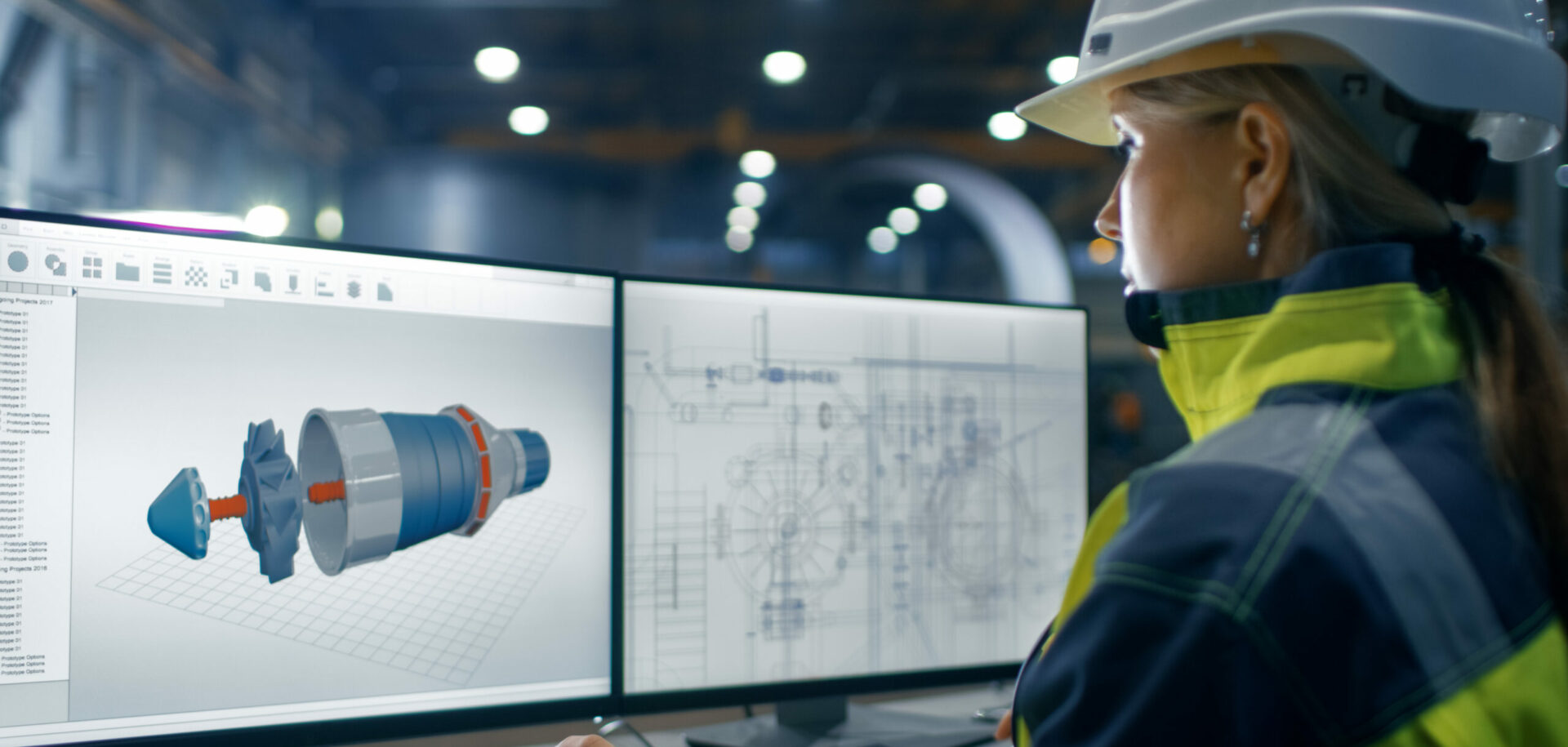
125 years of automotive history – SKF’s contributions to engine lubrication
Automotive lubrication has developed alongside the automotive industry. SKF Lubrication Systems Germany AG looks back on more than 80 years of experience in the field.
