particularly within the rollers that carry the cast steel.Steel manufacturing represents one of the harshest environments for bearing systems. In continuous casting, the push towards higher productivity, both in existing plants and new installations, has resulted in larger slab cross sections. This also means higher ferrostatic pressures. As the red-hot slabs move through the casting machine, they must be supported on as many points as possible. This can only be achieved through the use of smaller roller diameters.
The driven rollers have the task of drawing the strand or slab through the transition from the vertical to the horizontal roller bed. The high specific loads and the demand for minimal deflection require the use of multiple supported rollers. In the case of the one-piece rollers normally found in this application, multiple support can only be achieved by means of split bearing units. Common sizes of roller diameters in these applications range from 160 mm to 350 mm, with the bore diameter of bearing in the range 75 mm to 180 mm.
There is another issue – heat. The bearings need to be provided with a cooling system, as the temperature of the slabs can be up to 1,000 °C and only a few centimetres separate the slabs from the housing surface and the bearing raceways.
The casting principle
Continuous casting of steel was developed in Europe in the mid 1950s. In a typical plant, steel is poured into a ladle, transported to the casting bay and rests above the casting machine. A stopper rod or slide gate is used to control the flow of steel into a tundish reservoir. Once a pre-set level of steel is reached, nozzles are opened and the molten steel feeds into an open-ended mould set in a frame with internal water cooling. The solidifying cast slab passes from a vertical position in the machine to a horizontal plane where it is supported by a series of rollers. Further cooling takes place by spraying between the rollers.
The strand of cast metal continues travelling along the rollers to a gas torch cut off section where the strand is cut to required lengths. The end products of continuous casting plants are square section billets up to 150 mm x 150 mm, blooms that are up to 400 mm x 600 mm and slabs that are up to 250 mm thick by 2,500 mm wide. Other shapes can be produced, including round and octagonal sections.
Operating demands
The bearing units have to fulfil four basic demands in this application – high load carrying capacity, effective sealing, self-aligning ability and temperature stability. In addition, continuous casting also calls for a high degree of operational reliability and service life. Split bearing units, with specially cooled housings, have been developed to meet these demands. Depending on user requirements, these units can incorporate either spherical roller or cylindrical roller bearings.
Bearing unit design
The bearing unit consists of three split elements – housing, bearing and seal. The housings are located in a V-shaped recess in the roller frame either by screws or keys. The upper part of the housing incorporates the cooling chamber, while the lower half has a connection for the lubricating grease and the cooling water. During operation, the temperatures of the housing surface may reach 400 °C. To ensure adequate cooling of the bearings, the upper part of the housing has an integral water-cooled chamber with optimised cross section. Housings are coated with a heat and corrosion-resistant paint.
The bearings are either spherical roller or cylindrical roller bearings, depending on customer requirements. Normally they are non-locating.
Spherical roller bearings consist of two axially split inner ring halves, which are pressed tightly together by two split clamping rings, four machined brass cage and spherical roller assembly halves and one outer ring half. Compensation for length variation of the driven rollers is achieved between the bearing bore and the shaft. Also the inner ring halves have a lubrication groove and holes in the bore to ensure freedom of movement.
Split cylindrical roller bearings have a full complement of rollers. As there is sufficient space available, it is possible to join directly the two inner ring halves by four screws. Axial displacement, to compensate for length variations in the driven rollers, takes place inside the bearing between the rollers and the outer ring raceway. The outer ring half has a sphered outside diameter which allows the bearing to align itself in the housing. Split cylindrical roller bearings can be made of designs where there is limited width and small cross section, making them particularly suitable for thin slab technology, which is becoming increasingly popular for sheet metal production used in car manufacture.
Seals are necessary to prevent water, dust and scale from entering the bearing and causing damage. As for the rest of the bearing components, these are also of a split design. The conditions in continuous casting plants are amongst the most difficult of any production process; seals are also subject to high temperatures while also being required to have very high sealing efficiencies. The system used is a combination of an outer labyrinth incorporating a lamellar steel ring. For spherical roller bearings, the sealing performance can be improved by using additional split radial shaft seals.
Overall, split bearing units can provide tailor-made solutions for applications in the metallurgical industry. They are available in various design sizes for traditional slab casting machines as well as meeting the growing market for thin slab production where the steel is cast and rolled in a single operation.
Werner Palmetshofer,
SKF Österreich AG,
Steyr, Austria