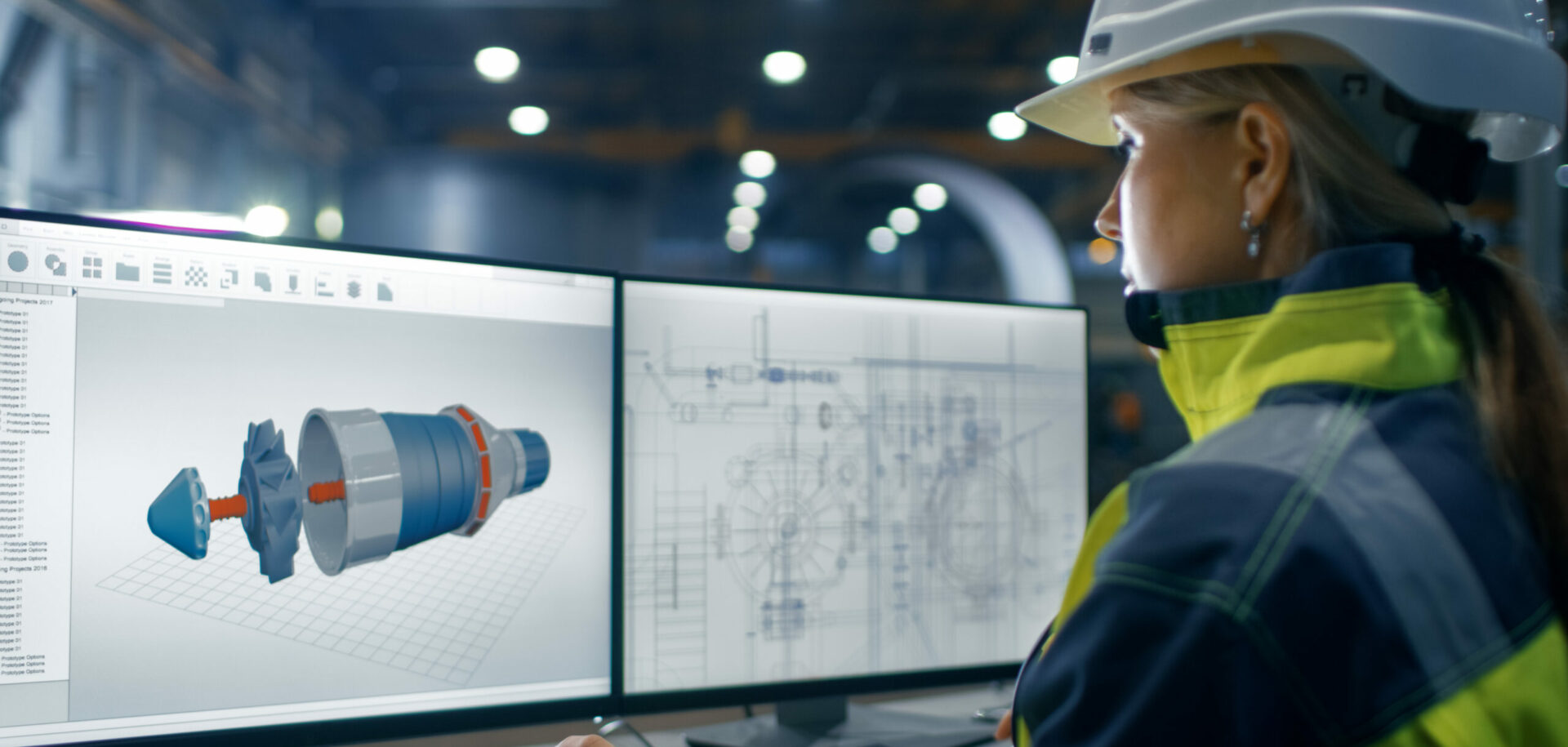
Axial load carrying capacity
Demanding applications with larger size cylindrical roller bearings are the motivation behind studies on the dynamic axial load carrying capacity for this bearing type.
In order to establishthe dynamic axial load carrying capacity of cylindrical roller bearings, different criteria compared with those used for the radial load carrying capacity need to be considered. Relevant are the application limitations to prevent wear, overheating and smearing in the flange contact, as well as flange fracture.
As a result of this work, the current SKF catalogue formula for dynamic axial load carrying capacity has been reviewed and new insights, e.g. for oil flow cooling
incorporated.
Design and applications of cylindrical roller bearings
In many applications, cylindrical roller bearings are used for the non-locating bearing position (N and NU designs) to accommodate axial displacement between the shaft and housing within the bearing, e.g. resulting from thermal expansion of the shaft. These bearings can only take radial loads. Cylindrical roller bearings with flanges on both inner and outer rings can support axial loads additionally – NJ design bearings in one direction and NUP or NJ+HJ design bearings in both directions (fig. 1).
An axial load between the inner and outer rings is transmitted between the flanges and the roller ends (fig. 2). The kinematic conditions in the flange contact always lead to a certain amount of sliding in the contact area (fig. 3), raising the total friction in the bearing. To improve this, SKF has continuously optimized the flange and roller end profiles. Nowadays the flanges have a slightly open design and roller ends are “blended” with an especially developed profile. This design ensures that the contact area is kept close to the flange undercut, so that even in case of roller skewing and tilting, the lubricant film build-up is realized. The result is reduced sliding friction and minimized stresses in the undercut.
