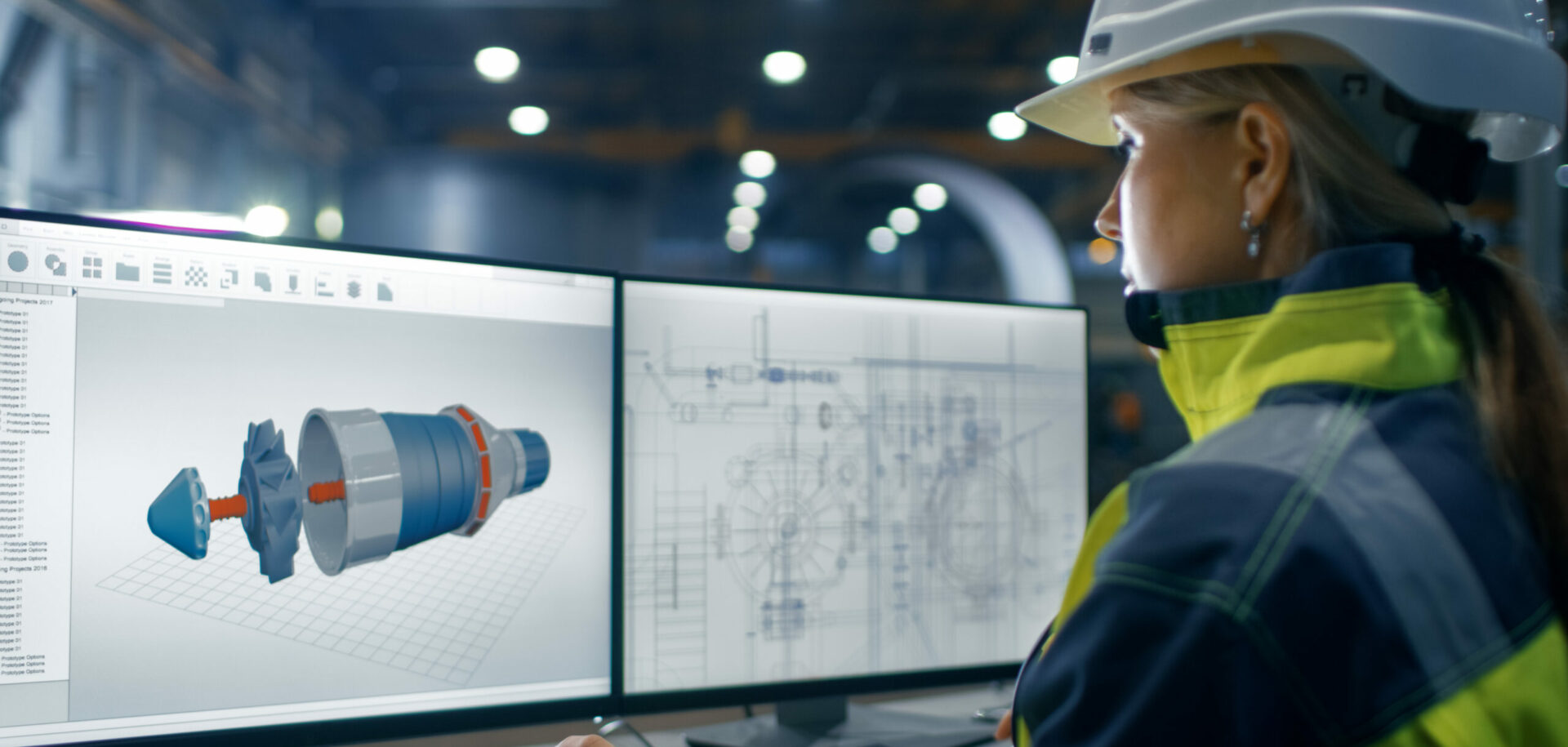
100 YEARS EVOLUTION – of cylindrical roller bearings
Design improvements in cylindrical roller bearings have arisen through more than 100 years of bearing evolution. Thanks to this breadth of experience, modern cylindrical bearing designs are characterized by the ability to offer reduced friction, high carrying capacity, longer life and downsizing
Summary
Cylindrical roller bearings have evolved steadily over the past 100 years. The SKF Explorer bearings that have emerged more recently out of engineering efforts are characterized by higher carrying capacity, longer life coupled with the opportunity for downsizing and significantly reduced friction. Further progress has led to more energy efficient designs that support its use in a broad range of applications as well as meeting the demands of more recent industries such as wind energy.
