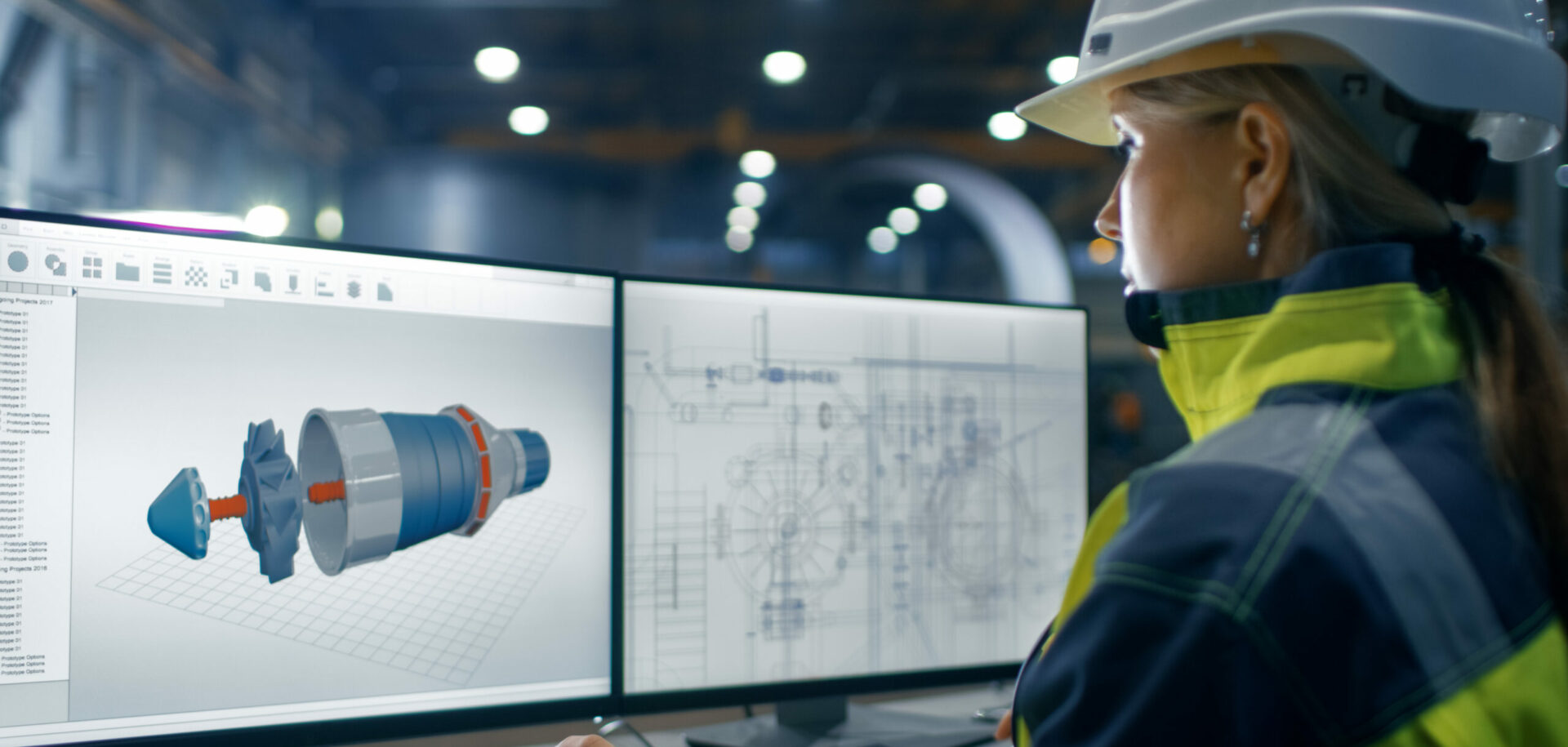
La lubrification automatique au service de la fiabilité
Les systèmes de lubrification centralisée automatique pour les engins lourds utilisés dans les secteurs du BTP et de l’exploitation minière sont vite rentabilisés. Ils réduisent les risques de défaillance des machines et améliorent leur productivité.
