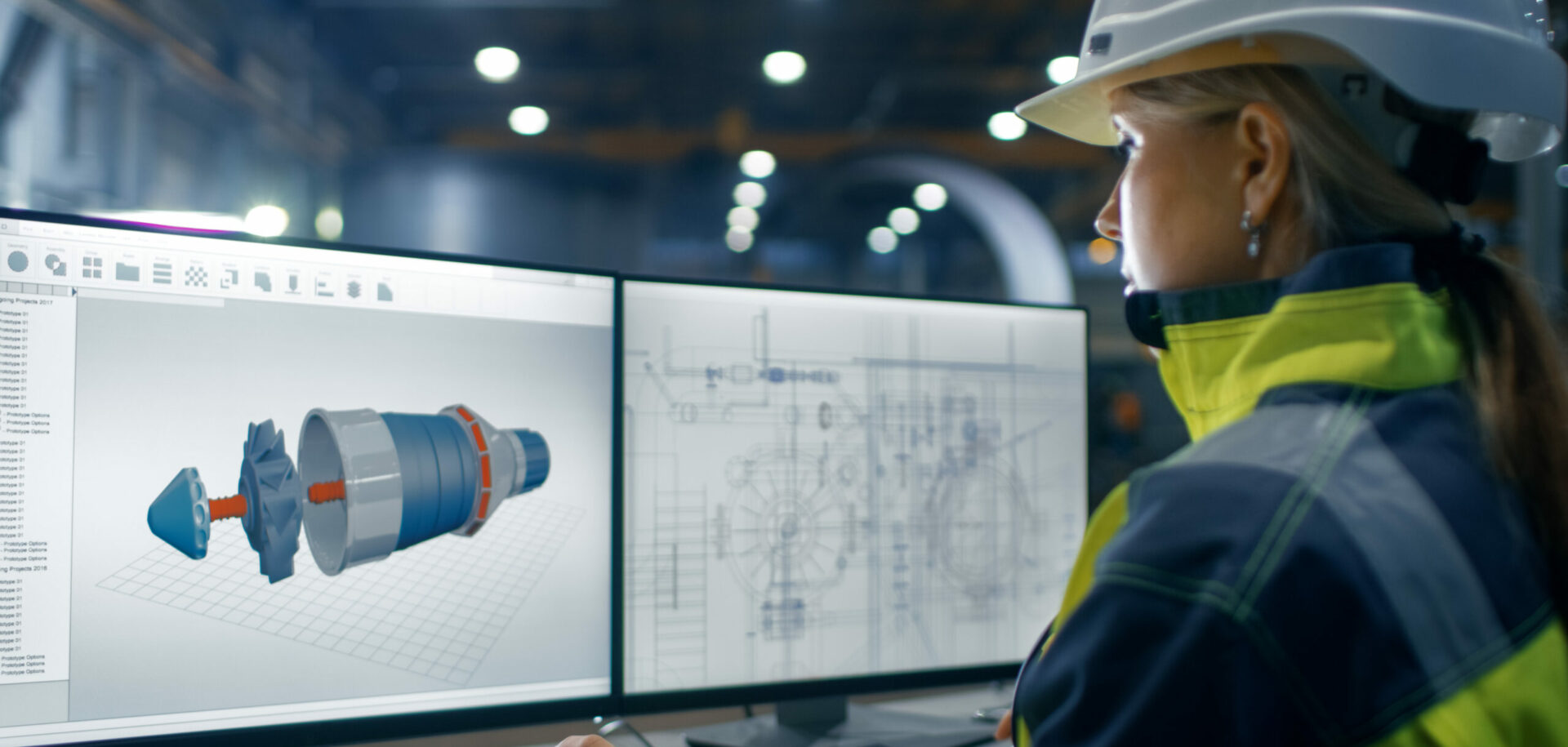
Always right on the spot
Spandau Pumpen handles the coolant supply for machine tools at the SKF Lubrication Systems plant in the Czech Republic.
An important part of ensuring high quality at low cost in metalworking applications is the reliable supply of coolants to the machine tools involved. At the SKF Lubrication Systems plant in the Czech city of Chodov, coolant pumps from Spandau Pumpen (fig. 3) are deployed for the machining process and for a modular island filter system (fig. 1), including a chip conveyor. Since their installation, supervisors have noted lower costs of energy and operations and higher system availability.
Progressive feeders for lubrication systems are among the products made at the SKF plant in Chodov. There had been problems, however, in the earlier production line. Internally cooled tools kept experiencing blockages due to residual dirt and grime. In addition, on the relatively slow machines, single-station solutions were used as the filter variant. SKF’s Manufacturing Technology project team, led by Steffen Siegemund of Germany, was tasked with ensuring that Chodov would produce more flexibly, with higher quality and at lower cost. It was decided to acquire fast single-spindle milling centres.
To clarify how chips could be handled efficiently and how coolant could be recovered and fed back into the production process, the SKF project team and the global purchasing department consulted with Mayfran GmbH in Aachen, Germany. Together with chip conveyor and filter systems specialists, they assessed and compared the advantages and disadvantages of the concepts for single-station and island solutions as well as centralized supply. The decision was ultimately made for a modular island system with a chip conveyor. Siegemund reports that he and his team were very satisfied with the solution. “We implemented the project successfully with Mayfran GmbH,” he says.