The design improvements for cylindrical roller bearings are built on a history of the development of rolling bearings that can be traced back to the 1870s, when the first bicycle factories were established, creating the need for bearings. Further demand for ball and roller bearings in general mechan-ical applications led to the advent of companies building and designing rolling bearings.
From the early days of the industry, the energy-saving credentials of roller bearings were clear. In a research project conducted in New York in 1905, W P Graham of Syracuse University compared the energy consumed by two equivalent streetcars: One was equipped with sliding bearings and the other one with roller bearings. The test showed that 52 % of energy could be saved when roller bearings were used.
First modern cylindrical roller bearing
In 1909, Dr.-Ing. Josef Kirner, a leading engineer at the Norma Compagnie in Cannstatt in Germany, was granted a patent for his invention of a modern cylindrical roller bearing. The bearing design had crowned raceways (fig . 1), thus avoiding damaging edge stresses at the roller ends. Bearings, developed in the following years, were equipped with short rollers that were accurately manufactured and exactly guided between flanges, resulting in many benefits. Kirner recognized the full impact of these benefits and introduced the bearings in Germany, against strong resistance of many fellow experts.
In 1914, SKF in Gothenburg, Sweden, acquired half of the shares of Norma Compagnie GmbH, and the company was incorporated into the SKF Group. Since then, the history of the single row cylindrical roller bearing has been intertwined with that of SKF, and there have been many developmental milestones.
The period from 1920 to 1925 is characterized by a complete recognition of the cylindrical roller bearing as an important design – so much so that competitors started to copy it. In the 1920s, there were important developments for railway applications (fig . 2): the combination of NU and NH designs for railway traction motors, which is still used today, and the combin-ation of WJ and WUJ designs for axle boxes.
In the 1930s, SKF was a driving force in standardization of the boundary dimensions of cylindrical roller bearings. Boundary dimensions became identical to those of standard ball bearings. The roller diameter of bearings in the narrow series became equal to their length, while the ratio of length to diameter of rollers of bearings in the wide series was approximately 1.5. Almost all of today’s basic and classic designs were established.
The B-roller became a reality in the 1950s. In the previous 10 years, the first theoretical descriptions of the ideal profile of rolling elements and crowned rollers with a circular arc profile emerged. The Lundberg theory formed the basis of the crowned profile of cylindrical roller bearings and finally yielded the B-roller, which had a straight profile in its central part and was slightly crowned toward the roller end. Great progress was made when this was implemented into practice. It was now possible to determine the required crowning height more precisely. With shaft misalignment, the crowning height had still to be estimated.
The introduction of E-type bearings in the 1960s was a milestone in the history of the cylindrical roller bearing. The E-type bearing design enabled optimization of the bearing cross section to incorporate a reinforced roller complement consisting not only of larger and longer rollers (fig s. 3a and 3b), but also of a larger number of rollers (fig s. 4a and 4b). This resulted in increased load-carrying capacity by an average of 35 % and a much-extended bearing life.
The E-type bearing was quite a challenge to manufacture, as roller dimensions changed and new cages were introduced. All bearings in the 2, 22, 3 and 23 dimension series were redesigned to the E-type. For the other series, only some selective items were redesigned.
1981 saw the introduction of the EC cylindrical roller bearings with modified roller end and flange contact surface. The geometry of the flange has an opened design (fig 5). The roller ends are surface treated to improve the effectiveness of the lubricant, reduce friction and lower operating temperatures, resulting in less need for maintenance. The improved roller end/flange contact results in higher axial load capability for those bearings that have flanges on the inner and outer rings.
The introduction in 1984 of the logarithmic profile of roller raceways was another optimization of the contact conditions. This profile provides optimal load distribution between the rollers and raceways to significantly reduce the risk of edge stresses and increase operational reliability, even in applications where there are misalignment and shaft deflections (fig . 6).
Performance milestone
The new millennium started with a very important milestone, the introduction of SKF Explorer cylindrical roller bearings (fig . 7). The SKF Explorer cylindrical roller bearings are the result of many years of intensive research by an international team of SKF scientists and engineers. During this time SKF materials and manufacturing specialists together with those responsible for production have successfully implemented a number of improvements. These include:
-
The bearing material features extremely clean and homogenous steel with a minimum of inclusions. The oxygen content, which is a measurement for cleanliness, has been reduced to extremely low levels. This increases the fatigue strength in the rolling contacts and extends the bearing life.