Les systèmes de lubrification centralisée automatique pour les engins lourds utilisés dans les secteurs du BTP et de l’exploitation minière sont vite rentabilisés. Ils réduisent les risques de défaillance des machines et améliorent leur productivité.
Technologie
La tenue de délais toujours plus serrés est décisive dans les projets de construction et de génie civil. Les engins de construction doivent en permanence fonctionner au maximum de leurs performances pour offrir à tout moment fiabilité et productivité élevées. Dans le cas contraire, le planning risque d’être dépassé, ce qui se traduit généralement par des coûts supplémentaires incalculables. Cette situation peut être très frustrante, notamment si la panne de l’engin de construction est due à une lubrification inadaptée ou à des joints défectueux.
Le frottement, l’usure, la corrosion et la saleté mettent les pièces mécaniques à rude épreuve, mais il existe un moyen éprouvé de les contrer : les systèmes de lubrification centralisée sur mesure qui lubrifient et protègent les points sensibles de façon automatique, en délivrant le bon lubrifiant, dans les bonnes quantités, au bon moment. Le système offrant les meilleurs résultats sur les plans économique et écologique dépend en grande partie du type d’engin, de la température ambiante et des conditions de service. Les mots magiques sont : conception sur mesure !
Les systèmes de lubrification centralisée mis au point par SKF pour les engins de construction offrent une fiabilité opérationnelle élevée grâce à leur construction robuste. Ils reposent sur des pompes à piston de la série KFG(S) avec boîtier de commande intégré (Fig. 1). Des distributeurs progressifs délivrent la quantité de graisse requise successivement aux différents points de lubrification pendant le fonctionnement de la pompe, en garantissant une lubrification optimale de chaque point.
Une technique de contrôle simple
SKF a développé un niveau-contact quasi-analogique qui permet à l’opérateur de connaître à tout moment le niveau de remplissage du réservoir de la pompe. Il détecte une variation du niveau de remplissage et affiche sa valeur sous forme analogique, par exemple par paliers de 0,5 litre. Cette technologie permet à l’opérateur de la machine de remplir le réservoir au moment le plus opportun, par exemple pendant les mises à l’arrêt entre deux utilisations. Une évaluation systématique du signal peut même être mise à profit pour déterminer la consommation de lubrifiant. En cas d’écarts importants par rapport à la consommation normale, une demande d’intervention pourra alors être émise.
L’unité IG502 de SKF constitue un dispositif de commande à la fois simple et universel pour les systèmes de lubrification centralisée progressifs. Le salon Bauma 2010 fut pour SKF l’occasion de présenter le nouveau boîtier de commande LC502 qui offre une série de fonctionnalités nouvelles et améliorées (Fig. 2). Bien que le boîtier de commande IG502 soit toujours proposé en standard, la nouvelle unité LC502 et ses nombreuses nouvelles options viennent étendre la gamme d’applications. Il convient de mentionner en particulier les nouvelles options de commande basées sur différents paramètres. Outre la commande en fonction d’un temps, réglable en minutes, cette unité offre désormais une commande basée sur la vitesse de la pompe. L’intérêt est d’éviter les variations de vitesse de la pompe qui ne sont pas prises en compte dans le cas d’une commande uniquement basée sur un temps. La vitesse peut varier sous l’effet de facteurs thermiques ou de viscosité, de fluctuations de tension et d’autres éléments. Une distribution précise du lubrifiant est particulièrement importante pour les points de lubrification qui nécessitent de faibles doses de graisse.
Ce nouveau dispositif se démarque également en termes de fiabilité de la lubrification par sa capacité à contrôler jusqu’à trois zones. Il est également équipé du contrôle de rupture de fils de connexion et de la protection contre les surcharges internes.