Application limits
The radial load carrying capacity of cylin-drical roller bearings is based on “classical” sub-surface fatigue theory. For axially loaded cylindrical roller bearings, however, the following criteria need to be considered:
-
frictional heat due to sliding in the roller end/flange contact
-
wear at the flanges and roller ends
-
smearing damage at the roller end/flange contact (fig.4)
-
disturbed kinematics if the axial load is too heavy compared to the radial load
-
flange fracture due to static or dynamic overloading
-
reduced grease life requiring shorter relubrication intervals if a constant axial load is applied.
Dynamic axial load carrying capacity
The dynamic axial load carrying capacity is a value for the permissible axial load that ensures a stable bearing operating temperature at 60°C above ambient temperature. That means that the frictional heat generated inside the bearing is equal to the heat dissipation via the shaft and housing at that temperature. This criterion has shown to be a good indication for safe operation without smearing at the flange contact, provided that lubrication conditions are adequate (viscosity ratio 2). The current SKF catalogue formula is based on a constant specific heat loss factor for all bearing sizes and a friction model taking into account SKF specific profiles and surface finishes:
where:
Fap permissible axial load [kN]
C0 basic static load rating [kN]
Fr actual radial bearing load [kN]
n rotational speed of the inner ring [r/min]
d bearing bore diameter [mm]
D bearing outside diameter [mm]
B bearing width [mm]
k1, k2 factors (=> table 1).
New developments
The SKF catalogue formula (1) was developed in the 1980s and has proved to have an excellent agreement with experimental results and feedback from the field. In the past few years, however, following the rapid development of new larger-size and high power-density industrial gearboxes designs, especially for wind turbines, did the limitations of the current dynamic axial load carrying capacity of larger cylindrical roller bearings appear.
A constant specific heat loss factor for all bearing sizes now seems to be too optimistic for larger bearings. So, new factors based on experimental results and ISO 15312:2003 have been derived for bearings with a heat conducting surface Ar> 50,000 mm² with
Ar = . B . (D + d), see fig. 5. Inserted into (1) this leads to:
For Ar = 50,000 mm²:
for Ar > 50,000 mm²:
Additional cooling
In cases where the actual axial load exceeds the theoretical value derived by (1) or (2), additional cooling can increase the permis-sible axial load by a certain amount. For a constant oil flow through the bearing with a temperature difference between incoming and outgoing oil flow [°C] and an oil flow volume through the bearing
s [l/min], the permissible axial load Fap.oil [kN] becomes:
as part of the frictional energy generated inside the bearing is taken away by the oil flow.
Comparison
In larger industrial gearboxes cylindrical roller bearings in the NJ 23.. EC series are used and subjected to heavy axial loads. Fig. 6 shows a comparison of the dynamic axial load carrying capacity versus bearing size.
For bore diameters up to 85 mm , the current catalogue formula remains valid, but the permissible axial load can be further increased by oil flow cooling.
For example: a NJ 2313 ECP bearing can withstand an axial load Fap.oil = 15 kN instead of Fap = 9 kN when it is cooled with s = 0.4 l/min oil flow through the bearing and the oil inlet temperature is
= 20°C below the bearing operating temperature for chosen reference conditions with
Fr = 29 kN and n = 1,600 r/min.
For bearings in the NJ 23.. EC series with a bore diameter larger than 85 mm , it can be seen that the “former” formula gives rather high values (curve “A”), e.g. Fap = 274 kN for a NJ 2360 ECMA bearing at Fr = 400 kN and n = 285 r/min which could, according to (2) and (3), only be realized with an oil flow of s= 11 l/min and
= 20°C.
Fluctuating axial loads
For “short periods of time” twice the value of Fap out of (1)/(2) can be permitted if it results in a temporary rise in bearing operating temperature of no more than 5°C. Depending on the bearing size, load and speed this “short period” covers only several seconds or can last a few minutes. As a rule of thumb, this “short period” can be considered as the time during which the axially loaded bearing runs 1,000 revolutions.
Other criteria
For slow running applications, in particular, it is not the frictional energy, respectively smearing in the flange contact, but the flange strength that puts the limit on the axial load carrying capacity of a cylindrical roller bearing. Easy-to-use formulas can be found in the SKF General Catalogue. However, for critical cases more precise calculations are recommended, e.g. by use of advanced FEA programs (fig. 7). SKF offers a consultancy facility through its application engineering services for this purpose.
Summary and outlook
With help of the reworked formula for the dynamic axial load carrying capacity of cylindrical roller bearings it is now possible to obtain a sufficiently precise estimation of the permissible axial load also for larger bearings with a heat conducting surface Ar > 50,000 mm². Operating conditions such as radial load, speed, lubrication, as well as internal geometry of SKF bearings and new friction models are taken into account. In addition, cooling by oil flow can be considered to calculate either the required oil flow for a given axial load or a permissible increase of axial load for a given oil flow. As SKF engineers are continuously aiming at improving profiles and materials, reducing friction, etc., these new formulas will also be continuously revised, presum-ably leading to even higher values in the future, which will have an impact of improved performance.