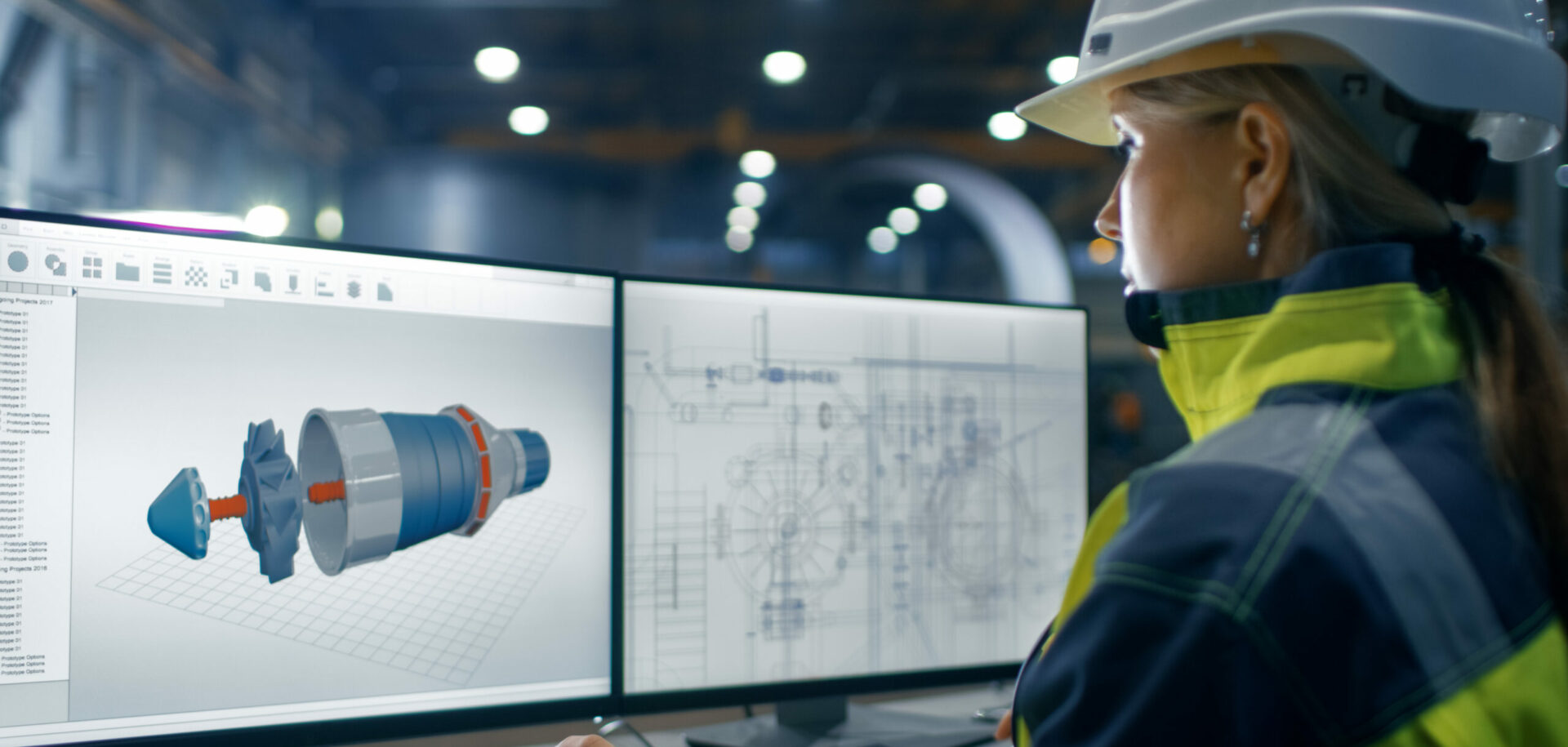
Automatic lubrication enhances reliability
Automatic centralized lubrication systems for heavy machinery in construction, civil engineering and mining industries pay off quickly. They reduce the risk of machine failure and support improved machine productivity.