Les ingénieurs SKF ont également mis au point un nouveau distributeur 5/4 voies pour les gros engins de construction sur lesquels le système de lubrification doit être divisé en plusieurs circuits indépendants (Fig. 3). La vanne est dotée d’une entrée qui peut être basculée sur une des quatre sorties à la fois, ce qui permet d’alimenter en lubrifiant et de contrôler par le biais d’un boîtier de commande distinct jusqu’à quatre circuits indépendants. La technologie de bus CAN (Controller Area Network) peut être utilisée pour optimiser la lubrification des engins de construction d’une autre manière, en intégrant le système de lubrification centralisée au sein du réseau de communication embarqué de l’engin. Cela nécessite bien sûr des aménagements appropriés de la part du fabricant, car une simple adaptation sur l’engin existant s’avère peu pratique.
SKF a développé le groupe motopompe FK pour répondre aux exigences les plus strictes concernant la lubrification des machines lourdes en termes d’alimentation en lubrifiant, de consommation de lubrifiant et de grandes longueurs de lignes, comme, par exemple, dans l’industrie minière. Le groupe est conçu de façon modulaire, se distingue par sa robustesse et offre un niveau élevé de fiabilité opérationnelle, y compris lorsque des lubrifiants extrêmement visqueux sont utilisés. Les pressions de service peuvent atteindre jusqu’à 400 bars (40 MPa). Le groupe motopompe FK a ceci de particulier que le client peut, lors de la commande, le configurer pour l’adapter au mieux à l’application envisagée. Le réservoir de lubrifiant est disponible avec une capacité de 15, 30 ou 60 kg. Le débit de distribution du lubrifiant peut être réglé par paliers entre 12 et 74 cm3/min. L’alimentation électrique, en courant alternatif ou continu, permet l’intégration du groupe motopompe FK dans tous les systèmes fixes ou mobiles courants.
Mise à niveau facile
Les engins de construction non équipés de systèmes de lubrification centralisée peuvent être mis à niveau sans trop d’effort, à condition de disposer de kits, faciles et rapides à installer, adaptés au type d’engin particulier. Les kits de mise à niveau SKF répondent à ces deux exigences. Ils ont été fabriqués d’après les spécifications de grands constructeurs et répondent à leurs exigences ainsi qu’aux normes sur les lubrifiants. Ils sont disponibles dans une grande variété de modèles. Il en va de même pour les kits de réparation. Pour garantir une mise à niveau ou une réparation sans complication, SKF fournit des kits complets incluant tous les éléments nécessaires, ainsi que les plans et instructions pour le montage d’un système de lubrification centralisée sur un type d’engin de construction donné. Le montage peut être effectué par un technicien de maintenance SKF sur demande.
Système de lubrification autonome pour marteaux et autres équipements hydrauliques
Les marteaux hydrauliques nécessitent un lubrifiant différent de celui des autres points de lubrification sur une excavatrice. L’expérience pratique montre que les clients utilisent ce type d’équipement sur différents engins. Le défi pour les ingénieurs SKF consistait donc à développer une unité qui soit autonome, peu encombrante et peu exigeante en termes de maintenance. Ainsi est née la pompe hydraulique autonome HS04, conçue pour une distribution fiable de lubrifiants spéciaux (connus sous la dénomination de pâtes à burin, à forte teneur en particules solides), qui sont utilisés pour la lubrification des marteaux hydrauliques. La pompe est montée directement sur l’outil et connectée au système hydraulique existant de l’engin. Dès que celui-ci démarre, autrement dit dès l’activation du système hydraulique, la pompe assure la lubrification des points de lubrification connectés. Il est possible de régler la quantité de lubrifiant délivrée. En lieu et place du réservoir à graisse conventionnel, la pompe HS04 est équipée d’une cartouche à visser à filetage standard pouvant être remplacée très facilement par les opérateurs. SKF propose également différentes options d’adaptateurs.
