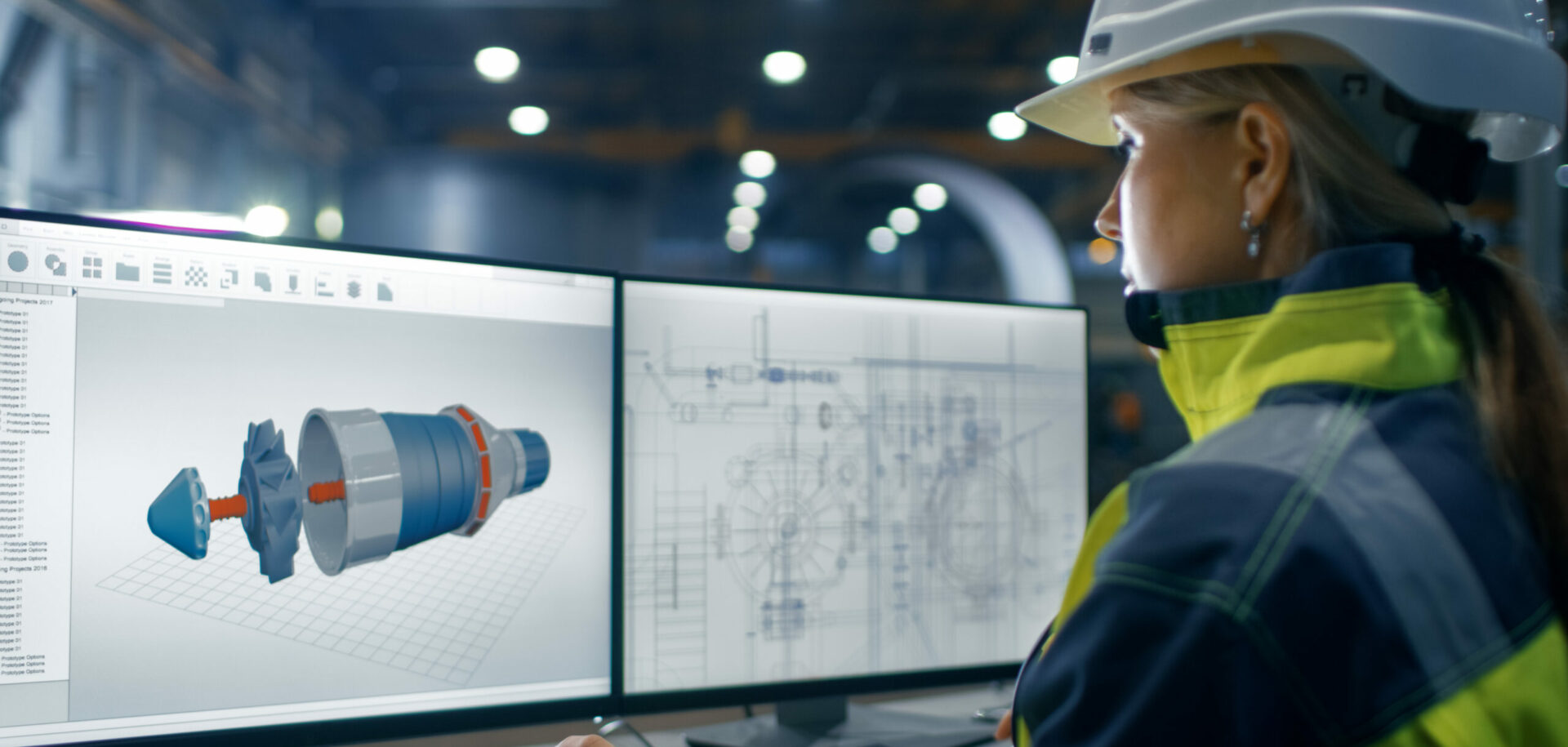
Summary
A new generation of engineering steels has been created that could transform the way bearings and other components are manufactured. Developed by SKF Group member Ovako Steel, the Ovatec family rethinks the concept of engineering steel manufacturing that has been the standard for more than a century.
The new steels offer high performance while eliminating processing steps that require the addition of polluting media. The main design criteria have coupled high-performance engineering applications with environmental friendliness, reduced total manufacturing costs and enhanced performance.