The filter system (fig. 2) serves two production lines, each with three machine tools ① ② ③ and ④ ⑤ ⑥ and a single-station solution ⑦. The system handles full-flow cleaning of chips down to 25 µm in size, plus down to 5 µm using a second fine-filter stage (bypass cleaning) using a hydrostatic paper filter ⑧. The medium filtered through this process is collected in the ultra-clean tank ⑬. The system is equipped with a secondary protective container and meets the requirements of the German Federal Water Act (WHG). It also has an immersion cooler ⑨ with a powerful control unit. The SKF plant is thus well prepared for increased production, and if needed it can bring this cooler on line to keep the coolant at a constant process temperature.
Support from within
The last piece, the right pump manufacturer, was still missing, but the SKF project team was able to find it within SKF: Spandau Pumpen, headquartered in Berlin, has been part of the SKF Group since 2004. The company develops and builds powerful solutions for centralized supply and disposal and for processing related to machine tools. “Spandau Pumpen is an independent brand within the SKF Group, so the decision to rely on in-house products was clear,” says Martin Zverina, plant manager in Chodov.
Spandau Pumpen is an independent brand within the SKF Group, so the decision to rely on in-house products was clear.
Martin Szerina
Plant manager in Chodov
Spandau Pumpen supplied three PS series low-pressure pumps (b) and three LMP series high-pressure pumps (c), each with frequency converters, for the modular island solution with chip conveyor. The standard commercial motors that were used could easily be retrofitted with a frequency converter using an adapter. The pumps with converters are operated in parallel, reducing the complexity of controls and increasing the dependability. Some components are designed redundantly to avoid system failures. The cleaning process always follows the same pattern. Spandau PSH rinsing pumps (a) feed the medium contaminated by machining from the machine tools back to the filter system.
The clarified and reusable fluid is fed into a reservoir ⑫. PS pumps (b) feed the filtered medium from this clean tank under low pressure, and the LMP screw pumps (c) feed the finely filtered medium back again under high pressure for reuse on the machines (fig. 2).
PSR flush pumps (d) clean the filter elements of the filter system ⑩ ⑪. PMS pumps (e) transfer medium from the sedimentation collecting tank back to filter elements ⑩ ⑪.
Due to parallel control of the pumps, with master function, they always operate according to demand and enable a long service life because they are loaded uniformly. The system feeds only as much coolant as required by the connected machines. The master or alternating control ensures a homogeneous running time of the individual pump units. Since not all process pumps are necessarily operational every day, a different master pump is selected every 24 hours, so all components are exposed to nearly identical levels of wear. The redundant pumps are checked regularly for proper function.
The sensors in the tubing feed the frequency converter with input on the actual state of the process pressure. The converter then controls the rotational speed of the pumps to maintain a consistent pressure level. This renders a bypass control unnecessary, as any additional energy requirement and unnecessary heat input into the coolant are avoided.
Efficient and powerful with low maintenance costs
Automatic adaptation of the speed by the frequency converter also compensates for a possible drop in performance due to wear on spindles or impellers. The desired working point continues to be controlled, and unplanned system downtime is avoided. An impending need for repair is thus detected in time, so maintenance work can be scheduled efficiently. The gentle system start-up using converter technology avoids pressure surges, protecting components such as fittings, hoses and filters and increasing the useful life of the entire system. The overall result is a notable reduction in operating costs in Chodov.
The system is also especially energy-efficient. “Based on consumption measurements and machining volumes, we’ve calculated energy consumption of just 40 % that of an operational single-station system,” reports Zverina – and that with energy savings of 60 % (fig. 2). Furthermore, four rinsing pumps (PSR series) for filter cleaning were incorporated into the system, as were two residual dirt pumps (PMS series) for removing residues. Two lift pumps (PSH series) each were provided for the chip conveyors with lateral pump stations (fig. 4). Thanks to this setup, the SKF plant is optimally equipped to meet the requirements.
The filter system has a modular design and can be expanded at any time. This can be done later as needed. The island filter system is also flexible with regard to the machine application. The same system type can still be used if, for example, a grinding centre or another milling machine line is added in Chodov. The only thing to change would be the filter quality.
The solution from Spandau Pumpen impressed the supervisors in Chodov from the start. They were pleased with the high availability when using the machines around the clock and the short maintenance periods. SKF emphasized a fully automated process in Chodov.
Baskets requiring manual cleaning in front of the lift pumps were not used. The components such as associated filter elements were specially developed for the purpose.
Spare capacity for further machines
Plant Manager Zverina reports that the reliability of machining has improved significantly. “We’re very satisfied with the performance of the entire system, especially the Spandau pumps (fig. 5),” he says. “They run 24 hours a day, seven days a week, and reliably supply seven key machines in our mechanical assembly area with coolant. We still have spare capacity in the high-pressure and low-pressure ranges for connecting up to two additional machines. With the solutions from Spandau Pumpen, the SKF plant in Chodov is strategically well positioned for the future. If other areas of production need to be converted to a similar production concept, another island system can be positioned and operated as a coolant network.
“Thanks to the modular design,” says Zverina, “it can be adapted to current demand at any time.”