La particularité technique de la pompe réside dans son système d’entraînement sophistiqué breveté. Installé sur un marteau hydraulique, un dispositif de lubrification est soumis à rude épreuve. Outre l’exposition à la poussière et la saleté, l’unité doit également supporter des secousses et des vibrations très importantes. Lors de la conception de la pompe HS04, une solution purement hydraulique a été préférée à une transmission mécanique en raison de la fiabilité du concept démontrée par de nombreux tests sur le terrain.
Le système peut être utilisé sur des équipements autres que les seuls marteaux hydrauliques. N’oubliez pas que nous parlons d’un groupe motopompe hydraulique, autonome, peu encombrant et peu exigeant en termes de maintenance. De nombreux équipements et autres outils pour engins de construction, également hydrauliques, ne disposent pas de leur propre alimentation et comptent un certain nombre de points qui doivent absolument être lubrifiés. Parmi ces outils, citons les grappins de démolition, les godets de criblage, etc. La pompe HS04 constitue une excellente solution pour garantir et améliorer la productivité de ce type d’équipements également, car, outre la pâte à burin, la pompe HS04 peut également distribuer des graisses standard de grade NLGI 2.
Retour d’expérience d’un client
La lubrification centralisée pour réduire de façon significative l’impact sur l’environnement.
Dans quelle mesure le fait d’équiper un engin d’un système de lubrification centralisée est-il bon pour l’environnement ? Pour répondre à cette question à partir de données empiriques fiables, Thilo Standhardt de SKF a contacté Andreas Englisch, directeur technique d’Albert Weil implanté à Elz, ville allemande située environ à mi-chemin entre Francfort et Bonn. L’entreprise, qui dispose d’une flotte de plus de 50 engins de construction de 3 à 87 tonnes, est un client de longue date de SKF (Fig. 4).
SKF a été en mesure de déterminer les économies de lubrifiant pour deux modèles de référence avec une grande précision, grâce à l’expérience pratique de Weil et aux paramètres déjà disponibles concernant le rendement des systèmes de lubrification centralisée. Une petite chargeuse à pneus Atlas 82E (Fig. 5) et une excavatrice à chenilles Hitachi ZX 470 de 45 tonnes (Fig. 6) ont été sélectionnées. La flotte de Weil compte 20 petites chargeuses à pneus et 28 excavatrices à chenilles de 15 à 87 tonnes.
Pour un entretien quotidien des engins conforme aux instructions, l’utilisation de systèmes de lubrification centralisée automatique permet, d’après les calculs, d’économiser sur un an environ 28 %, soit 668 kg, de lubrifiant pour l’ensemble de la flotte.
Ce calcul est basé sur les hypothèses pratiques suivantes :
-
8 heures de fonctionnement par jour
-
5 jours par semaine
-
1 course de la pompe à graisse manuelle équivaut à environ 2 cm3
-
1 cm3 = 1 gramme
-
Lubrification manuelle à la graisse conformément aux instructions : actionnement de la pompe à graisse jusqu’à visualisation de la graisse propre délivrée au niveau des points de lubrification
Le calcul a été effectué comme suit :
Consommation de graisse en lubrification manuelle
-
20 chargeuses à pneus 1 132 800 cm3
-
28 excavatrices 1 236 500 cm3
-
Par an : 2 369 300 cm3 (env. 2 369 kg)
Consommation de graisse avec la lubrification centralisée
-
20 chargeuses à pneus 752 600 cm3
-
28 excavatrices 948 900 cm3
-
Par an : 1 701 500 cm3 (env. 1 701 kg)
Différence entre lubrification manuelle et lubrification centralisée : 667 800 cm3 (env. 668 kg)
La lubrification centralisée permet une baisse de la consommation d’environ 28 % par rapport à la lubrification manuelle (668 sur 2 369).
En réalité, les économies de lubrifiant réalisées sur les engins d’Albert Weil sont encore plus importantes car, dans la pratique, les opérateurs ont plus tendance à actionner une fois en plus la pompe à graisse (surplus de 20 %) dans le raccord de graissage plutôt que d’injecter une dose insuffisante.