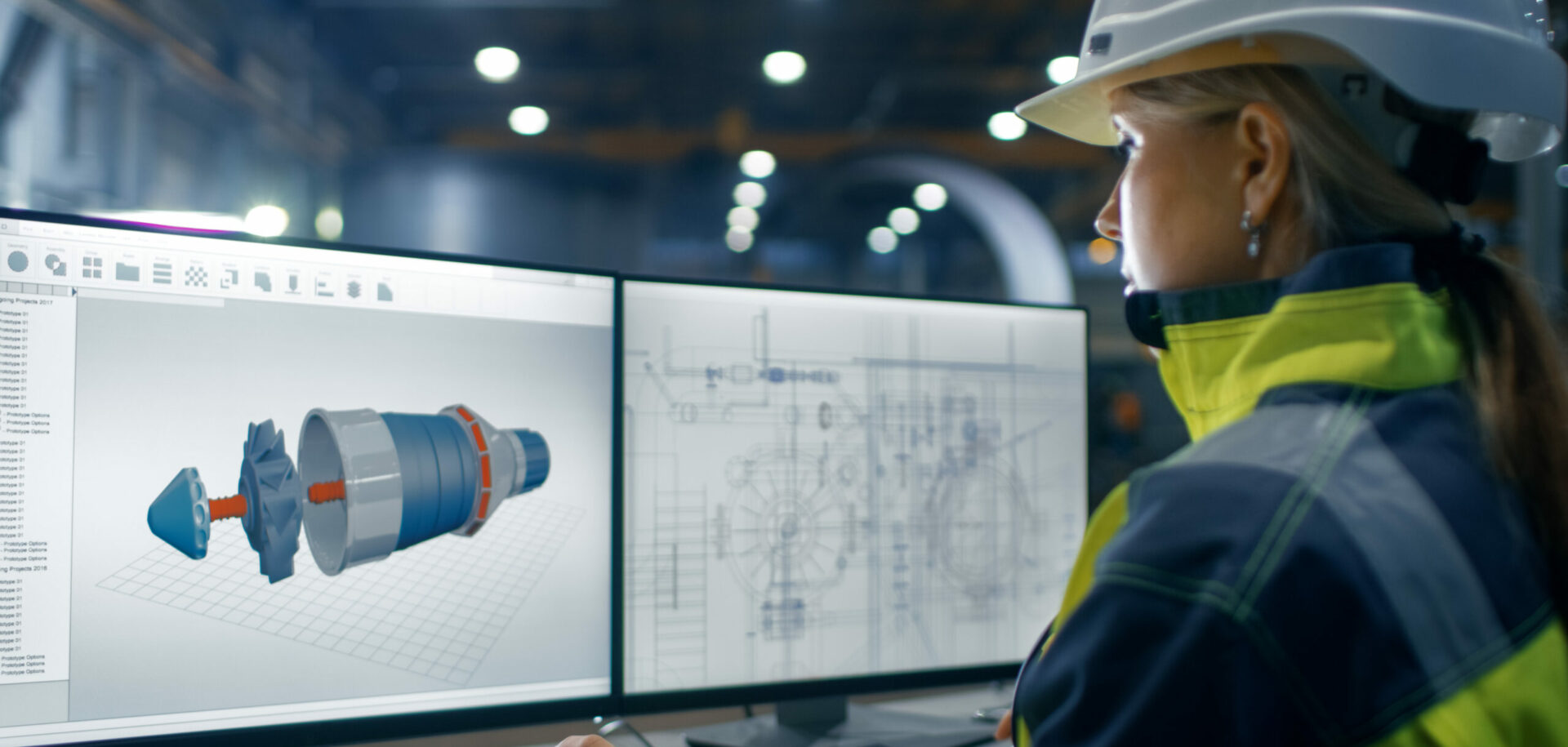
A grip on energy efficiency
SKF has developed a new family of bearings that reduce energy consumption by at least 30 percent compared with standard ISO products. This new bearing family comprises the world’s two most-used bearing types – deep groove ball bearings and tapered roller bearings.
SKF has developed a new family of bearings that reduce energy consumption by at least 30 percent compared with standard ISO products. This new bearing family comprises the world’s two most-used bearing types – deep groove ball bearings and tapered roller bearings.
The technical improvements that deliver the energy savings are design-related and combine surface topography, raceway profiles, optimized internal geometry, a special polymer cage, lower-friction grease and, in the case of the tapered roller bearing, also an optimized set of rollers. Manufacturing will start in the second half of 2007.
The energy-efficient tapered roller bearings are aimed at industrial segments where applications exceed one MW of power consumption, such as railway and transmissions in heavy industry, ships, wind energy, conveyors and extruders. First applications are expected to be in wind turbines.
The energy-efficient deep groove ball bearings will mainly be used in lightly loaded applications, and the first applications will be industrial elec-trical motors that drive machinery.
Web-based support for energy savings
Also, SKF has developed a Web-based Client Energy and Environment Analysis application (CEEA) that can significantly reduce energy consumption and save costs for process plants and manufacturing industries.
The CEEA establishes an “opportunity map” of potential energy savings and identifies those likely to give greatest savings as a function of percentage saved, payback period and cost.
Even small-percentage energy savings per machine can deliver huge cost savings on common equipment such as motors, pumps, fans, compressors, etc., when the effect across the whole plant is considered. In a typical oil refinery with more than 1,000 pumps, savings per pump could be as much as 20 percent.
Energy-efficient solutions
The prolonged work by SKF to develop products and solutions that help customers reduce their energy consumption, and thus their costs, has produced some excellent results:
• A reduction in energy consumption of more than 90 percent has been achieved in welding robots by replacing pneumatic actuators with compact SKF electromechanical actuators as the enabling technology for welding tongs in automotive plants in Germany.
• One million litres of fuel can be saved per business jet lifetime by the use of SKF Automatic Throttle Control units. The SKF Group has developed ATC units for business jets that enables a saving of 100 litres of fuel per flight hour, which is equivalent to 1 million litres over the lifetime of the jet.
• SKF electromechanical actuators and control units enable self-regulating sunblind systems to reduce energy consumption by 30–35 percent in the winter and 50 percent in the summer at the Berlaymont building in Brussels, which houses the headquarters of the European Commission.
In SKF’s own manufacturing operations
SKF has implemented a number of actions to reduce CO2 emissions and save energy in its factories. Already, in 13 factories, energy savings of 24 GWh have been made by installing more energy-efficient pumps and motors, new heating and energy recovery systems as well as new exhaust systems, recovering what would be “waste” heat, and by reducing compressed air usage and installing energy-efficient lighting.
The saving potential across the SKF Group is estimated to be up to 60 GWh per year, which is more than 2 percent of the Group’s current energy consumption.
CO2 reductions have been part of sustainability actions for a number of years, and the recent complete switch to “green” energy at the Gothenburg, Sweden, plant has given a 60 percent reduction compared with the use of non-green energy.
Says Tom Johnstone, President and CEO of SKF: “With these innovations and steps we will be able to support industry in making a significant contribution to energy savings today and in the future.”