Meeting ever-tighter project deadlines is critical in the construction and civil engineering industries. Construction machines must be in top shape, so they can reliably achieve high productivity at all times. If they aren’t, the schedule is at risk of slipping, which usually leads to incalculable follow-up costs. This can be very frustrating, especially if the construction machine fails due to inadequate lubrication or defective seals.
Friction, wear, corrosion and dirt cause significant damage to mechanical components, but there is a tried and proven way to counteract them: tailored centralized lubrication systems that automatically lubricate and protect the right points, using the right amount of the right lubricant at the right time. Which system provides the best results in terms of economic and ecological aspects depends largely on the type of machine, ambient temperature and operating conditions. The magic word here is: customization!
Centralized lubrication systems developed by SKF for construction machinery deliver high operational reliability thanks to their sturdy construction. They employ piston pump units of the KFG(S) series with an integrated control unit (fig. 1). The lubricant is distributed using progressive feeders, which consecutively supply the quantity of grease required to the individual lubrication points as long as the pump is running, making sure that each point receives optimum
lubrication.
Simple monitoring technique
SKF has developed a quasi-analogue fill-level switch so that the operator can get an overview of the current fill level of the pump reservoir at any time. It detects the change in the fill level digitally and displays this change in analogue steps, for example in 0.5-litre increments. This technology enables the machine operator to top up the reservoir in time and when convenient, for example during work breaks between machine usage. When the signal is evaluated systematically, it can even be used to determine the lubricant consumption. A service request can be initiated in the event of large deviations from normal consumption.
SKF’s IG502 base unit is a universal, yet simple control system for progressive centralized lubrication systems. At the Bauma 2010 trade fair, SKF presented the new LC502 control unit, which offers a range of new and improved features (fig. 2). Although the IG502 control unit is still offered as the standard device, the new LC502 control unit and its numerous new options open up a wide range of applications. Of particular note are the new control options using various parameters. In addition to time-dependent control in minutes, it can now also be controlled, based on pump speed. This provides the benefit of preventing pump speed variations that are not considered when using solely time-dependent control. Speed variations can result from thermal or viscous factors, voltage fluctuations and other reasons. Precise lubricant distribution is especially important for lubrication points with low grease requirements and correspondingly low metering volumes.
The new device also stands out in terms of highly reliable lubrication, as it can monitor up to three zones. It is also equipped with wire breakage monitoring and internal overload protection.
SKF engineers also developed a new 5/4 directional control valve for large construction machines in which the lubrication system must be divided into multiple independent zones (fig. 3). The valve incorporates an input that can be switched to one of the four outputs at a time, which enables up to four independent zones to be supplied with lubricant and monitored by a separate control unit. CAN (Controller Area Network) bus technology can be used to optimize the lubrication of construction machinery in another way by integrating the centralized lubrication system into the machine’s onboard communication network. This of course requires corresponding preparations by the manufacturer, as a simple retrofit of existing machinery is not practical.
SKF developed the FK pump unit to meet the high demands in the lubrication of heavy machinery in terms of lubricant supply, lubricant consumption and long lines, for example in the mining sector. The unit has a modular design and sturdy construction and offers a high degree of operational reliability, even when using highly viscous lubricants. It is designed for operating pressures of up to 400 bar (40 MPa). The special feature of the FK pump unit is that when ordering, the customer can configure the unit so that it is optimally suited for the desired application. The lubricant reservoir is supplied in a 15 kg, 30 kg or 60 kg capacity. The lubricant delivery rate can be set between 12 and 74 cm3/min, in increments. The electrical supply in VAC or VDC enables the FK pump unit to be integrated into all common mobile or stationary systems.
Retrofitting is easy
Construction machinery without centralized lubrication systems can be retrofitted with reasonably little effort, provided the required kits fit the particular machine type and can be mounted easily and quickly. SKF retrofitting kits meet both of these requirements. They have been manufactured according to the specifications of notable OEMs, and they meet their requirements and lubricant standards. The kits are available in all designs; the same applies to the repair kits. To make sure that retrofitting or repair can be performed without complications, SKF provides complete kits with all necessary components, plus the plans and instructions for assembly of a centralized lubrication system for the particular type of construction machinery. Assembly can be performed by an SKF service technician on request.