In the development of a steel family for high-performance environmentally friendly engineering applications, reduced total manufacturing costs and enhanced performance have been the main design criteria.The new steel family developed by Ovako Steel in Sweden, a subsidiary in the SKF Group, has been designated Ovatec, which is a registered trademark, and the steels are patent-protected. The reason behind the development effort is that billions of engineering components used in heavily loaded applications are produced in Europe each year. Common to all these products is the need to withstand awesome combinations of high stress, enhanced temperatures and dirty environments, and they also need to do this for very long times without failing. It is essential that they can be produced at a low total cost.
Bearing components and gears are typical examples of such products. Repeatable and highly robust quality and performance are required in order to assure customer satisfaction.
The steels used to produce such components today were first developed more than 100 years ago. Though they have proven their value over the century, today’s requirements for environmental friendliness, productivity, total manufacturing cost and performance make it necessary to re-think steel design, taking into account the long experience of steel-making technology.
Component production today
Since large-scale production of high- performance components has evolved – closely associated with the introduction of the automobile in the early 20th century – tremendous amounts of research have been devoted to improving the manufacturing and the performance of such components. Most of the research and development work can be summarised into a few categories directed towards improving:
- Steel cleanliness
- Hot formability
- Soft machinability
- Heat treatment and distortion
- In-line heat treatment
- Hard machinability
- Performance
Future component production
Using the wealth of existing knowledge complemented with the newer modelling tools available today to predict transformational behaviour based on steel composition, a new family of steels has been designed, developed and patent-protected.
The common denominator for this small family of steels is that they can be used for large-scale steel and component manufacture in a way not earlier available, using the standard steels available today. The Ovatec steels all have the capability to harden on air-cooling, for example. There are other benefits that open up in the application of these new steels in heavy-duty component applications.
There are hundreds of standardised steel grades in use today for the production of components. One common requirement for all of them is that they all need to be hardened to attain the desired properties. This involves a final heat treatment, which provides the components with the required hardness and wear resistance.
The three heat treatments employed to achieve final steel properties today are case hardening, tough tempering and through hardening. The three main steel categories used to achieve the desired properties are categorised accordingly – case hardening steels, tough tempering steels and through hardening steels. Rolling bearing steel, which is used for many applications beyond rolling bearings, is a typical through hardening steel.
The Ovatec steel family has been designed to have one member in each of these three steel groups. The range comprises one case hardening steel, one tough tempering steel and one through hardening steel (Fig.1). These three steels can replace the hundreds of variants currently used to produce components. It also has the benefit of significant environmental, economical and performance advantages. The common denominator for these steels is that they all have the capability of being hardened in a slow cooling process from hot forming or austenitising temperatures. By contrast, the standard steels used today for component manufacture must be quenched with a very high cooling rate in order to achieve the properties desired. This, unfortunately, means the use of polluting and health- hazardous fast-quenching media.
Steel cleanliness
In modern production of components for heavily loaded applications, high steel cleanliness is a pre-requisite. As the non-metallic inclusions always present in steel provide initiation sites for fatigue failure, their total contents must be minimised, and the size distribution of such defects must be carefully monitored. With the submerged ultrasonic techniques currently available, the occurrence of large inclusions can be controlled, and with the alloy design selected for the new steel family, it can be assured that very clean steel can be produced. Figure 2 shows the oxygen content of full scale produced Ovatec 677 heats. This is somewhat lower than what is achieved for standard bearing steels. Oxygen forms hard, brittle oxidic inclusions that impair fatigue properties of hard steels.
Hot formability
The hot forming is a crucial operation in the production of the pre-forms manufactured for component production. The Ovatec family of steels can be hot or warm, formed in the same way as the standard steels. The novel aspect of the new family is that forming heat can be used to instantaneously generate the properties required after a conventional heat treatment. The hot forming can be conducted in the same way as it is performed today, in some cases perhaps requiring a slightly higher forming force than currently used. Using hot forming temperatures to provide components with their final properties is not possible with conventional steels.
Machinability
Heat treatment cycles have been developed for all the three Ovatec steel grade variants. This offers not only equal, but on many occasions superior machinability compared with traditional steels. One reason for this is that the Ovatec family steels guarantee a fully homogenous structure for all the variants produced. This is exemplified in Fig. 3, which shows comparative machining data for Ovatec 677 and SKF Grade 3 steel.