Wherever there is a vehicle, there is a need for a lubrication solution in its manufacturing process. At SKF, more than 80 years of experience have been accumulated in this area. From centralized lubrication to the latest lubrication for small marine diesel engines, the company continues to be a key partner in the development of new solutions. This year’s publication in the leading German automobile club magazine ADAC, as well as several advertisements of the car maker Daimler AG, highlighted the 125-year history of the automobile. In part, it recalled the historic journey in 1888 of Bertha Benz and her 14- and 15-year-old sons Eugen and Richard from Mannheim to Pforzheim, in Germany, in a motorized tricycle. The Benz Patent Motorwagen, as the vehicle was called, was developed by her husband, Carl Benz, in Ladenburg, not far from Hocken-heim, and registered in 1886 at Germany’s Imperial Patent Office as a “vehicle with petrol engine”. Historians consider this the first automobile, and it sowed the seeds for a new industry and the creation of many thousands of jobs. As motor vehicles developed, so did the need for and importance of automotive lubrication. In the early 1930s, shortly after the company launch in 1929 of Willy Vogel Autozubehör GmbH in Berlin, the single-pressure centralized lubrication system for automobiles was introduced. It was a remarkable sales success in central Europe. However, over the ensuing decades the need for centralized lubrication applications in automobiles dwindled, thanks to modern materials, new bearing and seal technologies and heavy-duty lubricants. Intelligent centralized lubrication systems do continue to be used in the commercial vehicles sector – heavy trucks, buses and construction and agricultural machinery. Some of the lubrication tasks are handled by SKF CAN bus control units that are integrated into the machinery and adapt to its current work and stress conditions. Machinery used in automobile construction, including for cutting, punching, molding, drilling, finishing, grinding, assembling and testing, is still equipped with centralized lubrication systems. SKF is a leading and preferred supplier for many of these applications. The rise of the automobile also sparked a desire for ever-more-powerful engines. The petrol-fuelled four-stroke internal combustion engine with spark ignition came out in 1876, followed in 1893 by the diesel-fuelled two-stroke internal combustion engine without spark ignition, which created opportunities to power stationary and mobile applications as well as to drive ships, locomotives, trucks and cars. Industrial development experienced a sudden boom. Rudolf Diesel was the man behind the diesel engine. His large-engine design offered particular benefits in terms of reliability and efficiency. In 1897, MAN in Augsburg, Germany, introduced the first production engine, a single-cylinder engine with 20 hp (15 kW), a 250 mm bore, 400 mm stroke and efficiency of 26.2 % (fig. 1). In this engine, drip oilers were used for lubrication. In the field of lubrication, Robert Bosch, who was already famous for his magneto patent for petrol engines, recognized that force-feed lubrication systems were needed for two-stroke diesel engines. In 1909, he presented his patented, mechanically driven box lubricator for the lubrication of combustion engines. This was followed by directly flange-mountable oil-metering pumps, which were installed in the Lanz Bulldog on two-stroke (hot-bulb) diesel engines and in many other lubrication solutions for general mechanical engineering. Joseph Vögele AG, founded in 1836 in Mannheim, Germany, developed and built switches, transfer cars, turntables and shunting installations for railway applications. Starting in 1925, its production included, among other things, centralized lubrication pumps for railway applications. The Vögele asphalt paver was launched in 1928, and this literally paved the way for further developments in lubrication. In 1959, Joseph Vögele expanded its centralized lubrication port-folio, buying all rights and production facilities for manufacturing Robert Bosch centralized lubrication systems. A new Vögele lubrication pump plant in Hockenheim-Talhaus was built in 1960. There, constant development continued on large-engine lubrication applications in addition to other industrial segments. This continued even after the plant was acquired by Willy Vogel AG (1999) and later by the SKF Group (2004). Major engine manufacturers such as Caterpillar, Deutz, MAN, MTU and Wärtsilä prefer the SKF system solutions for their high-performance engines. The solutions are used mainly for inlet valve seat lubrication (four-stroke range) and cylinder lubrication systems (two-stroke range). Nearly 120 years after Rudolf Diesel’s invention, the efficiency of large diesel engines has reached a maximum of 55 %. Research projects have confirmed that exploiting all technical possibilities can yield future increases to an efficiency of 65 %. In the field of sea transport, which consumes approximately 4 % of all fossil fuels, this means considerable resource savings and reduction in emissions. SKF Lubrication Systems Germany AG is making an important contribution to this in the form of modern, load-dependent oil injection systems for cylinder lubrication. These systems use state-of-the-art crank sensors and map-controlled microelectronics to deliver the high-value, high-quality lubricating oil with millisecond precision in the stress areas on the piston and cylinder liner as identified by the control electronics. These developments have resulted in oil savings of as much as 40 %. The SKF timed CLU4 lubrication pump was developed for new engine constructions and retrofits in a power range of 7,000 to 80,000 kW. This output range covers large diesel engines with piston diameters up to 1 metre, stroke lengths up to 3.3 metres and engine weights with a maximum of 2,300 tonnes (fig. 2). Today, this technology is also available for newly developed small engines with piston diameters of 350 and 400 mm in an output range of 4,000 to 9,000 kW. In February 2010, the R&D department of the Wärtsilä company in Winterthur, Switzerland, issued a production release for the newly developed CLU5 lubrication system (figs. 3 and 4). In this advanced development by SKF, as many as three lubrication pulses are made per second with a metering time of a maximum of three milliseconds at four SKF Lubrication Systems Ger-many AG can look back on more than 80 years of experience in the field of large diesel engines. SKF continues to be a leading development partner for premium-class engine manufacturers. Lubrication solutions for large engines enable further savings in terms of lubricating oil, operating costs and CO2 emissions. They increase dependability and value for the engine manufacturer, marine classification societies, shipping companies and end users, making SKF a preferred supplier – much as the SKF Knowledge network implements customer wishes and significantly improves sustainability efficiently and cost-effectively.
Summary
Diesel engines
Modern two-stroke crosshead diesel engines
lubrication points per cylinder (fig. 5). The SKF CLU5 package contains one timed lubricator per cylinder, an oil supply system for each engine and a standardized spare parts kit. The system was launched on the market in July 2011.80 years of experience