-
New heat-treatment procedures optimize the bearing’s resistance to operational damage and temperatures without affecting dimensional stability.
-
The hardness of the rings and rollers has been selected for optimum performance. This makes them less sensitive to contaminants and contributes to their extremely long service life.
-
Upgraded manufacturing processes have contributed to a significant improvement in product quality. This means that the rings can be produced with an improved roundness, and the deviation from optimum form of the rollers has also been further reduced. The results of the tighter tolerances may be invisible, but the bearings run markedly quieter and with less vibration.
-
The logarithmic contact profile of the rollers has been further refined. The bearings are thus even less sensitive to minor misalignment and can carry heavier loads.
-
The optimized roller end/flange contacts are also present in SKF Explorer bearings.
-
The excellent design of the transition from the cylindrical section to the roller end drop of the logarithmic profile avoids damaging stresses.
-
The surface finish of the raceways on the rings and rollers has been further refined and provides enhanced lubrication conditions so that bearings can operate longer even under poor lubrication conditions.
-
SKF Explorer bearings are available with different cage materials and designs to withstand different operating conditions. The design of all the cages used in SKF Explorer bearings contributes to good lubrication of all contact surfaces, even under occasional interruptions in lubricant supply.
The improvements were confirmed by comprehensive service life tests.
The result is one to be very proud of: SKF Explorer single row cylindrical roller bearings set new standards with respect to performance and endurance. They have an enhanced ability to support dynamic loads and up to three times longer service life than the previous standard, which is superior to all other conventional cylindrical roller bearings. Recently, some medium-size bearings were redesigned and added to the SKF Explorer performance class. These items are identified by the designation suffix /PEX.
The performance improvements of SKF cylindrical roller bearings over the past 100 years have permitted downsizing, whilst still maintaining the required performance (fig . 8). Lower friction and a dramatic reduction in bearing mass have lead to lower energy use.
However, progress did not stop there. For some applications, such as the mining industry and industrial gearboxes, particularly for the windmill industry, high load-carrying capacity is of utmost importance to provide high operational reliability. SKF developed the high-capacity cylindrical roller bearing (fig . 9a and 9b). These SKF Explorer bearings have an increased number of rollers compared with the standard SKF Explorer bearings, whilst maintaining the same boundary and main internal dimensions. The wall thicknesses remain unchanged, in keeping with the E-type bearing design that has proved successful for 45 years.
The innovative design is in the cage development. In a high-capacity cylindrical roller bearing the cage is arranged far above or below the bearing pitch circle diameter and is ring shoulder-guided. The window-type steel cage is very strong – comparable with that of a two-piece solid-brass cage, although it has more rollers.
As compared with standard bearings, and depending on the cage design, the number of rollers in the bearing can be increased by up to two for bearings in the 23 series and up to three for bearings in the 22 series.
Following theoretical studies and simulations, this design was tried and tested for a year. The final validation test took 1,000 hours. Several sizes of SKF high-capacity cylindrical roller bearings have now been running successfully for years in wind turbine applications. Inspections have shown their superior performance in these applications.
Finally, to respond to the ever-increasing demand to reduce friction and thereby reduce energy use, SKF introduced the concept of Energy Efficient rolling bearings in 2007. The first SKF Energy Efficient (E2.) cylindrical roller bearings (fig . 10) developed are medium-sized bearings in the NJ series. Compared with the current SKF standard bearing, the new SKF E2 cylindrical roller bearings exhibit a friction reduction of up to 85 % in axially loaded applications (fig . 11) and a higher dynamic load rating by incorporating SKF Explorer features. These new, low-friction bearings are intended for a wide range of applications, but the main focus is on industrial and wind energy transmissions.
Key characteristics are lower friction, resulting in lower operating temperatures, improved lubrication conditions and higher axial load carrying capacity. This is combined with lower energy consumption and higher efficiency with lower costs and emissions plus higher speed ratings (+10 % compared to standard). This latest evolution of the cylindrical roller bearing offers extended service life and higher reliability. These new bearing designs follow a long heritage of roller bearings that have met the demands of their eras.