Heat treatment and distortion
The Ovatec family of steels have a hardenability that makes it possible to achieve a very high hardness, high performance structure even if the components hardened are cooled in a still air environment. This is very different from conventional steels, where cooling to low temperatures must be achieved within seconds to assure that the desired properties are achieved. The need to quench the currently used standard steels rapidly is a major reason for undesired and unpredictable dimensional change. This is one of the main problems generated in heat treatment today. With the new steel range, the cooling rate can be reduced significantly and the desired properties still can be attained (and in many aspects surpassed), due to the alloying design selected. The reduced cooling rate requirements provide a situation where hardening distortion can be largely reduced. Consequently, the very high cost of the grinding operations required to rectify the loss of geometrical precision caused by the heat treatment can be significantly reduced.
One example of this is given in Fig. 4, where the outer diameter out-of-roundness before and after air hardening of 50 small spherical roller bearing outer rings are compared.
The Ovatec family also adds a significantly increased robustness to the heat treatment process. Where a standard bearing steel needs to have a temperature control within a 10 ºC variation to achieve the desired properties, the Ovatec family allows 30 times this variation range.
In-line heat treatment
In heat treating today’s steels, either an in-house central heat-treating shop or an external heat-treating facility is used. With the Ovatec steels it is very easy to arrange a hardening unit that can match the production set-up in soft machining. Neither fire nor hazardous media need to be used in the working environment, and the Ovatec family steels can be hardened in a very robust way. It is straightforward to incorporate the heat treatment into the production chain.
Ovako Steel has installed a pilot plant for air hardening of components, which was built and supplied by the company Inline-hardening in Sweden. The pilot production cell comprises a soft machining unit with a robot that automatically feeds the hardening pilot plant. There, the components are austenitised in a magnetic heater, controlled air-cooled in an enclosed tunnel whereafter tempering takes place in a second magnetic heater. The process is fast, robust, environmentally friendly and can produce components to very tight tolerances.
Hard machinability
The most costly production step in component manufacturing today is the machining that needs to be carried out to rectify the distortion generated in the heat-treatment operation. It is not unusual that the final grinding on a component such as a roller bearing ring or a gear accounts for 20–40 % of the total component cost. It has been proven that the Ovatec family of steels can reduce the costs of this final operation because of the reduced distortion in the heat treatment. The hard machining in itself is far easier (Fig. 5), and offers new exciting processing possibilities, described later.
Performance
A number of tests within the SKF Group and outside have shown that the Ovatec family of steels provides improved component fatigue life (Fig.6), enhanced wear resistance, better dimensional stability, significantly reduced hardening distortion and improved property robustness.
New processing routes
The Ovatec family of steels provides completely new opportunities in component production. One fundamental aspect of these steels is that it is fully possible to produce high-performance products by allowing the components produced to harden on the cooling from hot forming temperatures. This is not possible with existing steels. The basic reason for this difference lies in the design of the steels. Traditional bearing steel never can be heated to a temperature above 900 ºC and hardened without giving severe quality problems. Ovatec steels, by contrast, can be heated to 1,200 ºC and allowed to air harden without any negative quality consequences.
This means that the processing heat is used to achieve the hardening required.
One example has successfully shown that deep groove ball bearing rings can be produced directly from tubes that are allowed to harden on the cooling beds in the tube rolling mills.
Potentially, this makes it possible to replace the re-heating and cumbersome soft annealing, the soft machining, the hardening operation and a very large share of the grinding of rings by a dry hard turning and a final grinding of a very high precision hard-turned and metallurgically finished ring.
A second example is where finished bearings have been produced and successfully endurance-tested, the current route of producing medium-sized bearings (ring rolling, soft annealing, soft machining, heat treatment, grinding, polishing) could very successfully be replaced by ring rolling, hard turning and polishing.
In both examples, significant improvements can be made in reducing environmental pollution. Annealing requires large energy expenditure, soft machining requires polluting cooling media, heat treatment uses significant energy, protective gases and the quenching media needed for today’s steels are health and fire hazards, grinding requires severely polluting cooling media, leaving hard-to-recover residues. Using the air-hardening capabilities of the Ovatec family of steels, it is easy to imagine and achieve an almost pollution-free production of components with extremely short lead times and very high flexibility.
Thore Lund
Ovako Steel AB, Sweden