Autonomous lubrication unit for hydraulic hammers and other attachments
Hydraulic hammers require a different lubricant than other lubrication points on an excavator. Practical experience shows that customers use this type of attachment independently of the carrier device. The challenge for SKF’s engineers was to develop a pump unit that is autonomous and space saving and has low maintenance needs. The result was the HS04 hydraulically driven autonomous lubricator, which is designed to reliably feed the special lubricants, known as chisel pastes, with high solids content, which are required by hydraulic hammers. The lubricator is mounted directly onto the tool and connected to the machine’s existing hydraulic system. As soon as the tool starts to operate, i.e., once the hydraulic system is activated, the pump lubricates the connected lubrication points. It is possible to regulate the quantity of lubricant delivered. Instead of the conventional grease reservoir, the HS04 is equipped with a standard-thread cartridge that is very easy and convenient for operators to replace. SKF also offers various adapter options.
The lubricator’s technical highlight is its patented, sophisticated drive system. Mounting on a hydraulic hammer places very high demands on a lubrication unit. In addition to dirt and dust encountered during operation, the unit must also withstand hard jolts and vibrations. When designing the HS04, a purely hydraulic solution was selected instead of a mechanical power transmission, a concept whose reliability has been proven in numerous field tests.
The lubricator can be used for more than just hydraulic hammers. Keep in mind that we are talking about a hydraulically driven, autonomous, space saving and low-maintenance pump unit. Many attachments and additional tools for construction machinery do not have their own power supply, are hydraulically driven, and have points that absolutely require lubrication. Tools such as these include demolition grapples, screening buckets, etc. The HS04 is an excellent solution for making sure and improving productivity for this kind of equipment too, as the HS04 can of course feed standard greases of NLGI class 2 in addition to chisel paste.
Customer experience
Centralized lubrication helps to significantly reduce environmental impact
Just how much does equipping a machine with centralized lubrication help the environment? To answer this question with reliable, empirical data, SKF’s Thilo Standhardt approached Andreas Englisch, the technical director of Albert Weil AG in Elz, a city in Germany about halfway between Frankfurt/Main and Bonn. Weil has a fleet of more than 50 construction machines ranging from 3 to 87 tonnes overall in weight and is a longstanding SKF customer (fig. 4).
SKF was able to determine the lubricant savings for two reference models very accurately, thanks to Weil’s practical experience and the parameters that were available for the output of centralized lubrication systems. An Atlas 82E small wheel loader (fig. 5) and a 45-tonne Hitachi ZX 470 crawler excavator (fig. 6) were selected. Weil’s fleet includes 20 of the small wheel loaders and 28 crawler excavators ranging from 15 to 87 tonnes gross weight.
Provided that the machines are maintained daily and according to instructions, the use of automatic centralized lubrication systems yields a calculated annual lubricant savings of approximately 28 % or 668 kg for the entire fleet.
This calculation is based on the following practical assumptions:
-
8 operating hours per day
-
5 days per week
-
1 stroke of the manual grease press represents approximately 2 cm3
-
1 cm3 = 1 gram
-
Manual grease lubrication according to instructions – actuate grease press until visibly clean grease discharges at the lubrication points
The calculation was performed as follows:
Grease consumption using manual lubrication
-
20 wheel loaders 1,132,800 cm3
-
28 excavators 1,236,500 cm3
-
Per year: 2,369,300 cm3 (approx. 2,369 kg)
Grease consumption with centralized lubrication:
-
20 wheel loaders 752,600 cm3
-
28 excavators 948,900 cm3
-
Per year: 1,701,500 cm3 (approx. 1,701 kg)
Difference between manual and centralized lubrication: 667,800 cm3 (approx. 668 kg)
Centralized lubrication results in approximately 28 % savings of consumption when compared to manual lubrication (668/2,369).
In reality, the actual lubricant savings in Albert Weil’s machinery are even larger, because in practice, operators tend to press one additional stroke of grease (an additional 20 %) into the grease nipple rather than use too little.